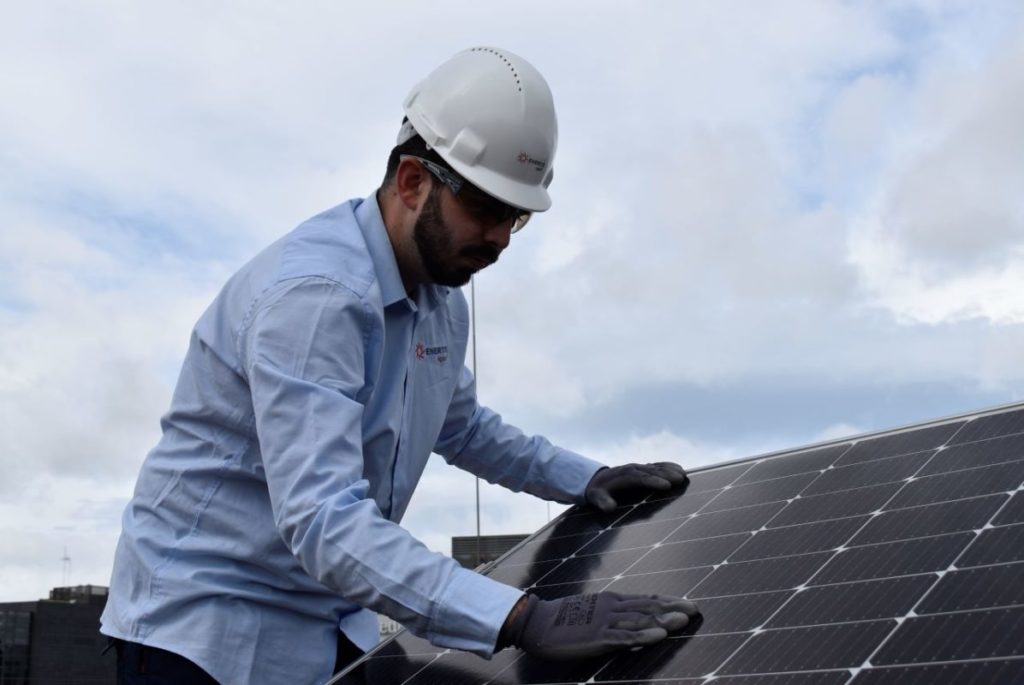
The rapid emergence of new PV technologies such as bifacial has in some cases outpaced the evolution of suitable technical and regulatory specifications. The occurrence hotspots in non-shaded areas of half-cell bifacial solar modules highlights the need for a rethink of international standards, write Sergio Suárez, Jose María Álvarez, Daniel Villoslada, Ignacio Fernández, Sofía Rodríguez and Gustavo Navas.
Unlock unlimited access for 12 whole months of distinctive global analysis
Photovoltaics International is now included.
- Regular insight and analysis of the industry’s biggest developments
- In-depth interviews with the industry’s leading figures
- Unlimited digital access to the PV Tech Power journal catalogue
- Unlimited digital access to the Photovoltaics International journal catalogue
- Access to more than 1,000 technical papers
- Discounts on Solar Media’s portfolio of events, in-person and virtual
The swift uptake of photovoltaic technology at a global level has led to a rapid pace of technological improvements, impacting both the tech innovation sector and the wider utility-scale market. As a result, over the past decade, the power output of solar modules has soared, while the cost per watt has been significantly reduced, two factors that led to a dramatic increase in the competitiveness of this technology. Recent advancements in the PV industry include enhancements throughout the solar module’s value chain, from the Bill of Materials (BOM) to the technology within the solar module itself.
This burgeoning demand and development have spurred scientific efforts to conduct studies and tests to ensure that international standards keep pace, yielding results that provide technical solutions for stakeholders operating in the solar industry.
In recent years, substantial technological shifts have occurred in the PV market, therefore companies face considerable uncertainty in the definition of the technical specifications of their PV projects. A prime example is the emergence of bifacial technology, which notably improved solar panel energy production, but also introduced widespread technical and regulatory uncertainty.
