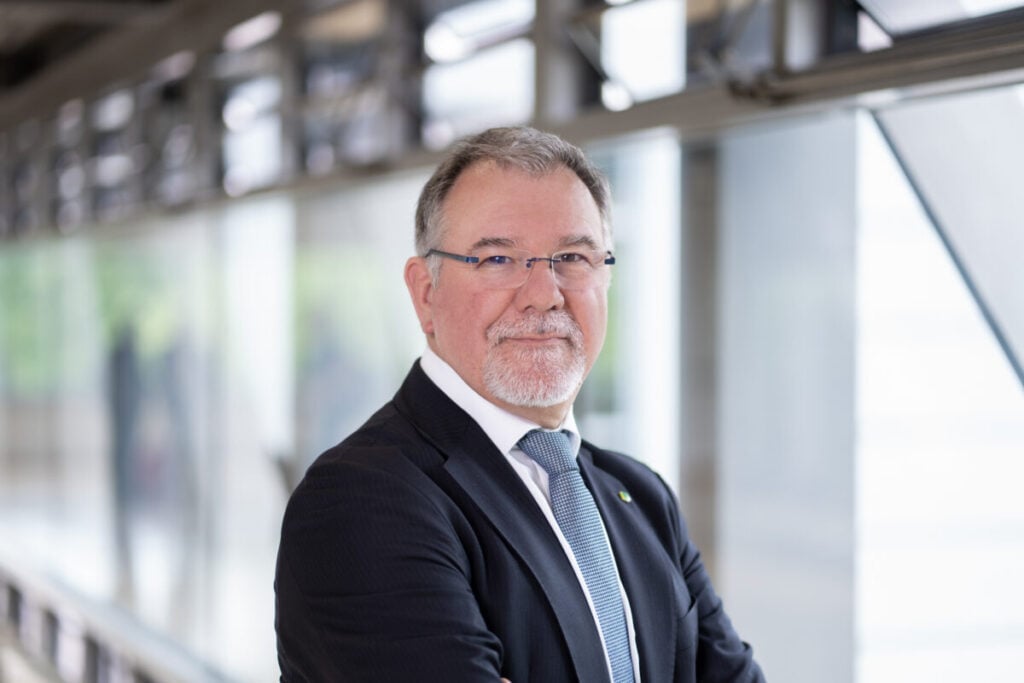
As PV power plant owners seek to maximise the power generation of their assets over time, revamping and repowering are coming to the fore as vital processes for squeezing the maximum potential out of a site. Both involve the replacement of parts and processes at a solar plant to improve its electricity output, but the key difference is that revamping aims to return an ageing plant to its original capacity, while repowering seeks to build on the original asset’s capacity and extend its lifetime.
According to Tomaso Charlemont, European head of revamping and repowering for the German developer BayWa r.e., more efficient components as part of the revamping process could improve a project’s electricity yield by as much as 40% and make a project’s land use more efficient by as much as 50%. As a result, Charlemont foresees a “huge wave” of interest in revamping and repowering on its way as plant owners seek to maximise revenues from their assets.
Try Premium for just $1
- Full premium access for the first month at only $1
- Converts to an annual rate after 30 days unless cancelled
- Cancel anytime during the trial period
Premium Benefits
- Expert industry analysis and interviews
- Digital access to PV Tech Power journal
- Exclusive event discounts
Or get the full Premium subscription right away
Or continue reading this article for free
The nuts and bolts
BayWa r.e. is among the leaders in this sector, having completed revamping and repowering work on close to 500MW of solar capacity across Europe. Speaking to PV Tech Premium Charlemont explains some of the decisions facing plant owners as they contend with assets that are underperforming.
“The replacement of modules is something that we currently do more out of technical necessity than out of pure performance motivation,” he says.
“It’s because there are—or there were—some technologies or materials used in the solar module manufacturing [process] ten years ago which are now revealing as inappropriate, as they can have a negative impact on the performance of solar modules,” Charlemont continues, highlighting how, while the rapid pace of technological innovation in the solar sector is encouraging, this can provide challenges for EPC and O&M companies that are constantly having to keep pace with these developments.
