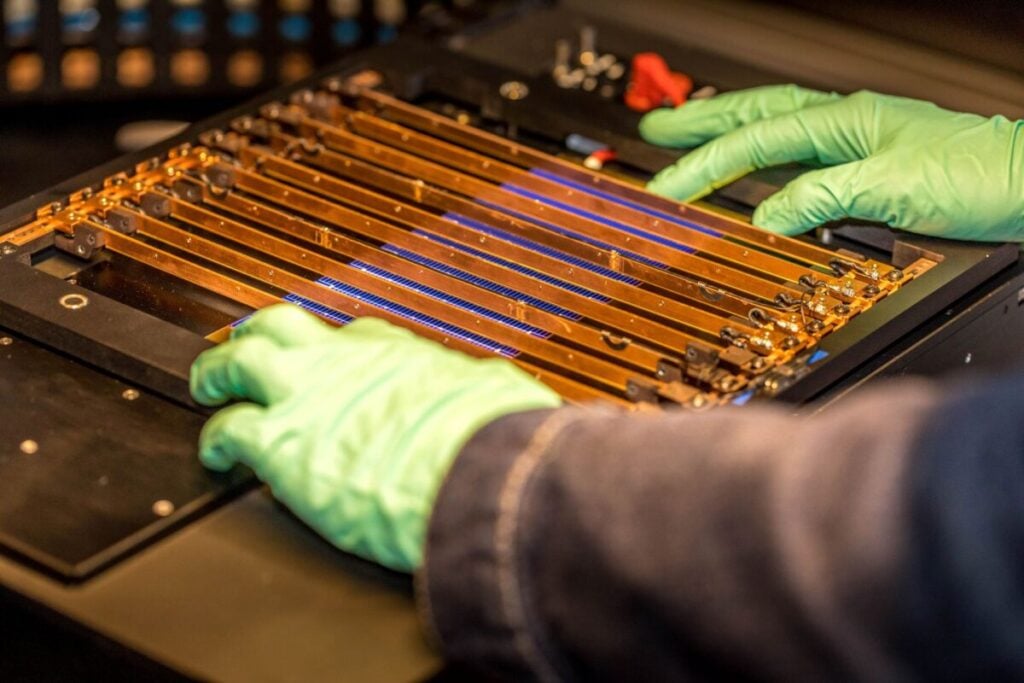
Degradation issues identified in new cell technologies such as TOPCon and HJT underscore the importance of module stability as well as efficiency. Tom Kenning reports on the testing of next-generation modules and efforts to ensure their longevity in the field.
PV modules are generally performing well across the solar industry but recent results from leading test labs suggest that some forms of next-generation modules are showing surprising levels of degradation in just a few years. The focus tends to be heavily weighted towards efficiency when a new module comes on the scene, but researchers from the likes of the University of New South Wales (UNSW) and Kiwa PVEL have issued warnings that concentrating on the long-term stability of a module is just as important. Moreover, if new innovations are brought into mass production before thorough testing is complete, the size of the industry today means that multiple gigawatts of suboptimal modules could be shipped before the necessary corrections are made.
Unlock unlimited access for 12 whole months of distinctive global analysis
Photovoltaics International is now included.
- Regular insight and analysis of the industry’s biggest developments
- In-depth interviews with the industry’s leading figures
- Unlimited digital access to the PV Tech Power journal catalogue
- Unlimited digital access to the Photovoltaics International journal catalogue
- Access to more than 1,000 technical papers
- Discounts on Solar Media’s portfolio of events, in-person and virtual
Nonetheless, the latest ‘PV Module Reliability Scorecard’ from California-based lab Kiwa PVEL painted a positive overall picture for the industry. Given that standard IEC tests allow for 5% degradation in testing, it is encouraging for stakeholders that Kiwa PVEL’s tests are not only three times longer than the IEC’s but they also found 84% of bills of materials (BOMs) had less than 2% degradation. This included positive results for passivated emitter and rear cells (PERC) as well as next-generation technologies such as tunnel oxide passivated contact (TOPCon) and heterojunction technology (HJT) modules.
The caveat is that there are examples of poorly made next-generation modules. As a result, the ‘Module Scorecard’ has had to balance its tone between celebratory and cautionary.