Proper technical advice at different stages of photovoltaic projects
Some standards that ensure in-factory quality control during the module manufacturing phase, such as the IEC 61215, have been updated with a broader focus and are supported by solid scientific literature. However, other standards, such as the IEC 62446-3, which are more oriented towards O&M services, have not yet been approached with such an expanded perspective. In this context, relying on specialised support from an independent third party, such as Enertis Applus+, is always underscored for proper technical advice at different stages of photovoltaic projects.
The study on “Thermal issues on half-cell bifacial modules. A way through albedo and mismatch voltage”, presented by Enertis Applus+ at this year’s EU PVSEC conference, offers an intriguing technical perspective on the thermal behaviour exhibited by half-cell bifacial solar modules under certain undesirable partial shading conditions during operational phases. These phenomena are not addressed by current standards, yet they provide valuable insights for industry companies.
Recent advancements pose fascinating technological challenges, such as characterising the “light source” from the ground in bifacial technology or the presence of parallel electrical circuits in half-cell technology, that carry certain physical implications when external variations are induced. In this study, we address the occurrence of hotspots in non-shaded areas of solar modules.
In Figure 2, captured using a standard thermographic camera in the field, an unusual element at the top of the module can be seen casting a shadow over one of the solar cells, leading to a typical hotspot in this type of semiconductor. However, a pattern of hotspots on the non-shaded part occurs in a way that is analogous to a reflection in a mirror. This is why we refer to this type of hotspot as a “hotspot mirroring” (Hmirror) during the study.
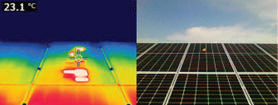
This type of defect ought to be scrutinised during ground or aerial inspections applying the IEC 62446-3 standard criteria. However, this is one of the instances where technological evolution has outpaced the standards: there is no classification for this kind of thermal anomaly, nor recommendations for its management, therefore it can potentially be mistaken for a thermal short circuit.
Surprisingly, there is a limited scientific discourse addressing these challenges, with international standards lagging in accommodating these findings.
While half-cell bifacial technology is widely integrated in utility-scale solar projects, anomalies are often observed with few misinterpretations. Recent trials we carried out on half-cell bifacial technology uncovered unique defects, prompting a re-evaluation of international standards. By merging on-field discoveries with internal experimentation, intriguing insights into the thermal behaviour of these modules emerge.
Enhancing quality control procedures
At Enertis Applus+, we conducted a series of forced-shadowing tests to categorise the new thermal anomalies found in these types of modules and we are excited to share some of these findings with the scientific community.
The overarching goal of our exercise is straightforward: enhance quality control procedures within the solar PV industry and chart a clearer, more definitive path in the unfolding renewable landscape that awaits all stakeholders in this transformative shift.
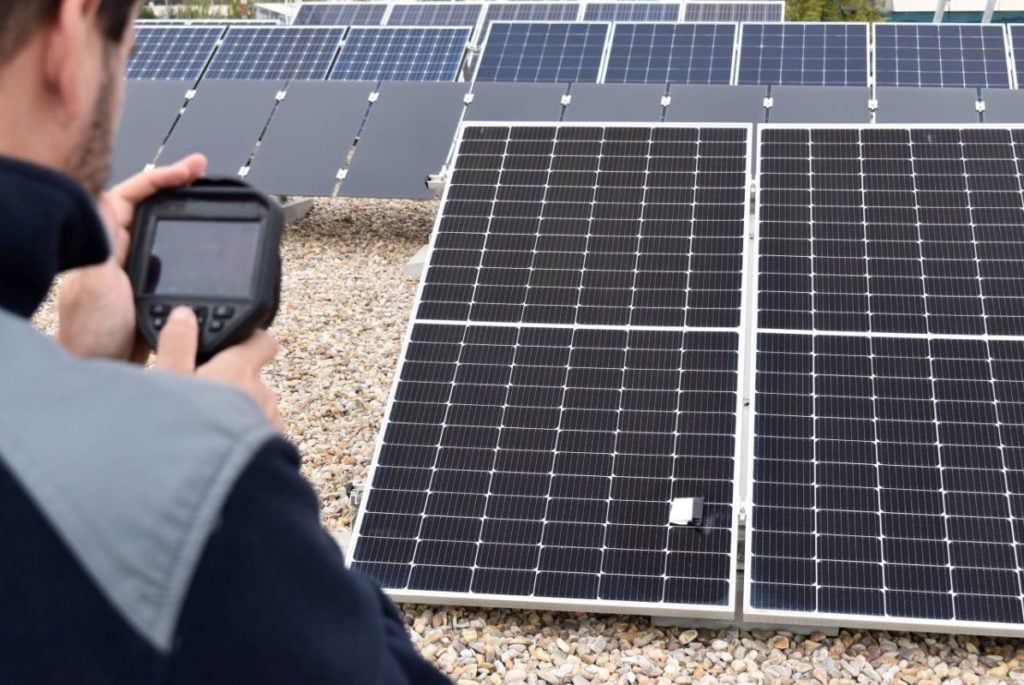
