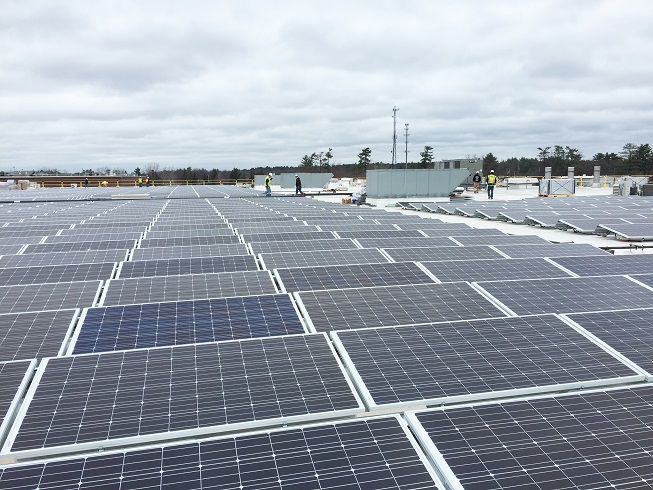
A growing regulatory burden on PV mounting manufacturers in the US has prompted some of the leading players to set up a new trade body to represent their interests. Ben Willis reports on how the new body’s members hope to turn back the rising tide of red tape. This feature originally appeared in the seventh issue of PV Tech Power. To be emailed every issue of PV Tech Power first, and a host of other benefits, sign-up for a free PV Tech Essential membership today.
Unlock unlimited access for 12 whole months of distinctive global analysis
Photovoltaics International is now included.
- Regular insight and analysis of the industry’s biggest developments
- In-depth interviews with the industry’s leading figures
- Unlimited digital access to the PV Tech Power journal catalogue
- Unlimited digital access to the Photovoltaics International journal catalogue
- Access to more than 1,000 technical papers
- Discounts on Solar Media’s portfolio of events, in-person and virtual
It would probably be fair to say that of all the components in a PV system, mounting – or racking – is the element that gets least public attention. Modules, as the engine room of an array, generally generate the most column inches, while in recent years increasing sophistication and competitiveness in the inverter space have ensured that segment has received plenty of interest. Mounting systems, meanwhile, frequently occupy the ‘everything else’ category that lumps them together with everything from cabling to switching under the catch-all title of ‘balance of systems’.
For those involved in this vital part of the solar value chain there is clearly frustration at the lack of profile mounting manufacturers get, particularly given the nature of the product they produce.
“In some respects I think it’s the most complex part of solar today,” says Jeff Spies, senior director of policy at US racking manufacturer, QuickMount PV. “I’m not going to deny that making an inverter work properly with all the sophisticated micro-electronics isn’t challenging, but [it’s made in] a controlled factory environment like a module is. With a racking system we’re at the mercy of an installer doing it the proper way. And because of the tremendous variations that exist in racking systems, we’ve got a challenge on our hands, no two ways about it.”
And Spies’ frustrations are about more than just pride. Adding to the basic complexity of a mounting system is the fact that as an essentially structural element it is subject to a swathe of building, fire and electrical codes that other components such as modules are not. In the US, these codes are enforced locally by thousands of different authorities, and it is not uncommon for local officials to interpret the rules in their own way. In some extreme cases, authorities have used the powers available to them to redraft some of the blanket codes to fit their own particular circumstances, creating an additional layer of red tape for mounting suppliers to navigate.
Tipping the balance
The combination of technological complexity, the increasingly onerous weight of bureaucracy involved in producing code-compliant products and the fact that those in the mounting sector often feel overlooked recently prompted racking manufacturers in the US to take matters into their own hands. Earlier this year, under the umbrella of the Solar Energy Industries Association, the main US solar trade body, a number of the country’s leading mounting manufacturers joined forces to launch a new committee to represent their interests at a national level.
The thinking behind the PV mounting system manufacturers committee (MSMC) is that as a segment of the industry that is being asked to take on more and more of the complexity and regulatory burden of PV system integration, manufacturers needed their own voice to ensure their interests are communicated to those involved in making the rules.
“We have a big responsibility within a PV system,” says Mark Gies, vice president of reliability and compliance at PanelClaw. “It’s been an ongoing discussion that I have had as well as all of our competitors – that we play an important role; we’re the ones that are looked to, to make sure things don’t fly off the roof. But yet we don’t really have a unified voice. And when we individually talk to stakeholders, we don’t have the gravitas that a Trina who’s a major module manufacturer might have, or on the other side from a permitting perspective, the City of LA or these big cities that have a lot of power.
“As the industry changes, we decided that we needed a unified voice so that our collective expertise is tapped into. With a unified voice, people pay attention more; it’s a louder voice as opposed to a lot of little voices.”
