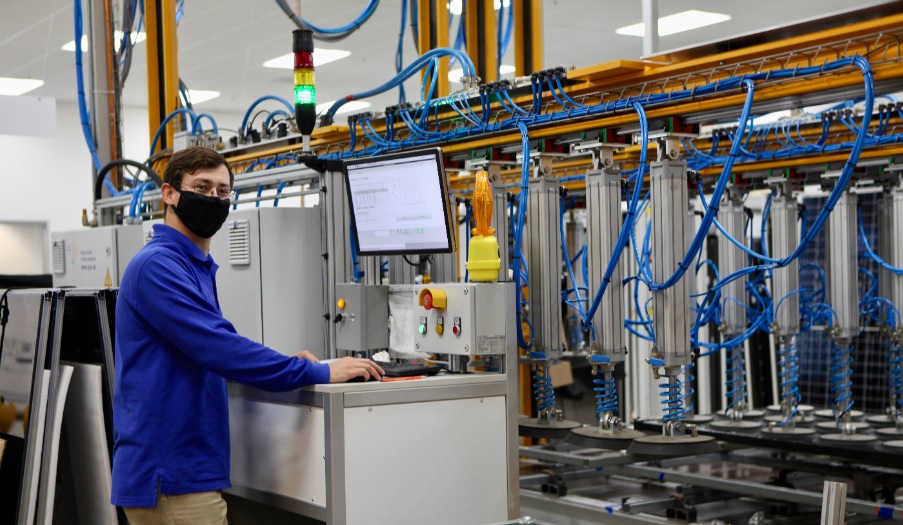
The rapid transition in the upstream manufacturing solar sector to significantly larger p-type and n-type monocrystalline wafers, cells and modules may be hailed a new era for the industry in higher module performance and a leap in reducing PV power plants LCOE (Levelized Cost of Electricity) in a rapidly changing downstream market that becomes subsidy free, bidding orientated and targeting grid parity and beyond.
As seen with previous transitions away from multicrystalline to monocrystalline modules coupled to the mass adoption of PERC (Passivated Emitter Rear Cell) technology the buck often stops at the downstream project developer, EPC and asset owners.
Try Premium for just $1
- Full premium access for the first month at only $1
- Converts to an annual rate after 30 days unless cancelled
- Cancel anytime during the trial period
Premium Benefits
- Expert industry analysis and interviews
- Digital access to PV Tech Power journal
- Exclusive event discounts
Or get the full Premium subscription right away
Or continue reading this article for free
Helping the downstream sector to navigate a new area in rapid module technology developments often rests with independent testing houses, tasked with identify and measuring claimed performance gains while laying bare any reliability issues that may surface and guiding on possible solutions.
We recently had the opportunity to talk at length with Cherif Kedir, the President and CEO at the Renewable Energy Test Center (RETC), based in Fremont, California.
The discussion touched on various issues currently impacting module design, certification, performance and reliability that are obviously critical to investors seeking to reduce risk in PV power plant investments and maximize long-term site returns.
However, we wanted to start the interview with an update on a topic that Cherif discussed at depth at the PV ModuleTech 2019 event in Penang last October– bifacial modules.
There have been many new developments with module design in the past 12 months, and since bifacial modules started to see good traction in the utility segment globally, there were still many concerns when implementing bifacial modules, including albedo measurements, tracker yields, reliability concerns, the impact of higher currents and powers, and generally whether or not the extra investments were worth the risk.
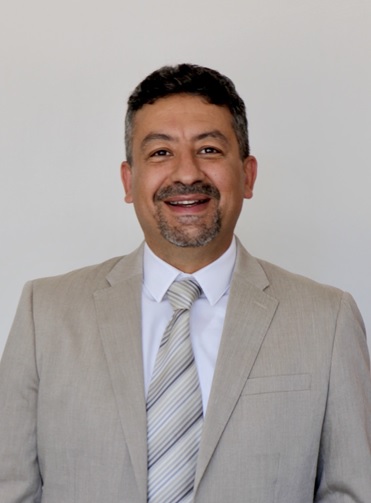
How should we consider bifacial modules today, in terms of performance and reliability? And what are the issues now that are most critical to understand prior to field deployment?
Cherif Kedir: “Bifacial module technology has been a good development for the PV industry with validated increases in energy yields in installations, ultimately reducing LCOE with a little additional investment from the EPC/Developers. Yet, there are some risks associated with the technology which have been found to be relevant and recurring during our tests. One common concern that the industry has been grappling with is long-term performance and reliability. Within the larger subject of concerns over performance and reliability, one topic that deserves focus is backside performance degradation which, in some cases, may be attributed to LeTID and PID.
