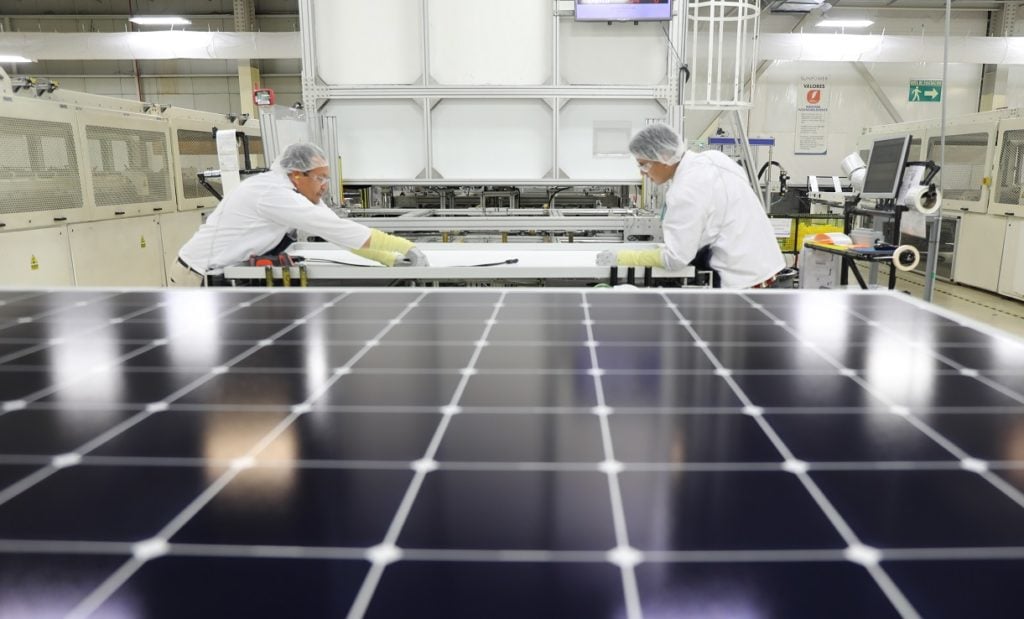
“I think the industry is full of people that do care about what they’re doing and how it impacts the planet,“ Lindsey Wiedmann, chief legal and sustainability officer at Maxeon said to PV Tech Premium. “I think inherent in the industry is wanting to solve the problem of climate change, but not do it in an irresponsible way.”
Industry commentators all predict that solar PV deployments are only going to increase year-on-year; InfoLink predicted last week that 1TW will come online annually by 2030. Simultaneously, the technology inside the panels is eking more and more usable bandwidth from the sunlight they harvest, outstripping the older panels installed a few years ago, and thousands of modules are being decommissioned and removed from service every year. PV Tech Premium sat down with Singapore-headquartered solar manufacturer Maxeon to discuss its practices for ensuring a more recyclable and sustainable future for solar modules.
Unlock unlimited access for 12 whole months of distinctive global analysis
Photovoltaics International is now included.
- Regular insight and analysis of the industry’s biggest developments
- In-depth interviews with the industry’s leading figures
- Unlimited digital access to the PV Tech Power journal catalogue
- Unlimited digital access to the Photovoltaics International journal catalogue
- Access to more than 1,000 technical papers
- Discounts on Solar Media’s portfolio of events, in-person and virtual
A 40-year solar panel
Maxeon claims to design and manufacture its solar panels with the end in mind. It also claims that its modules last longer than the rest; it boasts an estimated 40-year lifespan compared with the industry average 25-30 years. This in particular on its flagship interdigitated back contact (IBC) modules, which it ships with a Declare label that certifies the origin and exact detailing of the contents of the panel. Maxeon told PV Tech Premium that in Q1 2023 it shipped 198MW of IBC modules, representing 25.6% of its total quarterly shipments.
A paper written by researchers at the National Renewable Energy Laboratory (NREL) in the US – “Circular economy priorities for photovoltaics in the energy transition” – in September 2022 suggested that longer module lifespans require less raw material wastage than shorter ones. A modelled 50-year module lifespan scenario forecast that between 2010-2050, a 50%-recycling setup would require 91 million metric tons of virgin material, compared with 124 million for comparable recycling for a 15-year module.
Longer lifespans also yield more energy per module over the time they’re active. The NREL paper also indicates that at the current level, recycling infrastructure isn’t – and won’t be – sufficient to deal with the amount of panels that are deployed at increasingly fast rates; Q1 2023 was a record first quarter in US solar history, with 6.1GW installed in 3 months.
Manufacturing to push the final horizon of the modules’ lifespan as far back as possible makes sense from a statistical standpoint, then. Wiedmann told PV Tech Premium that when it comes to recycling, Maxeon “aren’t doing a lot [yet]…our panels just last a long time, which is good.”
“That will change,” she added, “I’m not sure we’re totally ahead of it, there are a lot of panels already coming to end-of-life, [and] It’s certainly a recent topic; I’ve been in the solar industry for 14 or 15 years and [back then] that was something nobody was even thinking about.”
