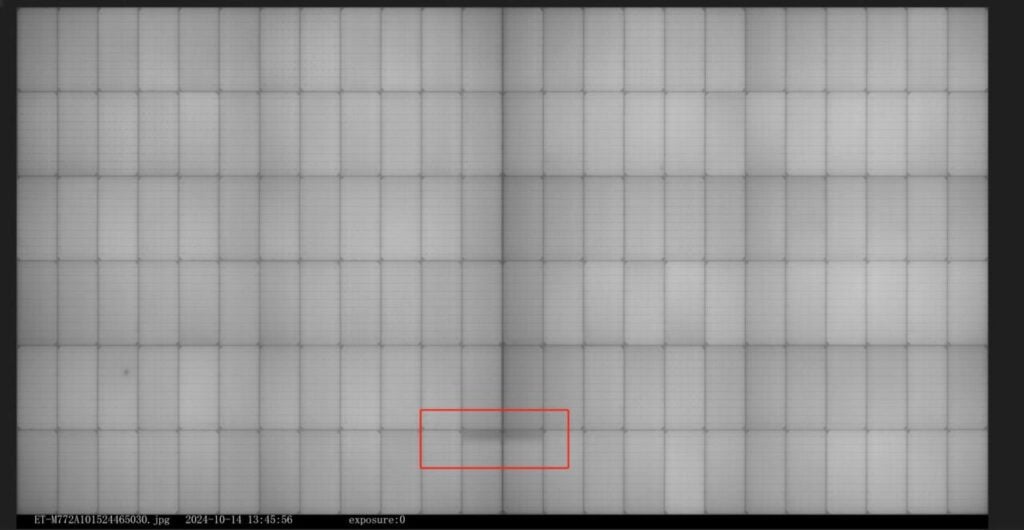
The electric grid is complex. For many generation technologies, the complexity lies in their sophistication. Gigawatt-scale nuclear and coal plants are inherently complicated, requiring a large on-site staff of technicians and engineers to ensure safe and efficient operations. In solar, the complexity lies elsewhere. The basic construction of a solar panel is relatively simple compared to a nuclear plant. The trick in solar is to get everything exactly and precisely right – specifications, manufacturing, transportation, and installation – over and over again. For example, a typical 200MW solar plant constructed with 600W modules requires 333,000 modules.
Significant attention has appropriately been paid to big technological changes in the solar industry, including the move to bifacial cells, the switch from PERC to TOPCon and the relentless increase in module wattage. But there is a much less visible, and less discussed, change that has improved the current collection in each cell but made the required precision of the manufacturing process more stringent.
Unlock unlimited access for 12 whole months of distinctive global analysis
Photovoltaics International is now included.
- Regular insight and analysis of the industry’s biggest developments
- In-depth interviews with the industry’s leading figures
- Unlimited digital access to the PV Tech Power journal catalogue
- Unlimited digital access to the Photovoltaics International journal catalogue
- Access to more than 1,000 technical papers
- Discounts on Solar Media’s portfolio of events, in-person and virtual
Over the past 10 years, solar module design has shifted from using two to three large flat wires to 18 thin round wires per cell. This change has lowered costs and dramatically reduced the impact of cracks, but at a tradeoff. It was easy to solder big flat wires in the proper location, but it may be much harder to precisely place the new, smaller, round wires. A small misalignment can lead to a “cold solder joint”, where the wire is not fully attached to the cell. Going back to our reference 200MW plant with 333,000 panels reveals the scale of the challenge: 18 wires per cell, multiple solders per wire per cell, and 144 half-cells per module translates to well over one billion solder joints!
To test the quality of solder joints, most manufacturers perform a destructive test offline (referred to as a “pull test”) on a very small sample as frequently as every four hours. The intent is to determine if there is a systematic failure in the soldering process, but this approach is not effective in catching infrequent defects. To complicate matters, the pass/fail criteria of the pull test can vary by factory. So, inevitably errors can go undetected.
Our company, Clean Energy Associates (CEA), recently summarised the results of our in-factory quality assurance findings across over 300 factories, covering production from January 2023 through August 2024. Cracked cells used to be the most common defect, but now cold soldering has become the highest frequency problem found during pre-shipment electroluminescence (EL) inspection.
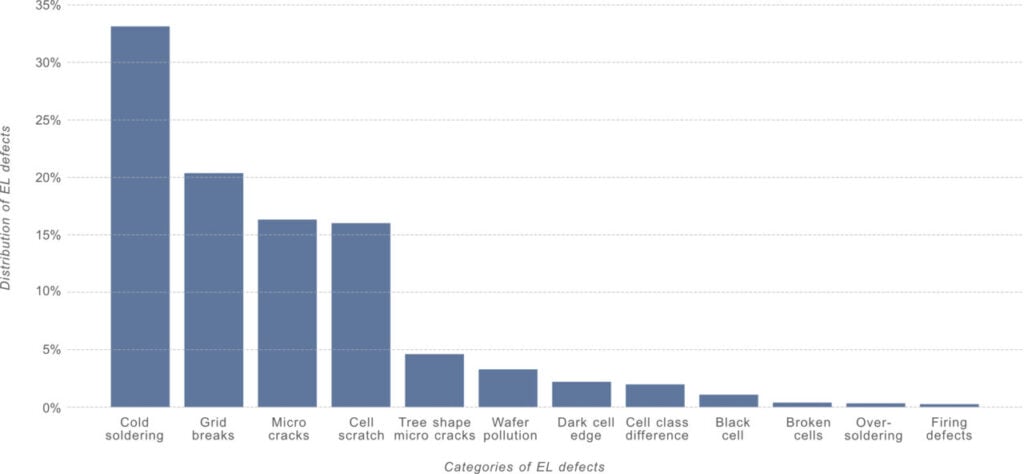
These defects were found at the end of the manufacturing process, which means they had eluded the in-process quality assurance checks and were ready to be shipped to the field.
A similar recent survey of defects found in the field by CEA’s Engineering Services team found 78% of sites contained modules with soldering defects (link to report here).
When solar panels with soldering defects are shipped and installed in the field, a number of problems can arise. A bad solder joint creates a resistance connection, which leads to higher losses to heat and reduces electricity generation. Bad solder joints may contribute to the bypass diodes turning on, disconnecting one third of the cells in the module and thereby reducing output of the module by a third. In the worst case, bad soldering can lead to extreme temperatures which can progress into catastrophic failure and a thermal event.
To make matters worse, when a string of modules contains a mix of good and bad modules, it makes it more difficult for the maximum power point tracker (MPPT) to find the optimal voltage for the string, further reducing output.
The good news is that there are effective strategies to protect buyers from soldering defects. The solution starts well before production begins, with the negotiation of the supply agreement. Buyers should include a clear definition of soldering defects in the agreement, the requirement for 100% EL testing in the factory, as well as the right to place third-party quality assurance (QA) specialists into the plant to observe production.
While your PV modules are being produced, your QA representatives can observe the production process to ensure that tools are properly calibrated, processes are being followed, and an adequate pull test is performed. Prior to shipping each day, your representative should select a statistically significant sample of finished goods for inspection to catch defects – including but not limited to soldering.
There is no such thing as perfect, defect-free manufacturing. But a well-negotiated supply agreement and a well-designed in-factory QA programme can dramatically mitigate your risk.
Paul Wormser is VP, technology, and Jake Edie VP, marketing, for Clean Energy Associates