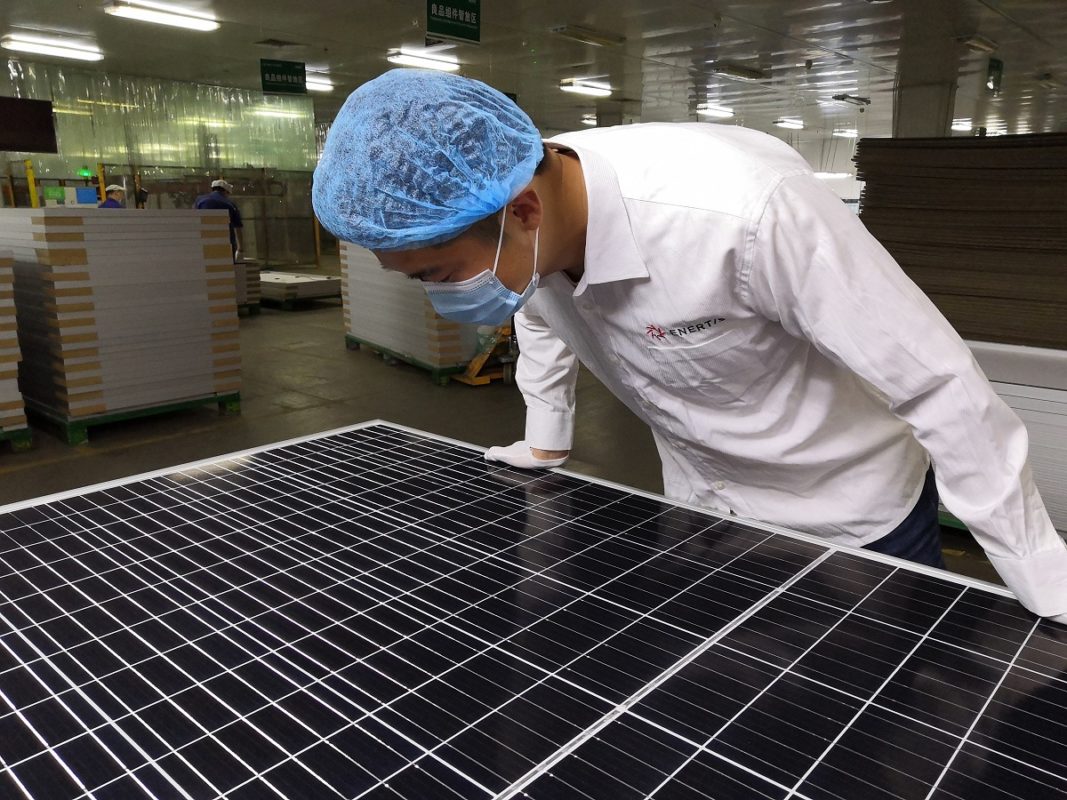
Nowadays, considering bifacial modules as a first option for a new solar plant is becoming mainstream in the PV market, thanks to their rapidly growing trend as a standard PV device worldwide.
In September 2018, the 9th edition of the International Technology Roadmap for Photovoltaic (ITRPV) report forecasted a market share for bifacial cells close to 15% by 2020 [1]. In fact, bifacial module deliveries exceeded 25% in 2019 and are expected to reach 40% this year and 60% in 2021, with no indications of a market slowdown in the short term.
Unlock unlimited access for 12 whole months of distinctive global analysis
Photovoltaics International is now included.
- Regular insight and analysis of the industry’s biggest developments
- In-depth interviews with the industry’s leading figures
- Unlimited digital access to the PV Tech Power journal catalogue
- Unlimited digital access to the Photovoltaics International journal catalogue
- Access to more than 1,000 technical papers
- Discounts on Solar Media’s portfolio of events, in-person and virtual
Not long ago, the idea of using higher performance, double-faced PV modules was still considered a sort of double edge-sword versus the traditional monofacial-based PV technology. The main reasons behind this were its higher price and the somewhat limited project bankability, due to the additional uncertainties to deal with, subsequently guaranteeing the theoretical energy gain from the modelling of many new site and PV system variables [2, 3].
