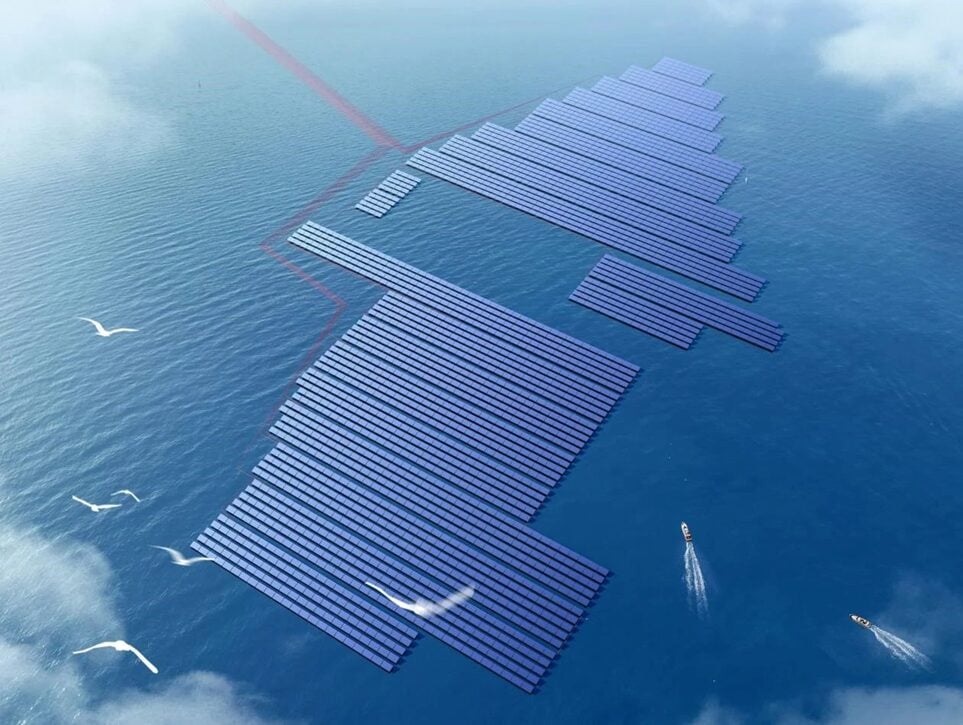
PV technology providers are developing new hardware solutions specifically for offshore solar systems. JinkoSolar’s Zhuoran Cui and Siyuan Xie report on some of the work the Chinese module producer is undertaking to develop and test products able to withstand the rigours of the marine environment.
According to a report from the International Renewable Energy Agency, the floating PV (FPV) market has spread globally, with more than 60 countries pursuing future deployment of FPV plants; of these, 35 countries are already harbouring 338 FPV power plants.
Unlock unlimited access for 12 whole months of distinctive global analysis
Photovoltaics International is now included.
- Regular insight and analysis of the industry’s biggest developments
- In-depth interviews with the industry’s leading figures
- Unlimited digital access to the PV Tech Power journal catalogue
- Unlimited digital access to the Photovoltaics International journal catalogue
- Access to more than 1,000 technical papers
- Discounts on Solar Media’s portfolio of events, in-person and virtual
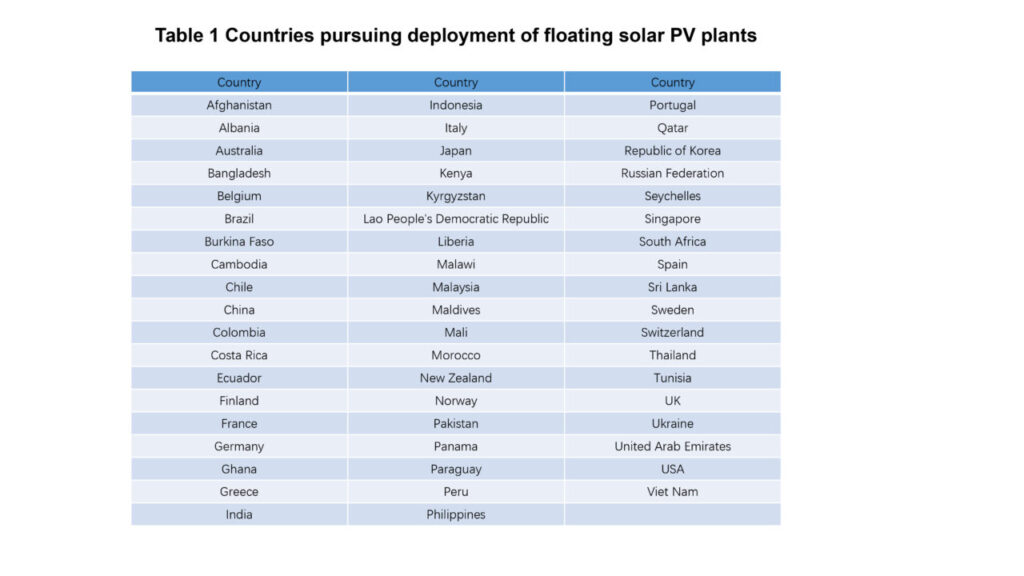
Table 1, above, provides a summary of some of the planned FPV projects globally in the coming years. Research forecasts predict the global FPV will maintain a growth trend, with installed capacity projected to reach 4,800MW by the year 2026. Five to six years from now, the market potential is anticipated to accommodate an FPV installed capacity of 30 GW, as seen below.
