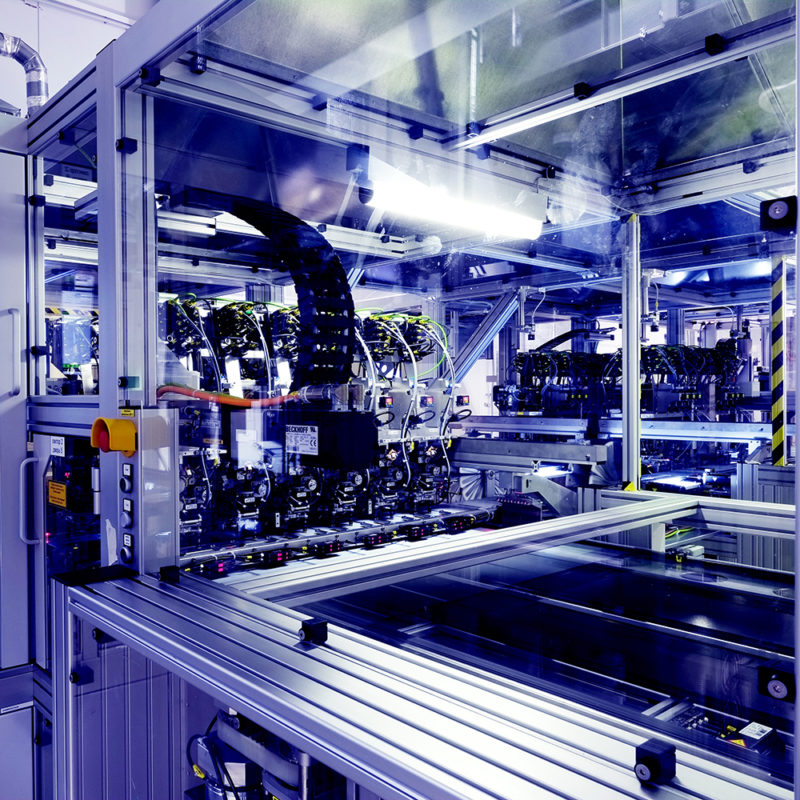
While Mono-PERC is the eminent solar cell technology presently, its dominance is expected to be short lived with n-type TOPCon cells primed to takeover. But when will that technology shift happen? What does it mean for heterojunction? And what does that mean for tandem cells or perovskites? Liam Stoker finds out
There’s an important caveat to make with any forecast relating to the solar industry: it’s a perennially and notably difficult industry to predict and, if anything, this is no truer than on the technology side. The industry shifted to 600W+ modules at breakneck speed and the rate at which nascent technologies and approaches such as TOPCon, heterojunction and perovskites are commercialised is just as uncertain.
Unlock unlimited access for 12 whole months of distinctive global analysis
Photovoltaics International is now included.
- Regular insight and analysis of the industry’s biggest developments
- In-depth interviews with the industry’s leading figures
- Unlimited digital access to the PV Tech Power journal catalogue
- Unlimited digital access to the Photovoltaics International journal catalogue
- Access to more than 1,000 technical papers
- Discounts on Solar Media’s portfolio of events, in-person and virtual
But while specific forecasts are difficult, trends and the broader direction of travel is evident. While the adage ‘bigger is better’ has obviously struck a chord with many in the solar sector in the recent past, wafers, cells and modules are unlikely to get much bigger – physically, at least – than those available today.
Jenya Meydbray, chief executive at module testing firm PV Evolution Labs, believes that in terms of physical size, solar modules have hit a ceiling. Today’s installation practices and technologies, coupled with how they are designed to withstand various elements and forces in the field – especially in the face of wind, hail and snow – are designed around modules being of a certain size and standard. Taking modules materially larger would require wholesale changes. “There’s a lot of small adjustments of the design that all stack up to be a pretty big headache for installers or require a lot of planning,” Meydbray says.