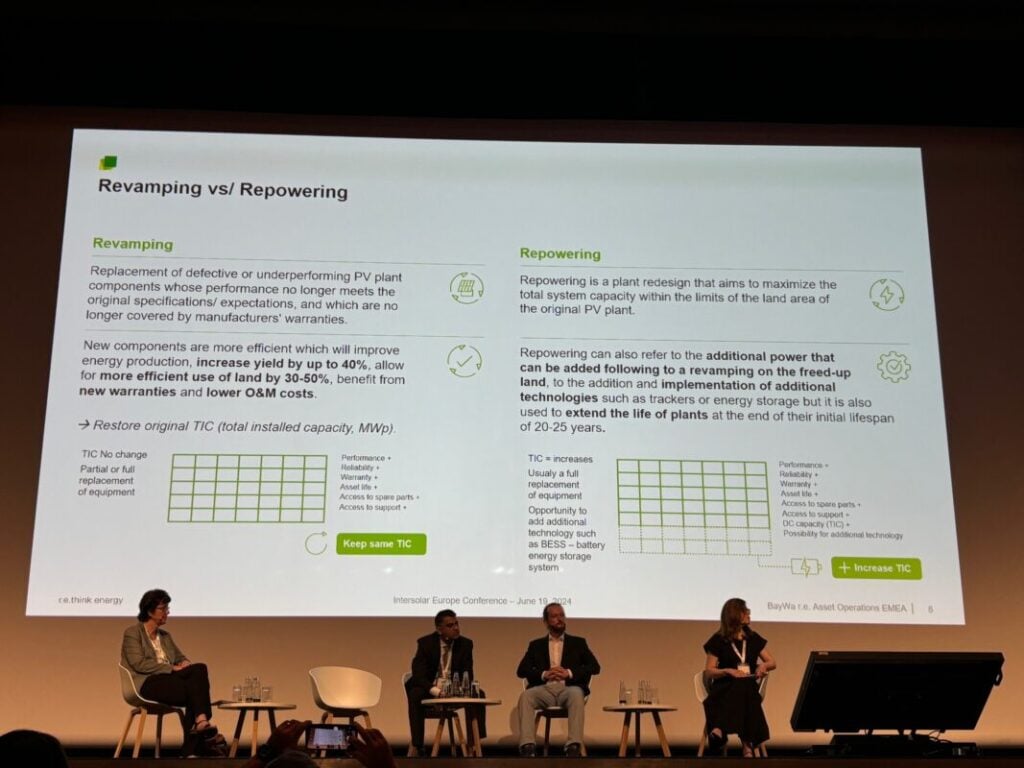
“The biggest issue we have is on the backsheet, which can clearly compromise the module to the point that the replacement of all modules of that make in a given installation is the only option.” says Charlemont. “This is something which no project developer, designer or investor had planned for or scheduled to happen ten years ago when the plant was designed.”
However, Charlemont notes that developers who install components and have every intention of replacing them can be blindsided by the pace of technological change. He uses the example of inverters, which many installers look to replace ten years into a 20-year operating life, to illustrate this.
“The inverter technology has also changed dramatically; inverters installed ten years ago no longer exist. We were installing 500-600kW central inverters and putting them in typically a 1-1.2MW station, with a big step-up transformer. There are only one or two companies left in the world that make those kinds of inverters.
“So what has become the standard today? It’s large 250-300kW string inverters, which you put on the structure underneath the modules and they cost a tenth compared to what central inverters were costing ten years ago.”
A new scale of challenges
Charlemont goes on to discuss how managing these components simultaneously can often provide challenges that a solar EPC is simply not equipped for.
“You realise that your entire intention of modernising the plant actually involves an enormous degree of mechanical and electrical engineering. An O&M organisation, for example, does not [do] engineering or procurement of large volumes of modules, inverters, cables and transformers. An EPC building only greenfield projects, on the other hand, will not have the experience and practice required to work inside an existing, partially operating plant.”
The fact that there is the potential for revamping and repowering works to spiral in this way means that, often, completing such work can take longer than simply building a new plant.
“[Revamping and repowering] takes considerably longer than building a new plant, because the plant is already there and is in operation. It is not something that we can just switch off; take out the defective components, or the modules, inverters and cabling and so forth; and then rebuild everything new, because the plant is in operation,” says Charlemont.
“Asset owners often have a contractual and legal obligation as to their energy production and feeding it into the grid. Thus, typically when we revamp and modernise a plant, we may have to do it in clusters, and switch off single transformer stations first, revamp the connected array, switch it on again and only then move on to the next.”
