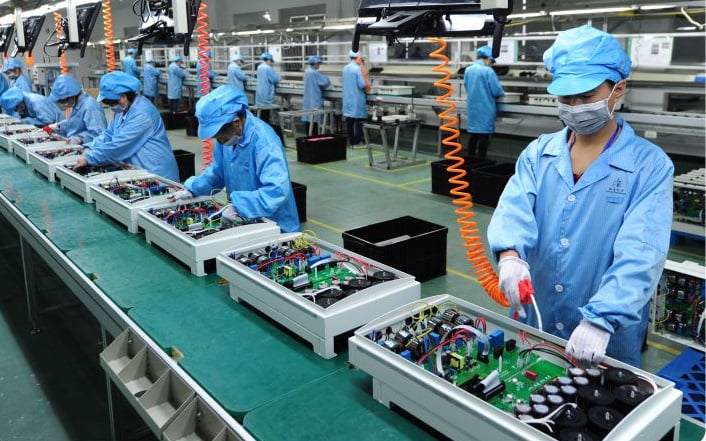
Essentially the brains of a PV plant, inverters’ key function remains the conversion of DC power to AC. However, their design and configuration is continually evolving, and so are the strategies of the companies making this important piece of kit, writes Jonathan Touriño Jacobo.
For many years, the utility-scale solar PV market has been dominated by central and string inverters, with each claimed to have their own benefits for utility-scale solar applications. Lately, modular inverters have also entered the scene, claiming to combine the benefits of both string and central inverters. This feature will explore different uses of each of these technologies, the current technology trends for inverters and how they have adapted to different types of environments ranging from desert areas to floating PV.
Unlock unlimited access for 12 whole months of distinctive global analysis
Photovoltaics International is now included.
- Regular insight and analysis of the industry’s biggest developments
- In-depth interviews with the industry’s leading figures
- Unlimited digital access to the PV Tech Power journal catalogue
- Unlimited digital access to the Photovoltaics International journal catalogue
- Access to more than 1,000 technical papers
- Discounts on Solar Media’s portfolio of events, in-person and virtual
There is also the fact that more and more utility-scale projects are developed with energy storage in mind, either to be co-located at the same time or with the possibility to add it at a later point. This is something that inverter suppliers have been working around as demand increases. Finally, we look at how inverter suppliers are preparing themselves for the introduction of 600/700W+ modules in the solar market.
String and central inverters are still favoured
With modular inverters claimed to combine the strengths of string and central inverters with a modular design, manufacturers have started to embrace that new technology. Modularity allows Spanish manufacturer Power Electronics to improve efficiency and availability, says Maribel Trenzano, the company’s solar & storage product & applications manager. “The efficiency improves because depending on the available power, only the necessary modules will need to operate. The availability increases because the system can keep working even if some modules are failing, and the power of the faulty module could be redistributed with the working modules.”
Ginlong’s inverter brand Solis meanwhile continues to specialise in string inverters which are flexible and suitable for various scenarios, says Lucy Lu, the manufacturer’s global marketing director. “With solar PV projects increasing in size and types, application scenario is more and more complex, it [design] needs to consider inverter devices for higher environmental adaptability and security.” For agricultural or mountain terrain PV projects, higher maximum power point tracking (MPPT) is needed and better algorithms for inverters to increase power generation. Meanwhile for desert areas, Solis takes into consideration both wind and sand resistance with better heat dissipation, adds Lu.
If some suppliers are advancing on modular inverters, for German developer BayWa r.e., this is still not an option it is envisioning to use as they are still too expensive, says Tino Weiss, head of purchasing and product development. If possible, the developer would rather opt for string inverters. “Because we are one of the drivers of string technology. So, whatever we built, if we have the chance to change from central to string, we will go for string,” adds Weiss.
The company sees a big advantage for string inverters in terms of operations and maintenance (O&M), as they always go with 10-year warranties. “We have a longer period of time without the risk of having additional costs on inverter exchange or replacement costs.” For the US, it is a whole different story as central inverters are favoured due to utilities and financing banks not accepting string inverters. “There we still go with central inverters,” says Weiss. BayWa r.e. did use modular inverters for one project due to issues related to power differences, to rectify mismatch losses, but its price is still not attractive enough for widespread adoption, according to Weiss.
Latest inverter technological trends
Although the nascent floating PV market includes various new technologies and project configurations, inverters are still of course a key component. Located on water, there has thus been a need to adapt to the different new environment the inverters are being installed in. Chinese inverter maker Sungrow is one of the market leaders in the floating PV market, supplying to more than 1.7GW of floating systems around the world, according to the company.
Jia Zhang, product marketing director for utility-scale PV plants at Sungrow, says that planned location of projects in complex environments “has put forward higher requirements on both hardware and software design of the inverter.” With their lifespans being possibly shortened amid higher humidity levels, this requires an ingress protection degree of IP65 and a safe high-level anti-corrosion design.
