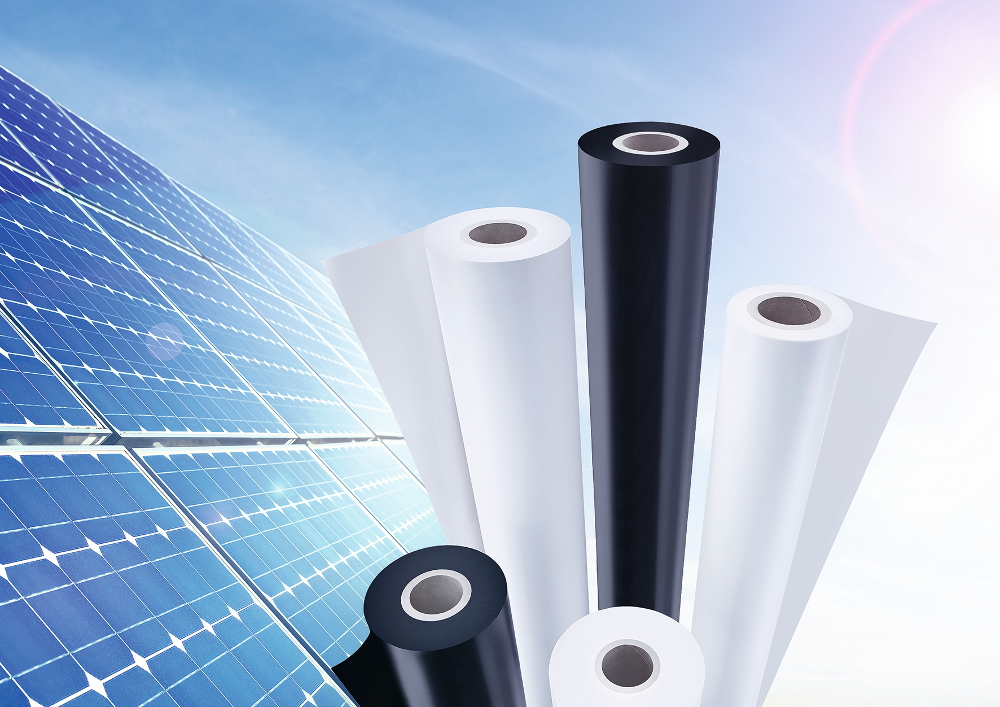
Bischof + Klein has introduced a new generation of PV module backsheets, designed to provide greater stability when exposed to UV radiation and increased protection against moisture ingress. The new B+K ‘BackFlex’ PP backsheet is based on polypropylene and is therefore naturally resistant to hydrolysis. It can withstand more than 5,000 hours of damp heat testing (85°C / 85% r.h.).
Problem
Unlock unlimited access for 12 whole months of distinctive global analysis
Photovoltaics International is now included.
- Regular insight and analysis of the industry’s biggest developments
- In-depth interviews with the industry’s leading figures
- Unlimited digital access to the PV Tech Power journal catalogue
- Unlimited digital access to the Photovoltaics International journal catalogue
- Access to more than 1,000 technical papers
- Discounts on Solar Media’s portfolio of events, in-person and virtual
PV modules are installed all over the world, and are therefore exposed to diverse, constantly changing environmental conditions for many years. The backsheet plays an important role in the lifespan of PV modules. It has to protect the inner parts against corrosion and hydrolysis by preventing the ingress of, for instance, water vapour over a period of 20 years and more. It additionally has to withstand the harsh climates to which PV modules are exposed. Electrical safety in terms of insulation also plays an important role. Finally, special requirements such as low shrinkage during vacuum lamination have to be met by the manufacturer.
Solution
The new B+K BackFlex PP backsheet developed by packaging and film specialist Bischof + Klein can withstand more than 5,000 hours of damp heat testing (85°C / 85% r.h.). Polyester (PET), in particular, is prone to hydrolysis due to its polymeric structure. The ingress of water vapour into PV modules can cause corrosion of the metallic components but also hydrolysis of the encapsulant EVA, leading to the formation of acetic acid. B+K BackFlex PP is said to reduce water ingress by more than 50% compared to market standards. System voltages can be high in PV installations so particular attention has to be paid to electrical safety in terms of insulation. B+K BackFlex PP is certified for a system voltage of 1.5 kV DC. The 360 µm B+K DuroFlex PP offers a dielectric strength of 60 kV. During PV module production, the module stack is vacuum laminated. In this process, backsheet shrinkage is minimised to reduce mechanical stress inside the module stack. The B+K BackFlex PP meets these requirements with unique shrinkage behaviour of no more than 0.3% in both dimensions, according to the company.
Applications
PV module backsheet.
Platform
The new B+K BackFlex PP backsheet can withstand more than 5,000 hours of damp heat testing (85°C / 85% r.h.) and is certified for a system voltage of 1.5 kV DC. The 360 µm B+K DuroFlex PP offers a dielectric strength of 60 kV. The optical reflectance of the backsheet significantly influences PV module efficiency. B+K BackFlex PP offers high optical reflectance within the solar spectrum that is comparable to market standards such as TPT or PPE. The backsheet is manufactured in a one-step co-extrusion process that leads to outstanding internal adhesion. No glue or solvents are therefore required to produce the product.
Availability
May, 2018 onwards.