Our study seeks to bridge existing research gaps by delving into the impact of ground albedo and voltage mismatch on the formation of hotspots in half-cell bifacial PV modules. Using an empirical methodology grounded in on-field data collection, our findings provide a more intricate view that deviates from previous simulation-driven research [1]. Within this context, we introduce the concept of hotspot mirroring (Hmirror) to highlight a distinctive feature of half-cell modules and we explore its ramifications for thermal management.
The primary ambition of our research is to furnish insights that could shape forthcoming technical guidelines and standards pertinent to the design and installation of half-cell bifacial photovoltaic modules.
The study focuses on inducing hotspots using a type of textile to observe the thermal behaviour across different parts of the photovoltaic module under varying levels of irradiance.
Throughout the thermographic testing, five distinctly differentiated parts become clearly visible. These are:
- The induced hotspot, referred to in this study as hotspot shadowing (Hshad);
- The substring affected by the shading, the mirrored hotspots (Hmirror);
- The upper substring impacted by these unusual hotspots;
- The lower substring impacted by these usual hotspots;
- The module’s normal operating temperature.
The hotspot mirroring (Hmirror) phenomenon stands out prominently in our investigation. It arises due to a voltage mismatch between the upper and lower substrings in half-cell modules. This mismatch is different from current mismatch between cells, and it manifests when a cell under forced shading starts to produce a negative voltage.
Since there are now three electrical circuits in parallel (one being the protection diode, another one the upper substring, and the third one, the shaded lower substring), the voltage across them must always be similar, due to basic electrical laws.
The presence of a negative voltage in the lower substring, which does not correspond with the positive voltage of the upper substring, results in a voltage mismatch that forces the non-shaded substrings to align their voltage with the rest of the circuit.
The ripple effect of this is a disturbance in the regular operation of cells situated on the opposite side of the shaded cell. A distinct checkerboard-like thermal pattern emerges as a result, primarily impacting the more vulnerable cells in the adjacent substring.
Our experimental observations of (Hmirror) align with conclusions drawn from previous simulation-based studies [1]. To elucidate this phenomenon further, we have incorporated an on-field infrared (IR) image (Figure 3), which vividly displays the checkerboard thermal patterns spanning the affected cells.
The experimental validation of the hotspot mirroring phenomenon underscores its significance in thermal considerations for bifacial half-cell PV modules, where the ground albedo effect can lead to increased current in cells and create potential partial shading under various specific conditions.
To conduct a thorough analysis of the thermal behaviour in both half-cell bifacial and monofacial photovoltaic modules, we developed an elaborate experimental framework. Both module types were integrated with a monitoring system, capturing data on irradiance and temperature at various locations across the tested devices.
Each module featured five thermocouples specifically for temperature monitoring (Figure 4). To ensure an accurate reading of irradiance, two sensors – termed Gfront and Grear – were placed on each module to measure frontal and rear irradiance, respectively. A visual aid showing the schematic representation of the sensor arrangement can be seen in Figure 4.