“We’re seeing more outliers, and the range of test results is getting larger than what it was in the past,” says Tristan Erion-Lorico, VP of sales and marketing at Kiwa PVEL.
In the Scorecard, 66% of all manufacturers experienced at least one testing failure, which is double the lab’s normal expectation. “Now the stakes are even higher, because we’re shipping materials on the gigawatt scale, rather than shipping a couple of megawatts of defects,” says Erion-Lorico.
Along similar lines, research from Sydney-based lab UNSW in 2023 revealed reliability challenges that, if not properly addressed, could result in a performance decline of up to 50% in TOPCon and HJT solar modules within only a few years of operation. This was due to the solar cell metallisation’s sensitivity to contaminants and, to a lesser extent, the solar cell’s sensitivity to particularly ultraviolet light. Bram Hoex, professor and deputy head of school (Research) of the School of Photovoltaic and Renewable Energy, UNSW Australia, says that most failure modes in n-type modules can be avoided by having the right bill of materials.
However, there are no 25-year-old TOPCon or HJT modules that are representative of the current technology to prove the longevity of either technology in the field.
TOPCon corrosion concerns
Unlike previous generations of solar cells, the key concern for TOPCon degradation lies in its front metallisation. The paste used contains a large quantity of aluminium particles to improve contact with the boron-diffused emitter, which makes the paste sensitive to corrosion.
There have been rapid developments in this form of paste, and although the corresponding sensitivities to corrosion oscillated between better and worse for each development, these changes were not always picked up in manufacturing companies’ standard quality controls.
“That’s where the big risk lies,” says Hoex. “The Tier 1 companies knew what was happening; however, they did not disclose this information because it was not in their best interest to do so. They accept the sensitivity at the cell level and use a glass-glass module with high-quality encapsulants, ensuring a stable PV module.”
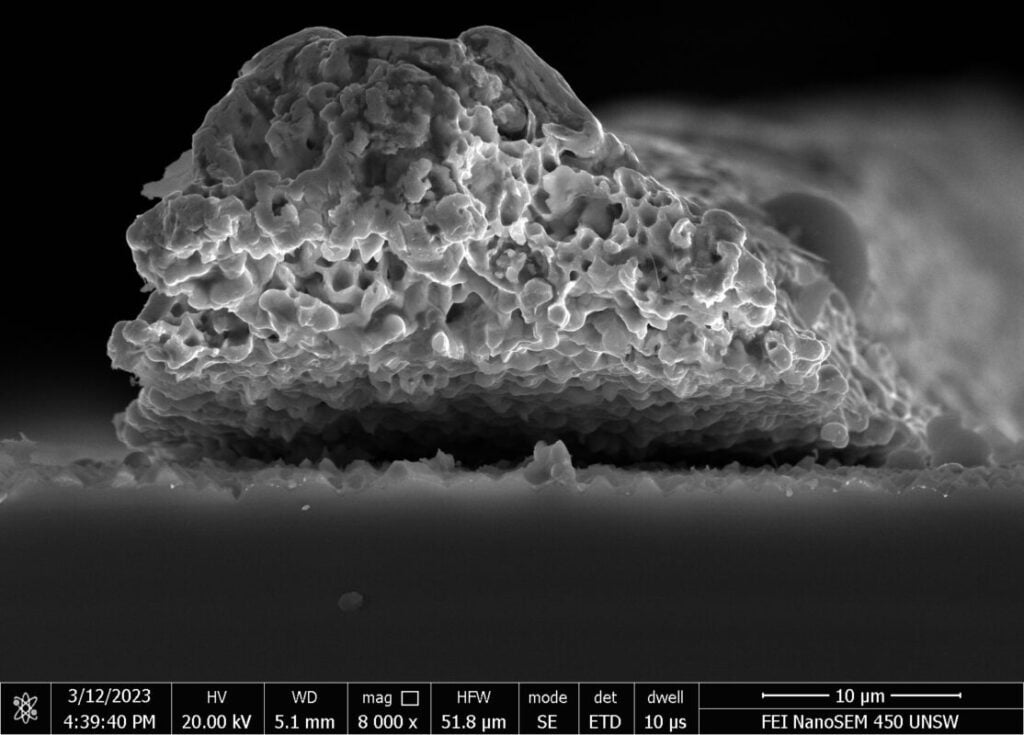
The problem becomes most pressing if, without any knowledge of the differences in cell sensitivity, new production lines or newcomer manufacturers start producing TOPCon modules under the assumption that it is similar to the older PERC technology.