And given that level of the water where a floating PV, or ‘floatovoltaic’ system is located will differ during the day, Sungrow has designed inverters that “adopt a lightweight and modular design for easy lifting,” adds Zhang. Its newer products, the SG350HX and the 1+X model inverter, have been favoured for floating projects.
Soli’s Lucy Lu adds that for floating PV, inverters require more stable and reliable leakage current protection and potential induced degradation (PID) repair function.
Another trend in the inverter market is connected to the increasing energy tariffs across Europe and other regions which ask for higher power generation efficiency of PV systems. “Inverters that have a higher wattage and higher power density have become an irresistible trend,” says Zhang.
From a developer point of view, BayWa r.e. is not in favour of string inverters getting bigger and bigger, power wise, with some inverters reaching 350kW. “From our standardisation approach, the bigger the inverter, the more complicated is our standard approach block design because the blocks get too big,” says Tino Weiss. Inverters of 500kW are not something Weiss envisages procuring. Instead, improvements need to be delivered from other angles instead.
Some of the issues that BayWa r.e. is currently facing are related to pack controlling, given that if two or more PV plants are connected to the same grid connection, you would need to know which one to shut down first and thus would need a complicated regulation, says Weiss. “If inverters could do this instead of a power controller, this would be I think one of the next step developments for inverter suppliers.”
Lowering failure rates and yield reliability of just 0.2% would have a bigger impact than price difference on inverters, adds Weiss. “Yield reliability and failure rate will be the decision factors in the future.”
As for the future of inverters, Zheng says that in three or five years, the use of AI technology in inverters could help developers increase their plants’ energy production more efficiently.
But probably the most important technology trend for inverters nowadays is the growth of co-located projects. Across the industry, optimising for co-located energy storage seems to be an even more important aspect to figure out than the impact the introduction of modular inverters might have.
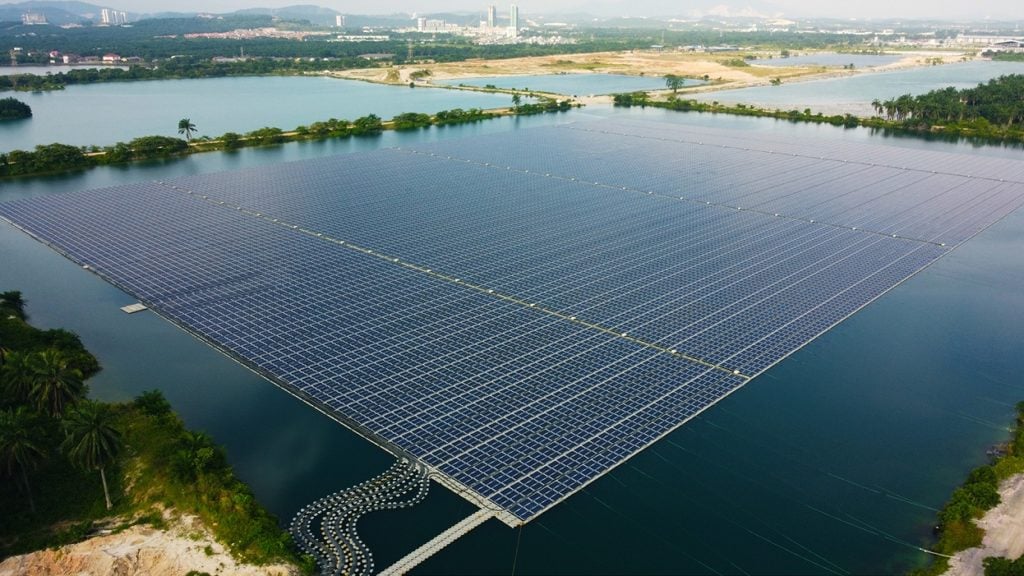
Different ways to adapt to the chip shortage
As more and more technologies rely on the use of semiconductors, or chips, in diverse industries from automotives to video game entertainment and of course solar PV, demand has outpaced supplies. This has been severely affected by the pandemic in 2020 and even in 2021. Inverter manufacturers have not been spared by this ongoing challenge and have replied differently to it. Power Electronics has for example adapted to the changing conditions. “The inverters’ design has had to adapt at the same time as the availability of materials,” says Maribel Trenzano. While Solis has managed the issue by actively exploring new chip suppliers, “we sincerely hope that outstanding chip enterprises can increase the chip capacity of PV inverters to meet the rapid development of the PV industry”, says global marketing director Lucy Lu. And with no end still in sight, inverter manufacturers will still have to cope with the current constraints of the chip shortage affecting many industries.