In addition, field conditions, which are location specific, have also come into play when we talk about performance and reliability. In the field, the O&M plan, field albedo, and the weather conditions in the field where products will be deployed, all have an effect on the successfully performing at expected levels. Developers should survey a future project field and assess the albedo at a given easy-to-access location using the data they collect to predict the albedo for all the modules to be installed in a few hundred acres. Developers know that value can and likely will change throughout the site and need to plan accordingly. Regardless of the individual location plan, the real field albedo will be greatly influenced by the EPC and O&M plan; the system and module design can have a profound impact on optimal operation as well as biological factors such as how the ground cover is maintained and the type of vegetation management/weed control used at the site.
Additionally, modeling accuracy and any assumptions made or implied about the model need to be considered for their potential impact. This is not necessarily a new issue, however, additional rear side performance assumptions add uncertainty; this is driven by how the modules are installed (1P vs 2P or 2L), wire management, and other factors impacting the rear side of the modules in the field.
A common concern in the industry is long-term reliability and durability. We routinely subject modules to a battery of tests in order to assess the likelihood they will last in the field and produce the expected energy throughout their lifetime. In recent months however, one new concern has been the hail susceptibility of PV modules as power plants face increasing hail events. As a way to address this, RETC has introduced the Hail Durability Test (HDT) where the front glass becomes the focus. Modules are generally getting larger with the use of large M4 and M6 cells and many use a glass/glass construction, which makes them heavier. The additional weight makes these modules harder to handle and therefore may negatively impact the installation labor cost. To remedy this, some manufacturers have reduced the glass thickness from 3.2 mm to 2.8 mm or thinner. This results in a lighter module, which in general is easier to handle. Thinner front glass often cannot be tempered and is instead heat or chemically treated to strengthen it. In our testing, we find a higher occurrence of hail damage on modules constructed with thinner non-tempered glass. As a result, these modules may be less durable in the field, have lower mechanical rigidity, and lower impact resilience.”
Cherif, you brought up mechanical durability and the glass characteristics of these modules, so let’s talk about hail. The Hail Durability Test (HDT) is one the new tests gaining importance relates to how modules can withstand the effect of hailstorms. Can you give some background here, why this is getting more attention from investors, and what tests can be done to simulate module performance due to hail?
“RETC developed the Hail Durability Test (HDT) to quantify and understand the effects of hail on modules. The market for modules is growing in the US Midwest and south which experience ranging severity in weather patterns, including hailstorms. Our HDT program enables us to categorize modules, their various construction processes, and their Bill of Materials (BOM’s) for how well they will endure ice projectile impacts in hail prone regions. We launch a variety of ice balls at the modules to mimic varying hail storm events with a range of ice projectile impact sizes at terminal velocities. This permits us to analyze a module’s performance near their threshold of damage and more accurately assess the risk they could pose in hail prone regions.
As previously mentioned, bifacial modules constructed with thinner front glass can be more susceptible to breaking during hail events. In our Hail Durability Testing, we see a higher failure rate on bifacial modules with thinner front glass than monofacial glass/backsheet modules with 3.2mm front glass.”
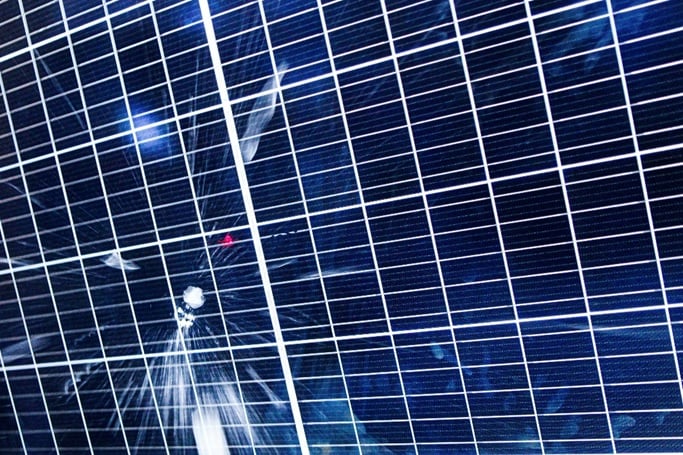
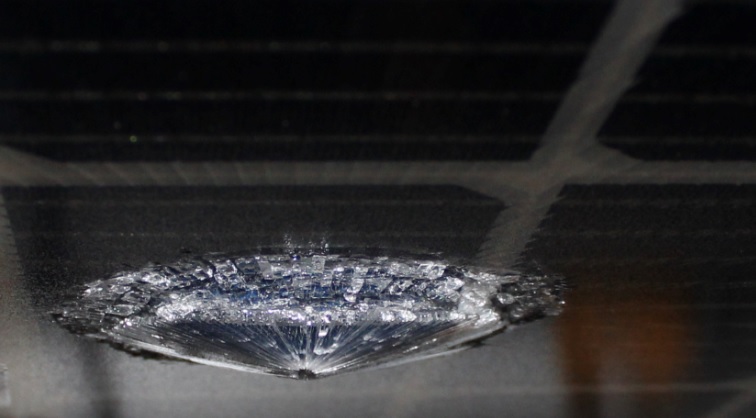
“In the RETC Hail Durability Test Protocol, we look at glass breakage as well as cell cracks and performance degradation. Though it is fairly common to see cell cracks at high impact energy using 50.8mm (2 inch) ice projectiles at terminal velocity, it is not very common for conventional monofacial modules to break. This is not the case with recent batches of modules. Historically, only 5 percent of modules we tested shattered when impacted with a 2” projectile at terminal velocity. In recent submissions, the rate at which modules are failing is in some cases 10 times higher. This is alarming considering the increasing frequency and hail size in many US regions, which are seeing the highest number of PV installations.
