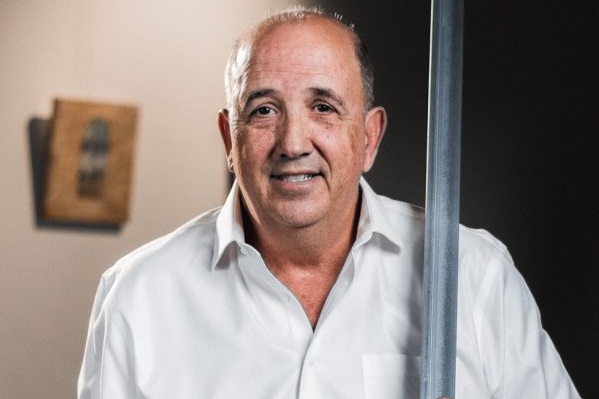
Origami Solar was founded in 2020 and is commercialising a roll form steel module frame solution that it claims can deliver cost savings, reduce greenhouse gas emissions and offer installation and O&M advantages. PV Tech caught up with the company’s co-founder and chairman Eric Hafter at the recent PV ModuleTech US conference to find out more. Eric will also be speaking at PV ModuleTech EMEA in Málaga, Spain, next week.
For readers who aren’t familiar with Origami Solar, could you give a brief introduction to the company and the role you are hoping to play in the future of PV modules?
Unlock unlimited access for 12 whole months of distinctive global analysis
Photovoltaics International is now included.
- Regular insight and analysis of the industry’s biggest developments
- In-depth interviews with the industry’s leading figures
- Unlimited digital access to the PV Tech Power journal catalogue
- Unlimited digital access to the Photovoltaics International journal catalogue
- Access to more than 1,000 technical papers
- Discounts on Solar Media’s portfolio of events, in-person and virtual
Eric Hafter: Origami Solar has been focused on improving the PV module frame, which has been made from extruded aluminium since the birth of the industry. One key reason for our focus is that aluminium frames are the only PV system component not to have decreased in cost. In fact, while all other component costs have dropped, aluminium frames are significantly more expensive now than in the past. Additionally, aluminium, often dubbed the “energy metal”, is a major contributor of greenhouse gases due to the amount of energy used to produce pure aluminium, as well as to extrude, harden, anodize and machine it.
Origami Solar is pioneering new manufacturing processes and designs that substitute roll-formed recycled sheet steel for aluminium, lowering the cost of PV, unlocking a global supply chain and dramatically reducing the greenhouse gas content of solar modules. Steel also delivers better module performance through innovative design and use of materials.
What was the main driver for Origami Solar seeking alternative materials for PV module frames?
Lower cost and greenhouse gas content were the original drivers for designing a steel frame, and we’ve proven that Origami steel frames deliver on both. Once we began testing our designs, we also discovered that they are able to perform much better than aluminium. Origami frames are much stiffer than aluminium frames, which reduces loading forces on the PV laminate, and therefore the PV cells.
This added strength results in fewer cell cracks, which can cause power degradation over time, thus delivering better energy production. The stronger frame is also needed for the new 670W+ modules, which are already pushing the limits for aluminium frames. Added strength is also key for installations in locations with extreme weather.
What do you think will be the tipping point for module manufacturers looking at alternatives to aluminium and how does steel compare to other options on the market?
The PV industry has a long history of moving quickly to adopt better, faster or cheaper solutions. We also see major companies spending hundreds of millions of dollars to reduce module costs by a fraction of a cent per watt. The Origami frame is not just better, faster or cheaper – it’s all three. Origami steel frames outperform aluminium in every significant metric. Manufacturing of steel frames takes about one-tenth the amount of time that aluminium extrusion frames do, and Origami frames will cost US$$0.01-0.02 per watt less than aluminium frames.
With all of these advantages, we anticipate the tipping point will occur soon, and that the industry will be largely converted to steel frames within five years. The passage of the Inflation Reduction Act and its significant incentives will ensure that steel supply and manufacturing will return to the US as we build the domestic supply industry to 50GW.
