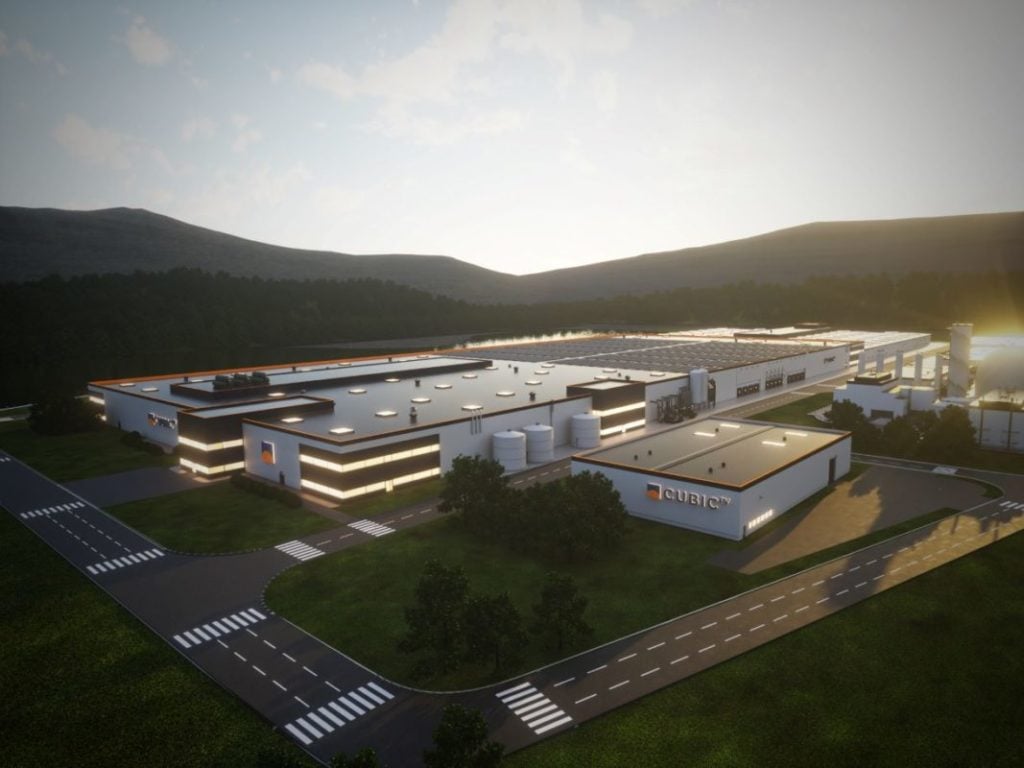
US solar manufacturer CubicPV has signed a long-term supply agreement with South Korean-owned polysilicon producer OCIM to support its planned 10GW solar wafer manufacturing facility.
The two parties signed an eight-year agreement totalling around US$1 billion that will see Cubic receive delivery of “high quality, low carbon and US compliant silicon”, the company said in a press release.
Unlock unlimited access for 12 whole months of distinctive global analysis
Photovoltaics International is now included.
- Regular insight and analysis of the industry’s biggest developments
- In-depth interviews with the industry’s leading figures
- Unlimited digital access to the PV Tech Power journal catalogue
- Unlimited digital access to the Photovoltaics International journal catalogue
- Access to more than 1,000 technical papers
- Discounts on Solar Media’s portfolio of events, in-person and virtual
A subsidiary of Korean chemical industries company OCI Holdings, OCIM’s polysilicon production operations are based in the Samalaju Industrial Park in Sarawak, Malaysia where it has 35,000MT of annual production capacity.
Frank van Mierlo, CEO of CubicPV said: “This agreement with one of the world’s foremost leaders in polysilicon production is testament to our manufacturing capabilities and the progress against our US manufacturing plans. OCIM’s high-quality, US compliant silicon is in extremely high demand, and we are fortunate to lock-in our supply with a trusted supplier.”
CubicPV is planning a 10GW silicon wafer production site, for which it said that under the terms of its agreement OCIM would begin supplying polysilicon in 2025. It said that the facility will be capable of producing both p-type and n-type wafers, but that it expects demand in the US to be for the latter. A location for the site is yet to be confirmed.
Upstream in the US
The supply of non-Chinese polysilicon to CubicPV’s operations could be a boon for the US solar manufacturing industry.
According to Bernreuter Research, OCIM was the 8th largest polysilicon producer in the world in 2022. The top four are all Chinese and thus would face import barriers to the US market, if there were any significant upstream PV manufacturers to supply. But, as it stands, capacity announcement of cells or further upstream components in the US are lagging significantly behind the production announcements for modules.
In a guest blog published by PV Tech earlier this month, Martin Meyers, principal consultant at the Clean Energy Associates (CEA), wrote that the US would be relying on imported cells for the foreseeable future. By the CEA’s estimation, solar cell capacity announcements due to be online by 2027 are around 33GW compared with over 150GW of module capacity plans. Those projected cell imports will also be subject to the import constraints like the Uyghur Forced Labor Prevention Act (UFLPA) and antidumping/countervailing duty (AD/CVD) tariffs that have plagued US module supply in recent years.
Imported cells also pose a challenge for solar manufacturers or developers looking to take advantage of the Inflation Reduction Act’s (IRA) domestic content tax adder, which calls for 40% of a module’s total cost to come from US-made products, rising to 55% in 2026.
As discussed in an interview with Canadian solar manufacturer Heliene earlier this year (premium access), the cell constitutes a large part of the cost of a module and without domestic production the adder will be out of reach for the majority of silicon-based solar manufacturers. The beginnings of domestic wafer production would simplify issues facing the industry around these tax incentives and wider supply transparency.
Van Mierlo spoke with PV Tech Premium in early 2023 about CubicPV’s long-term vision for US-made solar and his projection that with industry expansion and the Inflation Reduction Act’s incentives, US modules would be ‘the world’s most cost-effective’.