Beyond catastrophic glass breakage, the hail impact often causes internal cell cracks which could result in performance degradation, especially over the life of the product. In the field, the module is subjected to more stresses beyond the hail event. The hail impact triggers cell cracks and micro-cracks. And with subsequent heating and cooling cycles, as well as vibrations from wind and gust events, those cracks tend to worsen over time.”
The converstion then returned to changes in module design now, with our observation that it seemed that module suppliers were changing module design and power ratings, almost on a monthly basis. Our observations were that many people are confused now about how modules have gone very quickly from 370-380W to north of 800W. It seemed to us at PV Tech that many things have changed here, from wafer and cell sizes, module layouts and sizes and materials used, in particular during module assembly.
Can you talk about how some of these changes are impacting module reliability, in particular given all the changes during manufacturing and the bill of materials?
“We’ve definitely seen some new factors impacting module reliability here at RETC. Some of these issues are pretty basic as they end up relating to the increase in power output of higher-performing modules. Other times, changes in modules are centered on larger construction and more. A typical issue that we have seen often is the use of legacy components which were originally designed for monofacial modules with M2q cells. Diodes, cables, and connectors which were designed and proven to operate below 10A are now used on modules operating at 10-20% higher current. This results in excess heating at the connectors, causing them to fuse in various tests that we perform, and more frequent diode and junction box failures that range from shorted diodes to completely warped junction boxes.
Uneven shading also plays an important role in module reliability. Uneven shading is normally caused by factors like bird droppings, leaves, and nonuniform soiling that may accumulate on top of the module, causing some of the cells to overheat under normal operation. In bifacial module technologies, even the modules themselves, the installation, or racking design could cause some cells to hotspot. Some bifacial manufacturers use larger junction box designs that shade certain cells and cause them to operate at a higher temperature. The racking design and wire management play an equally important role and are sometimes the cause of non-uniform back side irradiance distribution.
A common issue that we’ve seen in recent months is the pandemic’s impact on the PV supply chain. Some manufacturers are having difficulties securing a stable supply of their raw materials (EVA, backsheets, even cells) to fulfill long-term obligations to their developers. This is causing a strain on the manufacturer’s ability to commit to a specific BOM which they are often obligated to do contractually by their customers, the developers. Beyond just the commitment and the ability to supply products with specific BOM formulations, the testing that’s associated with those BOM’s and performed well ahead of the project execution, may not cover the materials that manufacturers end up shipping to the site. This is an issue that manufacturers are dealing with and are trying to work out with their suppliers and the developers. Aside from the quality concerns, developers are now facing the reality of accepting untested materials. As a result, some developers are adopting periodic reliability testing to line up with major batch shipments. This not only ensures consistent quality for their supplies but serves as a preemptive action to validate new BOM’s they are given in the middle of the project execution.
These supply chain issues will likely persist for some time as the COVID-19 pandemic and its global impact is predicted to last into next year. However, the supply issue will inevitably be solved. Manufacturers have become more likely to take extra care in vetting their secondary and tertiary suppliers and to perform more rigorous and more frequent reliability monitoring tests. In our opinion, a developer’s decision to perform additional due diligence on these products will yield higher-quality installations, a result of manufacturers’ anticipation towards the additional testing and the increased due diligence that will be performed on their products.”
During 2019, RETC released the PV Module Index. What was the driving force behind this, and in the context of the changes in module design and testing protocols, how has the index been evolving over the past 12 months?
“Over the past few years, manufacturers have asked us to create a report that includes our findings in the test lab and the accomplishments that we’ve seen within the industry. They wanted us to show which companies were manufacturing great products. So we did– we created our PV Module Index (PVMI for short.)
After careful consideration, we have created and continued to improve our annual PV Module Index report (PVMI) so that the findings we published focused on the following:
● Creating a report that is free and accessible to anyone and everyone
● Providing specific, data-backed findings
● Including meaningful reports on performance
● Objectively highlighting manufacturers’ accomplishments and showing who is best at manufacturing product in the industry
In creating the PV Module Index, we avoided creating a report that ultimately ranked manufacturers. Instead, we focused on highlighting specific products and product families. We created our PVMI report to be as direct as possible. It’s as simple as this: in order for a manufacturer to be selected as a high achiever by RETC, they have to tick off all the checkboxes. They will need to have high-performance and high-reliability in all aspects.”