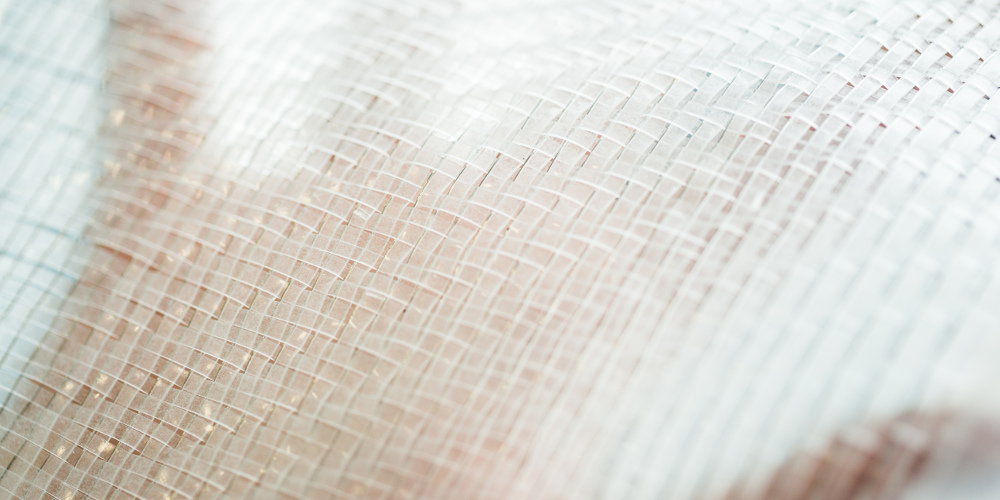
Belgium's imec introduces a new concept: a way of assembling and interconnecting PV cells using a fabric into which conducting and insulating wires are interwoven. Eszter Voroshazi reveals more.
As important as it is to keep improving the efficiencies of PV cells, the challenge in the coming years will be to lower the total cost of electricity produced by PV systems. This brings module manufacturing in the equation.
Unlock unlimited access for 12 whole months of distinctive global analysis
Photovoltaics International is now included.
- Regular insight and analysis of the industry’s biggest developments
- In-depth interviews with the industry’s leading figures
- Unlimited digital access to the PV Tech Power journal catalogue
- Unlimited digital access to the Photovoltaics International journal catalogue
- Access to more than 1,000 technical papers
- Discounts on Solar Media’s portfolio of events, in-person and virtual
Today, the module cost – materials and assembly – takes up over 40% of the total cost of a PV system. So it is really a no-brainer that we should go and look for new materials and assembly techniques to lower that share. But we could do even better: module innovation can improve the lifetime and efficiency of modules, adding an extra lever to lowering the LCOE (levelized cost of electricity).
With this in our mind, our PV research group has tackled modules from various angles. In these blogs, you may have read about alternative interconnection and switching schemes to improve module yield under e.g. fast-changing weather, a condition that classic modules have a hard time with.
Here, I want to introduce another concept: a new way of assembling and interconnecting PV cells using a fabric into which conducting and insulating wires are interwoven. This was an out-of-the-box idea of Tom Borgers, development engineer and module specialist at imec, who has also become our master weaver.
Adding the encapsulant material as weaving material, it is even possible to have the fabric interconnect the cells and encapsulate the assembly in one go. We believe this solves a number of issues in module manufacturing, simplifies the assembly process, and will improve the lifetime and efficiency of modules.
Such new fabrics square with the current evolution in PV interconnection technology, the trend to use more but finer busbars. With three-, four- or five-busbar technology, there is already a clear gain in module efficiency due to smaller shading surfaces. But taking this to its logical end, this leads to a technology where busbars are omitted completely. The first companies are just now introducing busbarless cells that employ a mesh of copper wires to connect cells. Some claim an efficiency boost of 3 to 5%, mainly because the wiring has better reflection characteristics and the denser network of interconnection wires allows a more efficient current collection from the cell. On top, this technology requires less silver, which also lowers the cost.
Metal wires woven in a glass fiber sheet
One of two approaches that we are developing is a scheme for back-contacted cells, around which we formed a project with a number of partner companies, including some from the Flemish weaving industry.
The idea is to interconnect cells with the conducting wires woven in the fabric. Critical for back-contacted cells is to insulate opposite polarities between the cell metallization and the interconnection. So we interweave conductive and glass fibers with a very carefully chosen, yet simple weave pattern. These conductive wires are solder-coated copper wires around which a glass fiber is twisted to insulate them from the cell surface upon positioning. The fabric is placed onto the cells, which have solder paste deposited on the exact locations where the contact with the wires should be made. Then the magic happens: when heated, the solder paste runs through the glass fiber twists and form a solder joint locally between the copper wires and cell metallization.
An ingenious scheme, but one that is specific for back-contacted cells. So what about two-sided contacted cells, or bifacial cells? Weaving, a most flexible art, gave us the answer.
