Indium, a silvery-white and slightly bluish metal in its natural state, is soft, ductile and corrosion resistant. It has the advantages of low resistance, good light permeability and strong electrical conductivity and Indium Tin Oxide (ITO) is widely used in areas such as the production of LCDs, flat and touch screens and optical film.
It is also used in the third step in the manufacture of heterojunction (HJT) cells. Specifically, through Physical Vapor Deposition (PVD) equipment, the ITO target material is deposited onto the surface of silicon wafers through magnetron sputtering, with transparent conductive oxide (TCO) film, with both sides consistent, subsequently produced.
However, since indium is a rare metal, its price is relatively high, leading Maxwell to adopt a ‘multi-pronged’ approach in terms of, among other aspects, equipment and technology, continuously promoting a low indium HJT TCO solution with a view to driving the industrial development of HJT technology with reduced costs and increased efficiency, while consuming less indium when manufacturing cells. The following sets out Maxwell’s three step approach for the reduction of indium consumption:
I. Equipment Optimization
In order to optimize the PVD equipment for HJT cells, Maxwell looks to decrease the unit consumption of the target material at the very start of the R&D process. After optimization of the sputtering unit, Maxwell’s latest equipment theoretically consumes 13.5mg/W of 100% indium-based target materials per unit, dropping from nearly 20mg/W. Old equipment can also be upgraded in this regard.
In the process of reducing the unit consumption of target materials, Maxwell has accumulated significant test data and solutions for improvement, forming a clear and effective technical path. The company expects to be able to offer an overall solution for HJT cell manufacturing with a unit consumption of 100% indium-based target material theoretically reduced to around 12mg/W by the end of 2023.
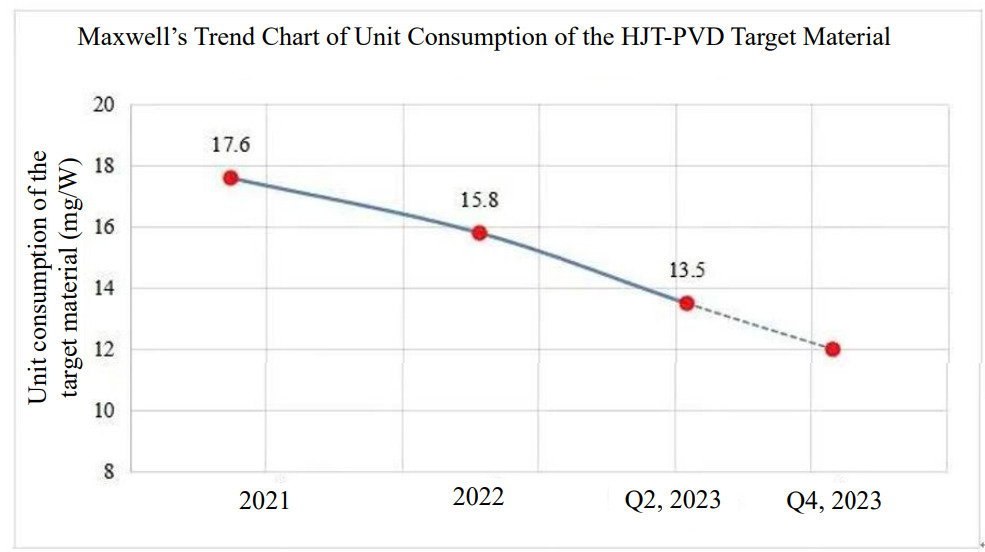
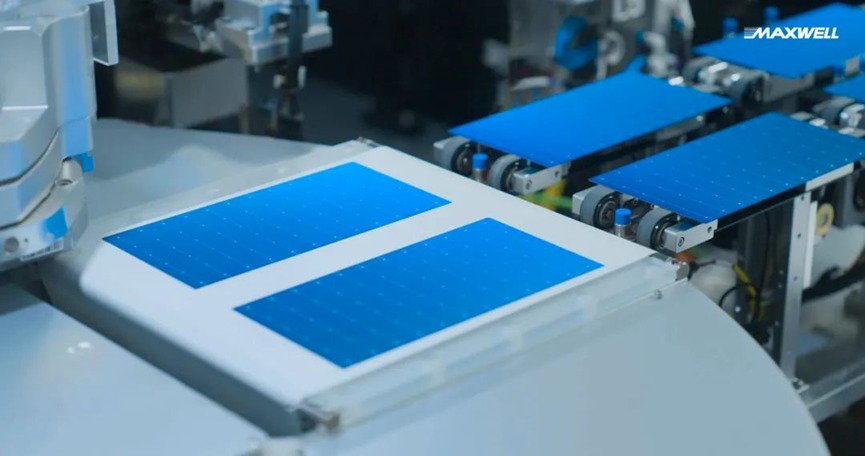
II. Low-indium Laminated Film
The combination of a low-indium laminated film solution (50% indium free) and the foregoing equipment optimization can help bring the theoretical unit consumption of indium-based target materials down to about 6mg/W.