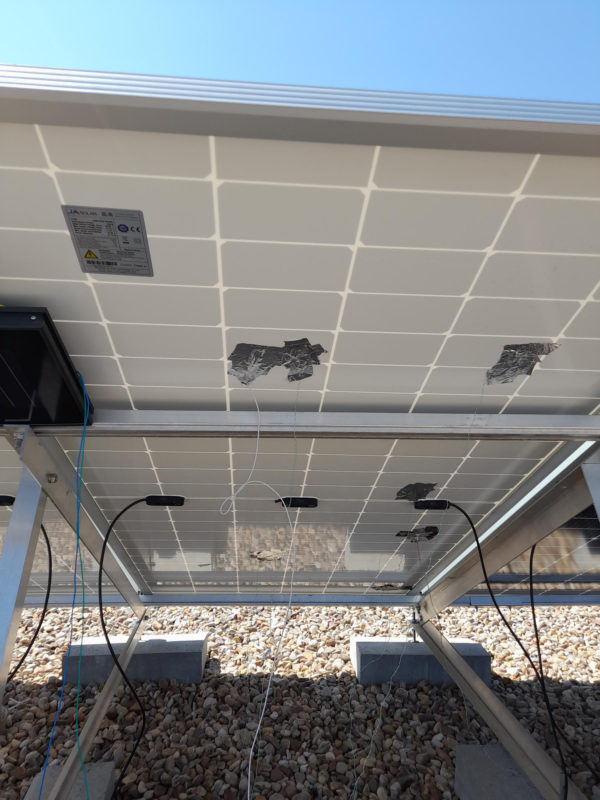
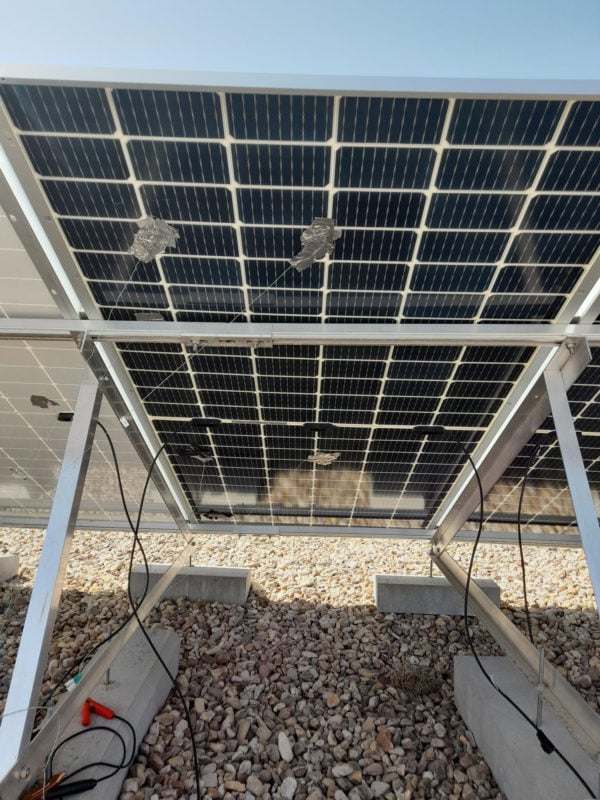
Such instrumentation ensured precise measurement of the irradiance conditions influencing the current production of the PV modules and the temperature gradients across various module sections.
To further our investigation, we introduced intentional shadowing to both monofacial and bifacial half-cell modules. The goal was to simulate and understand the phenomenon we term hotspot mirroring (Hmirror). Preliminary verification of the presence and spread of these hotspots on the module was done using thermographic (IR) camera imaging.
Irradiance and temperature data were collected over a 30-day period, establishing the relationship between irradiance and the temperature reached at each of the measured points. A clear distinction between bifacial and monofacial devices was observed, with behaviour varying depending on the type of day and cloud levels.
For a holistic grasp of the modules’ thermal behaviour, the five thermocouples were strategically positioned at:
A) Shadow-induced hotspot (Hshad);
B) Hotspot mirroring (Hmirror);
C) Upper substring region without thermal anomalies;
D) Lower substring region without thermal anomalies;
E) Central position free from thermal anomalies.
