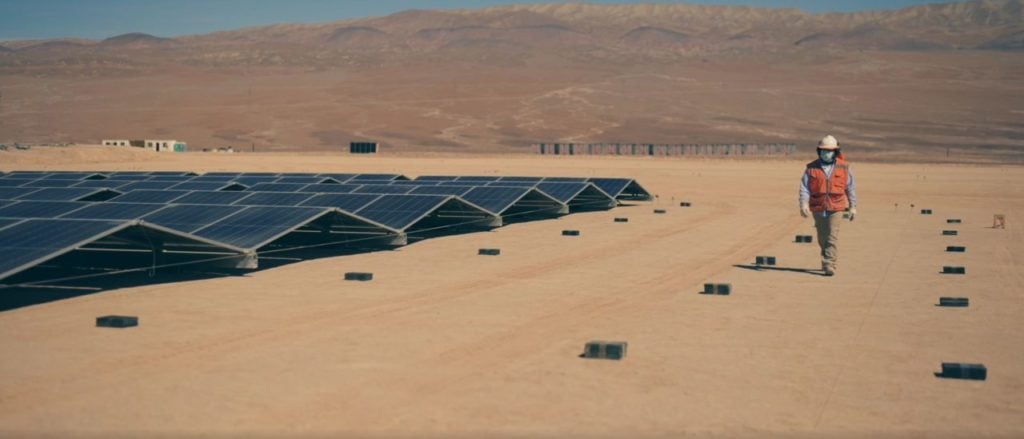
The future of solar module deployment could be rooted in mass, rapid deployment rather than precisely tilted, steel-mounted and spaced-out panels extending over acres of land. So says Australian company 5B, which manufactures accordion-style folding solar arrays that arrive at a project site flat-packed and ready to be deployed.
The central question behind the technology was put simply by 5B CEO and founder Chris McGrath in a conversation with PV Tech: “How do you get the costs of solar down and the speed of and ease of deployment and installation up?”
Unlock unlimited access for 12 whole months of distinctive global analysis
Photovoltaics International is now included.
- Regular insight and analysis of the industry’s biggest developments
- In-depth interviews with the industry’s leading figures
- Unlimited digital access to the PV Tech Power journal catalogue
- Unlimited digital access to the Photovoltaics International journal catalogue
- Access to more than 1,000 technical papers
- Discounts on Solar Media’s portfolio of events, in-person and virtual
Utility-scale solar PV is the cheapest and most efficient energy source in much of the globe, with over 1TW installed worldwide. Manufacturing announcements from China, Australia, India, the US and Europe appear weekly as global capacity continues to rise. As such, over time the price of modules has trended downwards, with the National Renewable Energy Laboratory (NREL) in the US reporting an 85% drop in module prices in the decade leading to 2021.
Is there, then, as much call for painstakingly squeezing every ounce of radiation out of every hour of sunshine when modules are more easily procurable? Why not deploy as many modules in as small an area as possible?
5B mounts its folding modules directly on the ground, adjacent to one another in a much more densely packed formation than axis or tracker-mounted modules can allow.
“Whilst we have lower yield per module, we actually get significantly more energy out of that particular site by putting more modules into that area, in the order of 150 to 200% more energy per hectare than other technologies,” says McGrath. 5B Maverick modules are mounted in an east-west configuration, without trackers or raised steel structures, and are essentially optimised for land use and economics, rather than per-module efficiency.
“East-west first became prevalent on rooftops in Europe, because they were trying to reduce wind load and make the installation simpler and faster, and use space more efficiently,” McGrath said.
“If you continue to follow that trend through as solar panels get cheaper and cheaper, then that’s the right way to build on the ground.”
NREL reported that utility-scale solar is expected to require between 4 million and 11 million acres of land by 2050 in the US alone, a country with no shortage of land. The argument of 5B, then, is that as modules get cheaper and easier to produce, and land gets more expensive and harder to come by across the globe, the solar sector is “past the inflection point as to when east-west makes more sense than tracking”.
Other companies have pursued very low-tilt, high-density PV solutions. US company Erthos creates ‘earth-mounted’ systems that resemble a photovoltaic swimming pool laid directly onto the ground. They offer useful solutions for small-scale sites or projects with physical constraints, though solutions for sourcing suitably flat land and protecting panels from degradation are not immediately apparent.
McGrath also spoke to PV Tech about 5B’s choice to prefabricate the company’s modules before arriving at a project site.
“Our mantra is moving as much time, cost and risk as we can from the field into the factory. And leveraging all the benefits of the factory, which is it’s faster, it’s more predictable, it’s better quality, it’s lower risk, it’s not exposed to weather events, it’s more ergonomic, safer for people to work, etc, etc.”
Prefabrication leads to very fast deployment. 5B says that a 1.1MW installation was deployed in Chile in a single day with a team of ten workers, a prospect that could significantly streamline and reduce costs for installers.
Prefabrication also has the potential to be cost-effective across the whole of the PV value chain. A standard installation takes a developer, module supplier, an EPC, a tracker supplier and other sundry parties who all converge at the deployment site. In theory, 5B applies the customer’s choice of module to its Maverick structure and arrives at the project site ready to deploy.
McGrath also spoke of the versatility of projects and terrain that prefabricated module structures can cover. “We work predominantly above the ground. If you’re working on sites that have challenging geotech or rock or soil conditions, or landfill sites, for example, we’re really flexible.”
A conventional approach requires embedding steel poles deep into the ground to ensure that the modules are stable. If subterranean conditions aren’t suitable that can cause significant time and cost increases for project developers, a problem that a more superficial approach mitigates.
A recent piece of analysis from insurtech firm kWh Analytics said that US solar assets in the US had been chronically underperforming, in part due to module degradation. The impact of degradation on near-horizontal modules, with a more directly exposed surface area to potential damage, remains to be seen and may complicate 5B’s economic thesis.
As it stands, 5B’s largest operational project is the 12.8MWp installation at Happy Valley water treatment park in South Australia. Whether the principles of prefabrication and land use over efficiency have the legs to cause a real change in the PV landscape and be deployed at real scale remains to be seen, but investments in 5B from bp and the Australian Renewable Energy Agency speak to a level of confidence.
With reports that the world needs to hugely ramp up its renewable energy deployment if it’s to reach global net zero targets, and solar positioned as a linchpin of that endeavour, perhaps volume and an easy-access IKEA-style flatpack solution for the masses is what’s needed.
McGrath said: “We’re trying to watch where the industry is going and will go over the years to come and make sure that the way that we’re developing our tech is optimised for that trend line, rather than where the industry has been.”