Durable panels are one thing, but the forward march of technology might render obsolete Maxeon’s efforts to prevent the need for recycling by building for the long-term. TOPCon and n-type panels are increasingly being produced at mass scale, whispers from either side of the Atlantic are bringing the word ‘perovskite’ to people’s attention and new efficiency records are being consistently reached. In 40 years, or even sooner, the efficiency offerings from PV modules might look markedly different and recycling or repurposing will be forced by asset owners looking to repower their sites.
Just last month, PV Tech’s coverage of the SNEC 2023 event in China touched on the increasing efficiencies in cell and module technology. Somewhere like Europe, where land is at a premium and a few per cent more efficiency might make a plant significantly more financially viable, acres’ worth of perfectly functioning, old panels might be retired and need dealing with.
The solar industry needs to avoid replicating across the rest of the world the overwhelming amount of electronic waste that piles up in dump sites in China, the world’s largest importer and creator of e-waste by some distance.
“Panels are a lot less expensive now, they’re a lot more powerful,” Wiedmann said. “Depending on what your PPA or what your electricity rates look like, it can actually be economical just to repower, even if your current system is not broken…you don’t have panels that are not performing, it’s just that ends up being economically viable.”
IBC panels are typically more applicable to rooftops at the moment, where efficiency and power density over a small area are more important factors than module price. Therefore Maxeon isn’t seeing much repowering at this stage, Wiedmann said, but it surely will start to happen over their IBC’s 40-year warranty and amongst the general trend towards greater efficiencies and their lower generation costs over time.
“Fundamentally, recycling is never going to be better than just not having that waste to begin with,” said Wiedmann, adding: “You always just want to reduce the need [for recycling], and that is something that we’re highly focused on. Our panels just last much longer. And they degrade much slower, which is a big part of it; if you have a panel that lasts a really long time but 30 years out it’s not producing nearly as much as it did when it started, the repowering argument becomes a lot more economical.
“What we’re trying to do first is avoid recycling for as long as we can and not make that problem large.”
As time goes on, more and more PV modules are going to be coming to the end of their lives. Whether through age, breakage, end of warranty or replacement via repowering, modules will die and need to be dealt with. A recent article from the BBC brought the issue to widespread attention, touching on many of the same points made in a feature published by this magazine earlier this year.
In that feature, the CEO of US solar recycling specialist company Solarcycle said that they were trying to ‘get in front of any looming waste problem’, and it’s true that the scale of waste is only going to increase with every commissioned project.
The jury is still out on the longer lifespan versus more recycling argument, and an ideal ecological scenario for the industry probably sees both practices deployed to maximise energy yield, limit waste and make recycling processes more economically competitive with landfill.
Transparent supply chains
Maxeon sports its silver Cradle-to-Cradle certification proudly, the highest that has been awarded in the PV industry by the Cradle-to-Cradle Products Innovation Institute. The institute awards certifications to companies that fulfil its transparency and sustainability criteria for their entire supply chain.
Matt Kasdin, director and senior counsel at Maxeon, said: “Built into all of our contracts we have supplier sustainability guidelines where suppliers are supposed to be adopting standards regarding waste [and other ESG factors], just as part of doing business with us.
“When you think about what a supply chain is, what we’re getting is raw materials – sometimes we’re getting components – and so the whole process of getting the Cradle-to-Cradle certification is very cumbersome. Essentially what you need to do is go out to all the different component manufacturers and get them to certify exactly what’s in all of the products, any toxic substances or anything of that nature.
“We had to get letters from 30-something different suppliers, certifying what was there.”
As the name suggests, the Cradle-to-Cradle certification also covers recycling and ostensibly requires that products are ‘intentionally designed for their next use’. If it’s executed thoroughly, this methodology brings the concerns of recycling and end-of-life to the manufacturing process by making it easier to track exactly what’s in the panels so you know what you’re left with 30 years down the line.
A potential circular economy has obvious climate benefits, removing the need for mining new metals or fabricating new energy-intensive components to keep adding solar capacity. It also holds market value for companies in the long term, as they would theoretically gain both lowered supply costs and the gold standard in eco-conscious PR.
Here arrives another concern for PV recycling: the quality. “I don’t think it’s necessarily that binary in terms of ‘is it recycled?’ or ‘isn’t it recycled?’”, Kasdin said. “A lot of companies just take off the aluminium frame because that’s very easy to recycle, but then the rest of it they don’t.
“Technically a Maxeon panel is 99% recyclable…it’s just about how to recycle all the rest of the stuff and how to recover it.”
In theory, a full report of all of the materials and their sources that go into the manufacturing process makes it easier to support high-quality recycling and reduce the scope 3 emissions contained within the supply chain. Collaboration and strategic partnerships have been shown to offer solutions to supply chain issues, and examples and pressure from within the industry – from companies like Maxeon and others – could set the same thing in motion for a circular supply economy.
Kasdin continued: “There are some bits of it that are going to be economically viable and then some that are going to be a lot more challenging. So I think that’s all the hard work we’re trying to do – how quickly can we make this piece more economically viable, or that piece, and so on.”
Whether this is adopted by the industry wholesale – in particular by the largest module manufacturers with gargantuan shipping figures out of China and Southeast Asia – remains to be seen. Whatever the case, it’s a problem that’s only going to grow as time goes on.