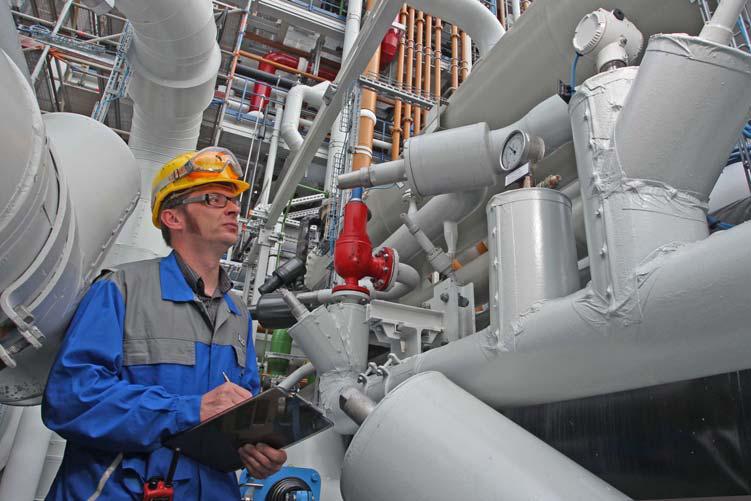
Major polysilicon producer Wacker Chemie has reported preliminary full-year 2019 financial results, highlighting higher than previously guided asset impairment charges on its polysilicon division as ASPs (Average Selling Price) remain at record lows leading to an EBITDA loss of €55 million.
Wacker said that its polysilicon division posted sales of €780 million in 2019, down from €824 million in 2018, a 5% decline, despite unspecified strong polysilicon volume growth. The key factor in the decline of revenue was ASP declines that are remaining at industry record lows, due primarily to major production capacity expansions in China in a well-know bid to become self-sufficient in polysilicon production for the PV and semiconductor industries.
Unlock unlimited access for 12 whole months of distinctive global analysis
Photovoltaics International is now included.
- Regular insight and analysis of the industry’s biggest developments
- In-depth interviews with the industry’s leading figures
- Unlimited digital access to the PV Tech Power journal catalogue
- Unlimited digital access to the Photovoltaics International journal catalogue
- Access to more than 1,000 technical papers
- Discounts on Solar Media’s portfolio of events, in-person and virtual
Wacker’s polysilicon division sunk to a preliminary EBITDA loss of €55 million in 2019, a 24% decline from an EBITDA of €72.4 million in 2018, which in turn had been a 75% decline from 2017.
However, the EBITDA loss would have been much higher without the one-time benefit of an insurance payment in the third quarter of 2019, related to an explosion and fire at its polysilicon plant in Charleston, US, which lifted EBITDA by €112.5 million. This also helped offset polysilicon inventory write downs.
At the group level, Wacker had recently announced an impairment charge on its polysilicon production facility assets to the tune of €750 million, although this was increased to €760 million in the preliminary full-year results.
The company said that the impairment charge included the “company's subdued expectations about future price developments for solar-grade polysilicon.”
Total group depreciation in 2019 was said to amount to around €1.32 billion, resulting in a total negative EBITDA of €630 million, compared to €260 million EBITDA in 2018. Total group revenue was €4.93 billion.
Wacker Group CEO, Rudolf Staudigl said “Our earnings last year were strongly influenced by non-recurring effects from insurance compensation received and from the impairment charge on fixed assets. In operating terms, especially our chemical business continued to perform well. Underlying conditions, however, remained unsatisfactory for solar-grade polysilicon, where prices fell markedly last year amid high overcapacity built up by state-subsidized competitors in China. We are currently working on a comprehensive program to make WACKER more efficient and capable, and to achieve substantial cost savings. We expect already to announce concrete targets for this initiative in Q1 2020.”
Wacker Chemie is expected to publish its annual report for the 2019 fiscal year on March 17, 2020.