Academics have broadcast for years that n-type technology such as TOPCon is more stable than p-type. However, this greater stability referred to degradation regarding boron-oxygen defects and light and elevated temperature-induced degradation (LeTID), but other potential issues such as corrosion-sensitive metallisation were overlooked, says Hoex.
A further drawback is that metal-related degradation is very likely to speed up when there are multimode failures. For example, if PID – corrosion caused by sodium penetrating a solar cell – is combined with humid conditions, this can cause further problems. These issues would likely not be picked up in a standard PID test of just 200 hours. However, a PID test followed by a normal damp heat test might pick this issue up.
Other than metallisation, certain additives in polyolefin elastomer (POE) can also be very detrimental to a TOPCon cell, while excess hydrogen resulting in an increase in surface recombination, typically referred to as “surface-related degradation”, can also cause degradation.
TOPCon also performed poorly in power degradation compared to other modules in Kiwa PVEL’s Module Scorecard, which found five TOPCon BOMs recording failures versus just one PERC BOM, substantiating the UNSW findings. Nonetheless, the many TOPCon modules tested with less than 2% degradation suggest these failures are not inherent to the technology.
In detecting problems, speed is of the essence given that innovations in PV tend to make it into end products within six months of development, meaning there is limited time to test for new defects.
“TOPCon cells and modules are more complex than PERC, and your choice of encapsulant, flux and metallisation are more critical than with PERC,” says ErionLorico. “In the late days of PERC, you could basically throw whatever you wanted at them and they would perform fairly well. Now, if you say, ‘Well, I’m just changing the encapsulant, like I did on my PERC modules’, the wheels might fall off of your TOPCon modules, because that processing window is tighter.”
Erion-Lorico calls for more due diligence on material use, both at cell and module level, to ensure reliability. Without this, the risks of underperformance are higher for TOPCon and HJT than they are for PERC modules, which tend to remain robust from a material selection standpoint.
“If one manufacturer’s switch in aluminium paste for TOPCon modules is spread across the industry while testing is still ongoing and it takes six months for the industry to realise it’s not a good idea, manufacturers might have shipped millions of modules in that time,” says Erion-Lorico. “I don’t blame them though. They’re not making any money right now, and we’re trying to squeeze that price down to as low as possible while also saying you’ve got to keep the reliability high.
“They’re motivated to change the encapsulant and change the pastes etc., so that they can lose less money; not to make money but lose less money. So, as an industry, we are not driving quality in the right direction, and we’re in this current race to the bottom.”
While there are conflicting interests between the industry motivation to bring in money-saving innovations as quickly as possible versus the reality that testing to replicate 25 years in the field takes time, Erion-Lorico calls for a return to patience and fully vetting new designs through both internal and external reliability testing before modules are shipped.
“I don’t know if that’s being followed and I don’t know if the price of modules today inspires manufacturers to do that,” he adds. “Quite the opposite.”
TOPCon is “not intrinsically unstable technology”, but it runs the risk of getting a bad name, says Hoex – adding: “If you are not aware of these failure modes and do not take the right precautions, then you might end up with these failures as we demonstrated by a 65% reduction in performance after only 1,000 hours of damp heat testing. That’s a shocking result and it was comparable to what we see at cell-level testing.”
JinkoSolar on TOPCon testing needs
Dr Menglei Xu, R&D director in the solar cell department of Chinese manufacturer, JinkoSolar, says that in the wider TOPCon sector, many attempts at optimisation of materials had been made to improve the quality of TOPCon products, for example, with improvement at the silver paste, passivation film, metallisation design and even the firing control process levels.
“At this moment, for our [own] TOPCon products, we do see that key technical designs and the critical controlling requirements have been [established] before launching new products to the market,” he says. “This is a must.”
