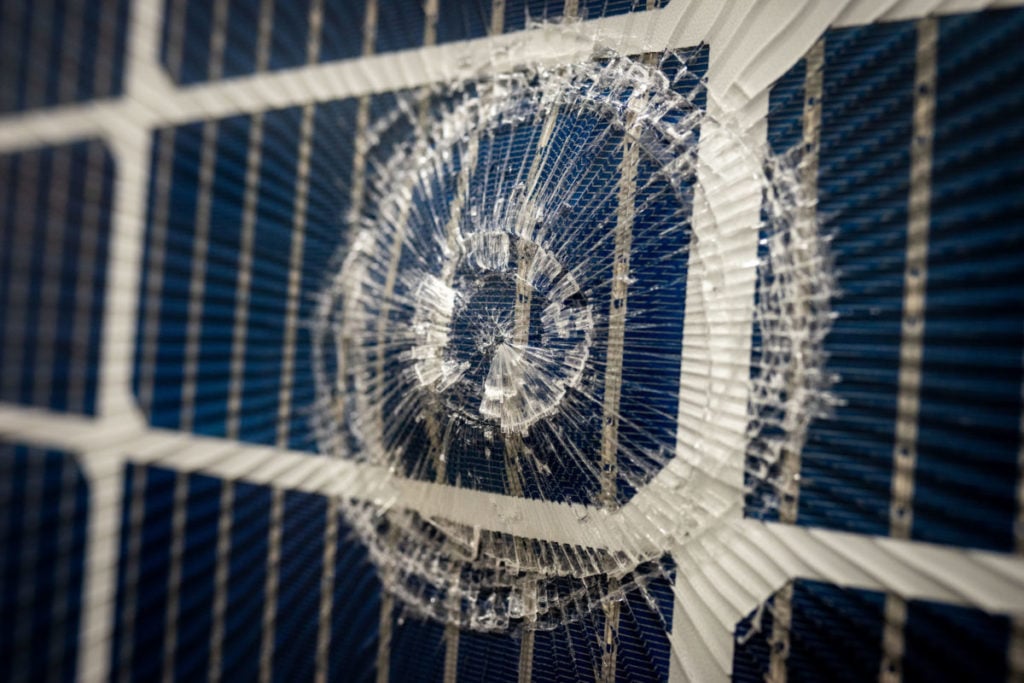
The growing trend of building larger and thinner PV modules has contributed to an increased number of breaks in module glass at utility-scale solar projects, although there is no single contributing factor more influential than the others.
These are the conclusions drawn by the National Renewable Energy Laboratory (NREL), which published its findings in a paper assessing the impacts of module design on glass vulnerability titled ‘Tough Break: Many Factors Make Glass Breakage More Likely’.
Unlock unlimited access for 12 whole months of distinctive global analysis
Photovoltaics International is now included.
- Regular insight and analysis of the industry’s biggest developments
- In-depth interviews with the industry’s leading figures
- Unlimited digital access to the PV Tech Power journal catalogue
- Unlimited digital access to the Photovoltaics International journal catalogue
- Access to more than 1,000 technical papers
- Discounts on Solar Media’s portfolio of events, in-person and virtual
The report identifies “spontaneous breakage” – cracks that emerge across panels with no clear point of origin such as a hailstone – occurring more often in thinner and larger modules, particularly those using sheets of glass thinner than 3.2mm, or “usually” as thin as just 2mm.
A range of damaging factors
The report notes that heat treatment in the glass sheet manufacturing process can “keep small flaws from growing” by increasing the compression of the sheet. It points out that 2mm glass tends to have a lower surface compression than 3.2mm glass, but the idea that 2mm glass cannot be tempered, which would increase its compression, is a “common misconception”. The report said with the proper equipment, 2mm glass can be heat-treated to produce fully-tempered glass or even more resilient safety glass. But this is not the only factor contributing to breakages.
The growing size of modules could be a more influential factor on breakages; when loaded with wind or snow, a bigger module has to support a greater mass. This can be intensified by the nature of the module mounting. For glass supported on its edges, these edges bear a greater load in bigger modules; for glass supported at four mounting points, these mounting points have to carry a greater load. This imbalance in the shape of module supports has led NREL to dub some of these panels “big floppy modules”.
However, the report again suggests that this alone is unlikely to have contributed to a significant increase in module faults, arguing that “size alone is not enough to explain recent breakage problems”. Similarly, the report notes that the wind and thermal expansion endured by the glass components of module can cause them to come into contact with metal mounting frames, damaging them further and contributing to cracks, but that this is also “not enough to explain recent breakage problems by itself”.
Collecting data and changing purchasing trends
In response to this range of contributing factors, the NREL authors say they are completing tests to detect modules vulnerable to breakage at low loads, and collecting damaged modules to better inform future conclusions. The report calls on suppliers to better communicate which specific weaknesses a product can suffer from, and tasks module buyers with acquiring modules with fewer of these risk factors.
This year has seen considerable research into module resilience, with a record number of “top performers” recognised by Kiwa PV Evolution Labs’ annual module reliability scorecard.
In the US, striking hail damage at the Fighting Jays project in Texas raised questions about the ability of PV systems to resist extreme weather events, which led to the Department of Energy and kWh Analytics launching a US$2.4 million initiative to enhance the resilience of PV projects.
PV Tech Premium examined the current module quality and reliability landscape in a long-read earlier this year.
The full NREL report can be read here.