1. Introduction
Over the last several years, China’s PV industry has developed rapidly, its newly installed capacity ranking first in the world for 8 consecutive years. The time is right for the integration of smart manufacturing with the PV industry, based on emerging technologies such as artificial intelligence, industrial Internet and big data.
In terms of quality control and process analysis, after nearly five years of application of AI+ vision recognition technology in PV module production process, it has now entered a full-scale stage. In this context, SC Solar and YOUCENG AI have launched a strong overall production process detection and big data platform, aiming to comprehensively improve the digitalization and intelligence of the module production industry, optimize the allocation of production resources, eliminate or reduce batch defects, control the transmission of important defects and realize the double improvement of production efficiency and product quality.
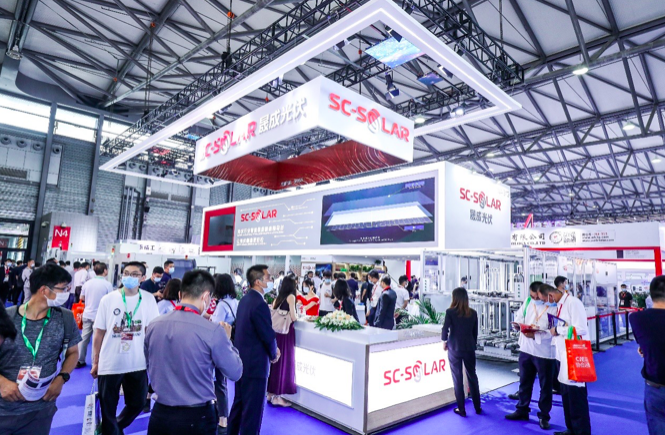
2. Vision AI + detection node
2.1 Introduction to the technology platform
SC Solar’s self-developed closed-source image process algorithm is based on artificial intelligence technology, independently developed and successfully applied to industrial scenarios; it can achieve small samples as well as high-accuracy of AI detection.
The algorithm is based on linear mathematics, non-linear correction, multi-image fusion and deep neural network technologies, and can be flexibly applied to all aspects of the PV module production process. The algorithm platform can independently provide software and hardware for integration to imaging equipment, process lines and data control center and, with strong practicability and scalability, it has been successfully applied in various links.
2.2 Application nodes of the overall process of PV module production
The following figure briefly summarizes the monitoring points of the main PV module production process. It can be seen that, for each node, SC Solar has a corresponding visual detection solution.
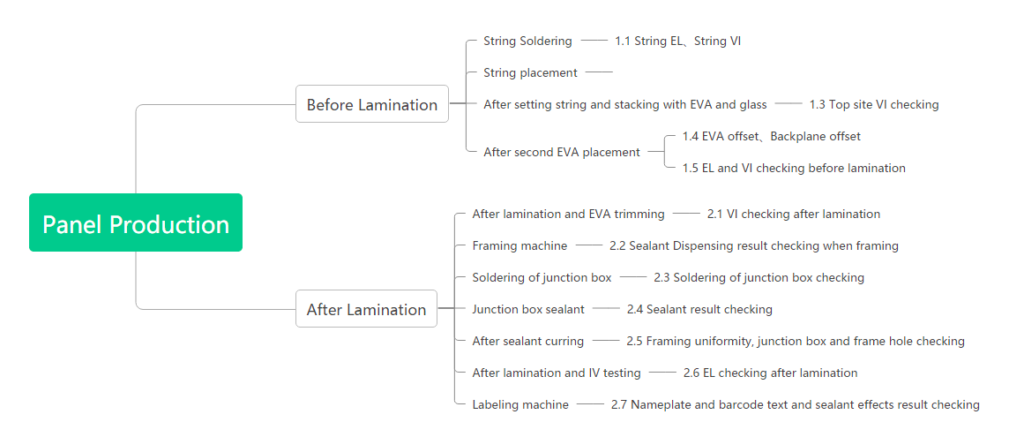
2.2.1 String EL and Appearance Check
As the most important process before lamination, the stringer is inspected online in real time to detect fluctuations in operating parameters and avoid batch defects, which is of great importance to the operation of the production line.
