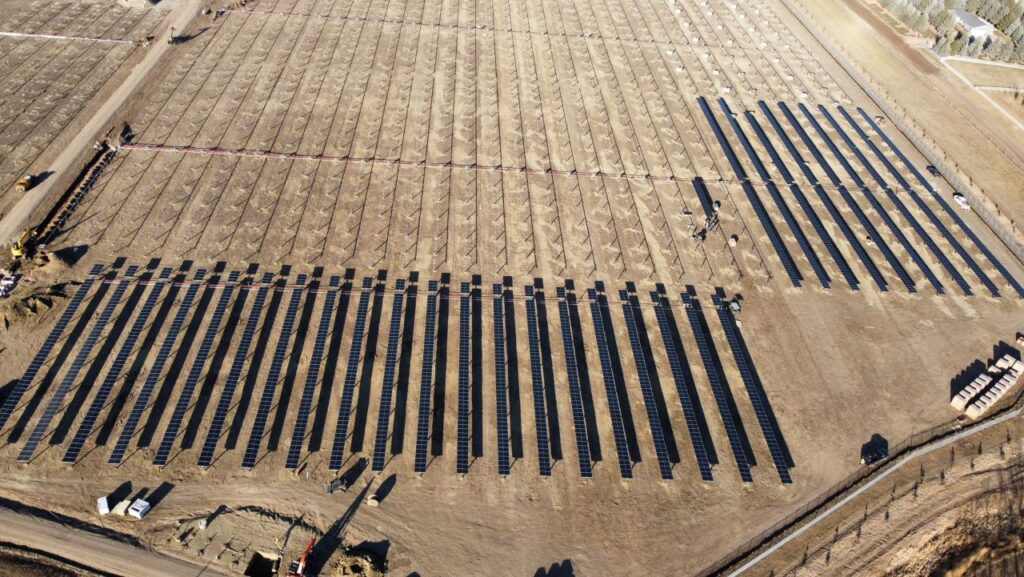
The foundations of a solar project offer multiple opportunities for driving down system costs. Arash Yazdani of PRI Engineering describes some of the key steps involved in investigating the specific conditions of a project site and developing a foundation design that will stand the test of time.
Unlock unlimited access for 12 whole months of distinctive global analysis
Photovoltaics International is now included.
- Regular insight and analysis of the industry’s biggest developments
- In-depth interviews with the industry’s leading figures
- Unlimited digital access to the PV Tech Power journal catalogue
- Unlimited digital access to the Photovoltaics International journal catalogue
- Access to more than 1,000 technical papers
- Discounts on Solar Media’s portfolio of events, in-person and virtual
The foundations of a PV power plant are quite literally that – the footing on which a project is built and, as such, a vital ingredient in its longevity and profitability, or otherwise. The foundation system provides the primary interaction between the site and its specific conditions, and the PV project’s racking system and modules. Any movement or failure of this component will affect the entire system, leading to costly change orders and overruns during construction and even failures during operation.
Optimal foundation design is therefore a potentially untapped source of savings in the overall costs of a PV project. Doing it correctly and thoroughly upfront may take a little more time and initial investment at the outset, but it’s an investment that will provide an outsized value in proportion to the costs avoided or saved further down the line.
It is critical for proper foundation design to take into account the specifics of a project site, enabling the structure to be optimised in line with the many variabilities of the subsurface conditions found on the site. Often designers employ a “one size fits all” philosophy to foundation design, but unlike manufactured materials, you cannot order set soil properties; rather, your foundation must be designed to match the site’s specific subsurface conditions. Optimising as the site varies could allow you, for example, to reduce the overall length or size of the foundation in areas where denser soils or other more favourable conditions are encountered. As typical solar farms contain a large number of foundation elements, the cost savings which could be gained from the minor optimisation of a pile length of just 0.3m could run into millions of dollars.
Site-specific design
When designing a solar project, we let the site determine the foundations and layout we need. An out-of-the-box solution or kit may work well on smaller sites with low variability. In contrast, large-scale solar projects require intelligent geotechnical design to minimise the upfront investment and decrease the time until your return on investment. Key considerations in finalising a design are the climate found in the project area, the project’s scale, site subsurface conditions and the optimal type of foundation that will best suit these parameters.
