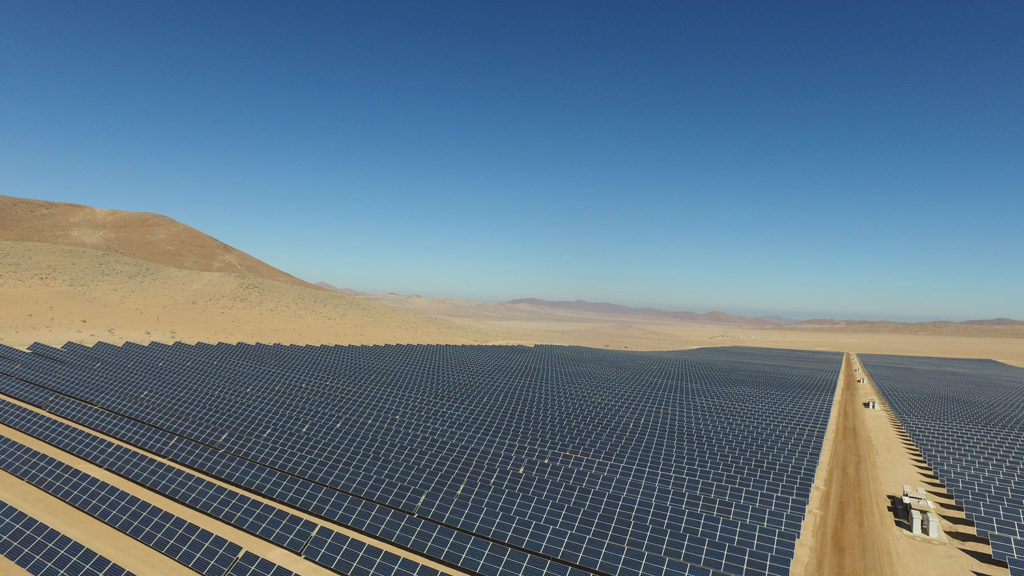
For many years the key performance metric against which Solar PV farms have been judged has been Performance Ratio (PR), essentially a ratio of how much energy a PV plant is expected to produce over a period of time against the amount of irradiance the modules receive. Contracts have been drawn up with clauses guaranteeing PRs of PV plants, and failure of the plants to meet this obligation can trigger heavy financial penalties for the EPC companies who have built them. In some contractual schemes, if PV plants fail to meet a PR by the end of their second year of operation (often called Final Acceptance), it is assumed that the PV plant will underperform by the same amount for the rest of its life. This lifetime might be as high as 25, 30 or even 40 years, and so the penalties to be paid for that shortfall can be very high if a plant is underperforming. It can happen to companies that their simulation assumptions are wrong, or too aggressive, or simply that some unknown environmental factor has upset the result, and the losses for such an error have been, in some cases, quite devastating.
Most companies will therefore be extremely careful with the simulations they produce, and it is very important for them to be able to control the risks and get a handle on environmental variables that might be out of the company’s control. For example, the base PR does not take into account the effect of temperature or wind speed on plant performance. Over time, more sophisticated models have evolved; in some markets temperature corrected PRs have been introduced, to compensate for the fact that unseasonably hot years have a negative effect on the plant performance. In parallel, capacity testing methods such as ASTM E2848 have been developed to establish the relationships of the energy production with both temperature and wind speed via multiple regression techniques.
Unlock unlimited access for 12 whole months of distinctive global analysis
Photovoltaics International is now included.
- Regular insight and analysis of the industry’s biggest developments
- In-depth interviews with the industry’s leading figures
- Unlimited digital access to the PV Tech Power journal catalogue
- Unlimited digital access to the Photovoltaics International journal catalogue
- Access to more than 1,000 technical papers
- Discounts on Solar Media’s portfolio of events, in-person and virtual
These methods have worked quite well up until the present day; they are by no means perfect, but they are fairly straightforward to understand and to calculate, and are easy to include in a contract. As long as an EPC understands properly the loss factors in the simulation they are undertaking, and include a certain amount of cautious contingency, then for a majority of PV plants it is possible to avoid getting their fingers burned, especially for systems with monofacial modules installed upon fixed mounting structures.
Technology is changing, however, and we are now entering a time when a huge market shift is happening towards bifacial modules installed on single-axis trackers, potentially combined with battery storage systems. Bifacial modules make use of the sunlight that is reflected from the ground in addition to the top-side irradiance, and this rear-side irradiance is not as homogeneous as the irradiance coming down from the sky, increasing the uncertainty and the risks of calculating PR incorrectly. Battery systems can also add in another layer of complexity, especially when used in situations with a lot of grid curtailment.
