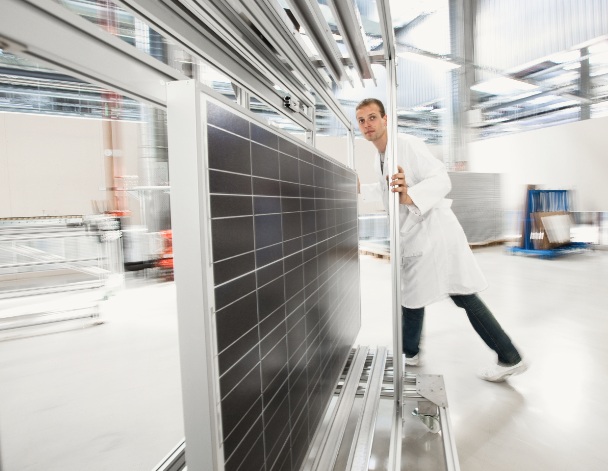
Heading into the PV ModuleTech 2018 event in Penang, Malaysia on 23-24 October 2018, PV-Tech is set to conduct a series of interviews with leading project developers and EPCs, to understand what downstream channels of the utility-scale PV segment are looking for, when choosing PV module suppliers and their respective module technology offerings.
With module supply globally seeing increased contributions now from countries outside China, developers and EPCs across the US, Europe, India, Japan and emerging global markets, are being confronted with greater choice in terms of companies offering modules and technology types that differ from the 72-cell p-type multi products that have dominated utility solar until now.
Unlock unlimited access for 12 whole months of distinctive global analysis
Photovoltaics International is now included.
- Regular insight and analysis of the industry’s biggest developments
- In-depth interviews with the industry’s leading figures
- Unlimited digital access to the PV Tech Power journal catalogue
- Unlimited digital access to the Photovoltaics International journal catalogue
- Access to more than 1,000 technical papers
- Discounts on Solar Media’s portfolio of events, in-person and virtual
To address these critical issues – that impact on plant design, quality of build, and energy yields – the forthcoming PV ModuleTech 2018 event is being organized to provide developers and EPCs with a platform to explain their needs, while hearing from the leading global module suppliers of 2018-2020.
Ahead of the PV ModuleTech 2018 event, PV-Tech is featuring key-company interviews with some of the EPCs and project developers that will be speaking and attending the event, in order to learn what issues are facing downstream utility companies today, and what they need from module suppliers to ensure that utility plants are designed optimally with minimal risk, while delivering maximum return-on-investment to site owners.
Before we hear from the companies making the decisions on module-supplier and module-technologies for global utility projects going into 2019, I will address in this article some of the disconnects seen today with the propositions from module suppliers and the buyers of the modules, while considering what, if any, the impact of new module offerings (bifacial, half-cut, shingles/singulated-cells concepts) will be on utility-scale solar in the next 12-18 months.
Historical copy/paste cookie-cutter site-design tactic nearing its end-of-life
Being a planner (either outsourced or in-house by project developers) of large-scale solar farms in the past few years has been a relatively easy task!
Often, more time has been spent on working out how to rehome great crested newts, than factoring in the impact of the latest module technologies and their impact on the structural layout of modules/inverters, and upside delta on site yields. The only major change in plant layouts has come from the shift from 60 to 72-cell modules, higher operating voltages and higher adoption of string invertors.
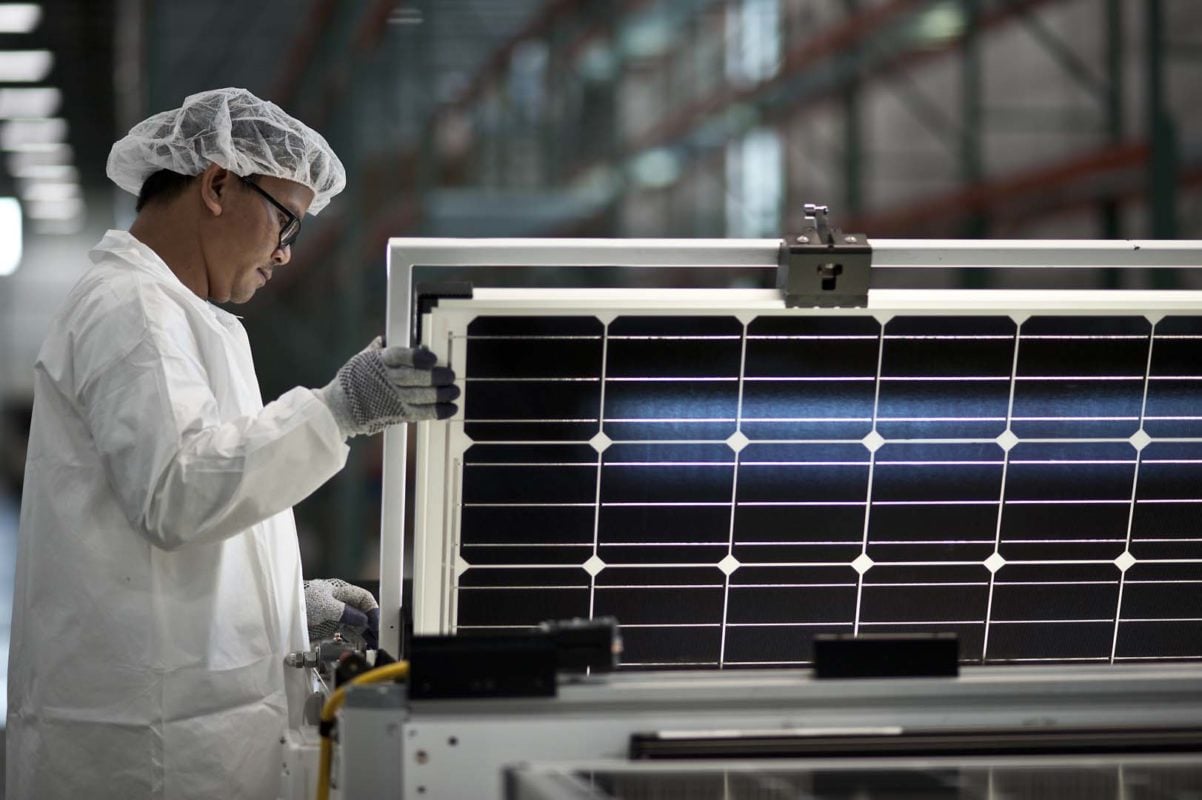
In fact, the dearth of 72-cell p-type multi modules being offered simply meant that panel dimensions on call-out boxes in site layout plans, were accompanied by text that would read ‘indicative module layout/dimensions’, knowing that the final developer/EPC would then have the choice to drop in the 72-cell panel of choice from across multiple module supply channels. To a lesser degree this even extended to one of the thin-film champion developers of recent years, Belectric.