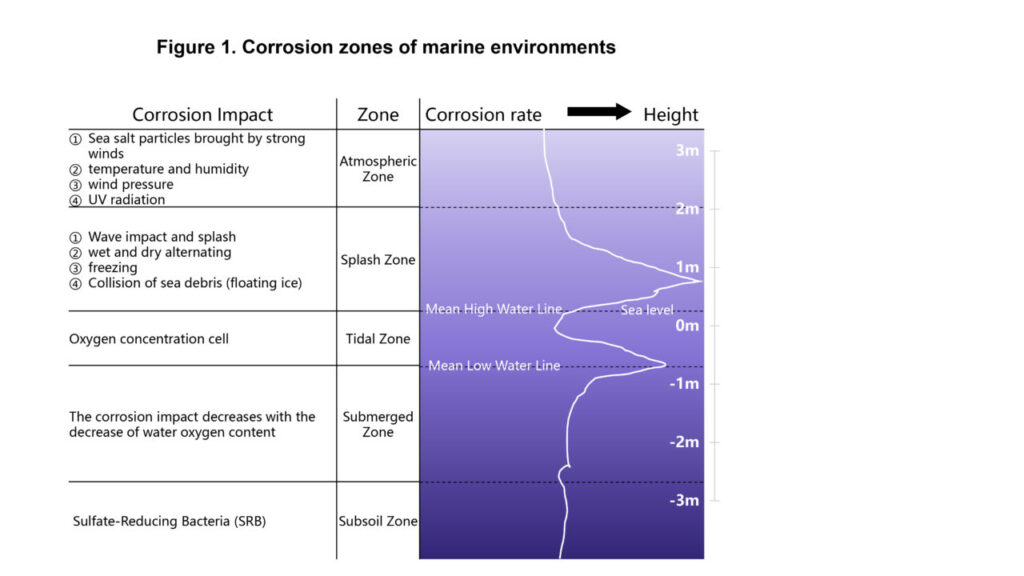
One arm of the floating PV segment that is currently attracting great interest in the industry worldwide is the concept of locating floating solar systems offshore, in the open sea. Offshore PV systems offer numerous benefits, including the alleviation of pressure on scarce land and higher module outputs of up to 15% due to the reflection of sunlight off water and the evaporative cooling effect of water. The marine environment facilitates easier panel maintenance using on-site water, reducing dust and heat-related power losses. Additionally, FPV can be integrated with aquaculture, providing a dual-purpose structure that supports both clean energy and marine life.
However, before the development of large-scale commercially sustainable projects in marine areas, further research is required. It can be envisioned that FPV systems transitioning to the marine environment will initially be deployed in sheltered coastal areas.
Marine environment characteristics
The marine environment exhibits significant differences at various altitudes, leading to diverse impacts on PV modules. Therefore, the marine environment is typically divided into five main zones: atmospheric zone, splash zone, tidal zone, submerged zone and subsoil zone.
The atmospheric zone extends above two meters from sea level. In this region, temperatures and humidity are relatively high and strong winds carry sea salt particles, resulting in a corrosion rate in the marine atmospheric zone that is four to five times higher than inland areas. Additionally, this zone is often subjected to wind pressure and severe UV radiation.