Questioned about the warnings about manufacturers putting out products before thorough testing has occurred, Xu says that before integrating any new technologies, JinkoSolar will perform not only standard reliability, stability and field tests at cell and module level but also its own bespoke studies to assess degradation risks.
However, Hoex remarks that there is little incentive for manufacturers to share their findings of defects with competitors.
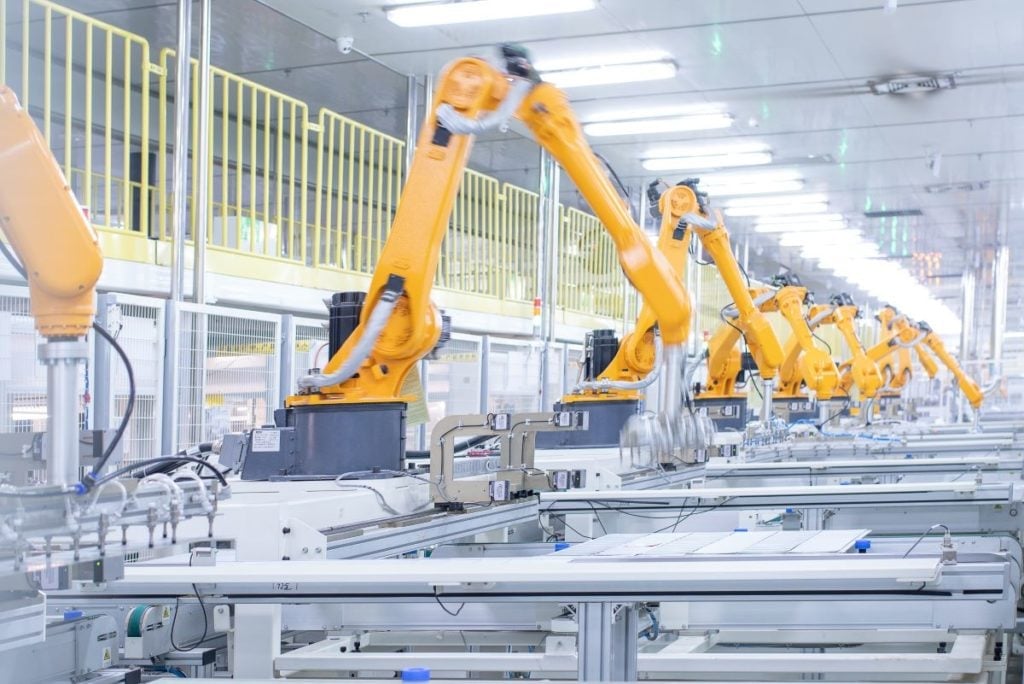
With JinkoSolar having just shipped the jaw-dropping number of more than 100GW of its Tiger-Neo n-type TOPCon modules, Wally Zang, head of JinkoSolar’s technical service centre, was able to provide robust reliability and performance testing results. For example, it found degradation after one year of just 0.5-0.7% with Chinese state-owned lab CGC, and degradation of just 0.6-0.9% with another state-owned lab, CPVT, for its TOPCon modules.
JinkoSolar also performed UVID tests on its TOPCon modules with third parties Kiwa PVEL and RETC to evaluate the potential deterioration in PV module performance after extended exposure to ultraviolet radiation. The results showed a degradation rate of 3.52% after 120kWh/m2 of UV exposure by PVEL and 2.83% after 220kwh/m2 of exposure by RETC (Figure 1).
LECO and ME: Solving the TOPCon aluminium issue
UNSW and Kiwa PVEL found that the number one cause of degradation in TOPCon is the use of aluminium in the front silver paste, but two technologies have been introduced to attempt to solve this issue.
Several years ago, major Chinese PV manufacturer JinkoSolar, saw the potential issue of front-side metal paste on cell or module reliability in its R&D phase, but it now uses its bespoke Metal Enhancement (ME) technology to enable the use of low-aluminium-content or even aluminium-free front silver paste for its TOPCon cells.
As a result, JinkoSolar has “no issue at all” with the potential corrosion issues related to aluminium use and no special encapsulation is needed, says Xu. Moreover, by solving the issue directly at the cell level, ME has helped improve the overall reliability performance of the module.