What are the wider market benefits of making the switch from aluminium from a sustainability and supply chain perspective?
Many media outlets and industry think tanks report that aluminium is rapidly becoming a supply bottleneck for PV. While not as dramatic as the electrical silicon supply problems of the mid-2000s, aluminium’s inability to keep up with the enormous growth of the PV industry is a real and growing concern. For perspective, the PV industry will consume 4 billion metres of module frames in 2022, a figure that grows every year.
Also, 100% of the aluminium frames used for solar PV come from China, Southeast Asia, and a small amount from the Middle East. Geopolitical challenges add substantially to supply concerns. Steel for PV module frames, meanwhile, is available on every continent and in quantities that do not strain the steel industry.
In addition, the PV industry’s reputation for being at the vanguard of green energy is seriously tarnished by the continued use of aluminium in such quantities. Moving forward, the solar industry must lead the world in energy decarbonisation, so PV components should also be part of the solution. Steel frames reduce the carbon footprint of a single megawatt of solar by ~190 metric tons. Moving to steel frames will be a huge win for the industry in terms of climate benefits and public perception.
Why/how does the extra strength and properties of steel matter for a module frame?
PV module frames have two primary functions: mounting the panels and protecting the laminate and solar-active materials. Steel is a significantly stronger material than aluminium. The Origami design leverages this inherent added strength by using thin sheet steel formed into a profile familiar to the PV industry.
The design also provides much greater resistance to the environmental forces that a solar panel has to withstand, resisting these loads better than aluminium. This results in reduced deflection of the laminate and forces on the PV cells. Test results demonstrate that the same PV modules using Origami steel frames have far fewer and smaller cell cracks due to loading than those laminates with aluminium frames.
Additionally, racking systems made from steel allow the Origami frame to create a code-accepted electrical ground, eliminating the need for supply and installation of grounding hardware for each module.
Steel frames weigh more than aluminium. Is this a problem?
By volume, steel is three times as dense as aluminium, meaning that for the same volume of material, steel will weigh three times as much. Origami is pioneering the use of a very thin sheet steel roll formed into a structural profile. This means we’re using much less volume of material than aluminium frames require, so the weight premium for a module using Origami frames is only 0.5-2kg/module, adding just 2.5%-10% to the module’s weight. We’ve conferred with EPCs, developers and system designers, all of whom think the added weight is immaterial, and for ballast-mounted systems is actually a plus.
How does the Origami frame compare to aluminium for resistance to corrosion?
Anodised aluminium is very corrosion-resistant and will deliver a sound frame over the expected life of the system; 25 years or more. Prior to the development of super corrosion-resistant steel coatings, such a metric would have been difficult for steel to match.
In 1998, a new coating was introduced using a mixture of zinc-aluminium-magnesium. This protective coating gives steel a very long lifespan and is produced and used by major steel companies around the globe. Multiple steel suppliers offer Z-A-M coatings: ArcelorMittal (Magnelis), US Steel (Z-Mag), Wheeling Nissan (ZAM) to name a few. Each of them comes with warranties of up to 40 years.
A number of international solar racking companies also use Z-A-M coatings, thus demonstrating their effectiveness and acceptance by the industry. Z-A-M coated steel used for Origami frames will deliver the anti-corrosion performance needed to meet expected system lifespans.
Why is Origami Solar focused on building the supply chain?
We recognise that major change is sometimes difficult. Further, every module manufacturer is ramping up to meet the growing demand for its products. To move forward with the new steel frame solution, module manufacturers need help in sourcing steel frames. And, like other technology changes, the switch to steel frames requires significant engineering, purchasing and project management resources.
Origami realised early on that, in order to shepherd this new technology into our industry, we must bring the key stakeholders into the process. We have been very active, working with steel suppliers and roll formers that not only can supply, but are eager to engage and support the transition from aluminium to steel for module manufacturers around the world. Origami Solar is working to lead the solar industry through manufacturing toward a cleaner, less expensive, better-performing solution.