Any wider, and tracker mounts will have to grow taller – impacting on component and balance of system (BOS) costs – due to the deflection of the middle of the glass travelling farther and the need to prevent it from touching the torque. Taller modules would however catch more wind, exerting more pressure on the module, while also getting closer to the ground at full tilt, requiring taller posts to clear any growing vegetation beneath the panel. Any repowering plans based on legacy designs would also require ripping up and starting again if module schematics changed materially in the future.
Dana Olson, global solar segment leader, Energy Systems at technical advisory DNV, concurs, stressing that “formidable challenges” in pushing wafers and cells would need to be surmounted before any further shift in size. Modules larger than today’s modern variants would also place greater structural challenges on a project’s design – especially when using the more durable double-glass bifacial format – due to the weight impact. Mounting and tracker providers would need to catch up with any further increase in size and weight.
This is also before any consideration is given to shipping, which continues to be a thorn in the side of project developers and component manufacturers alike. With the cost of shipping a container from Asia having risen by at least four-fold in the past year, it’s become imperative to ship as many modules and watts per container as possible. Stretching modules any larger could require an overhaul of container packing which could, in turn, reduce the amount shipped in each container, making each watt shipped more expensive in the process.
It is for these reasons that standardisation efforts launched by module majors, intended to set an industry-standard (or as close to a consensus the industry is likely to achieve) for module sizing and hole positions, has been widely received. Olson says this is particularly pertinent when it comes to developers that may diversify their module supply to de-risk a project or portfolio and may need to switch out modules across a project for whatever reason.
By extension, more standardised module sizes and mounting positions would help further alignment in system design and build principles which could, in turn, lend weight to automated or robotic installation. Meydbray notes that previous research and testing of robotic field installs has yielded disappointing results, however some start-ups are continuing to explore its potential. By 2030, aided by standardised module design, robots could cut down the time and labour costs of installing a solar farm drastically.
With modules therefore somewhat restricted in terms of size, solar PV is instead being driven to new heights and efficiencies – and indeed closer to the Shockley-Queisser limit – through innovations at the cell level, while the n-type path is one becoming frequently well-trodden.
The shift to n-type
While n-type cells and modules are, of course, nothing new, they have ceded significant ground to p-type mono PERC that has become the mainstay of solar PV today. But that dominance looks set to be eroded and from 2025 onwards, the industry will have shifted firmly to n-type. As the below graph, provided by PV Tech Power publisher Solar Media’s in-house market research team shows, p-type Mono PERC cells, which accounted for close to 90% of the market in 2021, will see their market share fall from 2022 and by the middle of the decade, will no longer be the leading PV cell technology available.
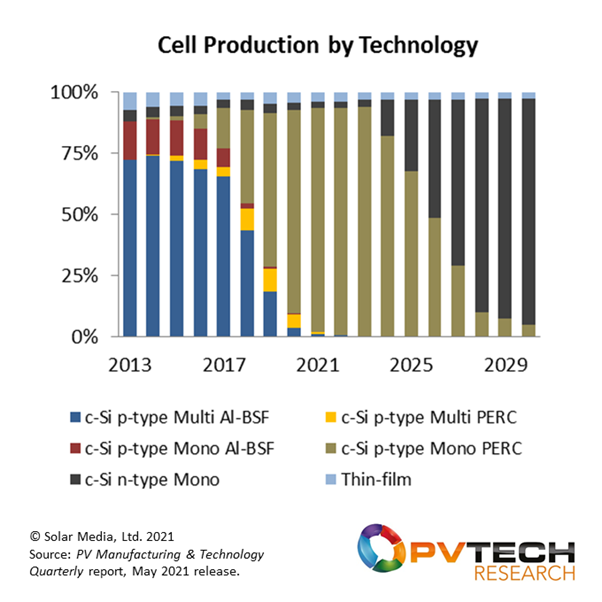
The technology forecast above assumes a near-complete transition from p-type to n-type occurring between 2024 and 2028. Credit: PV Manufacturing and Technology Quarterly Report
Olson says n-type cells are increasingly finding traction in the solar market today. The precise point in time at which they may overtake p-type is, however, difficult to estimate, predominantly because even p-type, as Olson puts it, “isn’t standing still either”. Cell efficiency improvements continue to be realised and as a result, it’s a “continually moving target” for n-type cells to outdo, Olson says.