Climate considerations
Before investigating a site’s soil conditions, we typically analyse the worst-case scenarios relating to a site’s climate. For a solar project, three primary climate-related considerations can result in minor to severe damage: frost and wind uplift, snow accumulation on the system, gravitational loading (or the dead load) and seismic activity. Proper consideration of the loading stresses these can put on solar racking foundations can help prevent costly repairs or a complete rebuild.
For frost and wind uplift, the design principles that prevent them are largely the same. When frost or wind uplift loads increase, the two main ways to compensate are to embed the foundation deeper or increase the size of the foundation.
Other measures to counteract frost uplift include the installation of a frost sleeve, which can help reduce the frost uplift to 30% and is an economical solution in a site with weak soils or where long colder winters are anticipated.
Gravitational loading is the result of the weight of the racking system and, in colder regions, resting snow bearing down on the foundation. Both can lead to problems if there is variation in the movement of adjacent piles as some settle or heave more than the adjacent foundation elements in the same table. This can lead to stresses on the racking, and permanent deformation in the structural members and even the PV modules themselves.
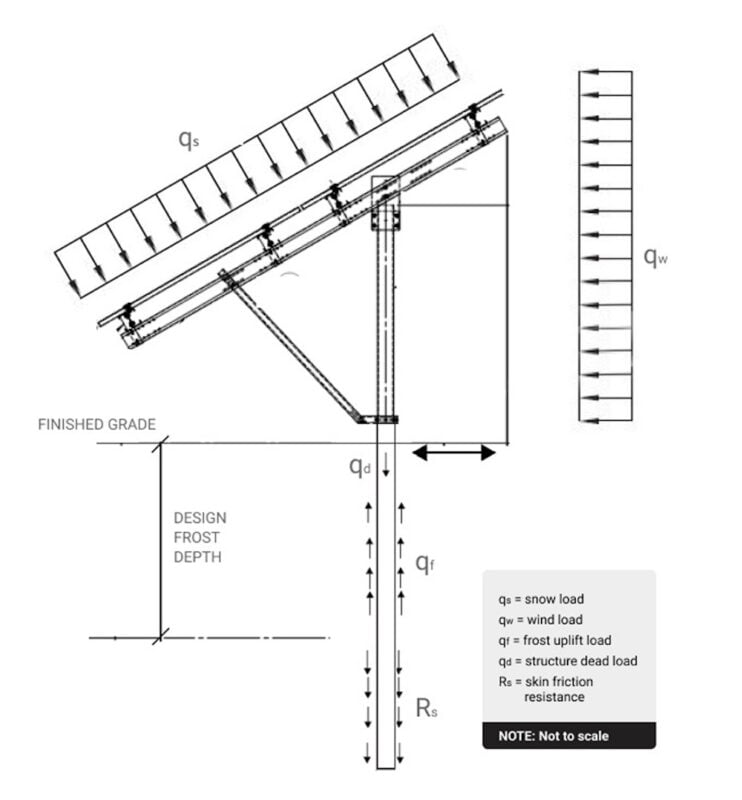
Seismic loading is not a concern in all areas, and even for projects in regions with regular seismic activity, the risk is still relatively minor due to the light weight of the structures. The main difference between seismic loading and gravitational loading and wind and frost uplift is the cyclical oscillations over an extended period that may result in fatigue, particularly if using aluminium for structural members. Since PV racking structures are relatively light and low to the ground, seismic activity typically does not exceed the racking tolerances, except when auxiliary equipment such as combiners, inverters or even motors for single-axis trackers are attached to the foundation element. As with other loading, larger foundations help compensate for seismic loading.
Project scale
As the size of a solar project increases, the potential for site variations increases as well as possible complex subsurface conditions. Larger projects also have more foundation elements, meaning more risk. But they also mean larger budgets which means budget allocations to engineering could be greater.
For a PV system above 600kW, a comprehensive geotechnical investigation is necessary. In addition to soil testing onsite, we would include in-situ pile testing and refine the recommended designs to the particular conditions on-site. This enables solar project developers to reduce steel costs and have greater confidence in the performance of the foundations across the site.
Geotechnical survey
With respect to your ability to control a construction project, the most variability will frequently come from the earthworks. This variability is often attributed to natural occurrences, due to depositional processes such as erosion, glaciation, volcanism, or different fluvial processes that create conditions that can alter designs in a very drastic fashion.
