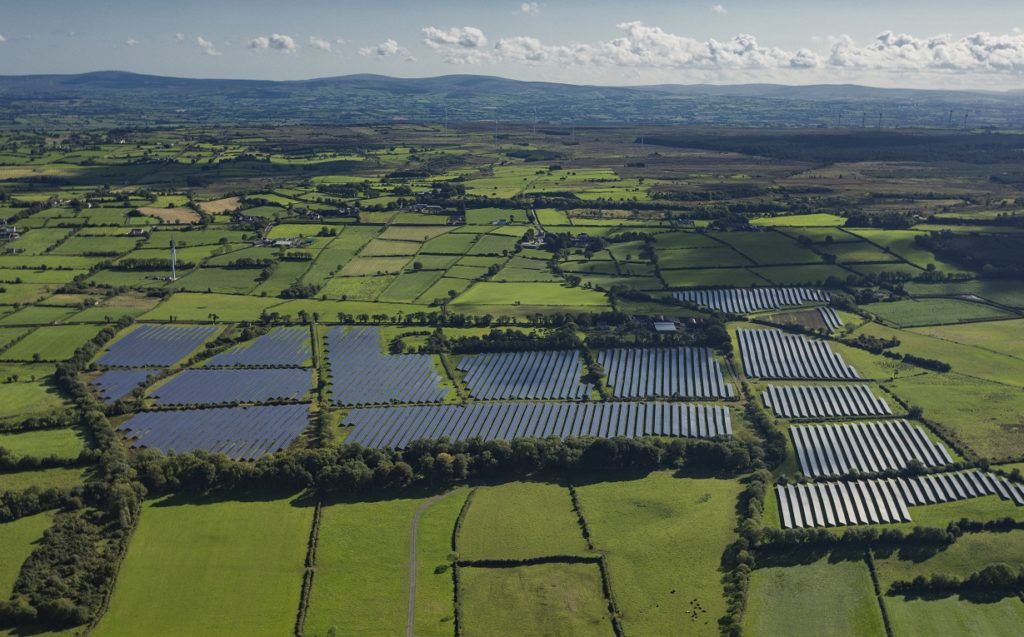
Curtailment is a rising threat to solar PV, exacerbated by antiquated grids and a power system in transition. But green hydrogen electrolysis is emerging as a potential solution to the problem, taking excess solar and converting it into hydrogen for either long-duration storage or use by other industries, writes Alissa Tripp, senior research and commercial analyst at Octopus Hydrogen.
As the UK charts a course towards net zero, renewable power from wind and solar farms will increasingly weigh on an antiquated grid until the system is transformed into one that can handle significant volumes of intermittent generation.
Unlock unlimited access for 12 whole months of distinctive global analysis
Photovoltaics International is now included.
- Regular insight and analysis of the industry’s biggest developments
- In-depth interviews with the industry’s leading figures
- Unlimited digital access to the PV Tech Power journal catalogue
- Unlimited digital access to the Photovoltaics International journal catalogue
- Access to more than 1,000 technical papers
- Discounts on Solar Media’s portfolio of events, in-person and virtual
To date, curtailment has been a key tool for managing grid constraints and locational issues around generation. However, developers such as Octopus Hydrogen are driving forward the nascent green hydrogen market and presenting a potential solution to these problems. Here we explore how electrolysers co-located with solar installations can be mutually beneficial as we transition towards a zero-carbon grid.
The role for green hydrogen
Electrolysis is the process of using electricity to split water into hydrogen and oxygen. If low-carbon or renewable electricity is used then the hydrogen produced is considered green. With current technology it takes roughly 60kWh to produce 1kg of green hydrogen, but when it’s used in a fuel cell it achieves roughly 30kWh out. This round-trip efficiency means green hydrogen isn’t suitable for all applications; it makes much more commercial sense to electrify sectors such as cars and domestic heating, for example.
However, green hydrogen plays a key role in many countries’ decarbonisation plans. Its benefits can be particularly felt in hard-to-abate sectors such as heavy goods vehicles (HGV) and out-of-town bus routes, where the weight of lithium-ion batteries rules out electrification. Aviation and shipping are other sectors where green hydrogen fuel replacement is being explored, and in heavy industry such as steel production green hydrogen is a promising replacement for coking coal.
How does an electrolyser benefit a solar farm?
When embarking on a green hydrogen project, developers must decide on the renewable power source. Co-location with wind produces more green hydrogen than with solar due to higher load factors, but in the UK that likely means production in Scotland. This introduces higher logistics costs to move the gas south, and potentially also higher development costs due to the terrain and isolation of some Scottish wind farms.