There could also be a slowing of the technology trajectory caused by the supply chain turbulence that has plagued the industry throughout 2021. Radovan Kopecek, founder of solar research institute ISC Kostanz, notes that when previous polysilicon shortages beset the industry to such a degree back in 2005, global annual solar deployment was at around 2GW. Now, it’s firmly up to 200GW. The deployment bottleneck is in polysilicon production, with the industry currently producing polysilicon sufficient enough to make ~190GW of modules each year. Major cell and module producers currently have an output of around 300GW, Kopecek says, meaning as much as one-third of production is essentially “standing still”. “This is hindering the big [manufacturers] from rolling out [TOPCon] technology because they’re not sure when this feedstock crisis will end,” Kopecek says.
TOPCon, or tunnel oxidised passivated contact, is nevertheless all but certain to be the first, or at least quickest, n-type cell technology to gather scale because of the relatively similar manufacturing processes to existing Mono PERC cells. Most ‘Solar Module Super League’ manufacturers now have TOPCon panels at their disposal and Kopecek is firmly of the belief that TOPCon cells and modules will dominate the industry from the middle of the decade. Olson agrees, citing the relative ease for manufacturers in adapting existing Mono-PERC production lines to produce TOPCon, rather than the wholesale changes necessary for heterojunction.
“TOPCon is only interesting when you have a certain efficiency distance from a PERC cell average efficiency.”
There are yet kinks in the manufacturing process still be ironed out, not least of all in the deposition of the polysilicon layer. Presently, most are using an LPCVD tool to deposit that layer, however further optimisations are necessary if the industry is to reach efficiencies upwards of 23.5%. PCB deposition tools are in development and become mainstays in the manufacturing process shortly, delivering a breakthrough which Kopecek likens to the aluminium peroxide transition which paved the way for PERC to accelerate.
“TOPCon is only interesting when you have a certain efficiency distance from a PERC average efficiency. What we believe is the real average PERC production efficiency is about 23%, and we are offering TOPCon at 23.5%… that’s already possible with LPCVD, but with PCVD it will be possible in the coming six to eight months,” Kopecek says.
There is also a slight hiccup, however, in that TOPCon and other n-type cells require higher-purity silicon than their p-type cousins, placing yet further strain on polysilicon producers to ensure that whatever added capacity does come onstream is capable of producing polysilicon of sufficient purity, which may be easier said than done. Earlier this year Daqo New Energy said between 30 – 40% of its poly output is of sufficient purity for n-type cells – the company is providing n-type polysilicon to four of its major clients – however this could increase to 70 – 80% based on industry demand. It’s perhaps worth noting however that this polysilicon comes at an added premium of around RMB2/kg (US$0.30/kg), and all at a time when polysilicon pricing is squeezed considerably.
Heterojunction cell manufacturing processes have different requirements altogether, including superior raw material quality to that of TOPCon/PERC production and advanced cleanrooms to prevent spoiling. Kopecek adds that heterojunction cell producers also have not yet solved throughput yield challenges, which are still some way off standard PERC production. Heterojunction modules also have a higher consumption of silver, another material to have witnessed pricing instability within the last 18 months.
Driving change
If such challenges persist, and if the Mono PERC envelope is indeed continuing to be pushed, then what’s set to cause the major technology shift that is obviously looming? Simply put, n-type cells and modules promise to deliver inherent benefits in terms of degradation and failure and also cell and module efficiency in production. Furthermore, given their potential average voltage in production, improve temperature coefficients mean modules can boast improved performance in more extreme temperatures.
It is, however, important to decouple the performance in ideal conditions achieved within a testing laboratory using particular materials and that of what can be expected from products from a mass manufacturing line. Table one, provided by ISC Kostanz, documents these differences while illustrating the stated performance improvements over modern and previous leading PV technologies.