The splash zone, located between 0 and 2 meters above sea level, is where PV modules frequently experience wave impacts and collisions with floating objects. The fluctuation of waves leads to alternating wet and dry conditions in this zone, creating an environment where corrosion is most severe in the marine environment. In winter, incidents of freezing and collisions with floating ice may occur.
The tidal zone lies between the mean high tide and low tide lines and serves as the cathode area of oxygen concentration cells, offering protection and resulting in a lower corrosion rate. However, this zone is at risk of marine biofouling. Due to the rise and fall of tides, marine organisms attach to floating PV floats during high tide, increasing the weight of modules and causing submersion over time.
Lastly, the submerged and subsoil zones exhibit relatively stable environmental conditions, with corrosion impacts decreasing as oxygen levels in the water decrease. These zones mainly affect the corrosion of anchor systems and pile foundations. Therefore, it is crucial for PV modules to focus more on the impacts of the atmospheric, splash and tidal zones.
Offshore PV system solutions
There are different solutions for offshore PV systems based on different seabed depths and marine conditions. Currently, there are three main types of offshore solar power plants: fixed pile-based, floating platform and thin membrane.
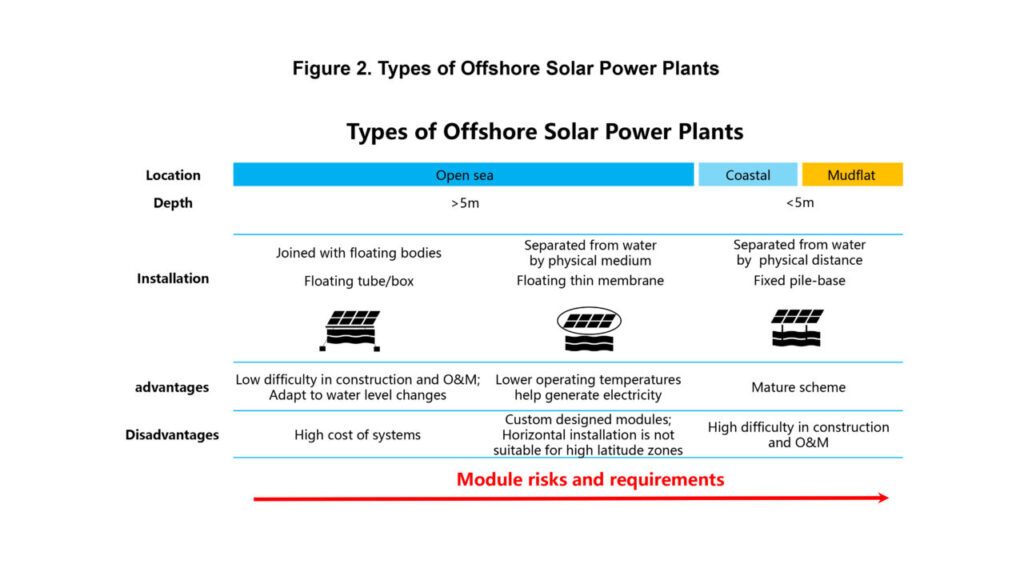
In coastal areas, such as mudflats or intertidal zones, where the sea depth is less than five meters, the fixed pile-based installation method is more suitable. This is the most common form of offshore PV system, with relatively mature system solutions, similar to the installation methods of onshore PV power plants. Currently, large-scale offshore PV systems built in coastal areas are mainly based on fixed pile-based installations.
However, the disadvantage of fixed pile-based systems is that waves can cause microbial attachment, and this design requires the construction of wave protection dikes, which increases costs. Due to the fact that the modules are elevated above sea level by the pile foundation, their impact is relatively minor. However, from an installation and maintenance perspective, it requires pre driving piles to construct large platforms, which involves the use of heavy machinery, making the overall construction process challenging and time-consuming. Specialised equipment is also needed to lift and install the modules, and subsequent module maintenance and inspection become more difficult due to their elevated installation position.
Specifically, fixed pile-based PV systems have different structural forms. The most common approach is to install conventional brackets on the piles and then install the modules. In order to reduce the number of piles and the risk of corrosion and water ingress, large-span steel structure platforms are also used. Currently, there are more installation options for fixed pile-based systems, such as cable truss flexible structures and honeycomb structures.