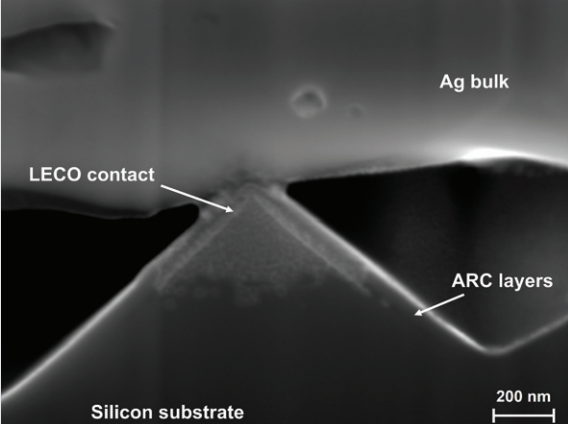
“When we noticed such issues at the R&D step, we had a lot of collaboration with the metal paste suppliers,” says Xu. “We did a lot of paste optimisation and process optimisation, and at the module level we also developed some encapsulation technology and the materials to further improve the reliability. For example, the damp heat performance is getting better by using improved silver paste as well as better encapsulation material.”
Right now, JinkoSolar uses ME for all large-scale production of its TOPCon products and it has seen an over 0.3% improvement in efficiency after integrating ME into its TOPCon cells with space for even further improvement in the frontside efficiency. Xu, however, was unable to disclose more detailed information on the specifics of the ME technique at this stage.
Along similar lines, UNSW produced a paper recently showing that using the paste for TOPCon in combination with laser-assisted firing decreases sensitivity towards sodium-related degradation as it enables the paste to be used without aluminium and still get a strong contact with boron. This technique, known as laser-enhanced contact optimisation (LECO), was developed by German firm Cell Engineering (CE) initially to improve the contacts in underfired solar cells. South Korea-based solar module manufacturer Hanwha Qcells now owns the intellectual property rights to LECO technology, having acquired CE.
While Hanwha declined to offer further comment on the technology, the technique is still new and UNSW has identified some concerns that Hoex is unable to disclose at present, which suggests laser-assisted firing may not spell the end of these reliability concerns based on metallisation.
Nonetheless, Hoex claims of LECO that it is “the biggest innovation in solar cell manufacturing in the last couple of years”.
Conservative BOM key for HJT
Some of the challenges for HJT technology also lie with metallisation, but the metal pastes used for HJT are quite different from those used for TOPCon. When it comes to screen-printed metallisation, curing at higher temperatures allows for far more organic matter to be burned off, and the pastes used for HJT can only be cured at 200 degrees Celsius or less, as opposed to 700 degrees or more for TOPCon.
As a result, in HJT, some of the binding materials used for the adhesion of the contact include non-silver compounds, which may cause chemical reactions that result in the contact becoming more porous or even detached.
Some manufacturers have historically struggled with the low-temperature soldering required for HJT modules.
However, thermal cycling testing by Kiwa PVEL for HJT modules showed marked improvement in the past year, suggesting that those manufacturers tested had overcome these soldering issues.
The soldering flux used to apply the metallisation can be “quite aggressive”, says Hoex, with components from the flux actually reacting with the heterojunction paste, which can cause heightened sensitivities and similar severe failures to those of TOPCon.
The soldering flux can even interact with the transparent conductive oxide (TCO) which is used to increase the lateral conductance of the front and rear of the HJT solar cell. Moreover, the industry is moving away from indium tin oxide (ITO) due to the scarcity of indium, despite it being known that alternative layers are typically more sensitive.
Moisture ingress worries While soldering has improved, Kiwa PVEL found a wider range of damp heat results in HJT.
“PERC modules really don’t like moisture,” says Erion-Lorico. “TOPCon modules hate moisture even more, and HJT modules really, really hate moisture. That’s where we’re seeing that the results are trending down.”
Kiwa PVEL has found that moisture ingress into the laminate causes higher corrosion in TOPCon than it did PERC and even higher still in HJT.