Additionally, climate change is causing ever more extreme weather scenarios, with months being consistently labelled the hottest, the wettest or the driest on record. Although temperature corrected PRs can protect against record breaking temperatures, consistently high irradiances can also mean that clipping losses on plants with high DC/AC ratios can be higher, and drier years will increase the soiling losses without rain to clean the panels. These variations are not taken into account in any of the PR or ASTM calculations, and therefore represent an important risk for any company signing up to a performance guarantee.
The changes in technology and shifts towards more sophisticated technologies are therefore driving an interest in alternative or more sophisticated KPIs that can be used to guarantee system performance, ones which are less vulnerable to changes in the real-world variables that are out of the hands of system designers.
The energy evaluation method
The equation for basic PR is essentially just a very basic model of the PV plant, which assumes a linear relationship between irradiance and energy generation, and which doesn’t take into account any losses. The introduction of temperature corrections or corrections for wind speed make the models slightly more sophisticated, and help to account for some of the most important variables which are out of the designer’s control, but if we want the equation to take into account the variability of other factors, such as clipping, power factor, the variability of cable losses or seasonal variation of soiling losses, we start to find that we are producing a very complex model, essentially similar to those that are used in commercial simulation software packages. This therefore beggers the question: why not simply use the simulation model itself in a contract, instead of using a basic equation?
The IEC standard 61724-3, which has been published since 2016, lays out an ‘Energy Evaluation’ method, the point of which is to obtain a ‘Performance Index’ instead of a PR. The index is obtained by keeping the same simulation model which was used to perform the contractual simulation, and then, at the end of the (usually annual) test periods, running the measured meteorological data from the site back into the simulation model, and comparing the predicted energy value against the real energy value. Depending on the sophistication of the simulation model, Performance Indices will be around the order of 100%, instead of PRs that are often 80% or so.
The advantage of this method is that it allows for a much larger number of climatic variables. As well as ironing out variations due to temperature and wind speed, a sophisticated simulation model can take into account losses due to increased clipping and higher ohmic losses in higher irradiance years, varying power factor being set by grid operators, varying albedo of the ground cover, and even the soiling factor. As well as being a method that can reduce the exposure to risk from environmental factors the plant designer cannot control, it is also an excellent troubleshooting tool. By comparing the expected vs real curve for any single day, issues of plant performance can be more easily identified.
As the technology being used in PV plants grows more sophisticated, the models being used to simulate them are also evolving to take into account single-axis trackers installed over complex topography, bifacial modules, and battery storage, in ways that a simple PR equation simply cannot capture. In the future the Energy Evaluation method may become the only realistic way to really evaluate the performance of such sophisticated projects. However, in order to achieve a wider adoption of this method, the commercially available simulation software packages need to evolve in order to make them more user-friendly to companies wishing to adopt the methodology. Commercial software packages have primarily been designed to make a prediction of yield in the future using historic climate data, and they haven’t really fully developed their potential as performance monitoring tools.
The most important issue is that PR uses in-plane measured irradiance as a starting point, while simulation software usually takes the horizontal irradiance as a starting point and transposes it to in-plane irradiance. This makes a lot of sense when you want to make a prediction of energy in the future, but it isn’t very helpful when trying to assess plant performance once the plant has been built, where in-plane pyranometers are installed. The transposition step can be quite accurate for a fixed-tilt monofacial system, but for tracker systems using bifacial modules, potentially employing sophisticated AI-based tracking algorithms, the transposition is extremely complicated or even impossible to predict accurately, unless the angle of the trackers at every point in time is also input along with the climate data.
Therefore, in order to use the Energy Evaluation method, it would be helpful if it were possible to directly input the in-plane irradiance values, measured on both the front plane AND the rear plane of the PV modules, directly into the model. Additional features that would be helpful would be the ability to input the angles of trackers and changes to grid conditions (such as changing power factor and export limitation) to at least an hourly resolution, and the ability to simulate the plant at the same resolution as the measured data. Many simulation applications are restricted to 1-hour resolution, but far greater resolutions are available from PV Plant SCADA systems. Although such changes aren’t straightforward, such developments to the software tools would be hugely advantageous to the broader PV industry by allowing a broader use of the Energy Evaluation Method in contracts.
Monitoring of bifacial systems
IEC standard 61724-1 is the main standard that sets out the monitoring requirements for PV plants, including numbers and types of sensors required, as well as describing the standard and temperature corrected PRs. The standard is currently under review, with a current forecast publication date for late 2021. Some of the proposed changes are intended to take into account monitoring requirements when using bifacial modules, including additional sensors, and potential formulae for Bifacial PRs.
Bifacial PV systems are complicated, because the ground below the PV modules and spread across a solar farm can vary, both with topography and with changing albedo of ground cover due to types of soil and vegetation. This means that the irradiance that is reflected onto the rear side of the modules will vary throughout the plant, much more than the relatively homogeneous irradiance that is seen on the top-side of the array. Additionally, the ground cover can change throughout the year, in some countries most significantly because of snow, but also because of changes in the vegetation throughout the seasons.