Cable truss flexible structures combined with fixed piles are suitable for situations where the silt layer is not thick and the soil is relatively hard. Its advantage is that the structural stress is more reasonable, but it also brings higher costs in pile foundations and construction. The honeycomb structure requires fewer piles to support the modules, but the disadvantage is that the structure is more complex, and the construction is relatively difficult.
If the sea depth is deeper than five meters and the sea area is not affected by major typhoons, floating platforms can be used. Similarly, this installation method is basically the same as onshore installations. The advantage is that its maintenance costs are lower than fixed pile-based systems, and it can adapt to different wave conditions, making it the main form of future offshore PV systems. Installation and maintenance of floating platform solar stations only require the construction of simple construction platforms, without the need for heavy machinery, making the construction process faster and less challenging. Generally, with 30 workers, it is possible to install 800 to 1,000 modules per day.
Additionally, inspections and replacements of modules are relatively convenient, offering economic advantages in terms of maintenance. However, since the modules are closer to the sea surface, they are more susceptible to the higher requirements and risks posed by strong winds and waves. Another drawback is the overall high system cost, but as the installed capacity increases, the costs are expected to decrease relatively.
Another type of offshore PV is the floating thin membrane system, which can also be used in areas with a sea depth deeper than five meters. The modules need to be horizontally installed, and some customised designs are needed for the modules, such as installing sliding tracks on the long sides and installing junction boxes on the front. The advantage of this installation method is that the modules float on the sea surface, with the working temperature close to the sea surface temperature. The continuous cooling effect of seawater can increase the electricity generation capacity under lower temperature conditions.
However, since the modules are horizontally installed on the sea surface, this installation method is not suitable for areas with high latitude where there is insufficient sunlight shining on the modules, which affects the electricity generation capacity.
Reliability requirements for modules in marine environment
Challenges of marine environment to modules
Considering the environmental conditions in the atmospheric zone, splash zone and tidal zone, the marine environment is characterised by high humidity, high salt spray corrosion, strong winds, high UV radiation, freezing and biological fouling. These characteristics pose challenges to the performance and reliability of PV modules.
High temperature and humidity accelerate the corrosion of aluminium frames and glass and cause rapid ageing of encapsulation materials. Moisture ingress into PV modules leads to corrosion of internal components, resulting in electrical connectivity issues and power loss.
Salt spray corrosion is a significant challenge in the marine environment. Salt spray contains chloride-containing microdroplets, forming a diffuse system where chloride ions disrupt the protective layer of metals, reducing their mechanical strength. Additionally, salt deposition on module surfaces reduces surface resistance, increasing the risk of leakage current. Furthermore, salt deposition can cause shading, leading to decreased power generation efficiency.

High levels of UV radiation in the marine environment can have negative effects on the materials and efficiency of PV modules. Prolonged exposure to UV radiation can lead to material ageing in PV modules, manifested as material hardening, embrittlement, colour changes, etc., thereby affecting the structural stability and performance of the modules. Intense UV radiation can also promote the oxidation and decomposition of organic substances on the surface of glass films, causing wrinkling, cracking, peeling of the film layers and the formation of rainbow spots on the glass surface, resulting in reduced transparency.
Offshore areas are often subject to strong winds, posing greater wind loads on PV modules. High winds can directly lead to module damage, thereby reducing the performance of PV systems.
Freezing is another challenge in the marine environment. Freezing can damage the structure and electrical components of PV systems, affecting power generation efficiency. Low temperatures can affect the performance of module materials. For example, encapsulation films gradually lose elasticity and protective properties under low-temperature conditions, and adhesives and junction boxes also face severe challenges in low-temperature environments.
The marine environment is prone to biological fouling, such as algae and marine organisms. Biological fouling can cause surface shading of PV modules, leading to a decrease in PV efficiency.
Material optimisation of Jinko n-type modules for marine environment
To address the challenges in offshore projects, Jinko n-type modules have undergone comprehensive material optimisation in various aspects.
Ageing resistance: The use of dual-glass modules replaces the backsheet with rear-side glass to enhance module durability and ageing resistance. Dual-layer coated glass provides better resistance to moisture. POE encapsulant film in dual-glass modules offers stronger protection compared to EVA. Additionally, connectors are equipped with cold-shrink tubes and fluorine-containing sealants to form a dual-layer protection, achieving an IP68 protection level. These methods collectively reduce the impact of high temperatures, high humidity, UV radiation, and freezing on the modules, combating climate and external environmental erosion.