Variability typically means risk, and a geotechnical investigation completed by a qualified geotechnical engineer, familiar with the local geological depositions and these materials’ engineering properties, is the most effective way to complete an appropriate foundation pile design for a racking system and thus mitigate and manage site risks. Results of detailed investigations should be included for potential contractors at the bidding phase as it will typically mean you will be getting more competitive pricing and taking on less risk.
Inadequate geotechnical investigation and foundation testing prior to the bidding phase could lead to highly complex subsurface conditions not being discovered. These unknowns typically arise due to the variability of site subsurface conditions that were not discovered due to minimal information being collected, or when supplemental information may have been needed but was not collected – typically due to budgets, but also due to schedule constraints or just an overall misunderstanding of the risk. Unknowns can lead to change orders during construction, which will increase costs.
Subsurface conditions can vary drastically from site to site, and depending on the subsurface conditions, many of the design considerations may change accordingly. Some conditions that must be determined are the overall gradation of the site soils to develop an understanding of the required analysis requirements and engineering properties for encountered materials. The presence of obstructions or other deleterious materials such as organic-rich materials, which are traditionally problematic for all types of foundations, must be assessed. And the overall excavation/boring stabilities and groundwater conditions must also be assessed.
These can influence several parameters relating to the design of the foundation, such as the adfreeze pressures, frost design depths, corrosive nature, overall resistance to design loads, and constructability. All of these parameters are affected to a significant extent by the site’s soil classification, which broadly falls into two categories: coarse-grained (predominantly sands and gravels) or finegrained (predominantly silts and clays).
As an example, with adfreeze pressure – the pressure generated from water freezing within the pores of the soil – a coarse-grained material generally holds more water in its pores because of a higher porosity and therefore can have a higher adfreeze pressure compared to fine-grained material which has a lower porosity and therefore a lower adfreeze pressure.
Soil composition also affects frost penetration depths and thus vulnerability to frost uplift: gravelly sands, which are more porous and consequently have a higher void ratio, are more susceptible to frost penetration when compared to finer silts, clays, and fine sand materials due to different thermal conductivity properties.
A common misconception is that if you remove frost susceptible soils from a foundation that you have eliminated the potential of frost uplift, but in fact this is incorrect. If water can still enter the pores of the non-frost susceptible soils but cannot adequately drain, then the adfreeze pressure will be higher than that of a fine-grained soil which worsens the effect of frost uplift.
Constructability is, as it sounds, a measure of how easily a structure can be built, and with thousands of foundation elements, it’s a key consideration in designing a cost-effective solution. Subsurface conditions can cause significant grief where construction is concerned, and broadly these are obstructions, groundwater and organic materials. Obstructions, typically in the form of cobbles, boulders, bedrock and buried refuse, are a deterrent to screw or driven pile foundations from reaching their target embedment depth.
Groundwater can create several construction challenges, including negatively impacting soil stability. Organic soil materials typically provide little resistance, with the likelihood of resistance decreasing as the organic content increases. Organic soils are often associated with the presence of saturated environments, which create further challenges related to overall soil resistance.
Survey methodology
The survey methodology must be selected based on the site-specific conditions, but that is often not known until the investigation work has started; the encountered conditions may necessitate a change in the proposed methodology at the start of the investigation, and how the process accommodates these changes can directly impact the quality of the collected information and overall reduction in risk.
The most common methodology is to start with boreholes, which includes soil sampling, whether that be of disturbed or undisturbed samples for classification and completion of subsequent laboratory testing and the completion of in-situ testing such as standard penetration tests, field vanes or the use of a cone penetrometer.
Since deep foundations are so commonly used for solar projects and can contain such a large number of foundation elements, understanding the potential for refusals, or the foundations’ inability to reach the target embedment depth during construction, is important. Test pits are therefore also advisable.
These allow for direct observation of excavated materials, whereas drilling methods require us to infer the presence of obstructions which can be less accurate.
Pre-production testing
The geotechnical investigation should provide a full understanding of the subsurface conditions and their corresponding geotechnical engineering properties, whether they are preliminary or final design parameters. You would also want to understand the potential variability of the subsurface conditions, and if a variation of the same foundation would be sufficient to ensure successful installation of the foundations or a completely different design should be considered.
Once the geotechnical investigation is completed, it is beneficial to complete a pre-production testing programme to optimise and verify design parameters and gain an understanding of any concerns that may arise during construction. The process involves field testing of a number of pile sizes and types in order to refine the design.