(1) String EL detection
The AI model of string EL can cover all process types of PV cells and strings. The system can be independently set according to a cell size of 15x-210, compatible with or without chamfering cells. Defect types include cracks, not soldered, black cell, light and dark cells, bus-bar interruption, black spots and scratches. They can be corrected by means of the threshold value of each detected item being set to meet the process requirements of different customers and different incoming materials.
(2) String appearance check
For type of defects that EL unable to detect, such as cell spacing, ribbon offset, overlong of ribbon (risk of short circuit), flux residue and foreign objects, it is necessary to add string appearance check, by use of an advanced inline scan camera to obtain high-resolution pictures. Compared with similar solutions in the industry, the detection effect of this solution is more stable and reliable.
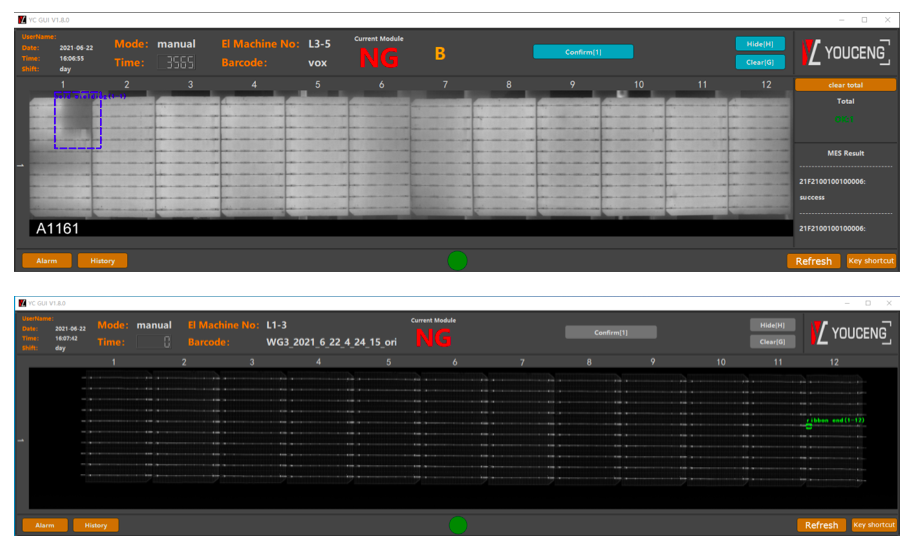
(3) Detection of string length and ribbon ends
In an auto string lay-up machine, string length and ribbon ends detection are added. Inaccurate string length, ribbon ends misssing, angle deflection, insufficient length and misalignment can be detected.
2.2.2 The appearance detection of the reverse side after string lay-up
After the laminates unload from the string lay-up machine, the back side is facing up, and an image acquisition device is set here. With the algorithm, it can detect problems such as abnormality of string spacing, insufficient creepage distance, broken cells (larger) and large dirty foreign matter.
2.2.3 The appearance detection of the reverse side after bussing
After bussing, before the 2nd EVA Cutter, it can clearly see the position of the bus bar and lead wire, where it is possible to detect defects such as ribbon offset, the position of the bus bar lead point, string spacing and creepage distance.
2.2.4 Appearance detection after 2nd EVA laying
The main problem after the 2nd EVA laying is that the lead wires may fail to pass through punch the holes, resulting in the failure of the subsequent process to operate normally. Taking pictures of the lead wires here can effectively block the defects.
2.2.5 EL and appearance detection before or after lamination
EL and appearance detection equipment have been used in the industry for many years. SC Solar’s automatic detection system, combined with AI has also been successfully applied for the high tier manufacturer’s production line.
The AI model covers all detected items of EL and appearance, such as not soldered, cracks, bus-bar interrupt, broken cells, fragments, parallel series and solder strip offset, covering all cell types and compatible with all versions; in addition, detection on the production line adopts the first-out-after-judgment model, and the production line cycle time is better than before the introduction of the AI system. Judging from the operating data of several years of stable application of the system actual production lines, the platform has effectively saved labor costs and greatly reduced the module degradation rate.