Anti-salt spray corrosion: Anodised AA20 reinforced aluminium frames enhance the module’s resistance to salt spray corrosion. Anodising forms a solid oxide film that protects aluminium frames from salt spray erosion, prolonging the module’s lifespan.
Wind resistance: Dual-glass modules use semi-tempered glass, which is twice as strong as ordinary float glass. Moreover, the combination of various installation methods, such as bolt and clamp combinations, enhances installation stability and resistance to strong winds. This effectively reduces the risk of PV modules being lifted away by sea winds.
Reliability performance of offshore n-type modules
After optimising Jinko’s regular n-type module, it can be applied in various offshore PV system solutions. In the long-term operation process, the reliability of offshore modules needs to be considered in advance to ensure stable performance in harsh environments. Therefore, Jinko conducted relevant tests in collaboration with TUV NORD.
In addition to normal degradation reliability testing, Jinko, in collaboration with TUV NORD, conducted a series of performance tests tailored to harsh marine environmental conditions. These tests include salt spray testing, wind tunnel testing, ageing testing and hot spot testing.
During wind tunnel testing, n-type modules were subjected to incremental wind loads from low to high, with each wind load lasting for three minutes, to evaluate the mechanical strength and wind load resistance of n-type modules under strong wind conditions.
During salt spray corrosion testing, saltwater mist would come into contact with the surfaces, frames, and connectors of n-type modules, potentially leading to corrosion and oxidation issues. By assessing changes in the appearance, performance and electrical parameters of the modules, the long-term reliability of n-type modules in marine environments was ensured.
In terms of ageing testing, n-type modules underwent various tests such as thermal cycling, damp heat cycling and ultraviolet ageing. These tests simulated conditions such as high temperatures, high humidity, extreme temperature changes and intense ultraviolet radiation in offshore environments, validating the durability and performance stability of n-type modules under these factors.
In hot spot testing, n-type modules that were not cleaned after salt spray were subjected to hot spot testing to detect and locate possible localised temperature anomalies on the module surface, thereby assessing their thermal performance and operational status.
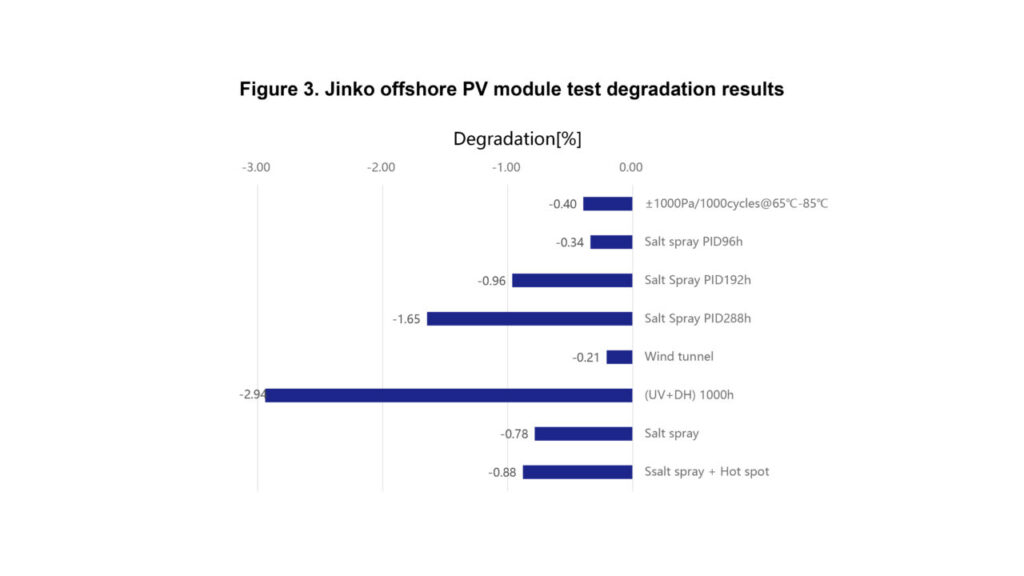
Based on the above tests, as shown in Figure 3, it can be observed that Jinko offshore photovoltaic modules can still maintain excellent performance under more stringent salt spray conditions. As a result, Jinko has been awarded certification by TUV NORD, proving the modules’ good marine adaptability.
