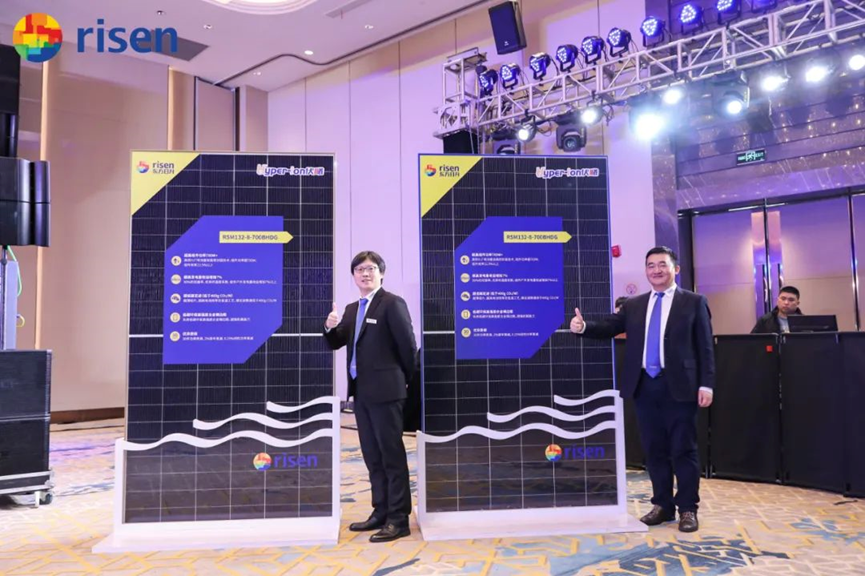
The solar PV industry’s transition to n-type gathered pace over the course of 2021 and 2022 looks very much to be the year that direction of travel is cemented. The year to date has seen numerous product launches and, last month, Risen launched its long-awaited heterojunction range of PV modules, dubbed the Hyper-ion.
Hyper-ion modules use half-cut, 210mm heterojunction cells based on a microcrystalline structure. Cells are 120μm-thick, delivering cell efficiency of 25.2% and module efficiency of 22.52%, with power outputs topping 700W.
Unlock unlimited access for 12 whole months of distinctive global analysis
Photovoltaics International is now included.
- Regular insight and analysis of the industry’s biggest developments
- In-depth interviews with the industry’s leading figures
- Unlimited digital access to the PV Tech Power journal catalogue
- Unlimited digital access to the Photovoltaics International journal catalogue
- Access to more than 1,000 technical papers
- Discounts on Solar Media’s portfolio of events, in-person and virtual
Speaking to PV Tech at the product’s launch last month Dr. Pochuan Yang, general manager at Risen’s HJT business unit, explained the approaches and technologies behind the Hyper-ion range.
“By replacing the a-Si doped film with microcrystalline, the conversion efficiency of HJT can be 0.5% higher than that of an a-Si doped cell,” he said, adding that there was still room for an efficiency gain of between 0.3 – 0.4% through the optimisation of the microcrystalline process.
Those gains will be realised through refinement of techniques typical of when new approaches begin commercialisation. Yang said that Risen had researched upgrading equipment and materials over the last few years, establishing a pilot line that, after two years of batch testing, provided Risen with enough experience internally to develop its approach. Six months on, the results are meeting expectations.
The aim now is to explore other technology and material advancements, such as metallisation, indium-free TCO materials and electroplating to take HJT efficiencies up to 26%.
Time for HJT to match the industry’s hype
For Risen, HJT technology is not the principal issue – it’s about reducing manufacturing costs while delivering high efficiencies in a timely fashion.
“The hype [surrounding HJT] has lasted for several years, yet the actual output is not that prominent. Reducing cost is the underlying problem and our objective revolves around how to bring down those costs effectively for mass production,” Yang said.
Risen is addressing this by benchmarking HJT with PERC production at each stage from raw material to module manufacture, targeting savings wherever possible. At the wafer level, for instance, thinner wafers are being selected over thicker, more expensive n-type alternatives, with n-type polysilicon and wafers already at a price premium compared to PERC.
With 120μm-thick wafers – thinner than those used as standard in PERC and TOPCon production – a-Si passivation technologies can produce voltages of over 750mV while delivering savings in both cost and carbon emissions.
Yang said this is a trait limited to heterojunction. “Only HJT can support producing 100μm cells on 210mm wafers while maintaining high efficiency. HJT supports thickness reduction greater than 10μm or 20μm,” he said, adding that with n-type wafers currently costing around 5% more than p-type ones, the aim is to reverse that trend.
Thinner wafers does, however, pose problems further down the manufacturing process, both in their availability – Yang stressed few manufacturers in the industry make wafers and cells of that thickness – and the production of qualified modules. Yang said Risen’s experience in this field is crucial, while the use of 24-busbar technology – which the manufacturer claims to have pioneered – critical to heterojunction’s forward progress.
“HJT requires low-temperature paste, which includes conductive metals such as silver and some polymer materials. Such materials cannot be pyrolysed at 200℃ [and] remain in the paste, resulting in poorer conductivity compared to high-temperature paste,” Yang explained, highlighting a critical area of development for HJT.
To plug this gap and address that conductivity issues, more busbars have been added at the module design stage. Simulations and testing conducted by Risen found that 24 busbars was the most cost-efficient solution for HJT modules.
But from a cost perspective, especially using PERC as the benchmark, the right paste is still absolutely necessary. Risen uses a paste with a low silver content on the back of the cell, an approach borrowed from PERC production. “People care more about silver paste consumption than allow consumption, and the same logic applies to HJT, where silver consumption per watt will not exceed that of PERC,” Yang said.
Away from the cell, Risen’s Hyper-ion range uses high-strength alloy steel frames which cuts the CO2 emissions linked to manufacture from 570kg of equivalent CO2/kWc to 400kg eqCO2/kWc without sacrificing any loading capacity and further contributing to cost reductions.
Ramping HJT manufacturing
The benefits of n-type products – in terms of increased bifaciality, improved temperature coefficient and lower degradation – have been well documented and warmly accepted by an industry in pursuit of levelised cost of electricity advantages wherever they can be found.
The only obstacle to heterojunction over, say, TOPCon, Yang said, is price. That, until now, had limited the adoption of HJT to high-end markets. With elements of cost now being chipped away, Yang said HJT modules are now capable of serving all markets.
This evolution is placing greater emphasis on module design over price and the availability of significant quantities of product through mass production, which Risen is addressing through upgrades to its HJT pilot line in Jintan. Upgrades and new equipment will take the line’s annual capacity to hundreds of megawatts, while a new facility – slated to be ramped up from Q1 2023 – will take that capacity into the gigawatt range.
By Q3 2023, Risen expects the industry’s total heterojunction manufacturing capacity to exceed 5GW.
“I think this year marks the beginning of a growing market, which is why we’ve launched Hyper-ion at this time. It’s more than a single product, it signifies that HJT integrates efficiency, cost advantage and the possibility of mass production. We’ve found the way and we are capable of doing that,” Yang said.