In terms of system solutions, SC Solar provides multiple operating modes such as single tool, intehrated tools and centralized judgment, which are convenient and quick to switch. Taking the three production line co-operation modes as an example, only one person is required to re-judge the AI detection and all daily tasks can be completed, as shown in the figure below:
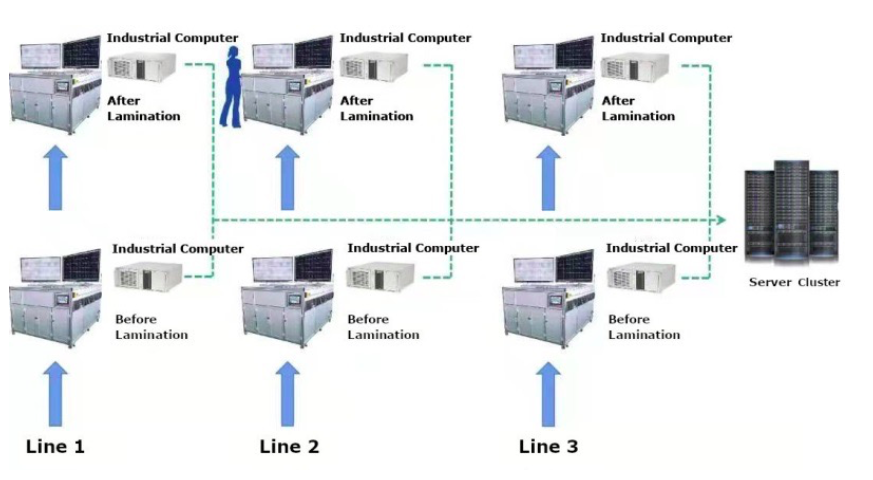
2.2.6 Appearance detection after lamination
Appearance detection after lamination is mainly aimed at shooting the appearance of the laminated module, including the front appearance of a single-glass module and all of a double-glass module, detecting defects such as bubbles and cell chipping caused by the lamination process. By inspecting the laminated module, if continuous defects are found, the problems of the laminator can be predicted in advance and can be checked and repaired to reduce any loss in production. Finally, through image synthesis, images and defects are displayed in the GUI for easy use.
2.2.7 Sealant Dispensing checking for framing
Should an intermittent sealant problem occur in the framing machine, the sealant can be added manually at manual station. This will not only waste of labor resource and reduce the production line capacity, but also cannot fundamentally solve the quality risk of the sealant. SC Solar uses dual cameras to monitor the sealant dispensing process in real time, detect intermittent sealant dispensing and give an alarm, which is necessary to prevent defects.
2.2.8 J-box soldering picture archiving and detection
The main process of the J-box is soldering, detection and repair, then directly entering the sealant filling process. If there are subsequent failures and customer complaints, it cannot be traced. For soldering quality monitoring, a high-pixel single-point straight shooting method is adopted to collect and archive pictures of each J-box before the sealant is poured, so that subsequent problems can be traced. At the same time, for the image combined with invalid barcode recording and analysis, through a large amount of data and algorithm combination iteration an effective algorithm is obtained, and the defect detection is performed at the same time as the image is collected.
2.2.9 Sealant filling effect detection
After the sealant filling machine, the quality of sealant filling and the installation of the J-box (the bottom sealing rubber ring outside the box) can be inspected to avoid quality problems caused by too little sealant or leakage and poor sealing rubber ring at the bottom of the J-box. Use of a deep learning algorithm combined with a traditional algorithm achieves effective detection and sealant filling quality control. The following are typical online checkout results:
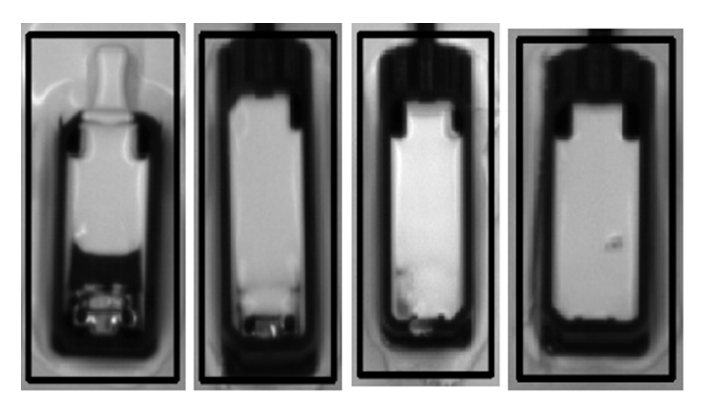
2.2.10 Frame detection before and after curing process
Using imaging to measure the frame size of a module, accuracy can reach 1mm; in addition, it can detect mounting, leaking and grounding holes at the same time, and measure the positions of the mounting holes.