Meanwhile, as depicted in Figure 4, Jinko offshore PV modules, after material optimisation, undergo one to three times PID testing compared to conventional modules. The PID degradation of Jinko offshore photovoltaic modules under salt spray 8 environment is significantly better than the conventional PID degradation of general modules, further confirming the outstanding reliability of Jinko offshore photovoltaic n-type modules.
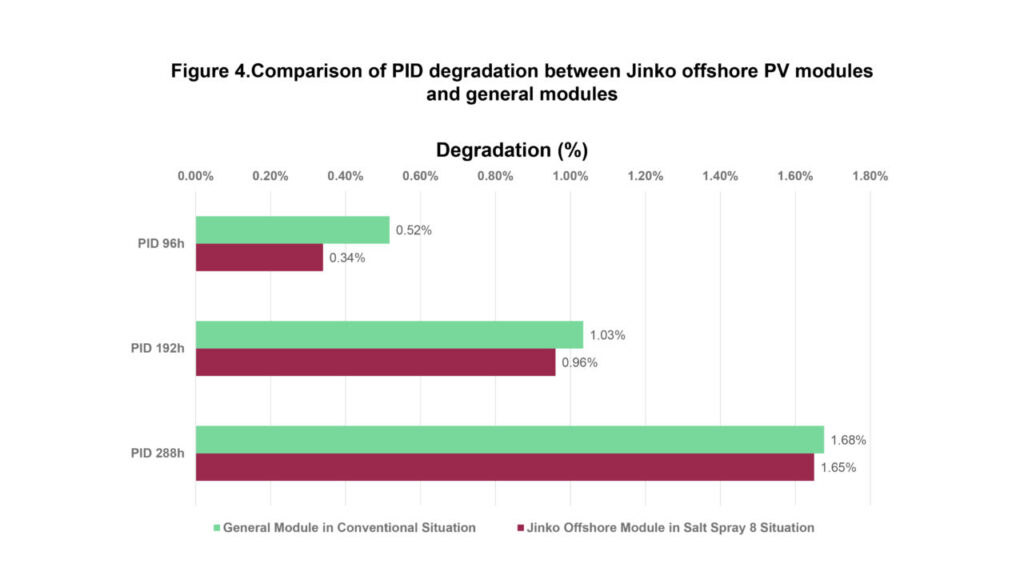
Offshore module project cases
Jinko has collaborated with CIMC to establish a semi-submersible offshore PV demonstration platform. Located approximately 6 kilometres offshore from Yantai, Shandong Province, China, at geographical coordinates: 121.52°E, 37.49°N, the PV platform has been operational since 31 March 2023.
In terms of project scale, the offshore platform is divided into four smaller platforms, with modules installed on two of them. The first platform has 172 pieces of PV modules installed, while the second platform has 180 pieces of PV modules installed, totaling 352 pieces of PV modules. The platform structure is a buoy-fixed bracket type, with the bottom of the modules approximately 5 metres above sea level.
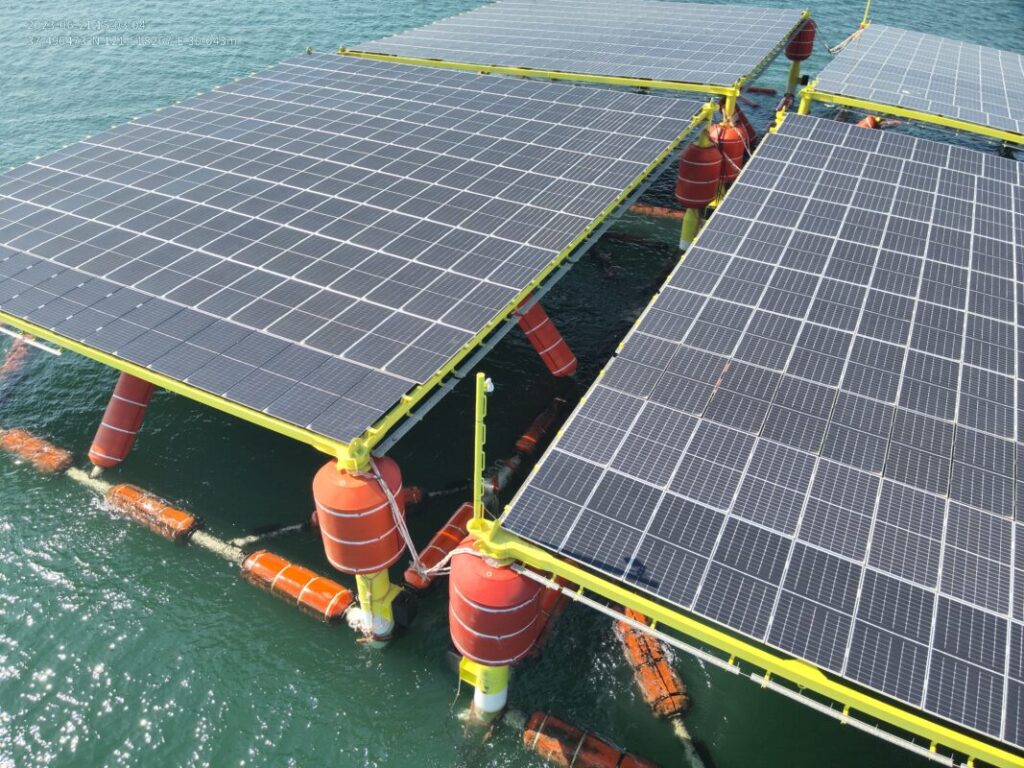
After thermal imaging hotspot detection and camera observations, the relevant results are shown in the accompanying figures. No significant exterior defects were found in the 352 pieces of modules themselves, mechanical structures, connectors, metal parts, or lamination performance on both platforms.