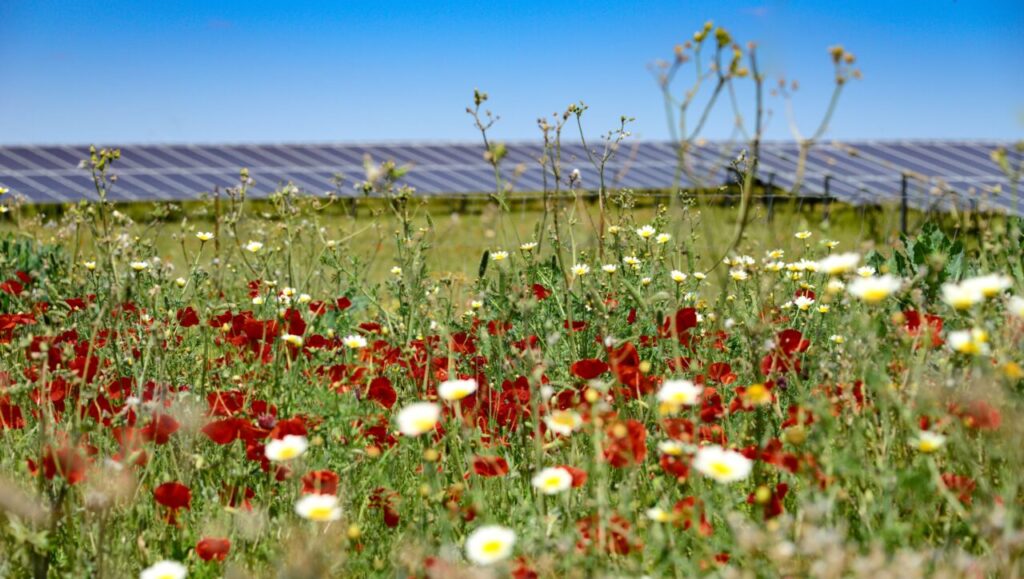
These legal obligations can provide another type of challenge, not just for the asset manager, which is obligated to produce a specified quantity of electricity, but any companies looking to engage in revamping and repowering work, which have to work across a range of jurisdictions with policies that, as Charlemont describes, can vary wildly.
“Every market is different. In Italy, we can modernise a plant to the extent that we can even replace the fixed-tilt structure [and] replace it with single-axis trackers … but you can only deviate from the originally installed capacity within a margin of +/-1%. Therefore, if your plant has a registered capacity of 1MW, for example, you can only install either 990kW or 1MW plus 10kW.”
“[This] is completely different in France, where you have a tolerance of +/-10%. This makes much more sense because it is very complex rebuilding a plant with the exact same power if you replace all the modules. In France nevertheless, you are obliged you to respect the layout of the original structure because it is tied to the original building permit; so if it was fixed-tilt, it has to be fixed-tilt.”
“It is very different from one country to another. In any case, revamping needs to follow certain rules, as when it comes to injecting energy into the grid, there are obligations written down in the feed-in tariff contract. That is why we can’t completely switch off a plant, for example,” says Charlemont.
A mature market
This breadth of challenges in the revamping and repowering space, alongside the rapid rate of change in the sector, means that the practice is one that has changed very quickly, even within the context of the fast-moving solar sector.
“It is a business which keeps evolving, year after year,” says Charlemont. “It is important to understand that revamping and repowering is a complex construction business. It is not a quick fix, where you go in, replace a few components, and you are done.”
He goes on to note that BayWa r.e. has worked on projects across Europe—naming France and Germany as regions in which the company has completed work, alongside Italy, Spain and the UK as countries where BayWa r.e. plans to work in this space—at a rapidly-growing scale. Charlemont says that some of these projects can have a capacity as large as 20MW.
“A few years ago, revamping and repowering typically involved a single plant, mostly, of 1-3MW,” says Charlemont. “Now large asset owners, utilities [and] investor funds come with whole portfolios; they have hundreds of plants bundled into special purpose vehicles (SPVs) [which can include] several different sites. We started handling these bundles of projects over the past two years.”
Part of this change stems from favourable market economics in the revamping and repowering space. While much has been made of the financial struggles of the European solar manufacturing sector in particular in recent months, Charlemont describes the revamping and repowering sector as one that is increasingly “mature”, and one driven by financial opportunities.
“The plant is an SPV, a company with a contract, which regulates the supply of energy to the off-taker, which, ten years ago, typically, were state-owned utilities and all that was happening under the incentive schemes like feed-in tariffs,” explains Charlemont. “They were signing 20-year contracts that were backed by the government, and paying the energy at a very high price at the time, because building a solar plant was very expensive.
“As long as these contracts last, they will often keep selling energy at that attractive price. That well justifies investing in the revamping of assets, especially if they are underperforming.”
Looking ahead to a new discipline
Despite their complexity, the potential financial gains to be made by investing in revamping and repowering could mean the practices sees even more interest in the coming years. Charlemont notes that those involved in revamping and repowering work will ultimately establish their own distinct industry, which he dubs “value-added EPC”.