Combining the above sealant filling effect solution, SC Solar has created a new 3-in-1 detection process, simultaneously detecting the sealant filling effect, frame size and frame hole position at the same station. The following is the actual detection software interface.
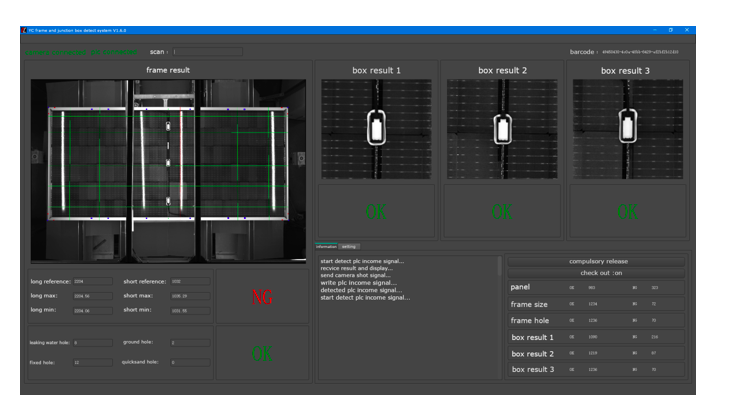
2.2.11 Nameplate and barcode detection
Regarding possible defects of nameplate and barcode auto labelling, such as bubbles, wrinkles, unclear printing, skewed, missing and incorrect label pasting, SC Solar’s platform has shown excellent detection capabilities.
3. Introduction to the quality of technology big data platform
3.1 General introduction
SC Solar’s big data platform for the product quality of intelligent PV module production is a real-time, multi-point, human-computer interaction system based on big data algorithms. The system platform has the functions of data collection, storage, visualized real-time data reports, process analysis tools and data correlation mining for the whole process of product quality.
The platform uses advanced big data mining algorithms to locate data relevance, combined with expert systems to analyze equipment, process, and product quality relevance to reduce complicated data statistics. Through the system, a more reasonable long-term solution can be obtained to optimize work efficiency, streamline manpower and improve quality.
3.2 Peculiarity of system operation
Information collection in the production process is realized through the high integration and data visualization of detection information.
The typical shape of defects is closely related to their cause. Combining process experience and image big data algorithms, an automatic, real-time, intelligent platform can replace the current cumbersome analysis of data and locate the entire process of equipment failure.
Using big data tools, through the analysis and mining of detection data, self-learning iteration, associating equipment and processes, it is possible to realize predictable maintenance as well as creating another round of added value.
3.3 System structure and function introduction
3.3.1 System structure
The big data platform consists of data sources, process expert systems, deep learning, data analysis systems, and process equipment strategy systems. The data comes from the full-process detection system, assembly line operation data, MES part data and equipment operation data described in Chapter 2 of this article. After fusion, the data enters the process expert system. After the data is organized and regularized, it is sent to the deep learning data mining network for inference, and the action decision of the process equipment is obtained. The entire process continues to be closed-loop and spirally improved to achieve the goal of optimal control of the production line.