Designated locations of the area shadowed (left) and the area subjected to thermal defects (right) can be visualised in Figure 5.
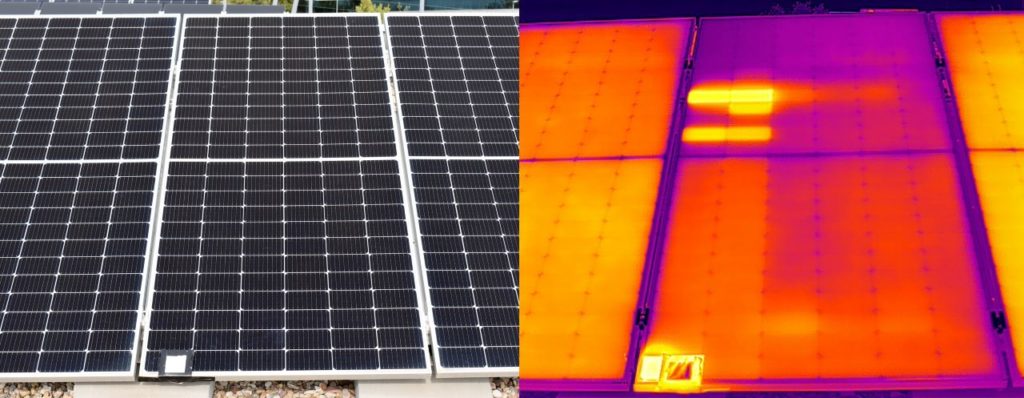
To comprehensively gauge and juxtapose voltage mismatches in both configurations, we calculated temperature gradients using thermocouples judiciously distributed across the modules. Over a span of 30 days, a pronounced correlation emerged between temperature gradients and the irradiance levels each module received. This correlation was particularly evident on cloudless days with peak irradiance. By utilising the central thermocouple (point E) as a benchmark, we calculated temperature differentials, contrasting shadow-induced hotspots and hotspot mirroring effects.
To graphically evaluate the behaviour of each measured point, a chart is presented in Figure 6, which displays two types of days distinguished by the shape of their thermal curve. A clear day is characterised by a smooth curve reaching operational temperatures above 60° C, and a cloudy day is marked by a serrated, sawtooth curve with abrupt changes in the module’s temperature.
Figure 6 illustrates the temperature increase of the hotspots A&B (Hshad and Hmirror, black and red lines, respectively), showing an aggressive rise as the module’s irradiance increases. Beyond a certain thermal stress and irradiance level, the negative voltage reached in the shaded cell is sufficient to trigger the protection diode, leading to the deactivation of the substring. This results in a cooling effect with a degree of thermal inertia, eventually reaching thermal equilibrium with the rest of the module.
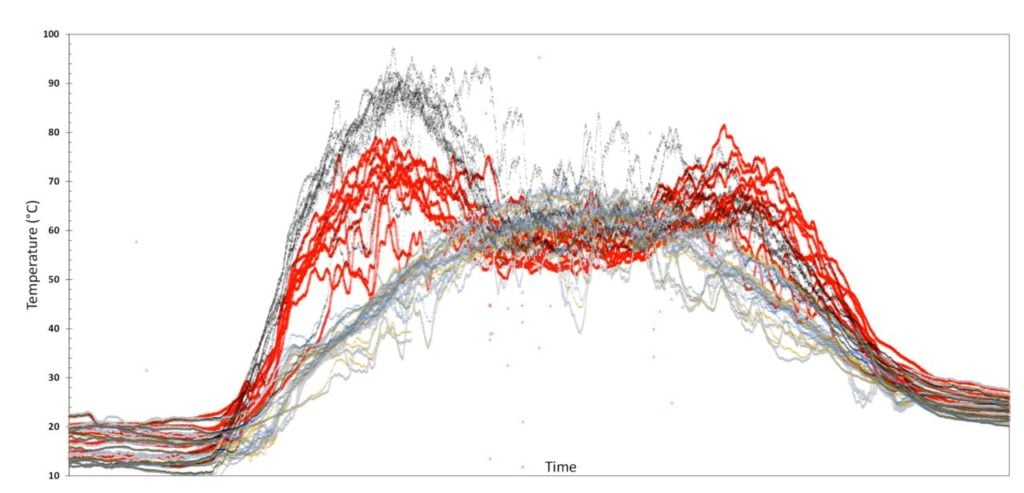
The relative thermal difference between these two hotspots depends on the time of day when it has been inspected, achieving higher thermal values at mirrored hotspots in the afternoon for this shading. However, the results between both types of hotspots are highly dependent on the type of shading performed and the percentage of covered area, such as the number of shaded cells in the module.