Heterojunctions are also very sensitive to contamination during the manufacturing process, while HJT cells are also sensitive to temperature and illumination and can be described as “metastable”, meaning that they have the potential to get better or worse over time; Hoex believes the full impact on the lifetime yield is not fully understood. Likewise, HJT’s sensitivity to UV degradation also raises questions about long-term stability that need to be further investigated.
However, unlike the rapid expansion of TOPCon, only a few manufacturers are putting large volumes of HJT products onto the market. Most are quite conservative in their bill of materials, which leads to decent levels of stability, says Hoex.
For example, Chinese firms Huasun and Risen, the largest global producers of HJT, are both conservative with their BOM but are also able to demand a premium for their products.
Hoex is more concerned about the potential “mass application” of heterojunctions in the future since, in his view, the paste is even more sensitive than TOPCon paste.
HJT built on firm Panasonic foundations
PV Tech Power consulted Huasun about whether it was concerned about the potential for new players in HJT manufacturing to stray from advised conservative BOMs and damage the reputation of HJT products.
Christian Comes, director of business development at Huasun Energy, says that HJT technology is built on a firm foundation with proven and historical durability demonstrated by the Sanyo Panasonic modules that were invented as far back as 1993 and introduced to the market in 1997. This length of availability allowed producers to discover failure mechanisms that may occur over a long period and cannot be seen in testing. Steps could then be taken to mitigate these failures.
Comes quotes a UNSW scientist recently stating that the Sanyo Panasonic modules were some of the most reliable and durable modules that UNSW has ever tested, despite using production methods available a decade ago. The warranty cases published by Panasonic numbered fewer than 50 pieces per million sold – even decades after introduction. Moreover, these production methods for HJT have also kept on improving to the present day.
Comes agrees that the main way to make mistakes with HJT is to tamper with the BOM, so if all producers stick with a conservative BOM there is little to worry about. Given the stable base offered by Panasonic’s experience, Comes believes it is unlikely for newcomers to come in “out of the blue” without knowing how to produce HJT modules well.
Most high-efficiency modules use sophisticated cell passivation, but those passivation layers are typically the parts that can be negatively affected by the environment and cause degradation. As a result, Comes again stresses the importance of a conservative BOM to ensure the prevention of UV and water ingress.
“If you are trying to solve the effect of the water ingress, you need to solve all of the problems that happen when water is inside, and some of them are not well understood even for TOPCon,” he says.
Allowing this ingress can then lead to what he calls a “whack-a-mole” approach where the solution to one issue may cause a different issue elsewhere in a repetitive cycle of new failure modes, so it is advised to prioritise that ingress does not happen from the offset.
HJT touted for perovskite future
Comes claims HJT technology has a unique level of robustness and insulation from the environment, such as blocking UV and humidity ingress, as long as two factors are met. Either conservative BOMs must be adhered to, or whenever there are changes to the cell, a very strict battery of testing must be carried out to ensure that the robustness either remains the same or improves.
As a result of this protection, Comes expects a bright future for the technology in line with increasing demand for the newest solar energy innovations.
“We think that HJT moving forward is going to be the key technology because that very durable and very well-protected module and cell structure is going to be the substrate for tandem heterojunction with perovskite in two or three years from now,” he says. “And that will require very good isolation from the environment, such as the isolation that HJT is giving.”
Enter zero busbar
Erion-Lorico also mentioned the new trend of zero busbar modules for TOPCon, which were displayed widely at the SNEC exhibition this year in China, as having the potential to cause a wide range of testing results as some manufacturers struggle to get the technique right.
“I think we’re going to see some pretty ugly zero busbar thermal cycling results in next year’s scorecard,” he says. “My concern is that because it saves silver and you save [money] per watt, you can raise the module power up by a power class that’s going to push manufacturers to start producing gigawatts of zero busbar before they confirm that the soldering is adequate.”
Huasun’s Comes says zero busbar “is the most important innovation of the last five years”, but it would require very careful damp heat and thermal cycling testing.
Looking at the overall picture for nextgeneration PV modules, particularly HJT and TOPCon technology, Hoex concludes: “The main thing I’m saying is stability is as important as efficiency. So, if your degradation rate increases significantly, then your high efficiency is worth nothing. You lose all the benefits. If your degradation rate goes up, then your LCOE may even be higher than a stable PERC module.