Solar already tends to be located in the south of the UK close to where demand is likely to emerge, resulting in more attractive logistics costs. Both wind and solar co-location require generation forecasting, but it’s easier to have an idea of the shape of solar generation in an upcoming week than it is for wind. This lends itself to scheduling of gas production. However, for a project to go live it must be beneficial to both the electrolyser and solar developer – which begs the question: what value can an electrolyser add to a solar farm?
Overcoming network constraints
Solar farms are often forgoing revenue due to active network management (ANM), where they agree to the local distribution network operator (DNO) controlling how much power they can output at certain times. This is known as curtailment, and is the option many solar developers opt for in the development phase because the alternative is reinforcing the local grid, which can be expensive and have a long lead time.
The result of ANM is that during these times of curtailment solar farms will not be exporting as much energy as they are capable of, and because payment is on exported volume the solar farm’s revenue stream is reduced.
Looking forwards, with an increasing number of intermittent generation connections, and particularly on local grids where a ‘last in, first out’ approach is used by DNOs to assign ANM connections, curtailment will increasingly eat into the potential revenue of solar farms. As solar farms are added to the grid and without systemic grid transformation, curtailment for these new developments could be anything from a few percent of expected annual export to tens of percent.
“Electrolysers of 5 – 20MW scale provide an ideal complement to solar farms of up to 100MW, providing a much-welcome revenue stream for some of the power that would otherwise have been curtailed”
This is where electrolysers can come in: electrolysers can be directly connected via a private wire to the solar farm, with a modest import grid connection to satisfy power demand at times when the solar isn’t generating. With well-planned commercial structuring the electrolyser can have no impact on the price the solar developer sells its exported power for; indeed, it could even provide more competitive pricing.
The behind-the-meter connection allows the electrolyser to use power that can’t be exported due to the ANM connection, i.e. curtailed power. This provides the solar farm with access to a pricing mechanism for its curtailed power, restoring some of the revenue stream lost to ANM. As curtailment is generally still a modest subset of total production this alone isn’t enough to make a solar project viable in the development phase. But it’s a helpful and non-negligible revenue stream that only increases in value as curtailment on the distribution grids increases. Solar farms are currently being commissioned without revenue for curtailed power, so this is pure upside for the solar developer.
Achieving the best balance
The optimal configuration of solar and electrolyser is not to have them at the same capacity, but to scale back the electrolyser to best balance power from the solar and power from the grid. Take a 70MW solar farm as an example: if this was connected to a 70MW electrolyser then only during solar peak in summer would there be enough solar generation to come close to making use of the electrolyser capacity. The rest of the time the electrolyser would either be idle or drawing power from the grid, incurring expensive grid charges.
A more suitable alternative would be to connect a 10MW electrolyser to the 70MW solar farm via private wire, with a grid import connection of perhaps 2 – 4MW. The electrolyser would then draw the first 10MW of generation from the solar and the rest of its power from the grid. This results in the electrolyser using approximately 40% of the solar farm’s annual generation, with the remaining 60% exported to grid. Octopus Hydrogen has assessed alternative structures, such as a simple off-grid solar and electrolysis setup but concludes that this is the optimal configuration.
It allows the solar developer to achieve maximal prices for power whilst preserving flexibility in how the electrolyser can be run.
When it comes to utilisation of the electrolyser, it turns out that the best value is not achieved by running it at 100% and maximising the gas production. This is because the price of power is roughly two-thirds of the cost stack when it comes to producing green hydrogen. Power prices vary greatly by half hour just before delivery and it turns out that 40 – 50% average utilisation is the best way to run an electrolyser, turning it up in times of high wind and solar generation, and switching it off during expensive peak periods. Through winter the electrolyser will be drawing relatively more power from the grid than the solar farm, so it’s important to have an import connection that will suffice for the required level of hydrogen production.
