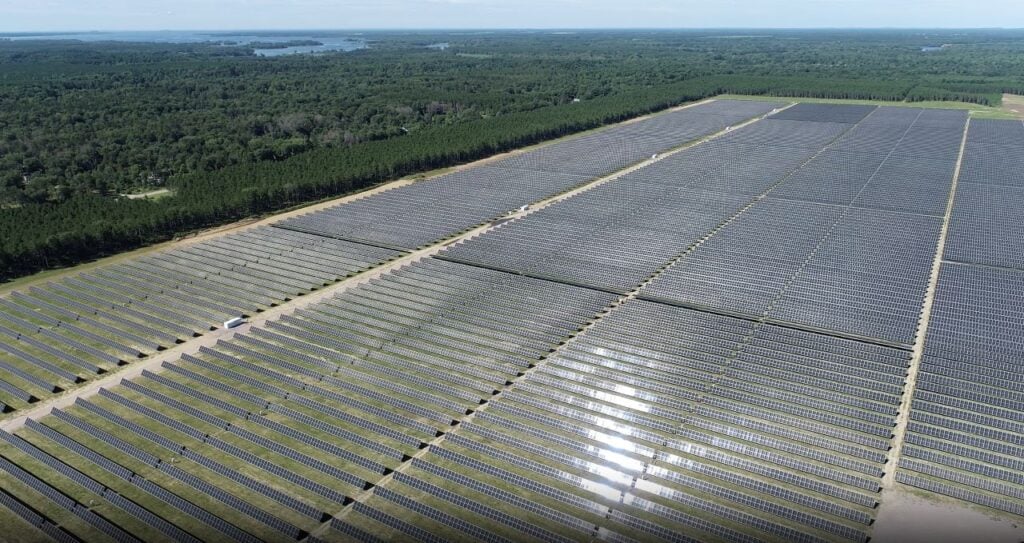
As the solar industry continues to grow and evolve, module blending can offer practical solutions for reducing project cost, particularly as antidumping and countervailing duties (AD/CVD) tariffs could be applied to Chinese products and US domestic content is incentivised. There are strategic considerations for designing and constructing solar sites with blended modules.
Understanding module blending
While it is common to have a mix of different module power ratings within the same type of solar module, module blending specifically refers to using different types of solar modules — varying in manufacturer, cell size, cell count, cell technology and more — within the same project site. This approach is often driven by the need to navigate supply constraints, value economic incentives and realize tariff relief. For instance, with the Inflation Reduction Act (IRA) mandating that products be domestically manufactured or sourced from approved regions to qualify for certain tax credits, blending modules may be a viable strategy to meet these criteria while managing costs effectively.
Unlock unlimited access for 12 whole months of distinctive global analysis
Photovoltaics International is now included.
- Regular insight and analysis of the industry’s biggest developments
- In-depth interviews with the industry’s leading figures
- Unlimited digital access to the PV Tech Power journal catalogue
- Unlimited digital access to the Photovoltaics International journal catalogue
- Access to more than 1,000 technical papers
- Discounts on Solar Media’s portfolio of events, in-person and virtual
Availability and tax implications
Module blending is driven by changing costs and availability of solar modules. Developers might procure modules early to safe harbor a project under favorable tax conditions, then opt for different types as market conditions change and project demands accrue. This strategy helps meet domestic content requirements set by the IRA, qualifying for investment tax credits (ITC) and potentially earning up to a 10% bonus. Once the domestic content percentage is met, project owners can manage costs more effectively by using less expensive, nondomestic modules — thereby reducing tariffs, as well as optimizing capital expenditures and operational efficiency.