A quantitative comparison of the thermal gradients produced between the various inspected points for each technology is presented in the results, providing average and maximum values for the 30-day test period and for the same degree of partial shading. Upon computing maximum values, a peak deviation of 27.0°C for monofacial modules and an even more significant 41.9°C for bifacial modules.
The observed increase in temperature in the bifacial module, compared to the monofacial module, is primarily due to albedo, and therefore, the irradiance reflected by the ground.
The influence of albedo on bifacial and monofacial modules showed distinct characteristics. While its impact on temperature in monofacial modules was marginal, bifacial modules demonstrated heightened sensitivity to changes in ground reflection. This was particularly evident in the traits of hotspots under varying shading conditions.
One of the key aspects that was investigated is the peak irradiance levels that trigger the protection diodes in both monofacial and bifacial modules. The diode’s activation is marked by a noticeable dip in hotspot temperature. It is worth noting that, in contrast to monofacial modules, bifacial ones are also exposed to rear irradiance (Grear) which influences the circulating current and, as a result, accentuates the thermal gradients.
A comparative analysis between monofacial and bifacial modules in Figure 7 reveals distinct irradiance thresholds for diode activation. The monofacial module triggers its protection diode at an irradiance of 770 W/m2, while the bifacial module’s threshold stands at 630 W/m2.
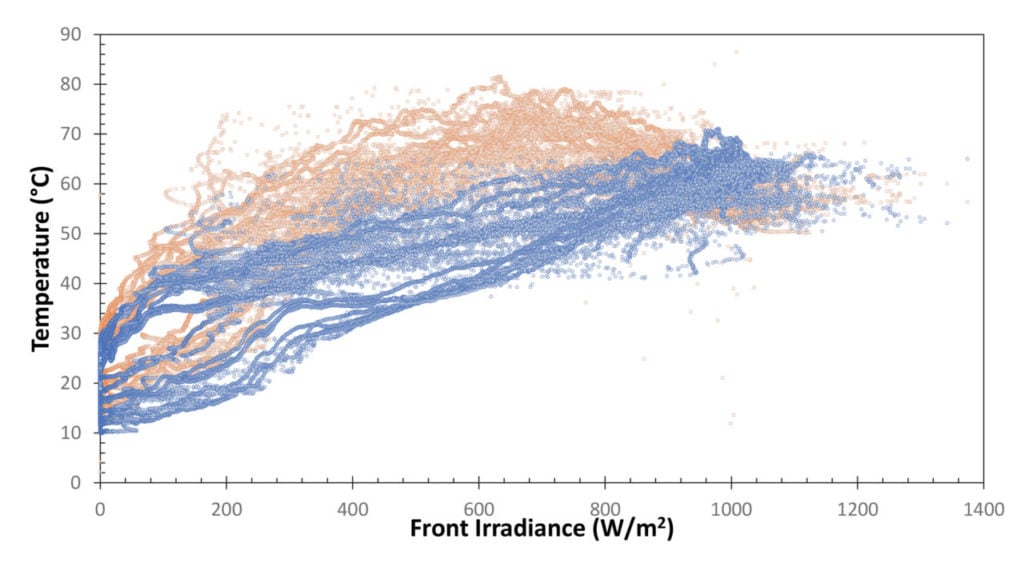
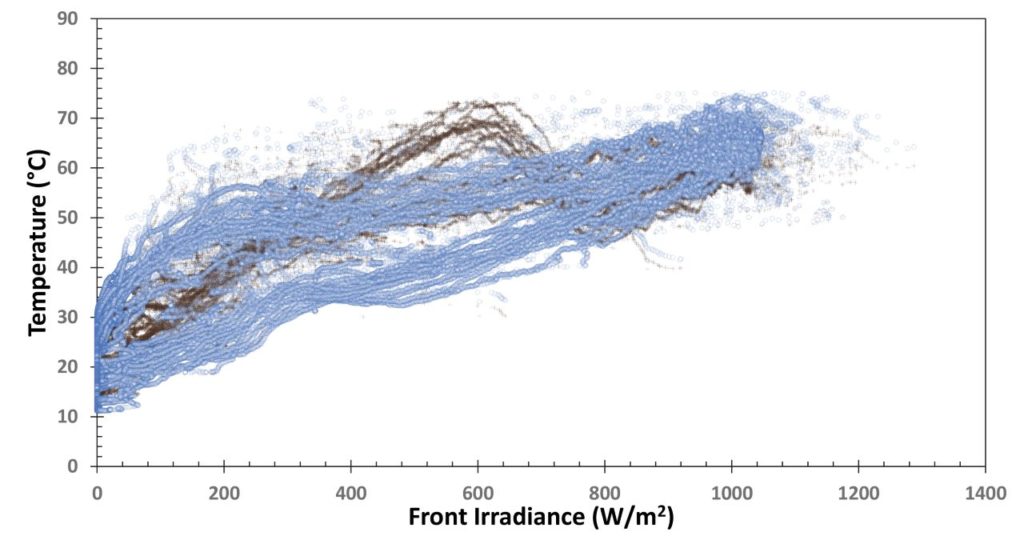
Comparative temperature profiles between Hmirror and the central position for both monofacial and bifacial devices. The thermal profile assessment indicates the point at which hotspot temperature achieves thermal equilibrium with the module. A shift in the profile slope denotes diode activation due to heightened heat generation by affected cells and subsequent negative voltage in shaded areas.