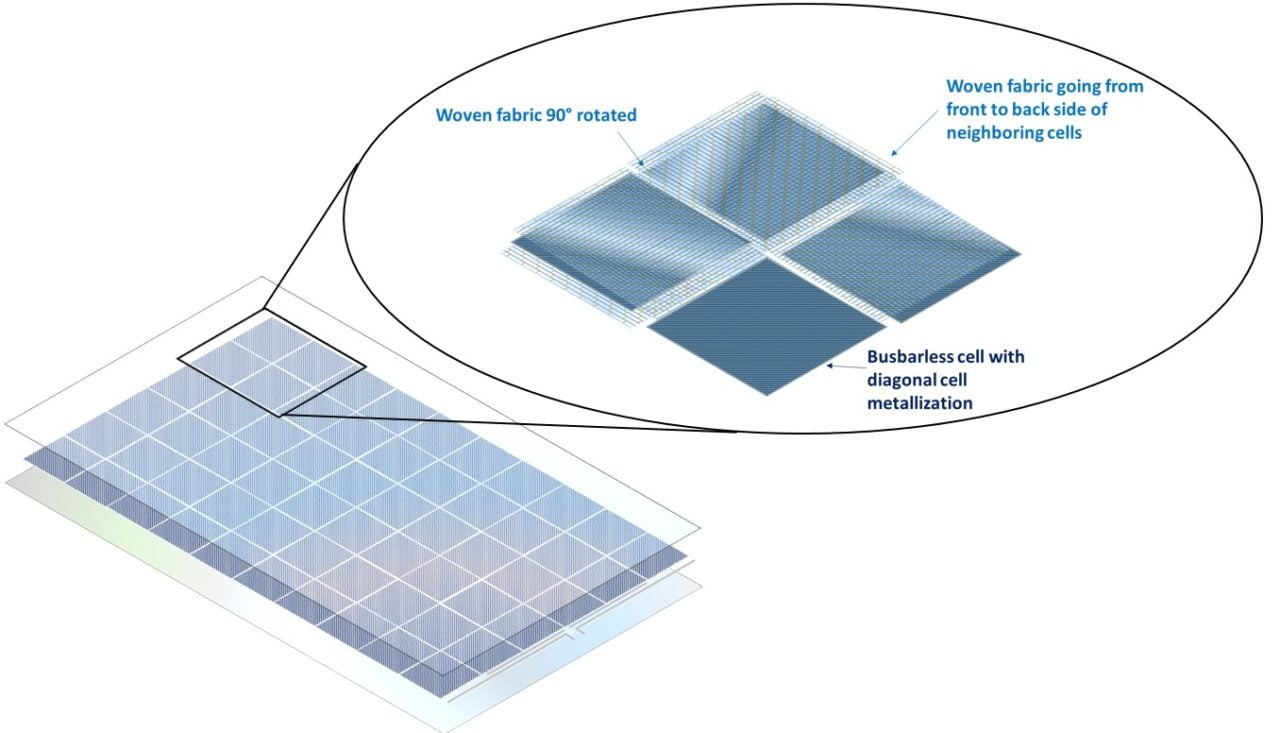
A fabric made from copper and encapsulant
As weaving materials, we obviously need copper wires and an insulating material. As insulator, we could use glass fiber again, but later in the process we have to add a second insulator, the encapsulant. So why not simplify: use one material and weave with ribbons of encapsulant? And if we do that, why not eliminate the step of adding an extra encapsulation layer, and just use the encapsulant material for both the weaving and encapsulation?
The tricky bit, where we still have some way to go, is the exact choices of materials. Because once the cells and the fabric have been laid out, you’ll still need to do soldering and encapsulating. And of course the electrical contacts have to be made before the encapsulant material starts to flow. So we propose one process with two steps: First we solder the wires to the cells at a lower temperature, during which the encapsulant material remains solid. Next, we turn up the temperature to liquefy the encapsulant.
The second innovation we envisage involves the interconnection of the cells. We propose to cut our fabric into sheets the size of two cells. On top of a first cell, the first half of such a sheet is placed. A second cell is then added on top of the second half of the sheet. This broadly resembles traditional stringing processes. The trick comes at the end of a string, where conventionally additional ribbons are added to connect parallel strings. Our fabric allows for 90º turns with the exact same process making the parallel cell string connection much simpler. Another step and superflux materials in the module assembly removed.
Leveraging expertise of weaving industry
This new approach, we believe, has a lot of potential to simplify module manufacturing and lower the LCOE. It significantly reduces local mechanical stresses on the cells because a fabric with an even thickness is placed on the surfaces, replacing the bulky busbars and metal tabs. It also allows to lower the process temperatures considerably. Reducing stresses and temperatures in processing will become a necessity when thinner wafers are introduced. But more importantly, it simplifies the whole assembly process, replacing a number of sequential steps with one single repeated step of placing a sheet and adding a cell. And because these steps allow 90% rotations, the amount of metal needed is reduced without losing a single electron.
For our two approaches, our module expert manually wove the necessary fabrics, experimenting with weaving patterns and materials. From these, we built functional prototypes. Shown our results, the industry and research community were excited, naming these concepts one of the most promising innovations under development. And at the EU PVSEC conference in Münich (June 20-24), we got a slot for a keynote presentation.
Flanders, where our R&D lab is headquartered, has an extensive and rich tradition in weaving, with a number of world-leading producers e.g. in tapestry and technical textiles. And the encapsulant suppliers, some of which are also located locally, have shown interest. So there is sufficient enthusiasm, potential, and experience to turn these new PV fabrics from a concept into a success.
Eszter Voroshazi, imec team leader PV module technologies. The weaving concept is being showcased in a keynote at EU PVSEC in Munich. Eszter can be reached at [email protected]