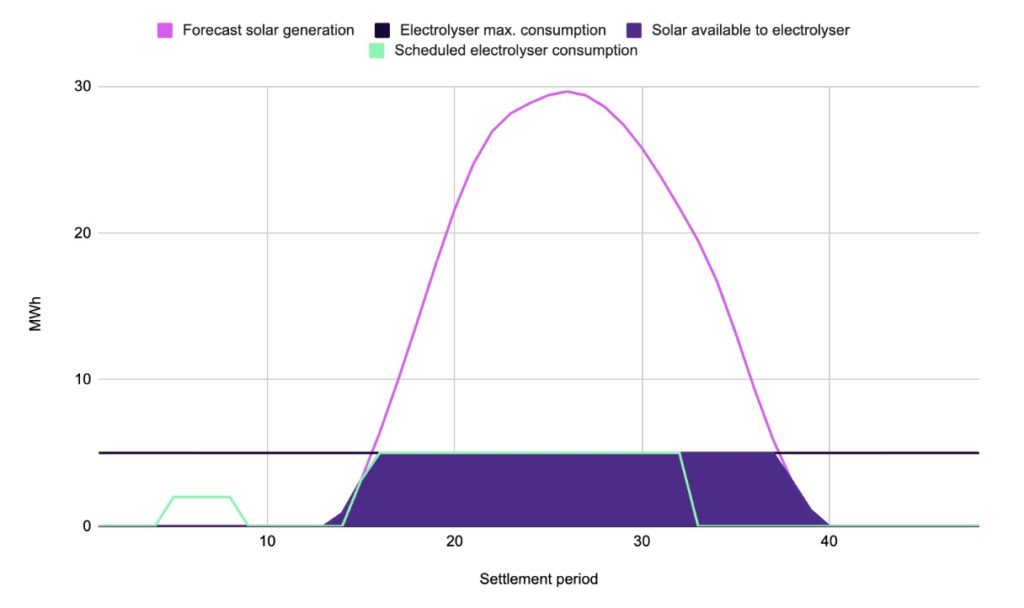
Equipment and expertise
To paint a picture of the physical set up, a 10MW electrolyser and its associated kit would require about an acre of land, with enough space for an HGV turning circle. The main pieces of equipment required are an electrolyser with a water supply, a compressor to compress the gas to the required pressure for the offtaker, and either mobile or static storage. If offtakers are coming to the site to refuel directly then a refuelling unit will also be required, though this can be combined with the storage. Supply chain lead times can be up to 12 months, and the configuration of all this kit and the tailoring of it to specific solar projects requires a high level of engineering expertise.
The obstacles to achieving planning permission are not dissimilar to those faced by battery projects. However, unlike batteries, which overwhelmingly attain their revenue streams via ancillary services, a deeper knowledge of energy markets is required to make an electrolysis project viable. This is because the bulk of the returns made on an electrolyser depend on how effectively demand is shifted throughout the day, rather than in frequency response. Octopus Hydrogen has utilised its UK power expertise to build software that allows remote controlling and optimal scheduling of hydrogen production. This allows a hydrogen producer to minimise the cost of power and maximise the greenness of gas produced.
Limits to retrofitting
In terms of physical feasibility, it is perfectly possible for electrolysers to be retrofitted to existing solar developments, but in practice this is unlikely to happen due to the requirements of green hydrogen subsidies. One such subsidy comes from the Renewable Transport Fuel Obligation (RTFO), whereby certificates are awarded for green hydrogen sold into transport. Similar to the UK’s Renewable Obligation Certificates, these can be sold into the market of participants who must comply with the RTFO.
This subsidy has an ‘additionality’ requirement on the power used in the electrolysis, dictating that it must be from new-build renewable connections. Curtailed power from existing farms does also qualify, but the level of curtailment most existing sites are subject to provides an insufficient load factor to make the commercials of an electrolyser project there stack up. Other subsidy schemes such as the Hydrogen Business Model also include additionality criteria as part of their assessment of applications, but it’s not a requirement.
Solar to play a key role in green hydrogen production
The UK’s plans for decarbonisation rely on building more and more wind and solar, which consequently comes with ever higher levels of curtailment. Electrolysers of 5 – 20MW scale provide an ideal complement to solar farms of up to 100MW, providing a much-welcome revenue stream for some of the power that would otherwise have been curtailed.
At the outset of the green hydrogen industry the combination of renewable generation location and offtaker demand will dictate where the projects are within the UK. As the market matures and logistics can be handled at scale it is likely that more production will come online abroad. In addition to locations being skewed towards demand hubs, places with an abundance of space and cheaper, more reliable renewable energy are strong contenders to become green hydrogen production hotspots, where electrolysers can be installed in the hundreds of megawatts.
Solar will play a key role in fuelling the production of green hydrogen. Though the benefit electrolysis can offer solar farms today mainly revolves around providing revenue for curtailed power, in the future green hydrogen will play a much more central role in the commercials of newbuild solar.
Author
Alissa Tripp is the senior research and commercial analyst for Octopus Hydrogen, responsible for research into global hydrogen subsidies and energy systems, and analytics to assess the commercial viability of electrolysis projects. She has a background in renewable energy trading and interest rates strategy.