Given the pronounced influence of Grear on the thermal performance of bifacial modules, it becomes imperative to reconsider the standard guidelines for accurate characterisation and defect diagnosis. Our study showcases the limitations of the existing IEC 62446-3 standard, particularly with the omission of the hotspot mirroring phenomenon and the lack of provisions accounting for the rear irradiance’s impact.
Evolution of the governing standards alongside technological advances
For the solar industry to continue its trajectory towards improved efficiency and reliability, it is essential for governing standards to evolve alongside technological advancements. Outdated or incomplete standards could lead to overlooked defects, premature module degradation, and suboptimal PV plant performance, thereby undermining the investments and efforts in promoting sustainable energy sources.
Since the same thermal level for two similar defects is recorded at two distinct irradiance levels, the standard requires normalisation to Standard Test Conditions (STC) of 1,000W/m2. At this juncture, a thermal gradient at a given temperature can be extrapolated to the thermal gradient that would be expected at STC irradiance.

This is a clear example of the current regulatory framework not being up to date, where, pending a future revision, the levels of reflected irradiance or ground albedo are not taken into account when normalising thermal gradients in bifacial technologies.
In this study, we have presented some of the most striking examples, showcasing the results of albedo behaviour and voltage mismatch in the formation of hotspots. However, it is worth noting that the existence of parallel circuits in half-cell technology or rear shading in bifacial technology leads to a series of peculiar consequences under certain conditions.
In Figure 9, we present a similar case observed during an on-field inspection, where it can be seen that the diode is activated only in part of the circuit (left side of the image). The electroluminescence of the modules indicates a partial soldering problem that only affects one of the two parts of the lower substring.