The inclusion of rear-side irradiance will always introduce a higher level of uncertainty into the yield assessment than when using monofacial modules, and so in order to try and minimise this uncertainty, more sensors are needed to measure the rear-side than the front-side, and these are spread out at different points in the plant, for example both at the ends and middle of rows, in order to try and capture as broad a cross-section of the situation as possible.
The type of sensors to be deployed will depend upon the methodology used to calculate plant performance, and what the inputs for this performance should be. If using a bifacial PR, or if using the Energy Evaluation method of IEC 61724-3 in a way that skips over the transposition step, then the sensors should be placed to measure the rear-side irradiance in the same plane as the PV modules. However, if the intention is to use the Energy Evaluation Method with the horizontal irradiance as the base input, then albedometers are used to measure the ground albedo instead; the simulation model then performs a transposition based upon the combination of horizontal pyranometers and albedometers to obtain the rear-side irradiance.
It might well be that the measured in-plane rearside irradiance and the derived rear-side irradiance from the albedometers are different, due to the fact the transposition model in the software is not completely accurate. At present, accurately predicting and assessing the performance of bifacial PV plants is difficult, and more work is required by the industry, research institutions and software developers to quantify the uncertainties in the models and introduce improvements to mitigate the risks.
Availability
Solar PV is a relatively peculiar industry in that the entire contractual performance of a plant is boiled down to one number, the PR or Performance Index, which somehow has to account for all potential problems and liabilities in the PV plant, and this number is often written down in a single contract and pinned to a single head who suffers the consequences if the reality does not live up to the modelling. In many other different types of projects, outside of the solar world, the liabilities are spread out amongst several parties instead of one. So, another solution to the problem of quantifying the performance of ever more complex plants in contracts might in fact be to side step the issue altogether, and instead focus the contractual obligations upon the reliability and quality of components and workmanship instead.
Perhaps additional emphasis or attention could be placed on another key KPI of solar PV – Availability. Availability is a measure of the fraction of uptime of the main equipment on the plant with respect to the total operating time. For solar PV, it is tackled in IEC TS 63019, where the equipment is defined as being ‘available’ if it is capable of providing a service, independent of whether it is actually providing that service or not. Availability is typically defined in O&M contracts at a plant or inverter level. However, this level of granularity can be increased to string level monitoring as well if the equipment is available, and the concept of availability can be extended to other equipment as well, such as trackers.
With PR or even Performance Index, the EPC is in some way guaranteeing the simulation model being used, perhaps even more than they are guaranteeing the quality of the PV plant they are building. This focus on PR can actually obscure a lot of problems; although a higher availability will often mean a higher PR, this isn’t always the case. In fact, on some PV plants, problems in plant quality can in fact be hidden behind high DC/AC ratios; if clipping is high, it is possible for several strings to be offline during the middle of the day and not affect plant performance at all. These problems can fester, multiply, and ultimately become very expensive to repair later on in a PV plant’s life. If string level availability is being measured, however, these problems can very quickly be picked up and resolved, and there is more of a motivation for companies to use higher quality cable and easier to maintain installation methods.
So, perhaps there is an argument for the PV industry to mature to the level of other industries, get rid of a ‘single number’ that tries to embody everything, and instead look at the individual guarantees of manufacturers while relying on availability metrics of inverters, strings, trackers, energy storage systems and communication equipment in order to ensure that the quality of equipment and workmanship is high.
In short, the PV industry is long overdue for an overhaul in the way performance and quality is handled in contracts, and change is becoming more pressing due to ever more complex technologies being used in utility scale PV plants. Perhaps the best contender as a methodology for handling these changes is the Energy Evaluation Method set out in IEC 61724-3, but in order for the industry to be able to implement this methodology, it is important for the developers of simulation software to take note of this standard, and to implement features that make it easier for companies to use measured data from site back in the models that were originally used to forecast future performance.
Bifacial modules introduce a particularly challenging set of factors that increase the uncertainties in modelling, and so it is a particularly pressing challenge for the industry and research bodies to understand and quantify the uncertainties of all the parameters used in simulation models. Perhaps the complexities are so great that we need to look beyond just a single number that defines a PV plant that may be misleading and may even hide quality problems behind it, and instead the industry should be paying more attention to different contractual structures, with more of a focus on KPIs such as the availabilities of the key components in the PV plant: the inverters, the strings and the trackers. Either way, though, as we move into a future of larger plants, greater risks, and more advanced technology, it certainly looks like the industry has to move beyond PR.
Author
Christopher West is head of central engineering for the solar PV delivery unit of Statkraft, with over 10 years working in the PV industry, and experience in managing development, construction and post-construction engineering of large scale PV plants. He is an active member and contributor to IEC international standards.