In addition to the demonstration project, Jinko has also won the bid to supply 1.3GW of modules to the world’s largest offshore PV project to date, which has successfully commenced construction. The project is located in the Laizhou Bay area of Dongying City, Shandong Province, China, with the centre of the site being 8 kilometers from the coast. Further details are confidential at this stage, but as the first GW-level, large-scale offshore PV project, it will pave a new path for the PV industry, offering broader geographical coverage, lower land costs and more efficient electricity generation potential.
Economic advantages of offshore n-type modules
Offshore PV projects incur higher costs compared to traditional ground-based stations due to expensive marine usage and system costs such as piles, brackets and other infrastructure. In response to these cost challenges, Jinko employs n-type TOPCon cells in its offshore PV modules to amplify economic advantages and enhance cost-effectiveness for projects.
Taking a 4.4MW floating array as an example, the power of n-type is 30W higher than that of p-type under the same panel area. In this case, the number of modules can be saved by 414 pieces under the same DC side capacity. Meanwhile, the land cost of the power station system can be saved by approximately 5.2%. The construction cost of the power station system is closely related to the number of modules.
After adopting efficient n-type modules, the estimated BOS cost can be saved by more than RMB0.05/watt. Due to the higher bifaciality, lower temperature coefficient and lower degradation of n-type, a preliminary calculation comparison shows that the electricity generation of this case can increase by 3.7% throughout the lifecycle.
Summary and prospects
Jinko’s n-type modules have been optimised for environmental conditions such as high temperature, high humidity, high salt spray and intense UV radiation in offshore environments. This optimisation includes materials such as module frames, glass, encapsulation films and connectors. Through a series of performance tests including salt spray testing, wind tunnel testing, aging testing, and hot spot testing, the long-term reliability of n-type modules in offshore environments is ensured. In addition to reliability advantages, n-type modules also have higher power output, which can save BOS costs for offshore photovoltaic projects, reducing costs and increasing efficiency.
Jinko and CIMC jointly developed a semi-submersible offshore photovoltaic platform using Jinko’s n-type modules and combining CIMC’s platform equipment technology, realising photovoltaic power generation in marine environments. As a new mode of energy utilisation and development, it is believed that after large-scale application in the future, it can solve the problem of land resource shortage for large-scale land-based photovoltaic projects and enhance the off-grid power supply capability of remote islands. In the new track of marine clean energy, Jinko Solar will further enhance its product quality advantages, lead the industry in n-type technology upgrades and inject new vitality into the healthy and sustainable development of the offshore photovoltaic industry.
Authors
Zhuoran Cui is a manager for JinkoSolar Global Solutions. His role is focused on providing solutions for PV modules and delving into the value of n-type modules. Prior to joining JinkoSolar, Zhuoran Cui focused on materials R&D, earning a master’s degree in materials science and engineering from Nanyang Technological University.
Siyuan Xie is a manager for JinkoSolar Global Solutions. In his role JinkoSolar, he is focused on system solutions and how modules can be better matched with the system side. Siyuan Xie graduated with a master’s degree from the University of Manchester, majoring in renewable energy and clean technology.