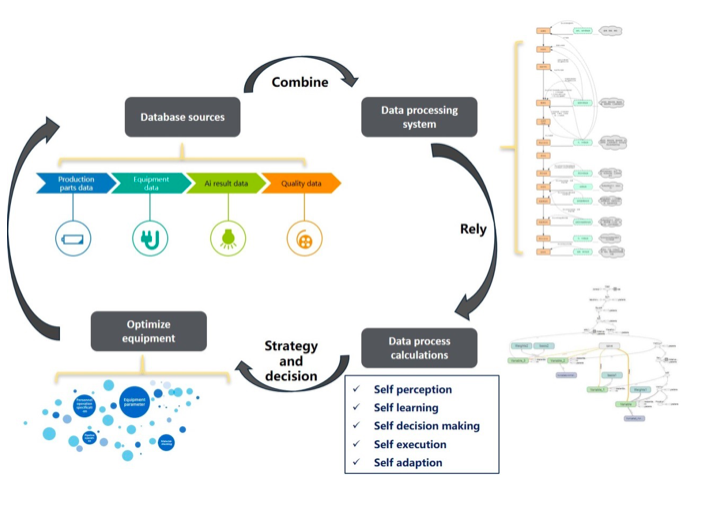
3.3.2 Partial function display
Taking detection before lamination as an example, the system can select the proportion of defects in the generation period according to the time, and display them on a mobile terminal and a computer terminal respectively. Some data statistic functions for serial detection and module defects are as follows:
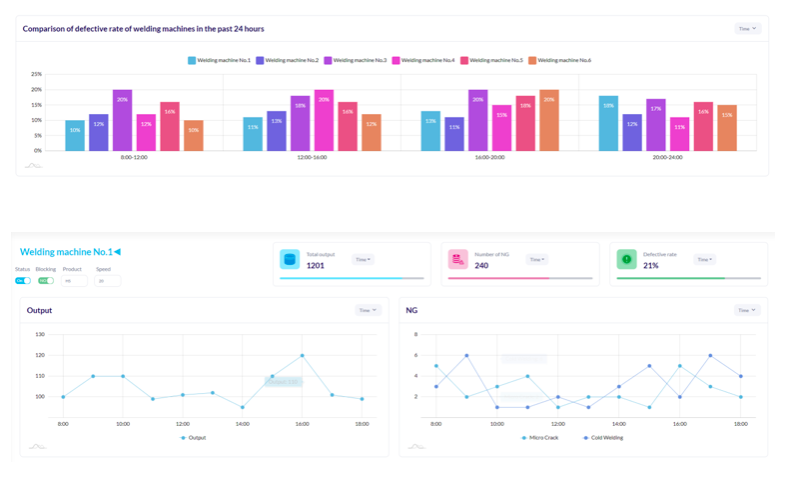
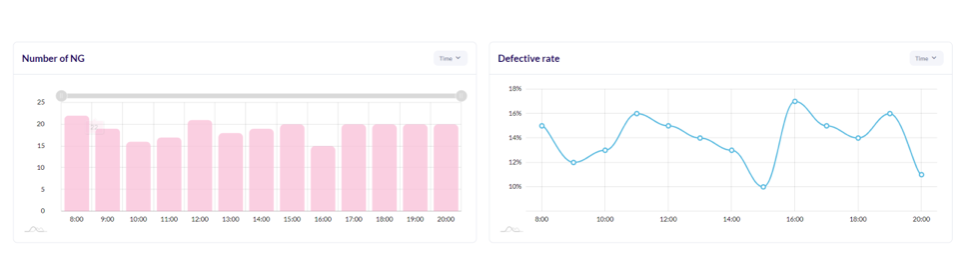
4. Future development trend
There is no doubt that intelligence is the development direction of manufacturing automation. It is imperative to apply artificial intelligence and expert system technology extensively in all links of PV module manufacturing, so as to optimize processes, improve the efficiency of production scheduling and quickly diagnose faults.
SC Solar and YOUCENG AI are committed to this round of smart upgrades in the PV industry, combining their own advantages, using assembly lines, functional equipment and intelligent testing equipment to form a data source network, analyzing and fusing a large amount of data to create a platform. On this basis, SC Solar will carry out an in-depth study of industry needs, continue to iterate and improve the capabilities of functional systems and finally help the PV module industry to achieve real intelligence.