Inverter suppliers adapting to energy storage
As more and more projects are built with battery energy storage system (BESS) technology, either at the time of first commissioning or with the option to add it as a retrofit at a later time, inverter suppliers have followed the trend. “Energy storage is the biggest trend,” says Lucy Lu, global marketing director at Solis. The company is working on coupling its inverters with energy storage, not only in utility-scale projects, but also in commercial and industrial (C&I) and residential, which takes another dimension if we add chargers for electric vehicles.
Solar PV inverters need to be designed to allow for DC-coupling with batteries to be as easy as it can be, says Power Electronics’ Maribel Trenzano. Power Electronics’ Bus Plus option allows the connection of various DC/DC converters in parallel with the connection of batteries for solar PV and with a direct channel between the inverter and the converter that allows for simultaneous control of the system. The demand for inverters with batteries in utility-scale projects has increased a lot in 2021, says Trenzano. With some of Power Electronics’ Freemaq brand models, the ability to connect up to four independent BESS is working particularly well this year in the US, the UK and Australia. “The future of renewable plants goes through the co-location of energy storage, the demand of hybrid systems is growing, and the regulation is already adapted to it or in the process to [do so] in many countries,” Trenzano says.
The use of energy storage co-located with utility-scale solar PV or as a standalone will keep increasing in the years ahead to integrate variable renewable generation, and thus it is no surprise that for many suppliers it is probably the most important subject nowadays. Sungrow is no exception. “Energy storage is a very popular topic in the last few years,” says Zhang. Sungrow’s R&D department has invested a lot of resources and time into optimising the connection between inverters and energy storage. This is the case with their latest modular inverter that has a built-in energy storage interface.
“For inverter enterprises, the deployment of integrated optical storage and charging products and solutions will be a new business growth point. Solis is also actively laying out this area and expects to launch related products and solutions in 2023,” adds Lu. Some Solis inverters already have in mind the use of energy storage at a later stage, without the need to change existing plant designs, with an “expandable storage interface to accommodate peak saving and provide electricity to support loads and to reduce the overall power supply cost,” says Lu.
BayWa r.e.’s strategy for solar PV plants co-located with battery storage so far has not changed its choice of inverter, although “if you have a DC-coupled system, a central inverter could be a good solution,” says Weiss. The developer is still looking into aspects of co-located projects but is not sure if it wants to “accept the disadvantages we get through the central inverter compared to the string inverter advantages we have right now,” adds Weiss. From a development point of view, what they are already doing is reserving space for battery storage in every project.
Even inverters with small batteries already integrated into them do not seem of interest for BayWa r.e. in terms of utility-scale projects, but they may be suitable for the commercial and industrial (C&I) segment. “If you have rooftops with one or two megawatts, adding hybrid inverters could be doable,” says Weiss.
Increased module power output
As modules are increasing their power output to 600/700W or more, and since inverters are the bridge between the modules and the load, manufacturers have had to increase the power of the conversion components. Manufacturers are actively looking at the increase in power output and optimising their inverters accordingly. In reaction to that change, Solis has optimised the system voltage resistance, component compatibility and system safety, among other features. Solis global marketing director Lucy Lu adds: “At present, affected by the progress of 600W/700W+ modules, inverters with a string current of 15A-20A has become the mainstream.”
In the case of Power Electronics, the power of its third generation of 1500V inverters has increased 15.5% in comparison with the previous generation. “This allows to get the highest performance and reduce LCOE of the solar PV plant,” says solar & storage product & applications manager at Power Electronics, Maribel Trenzano.
Meanwhile Sungrow has increased the MPPT current of its string inverters from 30 to 40 amperes in response to the module power output increase. “Our modular product performance is not affected by the PV module current change,” says Jia Zhang.
Importance of communication between suppliers and developers
One of the “key strengths” of BayWa r.e. is its relationship with inverter manufacturers it works with, to optimise the inverters to best suit each project’s needs. Before settling with Huawei and Sungrow, BayWa r.e. had a strong relationship with Italian inverter provider Power One.
“We were deeply involved in the product roadmap and designing their new inverters and of course, we were driving them to design the string inverters to our system design needs, and they followed us quite intensively until a certain period of time when pricing dropped because a lot of new players, Chinese players, came into the market and developed very big string inverters. So, they were not competitive anymore and they followed that route.”
When Power One and BayWa r.e. went their separate ways in around 2013-2014, BayWa r.e. decided to work with Huawei, despite the company being a newcomer in the inverter industry; with the caveat that instead of keeping a single source for their inverters, the developer also added a second supplier in Sungrow. “A single source in our market dimension is a very big risk,” adds Weiss. Such was the case when Huawei was on the US sanction list during the presidency of Donald Trump, which blocked the supply of its inverters for US solar PV projects.
“We have very strong relationships and with very few suppliers. It’s similar on everything we do. On modules you have five or six because you need them. For transformer or for switchgear supply, we always have only one or two suppliers we mainly work with. That’s one of our strategies, having a close relationship. Being involved in the development and of course, being a big customer to influence development.”