Often this may need to be an iterative process that requires multiple phases to reach a final design. In many cases, this is not completed, and it can often directly impact the success of the foundation erection work and the overall risk associated with this activity.
Foundation types
There are four principal foundation types: driven piles, micropiles, helical piles and groundscrews. Each is profiled below, along with some insights into their pros and cons:
Driven piles: can come in a variety of different profiles, such as c-channels, w-sections or hollow structural sections. They should not be utilised in areas of shallow bedrock or in soils with excessive obstructions (typically cobbles and boulders), or very loose/soft soils.
When shallow bedrock is encountered, consideration must be given to whether it is a softer bedrock (soft sedimentary bedrock or metamorphic) or a harder bedrock (hard sedimentary bedrock or igneous). If it’s softer bedrock it may be feasible for a driven pile to penetrate the material, but this is only the case with very soft sedimentary bedrock such as sandstone or claystone; alternatives could be a predrilled hole with a groundscrew installed into it or utilising a micropile. With harder bedrocks, a micropile would be the preferred alternative.
Helical foundations: These typically have a single-blade orientation but may require more in very poor soils. They can be used in softer soils that will not develop adequate uplift resistance for a driven pile. Helical piles are quite often used in climatic regions that encounter extended periods below 0oC and therefore are subject to frost uplift loads which are typically higher than the wind uplift loads generated from the actual racking system.
Typically, it is necessary to determine an approximate correlation between installation torque and uplift capacity. If this information is not interpreted by a qualified professional it could result in an underestimation of the uplift capacity. This often happens when minimal design investigation work has been completed or engineers with limited experience of these foundation types lead the design activities.
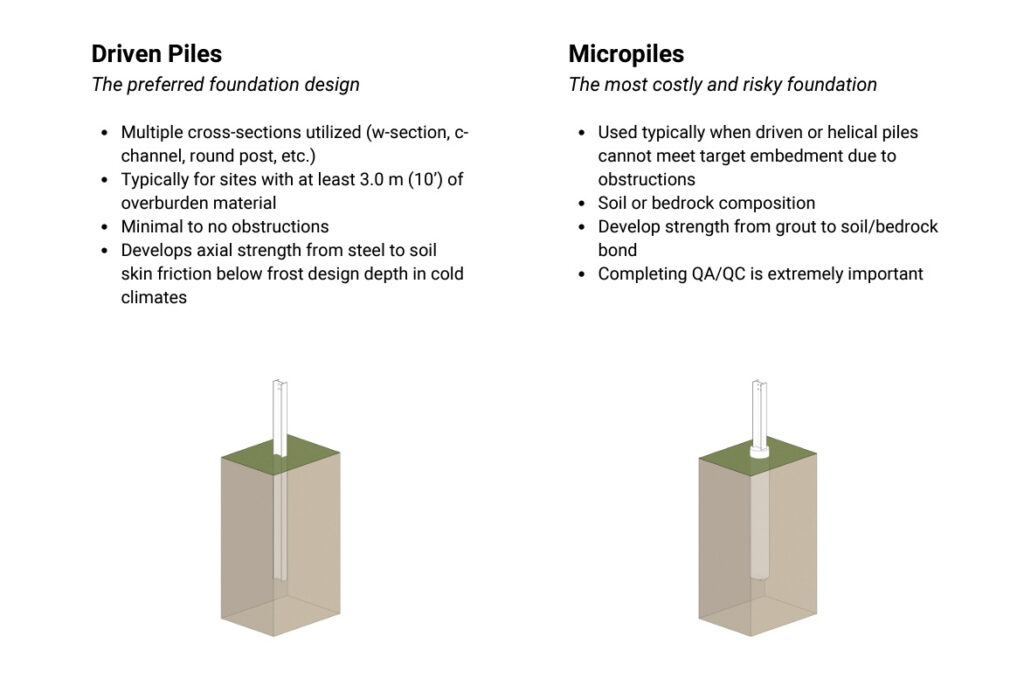
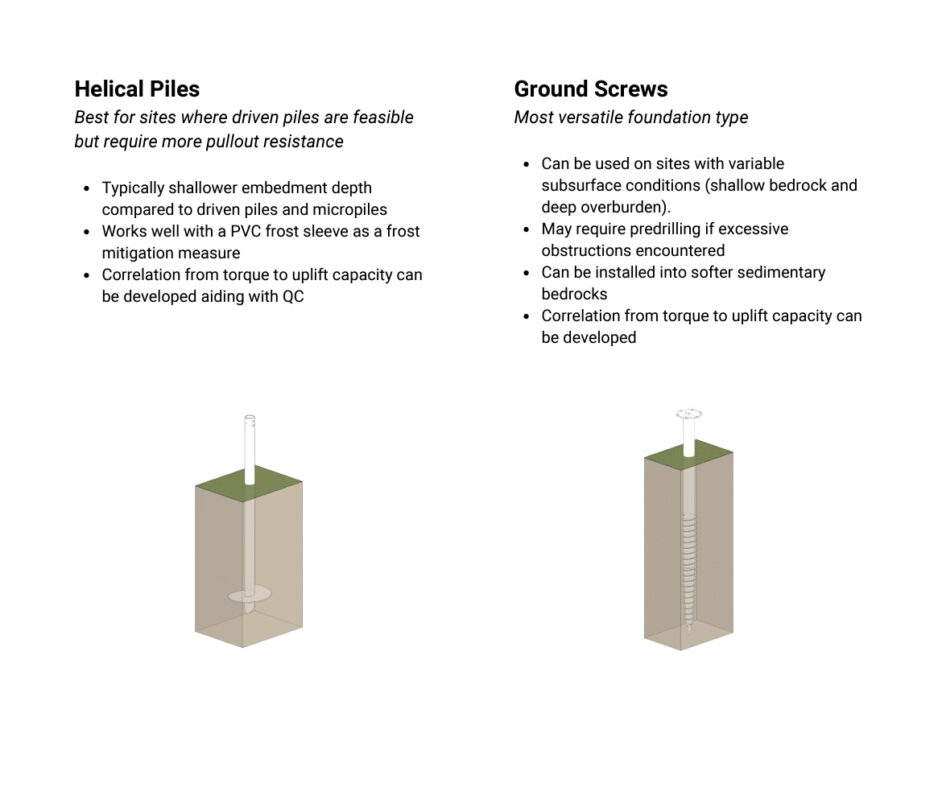
Groundscrews: These are typically used in very coarse materials, with large quantities of cobbles or boulders, and in soft bedrock environments. They cannot be used with very hard bedrock materials, unless you provide oversized predrill and then add aggregate back to this hole. This can result in a lot of effort to meet the quality control requirements and therefore is not a good solution as it may not yield favourable results and is costly. In a lot of conditions where this foundation is considered feasithe preferred design, predrilling will be required.