Notwithstanding this, it was implicitly understood – and, today, better modelled – that increased energy yield per module area was beneficial. The development was also favoured by the rapidly narrowing price gap versus traditional monofacial devices (basically the same, as of today), eventually leading to a remarkably minimised levelised cost of electricity (LCOE), as the key economic metric of a solar PV plant [4]. However, despite the fact that optimisation of the front side power output of a solar panel will prevail as a key factor to consider in a project development, the race for a comprehensive understanding of the performance gain offered by the back side of a bifacial module continues to be a test for any PV asset owner and EPC player. Therefore, a close and multidisciplinary cooperation framework with PV equipment manufacturers, technical advisors, modelling software developers, etc. is needed to rise to the challenge.
Even so, these uncertainties associated with the design of a bifacial PV system in turn take for granted that the bifacial module’s datasheet and international standards are perfectly determined, understood and experimentally validated when facing the purchase of thousands of panels for a utility-scale PV project; nothing could be further from the truth as of yet.
Therefore, and specifically concerning the design and power performance of a bifacial PV module, this article reviews some of the main sources of variability and outstanding uncertainties that need to be addressed by the industry to grasp and define a series of standard rules for a reliable selection, purchase and use of bifacial panels in high-performance PV projects, as a new technological paradigm in the solar market worldwide.
For this purpose, examples of real cases devoted to the advisory, manufacturing inspection and testing activities performed in the last year by Enertis in several Asia-based module factories are reviewed (Table 1). All of them refer to bifacial modules’ manufacturing for large-scale projects worldwide, which in turn were dictated by specific Module Supply Agreements (MSA), designs and Bill of Materials features, many of which are barely known in detail by the buyers prior to and even after production completion. It is here that the role of independent third-party inspectors as Enertis monitoring the processes is key.
Tier-1 Supplier | Nameplate Power/W | Cell type | BOM‘s key parameters |
---|---|---|---|
A | 380/385 | Half-cell 9BB | POE/Dual glass 2.5mm, transparent rear side glass. Wire cell connector Φ 0.35 mm Aluminium frame 30×28 mma |
B | 400/405 | Half-cell 9BB | POE and EVA+POE/Dual glass 2.0mm white ceramic glaze on rear side glass Wire cell connector Φ 0.35mm Aluminium frame 30×35 mm |
C | 370/375 | Full cell 5BB/12BB | POE/Dual glass 2.5 mm white ceramic glaze on rear side glass. Cell connector 0.23×1 mm (5BB) and wire Φ 0.40mm (12BB) Aluminium frame 30×28 mm |
D | 400 | Half-cell 9BB | POE/Dual glass 2.0 mm white ceramic glaze on rear side glass Wire cell connector Φ 0.35mm Aluminium frame 30x28mm |
E | 370/375 | Full cell 5BB | POE/dual glass 2.5mm, white ceramic glaze on rear side glass Cell connector 0.25×0.9mm Frameless |
Table 1. Manufacturing cases, suppliers, PV modules and related features cited in the present article; a BxC sides (C: coplanar to glass substrate, potentially leading to cell shading)
The present article will cover four key subjects, as follows:
- Lack of international standards adopted by the industry;
- Inhomogeneous bifaciality values, within and amongst manufacturers;
- Effect of module design and Bill of Materials (BOM) on bifaciality;
- Front versus rear-side performance asymmetries.
To conclude, a quick overview vis-à-vis the influence of bifaciality on the PV plant’s economics will be reported, so that the interest in controlling the bifacial properties of the modules at the early stages of development of a PV project is highlighted.
As a matter of fact, guaranteeing the bifacial values during the production of hundreds of thousands of PV modules for a large-scale plant is certainly not a straightforward task. Thus, this article is not a criticism of the activities currently performed by the module manufacturing industry, but a review of the actual picture that a module purchaser should consider when dealing with bifacial devices.
This is an extract of an article first published in Volume 24 of PV Tech Power. The full article can be read here, or in the full digital copy of PV Tech Power 24, which can be downloaded via the PV Tech Store here
References
[1] https://itrpv.vdma.org/
[2] R. Kopecek, J. Libal (2018) Towards large-scale deployment of bifacial photovoltaics, Nature Energy, 3(6) 443–446;
[3] T. S. Liang, M. Pravettoni, C. Deline, J. S. Stein, R. Kopecek, J. P. Singh, W. Luo, Y. Wang, A. G. Aberle, Y. S. Khoo (2019) A review of crystalline silicon bifacial photovoltaic performance characterisation and simulation, Energy Environ. Sci., 12(1):116–148.
[4] P. Tillmann, K. Jäger, C. Becker (2020) Minimising the levelised cost of electricity for bifacial solar panel arrays using Bayesian optimisation, Sustainable Energy Fuels, 4, 254-264