“We are an EPC, by doing engineering, procurement, contracting [and] construction; but all that with the added value of doing all that in the context of an existing plant on top. It is a new discipline, and that is what brings this complexity to the table,” says Charlemont of this combination of proficiencies that is sufficiently complex enough to deserve its own title.
Indeed, the need for specialised value-added EPC firms is likely to grow in the future, as investors will need to rely on companies with expertise in both conventional O&M work and working with projects currently in operation. At Intersolar Europe 2024, Charlemont suggested that, by 2030, the world’s revamping and repowering market could span close to 30GW of capacity.
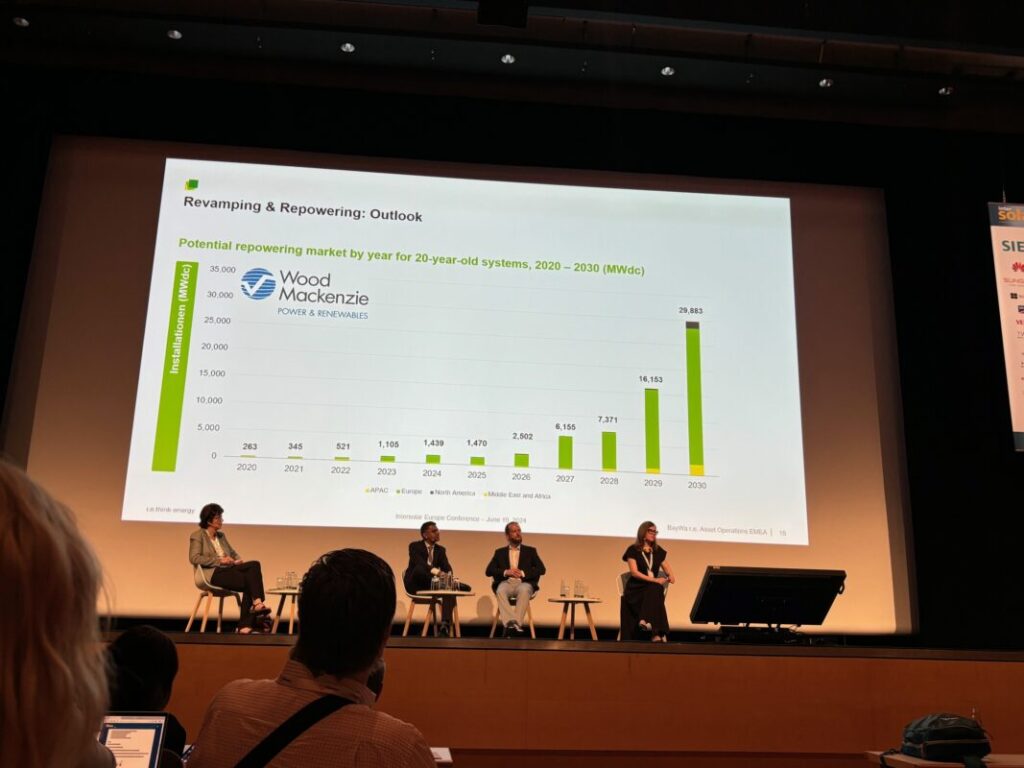
While specific solar module components can become obsolete, the land on which a project is based is a valuable resource that is not vulnerable to the same technological innovation. This is to say nothing of the lack of grid capacity in the global solar sector in general—and the European solar sector in particular, which is expected to have over 200GW of stranded assets by 2030—which will make the land itself, and proximity to grid connections, an attractive part of the solar sector.
“Plants [that are not revamped] will need to be dismantled at the end of their designed life; what remains is a piece of land, for which a building permit has already been established and a grid connection,” explains Charlemont. “This will trigger a new momentum that will be the huge wave of repowering; building a new plant where there has been one previously.”
“For those plants that are not revamped now, and which will reach the ends of their lives, the asset owners have the land and the grid connection,” he continues. “And as building a plant now costs one-tenth of what it was costing ten years ago they will most likely want to repower that land.”
“Even then, you will still need a company that knows how to do [this] because dismantling is not something to improvise either—you’ve got all the infrastructure, the cables in the ground [and] the foundations and all that—but that is where we can build a new plant with more capacity, maybe along with implementing new technologies, such as energy storage, or maybe build an agriPV plant instead of a conventional ground-mounted solar plant thus to bring the land and the solar asset owners’ interests together.”
Ultimately, the growing prevalence of revamping and repowering and the emergence of value-added EPC as a practice are reflections of the solar sector’s desire for constant growth and production. Considering the fast pace of the sector’s technological environment, which means that components become obsolete far before they reach the end of their lives, revamping and repowering look set to become a vital cornerstone of the operations and maintenance field long term.