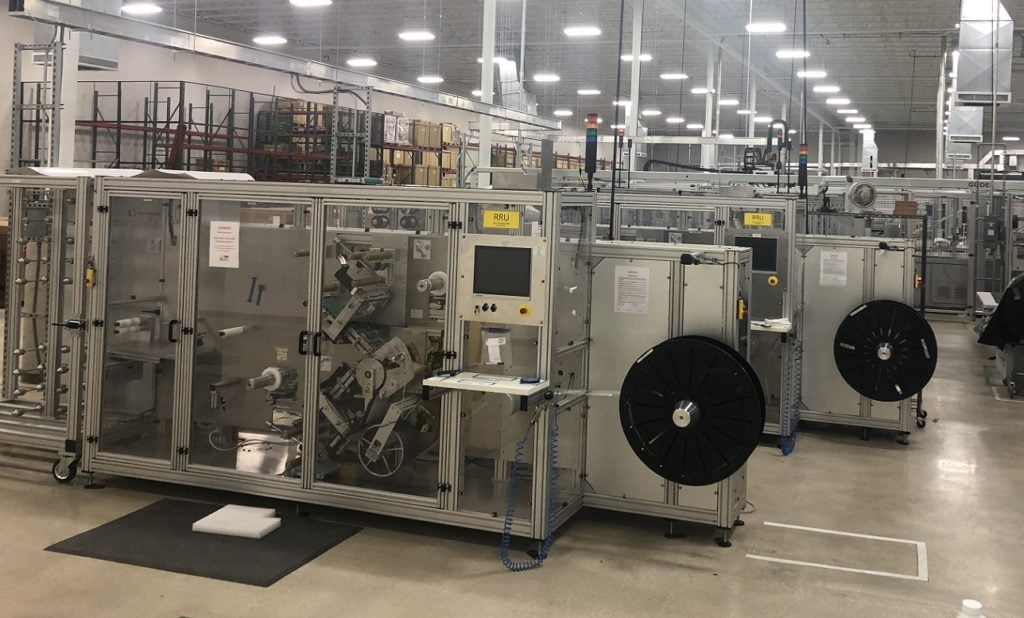
The IRS’ guidance on the domestic content tax bonus for solar projects under the IRA “makes it difficult for developers to attempt to access the 10% bonus ITC”, according to Martin Pochtaruk, president of North American solar PV manufacturer Heliene.
In May the Internal Revenue Service released guidance on the Domestic Content adders included under the investment tax credit (ITC) in the government’s Inflation Reduction Act (IRA). To qualify for the 10% extra tax credit adder, renewable energy projects – including solar PV – will need to show that 40% of the cost of their materials is represented by US-made products. From 2026, this level will rise to 55%.
Unlock unlimited access for 12 whole months of distinctive global analysis
Photovoltaics International is now included.
- Regular insight and analysis of the industry’s biggest developments
- In-depth interviews with the industry’s leading figures
- Unlimited digital access to the PV Tech Power journal catalogue
- Unlimited digital access to the Photovoltaics International journal catalogue
- Access to more than 1,000 technical papers
- Discounts on Solar Media’s portfolio of events, in-person and virtual
Manufacturing
As it stands there is relatively scant module manufacturing capacity in the US. Plans are in the pipeline, and companies like Qcells with its vertically integrated plans for Georgia, First Solar and Enel Green Power have all made significant announcements, but they’ll take time and won’t come close to being able to supply the US’ 30-40GW deployment predictions for 2023.
As far as the guidance suggests, solar modules and their components are subject to the 40%/55% requirement, including cells, wafers, glass, encapsulant and frames. Components like trackers and inverters are also included. A separate criterion exists for steel products, which must be 100% US-manufactured. This would apply to steel racking in a PV array but not to steel included in any of the module components.
Speaking to PV Tech Premium, Sagar Chopra, senior research analyst at energy insight company Wood Mackenzie points out that: “The guidance also does not address the electrical balance of system components like transformers, switchgear and cables which are key manufactured products that are essential parts of the PV system the requirements.”
Woodmac says that there are “a few” domestic manufacturers of these balance of system products in the US, but it could not confirm specific numbers. If these were included in the domestic content criteria, it might become easier to meet the 40% threshold on a cost basis, particularly for developers and asset owners. Chopra also cites the electrical balance of system sundries as a potential factor in the way companies might find novel ways to make the domestic content requirements more achievable, but that clarification is still needed.
“What is important is how that part of the IRA is attracting component manufacturers to set up shop in the US”, says Martin Pochtaruk, “It’s not just module manufacturers…how do we incentivise more manufacturing of backsheets and encapsulant, and frames and ribbon and all of the other components that go into a module?”
He emphasises the potential significance of aluminium manufacturing, to produce frames for modules. Heliene has a partnership with a company that produces its frames in both the US and Canada, but Pochtaruk says that the industry as a whole is not set up to produce them on a large scale.
“The aluminium industry in the US and Canada is highly protected with trade actions, so the price in the US and in Canada is higher than most countries on earth. It has been very difficult to find aluminium extruders interested in making frames for modules. It’s just kilometres and kilometres of the same extrusion, there’s nothing interesting or expensive about it so they don’t feel compelled to take the business.”