The predrilling diameter should ideally be no greater than the shaft of the groundcrew and ideally smaller so that you are not unnecessarily disturbing competent materials. If excessive amounts or shallow groundwater are encountered during predrilling, it’s typical to encounter collapsing soils which will affect installation and meeting the design requirements, specifically torque which similar to a helical foundation can be utilised to estimate the uplift capacity.
Micropiles: These are used in similar conditions as a groundscrew, but when either a groundscrew cannot feasibly be installed due to subsurface conditions or materials are very loose. It is the highest cost option when compared to the others. This is primarily because anything made with concrete can be challenging as it is time-sensitive – meaning if it is on-site too long it may be deemed as non-useable; typically this is two hours from the time of batching unless specific admixtures are utilised which only increase the cost of the concrete.
Also, these sites are quite often in remote areas and therefore the travel time to the sites could be high and once again because of the time-sensitive nature can be problematic. If being used in the most challenging places with groundwater issues and obstructions, micropiles will need to be installed using a continuous flight auger which will place the concrete (or grout) utilising an injection pump or other methods that place the material in a tremie fashion.
This is to place the concrete/grout at the base of the boring so that it displaces the groundwater upwards as it is injected into the boring, this will ensure that the cement and aggregates do not segregate and ensure that it will cure as designed.
A fifth option is surface ballast, when penetration into subsurface is not feasible – one of the largest applications of this approach is over a landfill or when the underlying material is contaminated and cannot be penetrated. The surface ballasts are typically made of concrete but can also utilise earth or other geological materials. The surface geo-ballast is quite often used in remote areas when concrete or other specialised equipment may not be available, or if there is an abundance of geological waste material which can be economically used at the site.