Influencing codes
The main focal point for the committee will be to ensure that it is heard in the processes that go into the production of the various codes to which racking systems are subject. Spies is blunt in his view that all too often codes are developed by people who “don’t know what the hell they’re talking about”. “This is a common theme in solar: that we’re seeing code requirements put into place where there’s only perception of a problem, but no real problem that’s been proven,” he says. “So they’re finding solutions to problems that don’t exist often.”
The main code for mounting is UL2703, but others such as UL1703 for modules and UL1741 for inverters also have some cross-over into racking territory. Looking more closely, the main areas impacting racking systems and covered in the various codes are bonding and grounding, mechanical loading, fire classification – how flammable a system is – and others such as the new setback requirements governing the spaces that must be left for firefighters.
Again, Spies is critical of many of the codes that have been drawn up. “In my opinion many of them have not been developed with any input, or very minimal input, from the PV industry. The code-making community claims they’ve got input, when in fact they’ve got one or two individuals often whom don’t have much engagement on that side of the business. So in my opinion we’ve seen a substantial increase in codes and standards which have had little or no input from the mounting and racking sector,” he says.
According to Gies, the ongoing work to update UL2703 will be one of the first jobs for the committee to influence. His hope is that ideas agreed upon by the MSMC on how to evolve 2703 will have greater import by virtue of the fact that they’ve got the backing of a number of companies rather than just one. “We now have a group to bounce ideas around so it’s not just a case of ‘me’ making up something that will help ‘my’ company,” he says. “And then when we go to the people who vote on it, we can say this is not just me, 20 of us have agreed on this point. It puts more weight behind it.”
LA story
Aside from collaborating with the relevant code bodies on drawing up and refining the overarching codes, there will also be instances where the new committee needs to work with individual jurisdictions. Indeed one of the first tasks the body has set itself is to work with officials at LA County on some additional requirements they have introduced on the safe bonding and grounding of mounting systems to reduce shock or fire hazard.
“The county feels the current codes they have in place aren’t really addressing all the needs that they feel they have there,” says Justin Baca, vice president of markets and research at SEIA. “And they wanted to either change or go above and beyond what was existing and develop a set of requirements they were going to apply specifically to LA County. And they’ve been working with the committee and members now to try to make sure that what they’re asking for is in fact achievable.”
There will of course be a limit to the extent to which the committee will be able to work with authorities on a case-by-case basis. But with California accounting for some 50% of US residential installations, and LA one of the key markets in the state, it made sense for the committee to single this case out as one to tackle directly.
And Gies says it’s highly likely that the committee will be working in this way again – targeting city or county authorities that are looking to introduce their own interpretations of codes. “We’d rather not see individual counties or cities take on their own rules, which make it harder for people to get projects permitted,” he says. “Our position is – there is a committee on the standard trying to update the code, take your ideas up to code [level] then everyone will have to follow it. We’ll be talking to other cities. Portland Oregon is another that has sort of created own rules – so that’s in store to collaborate with these major public agencies.”
Cutting soft costs
Ultimately, the committee’s overriding objective is to avoid a situation where there is a patchwork of different rules in different parts of the US. And this goal isn’t just about making life easier for hard-pressed mounting manufacturers, adds Gies. One of the perennial problems solar encounters in the US is that the so-called soft costs – all the costs that arise from the non-hardware elements of putting a system together – are frequently higher than in other parts of the world, and differ wildly from area to area within the country.
Gies believes that the very issue the committee has been set up in part to tackle is a key factor explaining the US soft cost conundrum. Therefore, if the committee is in some way successful in addressing the issue, the knock-on benefits for the whole US solar industry could be significant.
“There are multiple levels [of jurisdiction] – federal, state and the locality,” he says. “And once you get to the level where you’re actually talking to the people who are signing off on projects, everyone’s subjective, they have their own interpretations, so it turns into this crazy mix of having to jump through different hoops: for one project, one thing is an issue, the next project something else completely different is an issue.
“People talk about soft costs as being a big thing to try to reduce; this is where it really hits home. We’re spending a lot of resources in getting through the hurdles, getting things permitted and approved, you have to pay extra engineers, and everyone’s interpreting it differently. There’s a lot of opportunity to standardise – and what’s happened with racking is that a lot of functionality aspects that are really tied in with code and regulation have come to us. We’re the section of the industry that gets looked to, we’re the ones that go through the meat-grinder to make sure the systems are certified and approved.”
Spies agrees: “When we talk about the factors that increase the cost of solar, there’s no doubt in my mind that racking is the number one factor today. It used to be module price declining was the most significant factor in the cost of solar; today it’s the cost of the racking and the rules that you have to follow to get that racking system assembled and inspected. So that’s part of the challenge – that we have the most complicated product sector in terms of how it should be done correctly.”