Tracker manufacturing is present in the US through Nextracker’s steel component facilities, but inverter production is somewhat limited besides Enphase’s recently opened facility in South Carolina.
From a developer’s perspective, US developer Silicon Ranch tells PV Tech Premium: “recently released IRA guidance has raised several questions, notably around how to determine what constitutes domestically manufactured products, that make it challenging to assess how the rules apply to projects currently in development or construction. While the IRA stands to be one of the most significant pieces of legislation for domestic manufacturing and the transition to renewable energy, these challenges put at risk the nature of what its authors intended.”
Cost
The cell is by far the most expensive part of the solar module – Pochtaruk says that it represents around 50% of the price of a module on average. Without domestic cell capacity in particular the domestic content adder may be obsolete for solar PV.
PV Tech’s head of research Finlay Colville published a series of features saying as much in the last few months, discussing the need for the IRA to prioritise solar cell manufacturing and whether a 100GW cell foundry is could be the way to wrest some control of the global supply chain back to the states from China.
Pochtaruk says of Heliene’s operations: “With no US made solar cells or solar glass, even when all other module components are domestically produced and assembled, like Heliene’s, they only provide around 17 or 18 cents of the costs added by developers toward their 40% calculation.”
Under the guidance, a ‘Manufactured Product’ is considered to be made-in-America if: “(1) all of the manufacturing processes for the Manufactured Product take place in the United States; and (2) all of the Manufactured Product Components of the Manufactured Product are of US origin.”
In effect, this means that if any included ‘Manufactured Product Component’ of a module (cell, glass, encapsulant, wafers, frames etc.) is imported to the US, the module is no longer considered a US-made product. In the overwhelming majority of cases in the US, a fully-US made module isn’t currently possible.
As a result, manufacturers would be required to disclose their entire pricing stack for every component that has gone into the module in order to prove compliance with the 40% threshold. “It’s going to be a big ask from manufacturers to reveal their pricing structures including manufacturing costs, overheads and margins,” Sagar Chopra says. “The calculation for domestic content is cost-based, manufacturers must provide full transparency on their cost stack and margin levels, which is impractical and inconvenient for manufacturers.”
Some manufacturers – like Heliene – already do this, but it remains to be seen whether the majority of companies will play ball. Solar supply chains are increasingly under scrutiny and whilst manufacturers will likely be looking for ways to secure and clean up their supplies, the process of sourcing and breaking down costs to pass benefit onto their customers may be cumbersome.
“We sell ‘cost plus’,” Pochtaruk says, “So we issue our clients with the costs, the only thing we fix is the margin. To be able to do that you need to disclose your exact costs, component by component…you’re basically opening the kimono for everybody to look. We’re fine with that.”
The Long-Term
According to Chopra: “A 10% bonus credit is attractive, but it remains to be seen how competitive domestic components are against imported goods and whether the 10% bonus adder is attractive to offset any premiums from sourcing domestically.”
US-made products are going to be more expensive than imports, on the whole. Most PV modules – around 80% – come into the US from Southeast Asia where predominantly Chinese manufacturers have set up factories and supply chains. These are generally going to be cheaper than domestic products.
The long-running saga around the anti-dumping and countervailing duty tariffs is rooted in this disparity and what the US sees as unfair price manipulation, and subsequently market domination, by Chinese made or owned modules.
“A Chinese cell you can buy at 12/23 cents per watt,” Pochtaruk says, “but a cell that you import in the US, made outside of China with non-Xinjiang polysilicon, is roughly 20 cents.”
The question then comes down to whether the 10% is worth it compared with the premium for domestic products and the already increased prices that developers are paying for US-approved imports. The smaller the project, generally the higher the overall price per watt for installation and materials. A rooftop or community solar installation might then see a 10% price cut as too big to ignore. Pochtaruk tells PV Tech Premium that Heliene is seeing average install costs of around US$1.60 per watt for rooftops and closer to US$1.20 for community solar, which would see a 12-16 cent saving on every installed watt of power.
A utility-scale project would be under a dollar per watt, and as such the extra work at all levels may not be worthwhile for a 10% discount.
Pochtaruk continues: “We’re seeing that for developers installing community solar up to 5MW and rooftops – which is a few GW a year – and commercial and industrial, to leave it on the table is a lot of money.”
The domestic content adders are ultimately tied to the availability of supply in the US, which is currently subject to time. Silicon Ranch explains their position as a developer: “In the long-term, our company is well-positioned to leverage the IRA due to a pre-existing commitment we made to source materials as locally as possible, both in an effort to guarantee supply as well as optimise the positive economic impacts our projects can have on the local communities and regions in which they are located.”
“The long-term” might be key here. Like Heliene’s relatively small-scale US aluminium partnership, Silicon Ranch has made what look like concerted efforts to establish domestic partnerships and supply wherever possible. They have module supply agreements aplenty with First Solar – who produce a fair proportion of their Cadmium Telluride thin-film panels in the US – as well as Nextracker.
But the domestic content guidance as it stands is quite unclear, and the time that it will take for capacity to come online across the solar value chain in the US will probably make it difficult for developers and manufacturers to participate and meet the requirements of the adder.
For analysis of the implications for domestic content in the battery energy storage industry, see our sister publication EnergyStorage.news.