After continuous technology research and development, Maxwell now offers an HJT cell manufacturing solution of 50% indium-based and 50% non-indium-based laminated TCO. The conversion efficiency of this solution is equal to that of 100% indium-based TCO cells, with the low-indium solution both reliable and stable and able to be perfectly combined with other low-cost solutions including copper plating and silver-clad copper.

Maxwell’s PVD equipment is compatible with all these low-indium solutions and they can be imported by adjusting the target material and target position. Given that there are different types of non-indium-based target materials with a huge range of resistivity, Maxwell’s equipment runs with multiple input modes, making the sputtering of non-indium-based target materials more stable.
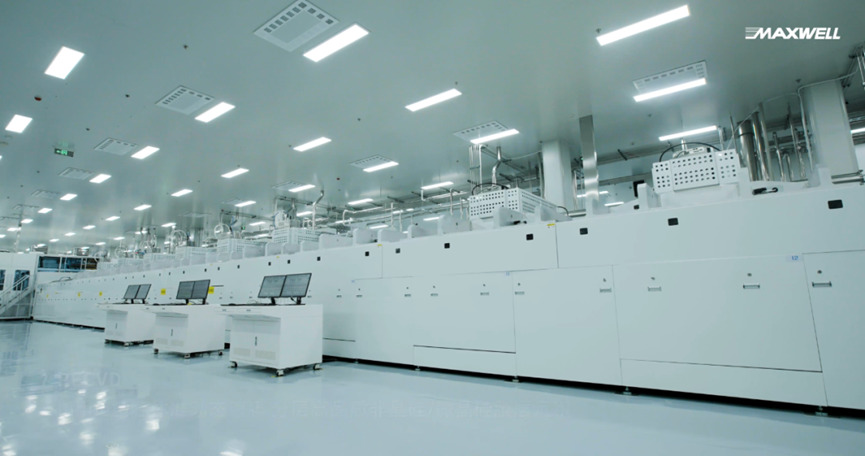
III. Large-scale Indium Recycling
Given the growing scale of the HJT industry, further recycling of indium materials can be achieved. As non-indium-based target materials become more widely used, the indium consumption at Gigawatt (GW) level HJT cell factories is expected to fall to 1mg/W.
Thanks to its continuous equipment optimization and technological innovation, Maxwell has acquired a great deal of expertise in HJT technology and is looking for additional ways to help HJT cell manufacturers reduce their costs and improve efficiency. Last August, the company combined its low-indium (50%) TCO technology with a copper plating busbar, receiving certification from ISFH for an HJT cell efficiency of 25.94%, equal to that of a 100% indium-based cell. With the above three approaches for the reduction in indium use, Maxwell is confident that it can contribute to a brighter and broader future for the HJT industry.