Technology | Equipment | Cell efficiency announcements (%) | Average cell efficiency in production (%) | Available module efficiency (%) | Average voltage potential in production (mV) | Average efficiency potential in production (%) |
Al-BSF | Standard | 20.29 | 19.5 – 20 | < 20% | 670 | 20.5 |
PERC | Standard, PERC-based | 24.06 | 22.5 – 23.5 | 20.2 – 21.1 | 690 | 23.5 |
TOPCon | Standard, PERC-based | 25.25 | 23.5 – 24.5 | 21.4 | 725 | 24.5 |
Low-cost IBC | Standard, PERC-based | 25.04 | 23.5 – 24.5 | 21.3 | 735 | 25 |
Low-cost heterojunction | Thin film-based | 25.26 | 23.5 – 24.5 | 21.9 | 735 | 25 |
Complex hetrojunction | Thin film and electronic industry-based | 25.26 | 24.5 – 25 | 21.7 | 740 | 25.5 |
Complex IBC | Thin film and electronic industry-based | 26.1, 26.6 | 25 – 25.5 | 22 – 22.8 | 740 | 26 |
Table 1: High efficiency announcements versus industrial reality of all relevant c-Si technologies on the PV market.
Cell and module efficiencies are just one part of the table, however. Future solar technologies and their deployment will be dictated largely by the cost of manufacturing and levelised cost of electricity (LCOE) produced by projects utilising them, with the technologies offering more bang for their buck set to lead the way. While complex structures such as IBC or heterojunction may win out in the production and operating standards, TOPCon still looks set to hold a competitive advantage – at least in the short-term. Kopecek says PERC-based technologies – TOPCon and low-cost IBC, benefit from lower cost structures and thus deliver better LCOEs.
If that’s the case, then what are the prospects for heterojunction moving forward and, further forward, perovskite-based tandem cells?
From 3G to 6G
Kopecek uses the analogy of the generations associated with telecoms networks, which have shifted from 3G to 4G and now 5G. If aluminium back surface field (Al-BSF) cells are 3G and modern Mono-PERC cells 4G, then the industry is now making its first significant inroads into the 5G era with the widespread manufacturing and adoption of TOPCon cells and modules. The 5G era will continue to see the adoption of new, more efficient cells, bolstered by TOPCon and TOPCon-IBC technologies, while heterojunction cells and modules will perhaps begin to be introduced towards the end of the decade as lower-cost manufacturing is delivered.
Another material shift could happen from 2030 onwards with the likes of tandem cells and perovskites, however these developments are difficult to predict, Kopecek says, with material improvements needed to manufacturing processes and stability. New research compiled by the Optoelectronic Materials and Device Spectroscopy group, which includes researchers from the University of Cambridge’s Cavendish Laboratory and the Okinawa Institute of Science and Technology in Japan, has shed more light on the disorder seen within perovskites that contributes towards rapid degradation of solar cells produced using them, however it’s considered that the industry remains more than a decade away from mass-produced perovskite-based cells and modules.
Referring back to his telecoms analogy, Kopecek notes that the leap from Al-BSF cells (3G) to Mono PERC (4G) took a considerable amount of time despite the fact that, barring a tweak to the deposition process, the crystalline silicon cell basis is fundamentally the same. “Coming from a crystalline technology to a tandem [cell] technology with perovskite on top – which are not stable and have reverse characteristics and the deposition technologies are still not yet developed… This will take more than 10 years,” Kopecek says.
With TOPCon rapidly asserting itself as the leading solar cell technology of the immediate future, all eyes are on manufacturing and deployment scale. With solar riding the cusp of wave, it’s becoming increasingly clear that deployment rests on the upstream sector’s ability to scale quickly.
Inverter tech trends
As PV modules evolve, so too must the associated components of solar system design, both electrical and structural. Trackers and racking designs are continuing to adapt to modules that are both larger and heavier – all while taking into consideration raw material costs – while inverters are also coming under increasing pressure from modules which produce more power. Zhang Yuehuo, product marketing general manager for PV and energy storage at Sungrow, says the core goal of the inverter is to reduce the levelised cost of electricity (LCOE) of a plant, however this is becoming an increasingly difficult task, especially relating to the product’s power density. Zhang says resource is also being channelled into developing more efficient semiconductors, heat dissipation design and algorithm iterations in order to produce inverters fit for the future.