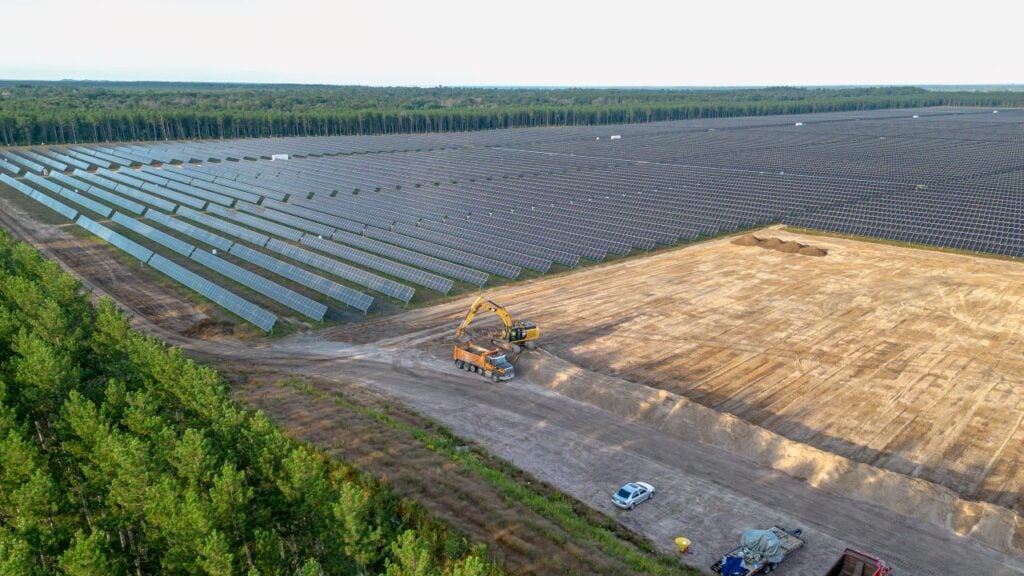
Practical implementation
Implementing a strategy for module blending involves several practical considerations:
- Vendor coordination. Coordinating with different vendors and managing the procurement, design and installation processes for varied modules can be challenging. Each module type might require specific handling, different electrical configurations, particular structural designs and additional engineering efforts to maximize compatibility and efficiency. Because of such complexity, finding the right design partner is essential when considering projects with the potential for module blending. Select reliable partners and establish clear communication channels to manage timelines and logistics effectively.
- Electrical design. Modules may have varying electrical characteristics, necessitating tailored designs for each module type. For instance, if the quantities of each module cannot be split evenly onto different inverters, several considerations come into play to determine an optimized solution. Options include purchasing an additional inverter, using inverters with multiple maximum power point trackers (MPPTs), or combining modules with similar electrical characteristics on a single MPPT inverter. While each can have its benefits and challenges, determining the appropriate solution ultimately requires careful design to get all parts to work together correctly.
- Design flexibility. In blended module sites, it is crucial to design with the ability to make late-stage changes to maintain the project schedule. For example, in a recent project, the final quantities of each module type had not been determined when the trackers and pile foundations needed to be purchased. Burns & McDonnell collaborated with a tracker manufacturer to develop a flexible tracker design, allowing the pile foundation placement and tracker hardware to be compatible with either module type. Once the module quantities were finalized, there was no need to alter the project grading design or purchase additional equipment, avoiding schedule delays.
- Construction. During construction, the installation crew must manage different module types thoroughly to avoid mix-ups from the moment they arrive on-site. Careful coordination on deliveries and laydown yards must be accounted for. Differences in offloading, handling and installation methods should be considered during the project’s design and cost estimation.
- Performance testing. In plants with different modules, it may be beneficial to test each module type separately to establish a baseline for each. In some cases, when different parties provide different module types, separate performance tests may be required by contract. The additional testing can extend the project commissioning schedule and require additional analysis.
- Maintenance. Servicing the site will be more complex over the project’s life cycle due to the need for different procedures, spare parts and cleaning routines for each module type. Even if the relative shapes and mounting of modules may be similar, subtle differences can often cause disruptions in the maintenance process if different products or procedures are required.
- Warranties. Developers must also consider the differences in warranty agreements when looking to blend, as not every module will have the same contract. Like any complexities during construction or installation, warranties must be thoroughly documented and understood during project planning so that the performance of each module type can be monitored adequately and remain warrantable.
Bottom line
Blending modules can be a practical solution to meet project goals and enhance project feasibility in a hot market where module availability is limited. With an engineer-procure-construct (EPC) partner, developers can count on plans for an effective blending process being crafted early on — providing an understanding of regulatory nuances, minimizing rework, and executing the project that achieves optimal performance and profitability.
Martin Gonzalez is an electrical engineer and engineering manager with more than 15 years of experience working with photovoltaic (PV) systems. He has been responsible for the full electrical design of commercial and utility-scale grid-tied PV and battery storage systems, in addition to various other renewable energy projects.
Kyle Burns is a professionally licensed electrical engineer with 12 years of experience in the renewable energy industry. He previously worked on an active NASA mission before pivoting his focus to renewables. Kyle focuses on electrical engineering for EPC PV projects.