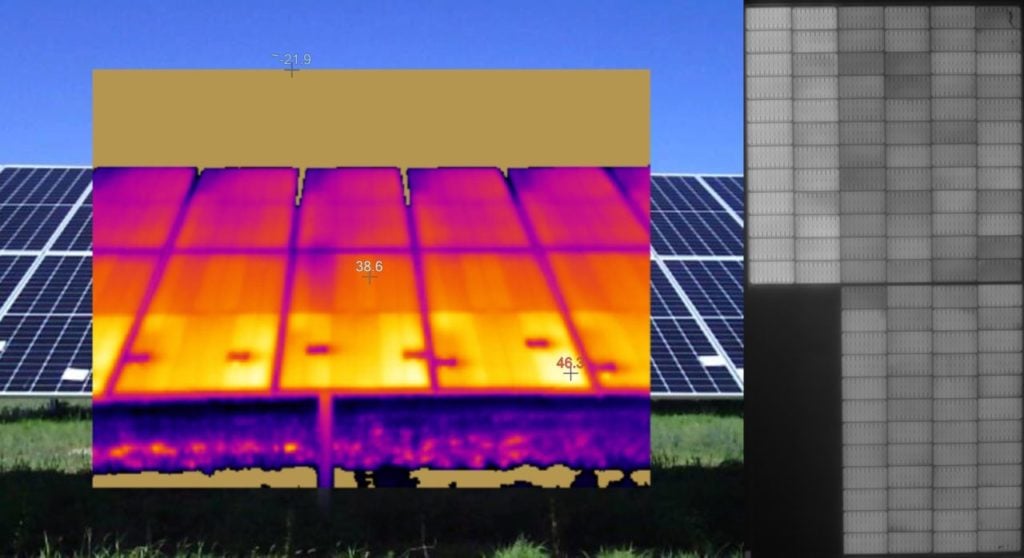
This is why we recommend thorough thermal investigation of modules to enhance international standards, always advocating for the inclusion of a technical advisor in your PV projects.
It is our hope that this research serves as a catalyst for the necessary amendments to the IEC 62446-3 standard, ensuring that it remains robust and relevant for the diverse range of photovoltaic technologies available today. The integration of half-cell and bifacial technologies into the mainstream solar market demands a comprehensive understanding of their unique behaviours and potential challenges.
In conclusion, as the global reliance on solar energy grows, there exists an urgent need for up-to-date guidelines and standards that fully encapsulate the complexities and nuances of emerging PV technologies. Only with an accurate and comprehensive foundation can we ensure the longevity, efficiency and success of renewable energy solutions in the years to come.
References
[1] J. Qian, A. Thomson, A. Blakers, and M. Ernst, “Comparison of Half-Cell and Full-Cell Module Hotspot-Induced Temperature by Simulation,” IEEE J Photovolt, vol. 8, no. 3, pp. 834–839, 2018, doi:10.1109/JPHOTOV.2018.2817692.
Authors
Ignacio J. Fernández is the head of testing and optimisation at Enertis Applus+. With more than 11 years of experience in the PV industry, Ignacio has managed TDD processes, contract negotiations, expert works and QA/QC campaigns related to PV plants worldwide.
Sergio Suárez Sánchez is the global technical manager of testing and optimisation at Enertis Applus+. With more than five years of experience in the PV industry, Sergio is currently taking a PhD in Electronics at UPV/EHU (Spain), an institution involved in the manufacturing of bifacial PV cells, participating in R&D projects as principal researcher, and developing new testing methodologies.
Sofía Rodríguez is the R&D manager at Enertis Applus+. She has worked on the development of innovative defect detection systems in solar photovoltaic modules, coupled with categorisation and classification techniques. She is currently dedicated to the coordination of different lines of research in the company.
José M. Álvarez Fernández is a project manager of testing and optimization at Enertis Applus+. With five years of experience in the photovoltaic industry, José María has managed the execution of QA/QC PV projects, as well as the development of new procedures and services on his department area.
Daniel Villoslada Fontán is a senior technical of testing and optimisation at Enertis Applus+. With more than three years of experience, he has participated in multiple QA/QC and R&D projects. Daniel is currently developing and coordinating QA/QC PV projects in Brazil.
Gustavo Navas is a technology expert whose career began in the oil and gas sector before shifting focus to solar photovoltaic energy. He holds an academic background in chemical engineering and a master’s degree in solar photovoltaic energy. Presently, he leverages his expertise as project manager at Enertis Applus+.