Case study
Location: US Virgin Islands
Customer: Polar Racking
Racking system: Core by Polar Racking (post storm)
Foundation: Groundscrew (pre-storm), driven round (poststorm)
Project Details: The site had been previously destroyed by Hurricane Irma. PRI Engineering and BMR conducted an extensive site investigation and component testing programme to support the design of the racking structures and foundations.
Previously, the facility had been supported by groundscrews, and little to no quality control had been completed during construction.
A driven round was utilised to penetrate dense overburden material and soft underlying bedrock.
The driven foundation utilised the in-situ strength of the soils instead of disturbing them as the groundscrews did.
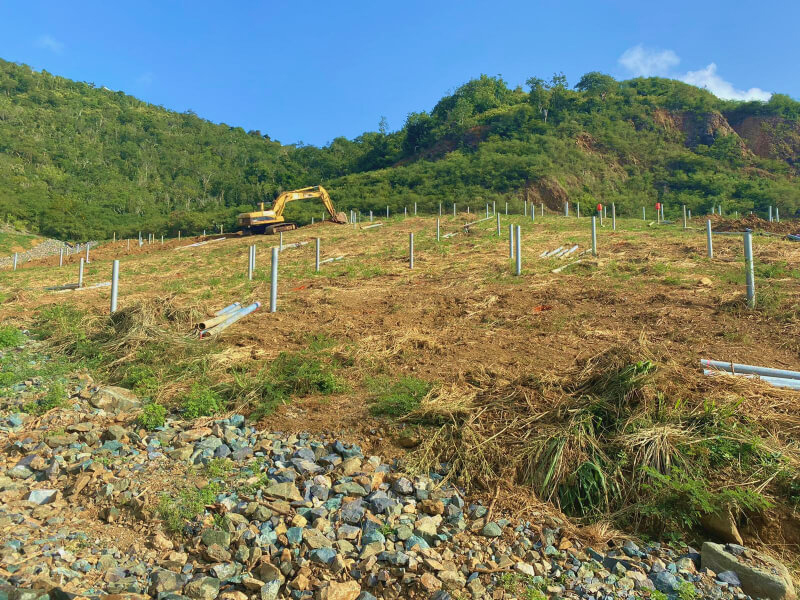
Construction
During construction, a quality assurance/quality control programme should be completed to ensure that the foundations are being installed as per the design requirements and the anticipated subsurface conditions are being encountered.
The subsurface environment can change dramatically throughout a single solar site. Preliminary desktop research and the pre-production testing efforts completed in advance, even the most thorough investigation, may not uncover all conditions that will be encountered during the construction process. While the clients and contractors will constantly mitigate equipment failures and disruptions, material supply, and most importantly, production rates on-site, these unknown site conditions can place severe strain on the site’s efficiency and schedule.
Foundation design in the future
The solar racking foundation design is unique, as the physical structure is very lightweight and covers an extensive area. Traditionally, built structures have a very high dead weight and therefore the loading in the axial direction is primarily compressive.
In the case of a solar racking system, most of the axial forces are in tension, which is due to either wind uplift acting on the racking system and then transferring these loads to the foundation system, or through frost uplift acting on the foundation and transferring these forces to the racking system and modules.
Multiply that by the number of foundations over the vast area PV projects frequently cover, and it’s clear there is a balance to strike between being conservative in the design because the risks are so high and our understanding of the interaction between frozen soils and foundations is limited, but also being aggressive with it because the number of foundation elements is so high that a small reduction in the foundation size or length could save millions.
Foundation design is a discipline that is sure to mature and develop in its sophistication. For example, in colder regions, our current understanding of the adfreeze process is only limited and needs improving for the determination of adfreeze pressure. It is a very complex process and currently, there are only limited guidelines, which can result in a conservative design.
But what is certain is that, with the foundations for a solar project typically consuming around 7.5% of a project construction budget, getting it right is a critical element in maximising value. Understanding what lies beneath your project site is a vital step to derisking a project and ensuring it operates for as long and as profitably as expected.
Author
Arash Yazdani is chief operating officer of PRI Engineering, based in Ontario, Canada. He is a designated professional and consulting engineer and has been working in the fields of geotechnical engineering and hydrogeology for over 15 years. Arash has developed geotechnical investigations and foundation capacity load testing programmes for solar projects throughout Canada, the United States and the Caribbean for over 5GW of projects and acted in various capacities as an advisor on over 500 solar developments.