This preponderance of me-too products, from so many channels, may actually be one of the key factors behind the number of solar parks underperforming today.
So many developers and EPCs seemed to be of the opinion that because this module type was in such widespread supply, it implied that the technology was both mature and dependable. In this way, it was much easier to justify driving down site capex, while creating somewhat of an auction across module suppliers when sites approach the build phase.
At the extreme end of this, we have the Indian market which today epitomizes the above narrative. Ultimately, component supply and site capex is of course a trade-off between upfront costs and how much sites can be sold for when it comes to flipping to the institutional investment sector.
Performance over 20-30 years, site yields and ensuing costs to fulfil IRR’s sadly have no compromise in this regard; time-and-again, the conversations with asset owners and O&M’s in the past few years have sounded like a broken record when reflecting on module choice enacted prior to their acquisition phase.
Where is the system letting down asset owners, and can it be fixed easily? This would perhaps be the most mature place to start; to identify the gaps in the system that allow multi-MW sites to be populated with modules that can barely perform over 2-3 years, far less 20-30 years.
Plenty want to bury the fact that so many solar plants are underperforming today, as though this would be an indication that the industry was short-changing its funders (government, state or city-based). However, to a man, virtually all of these stakeholders would like nothing more than knowing how their future investments can outperform prior rounds of financing, and that the solar industry as a whole recognizes that module inspection, certification and testing is not just a bean-counting exercise, but a channel through which everyone can get their act together professionally.
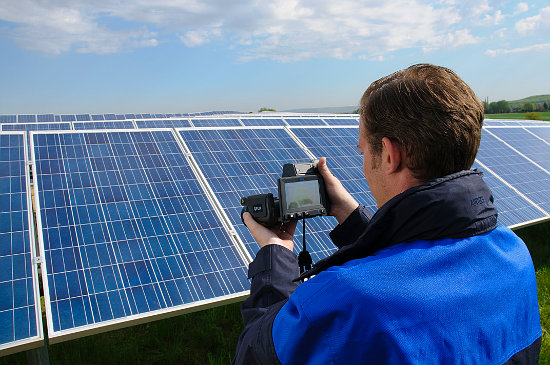
OK, so now we have untried and untested modules coming on the market!
One can sympathise with asset owners today, when they are now starting to see module suppliers offer the next-best-thing after 72-cell utility-based p-type multi modules, to EPCs and developers that are lining up future portfolios of built solar farms.
The manufacturing sector seems to have hit the technology-upgrade button, almost overnight.
It is no longer simply p-type multi modules flooding the market; there is now mono-PERC, and thrown into the mix bifacial modules, half-cut cells and shingled products. (Note – the shingles term is actually a misnomer, as the correct assignation should be singulated cell strips, but for now this is not a big deal.)
For sure, many developers and EPCs are confused. Which of the new product types – and companies supplying them – are actually offering a higher spec product that has inherently lower degradation and lower risk than products of yesterday? And which – despite what it says on the tin – just need to be sidelined until there is field data to show real-world performance?
Knowing the answers to these questions is probably what will differentiate the solar farm builders globally over the next 12-18 months, and right now, everything leading into the PV ModuleTech 2018 event is being configured to have an independent platform to allow rational decisions to be made by EPCs and developers. And not to mention informing the asset owners of today’s multi-GW portfolios that can ultimately influence the lenders about component choice they need to pass down to the EPCs on-site.
Within the overall mix of higher performing products (let’s classify by stated panel powers at STC here), there are some excellent choices to be made. For example, the move from multi to mono is intrinsically advantageous from a degradation standpoint; and the use of glass-glass modules (mono or bifacial) has many benefits also. And on the thin-film side, moving from a First Solar Series 4 to Series 6 panel size opens up plant capex benefits that are highly-positive from a return-on-investment standpoint.
In short, the world is moving inevitably away from me-too 72-cell p-type multi modules to a mix of higher-performing and potentially more-reliable offerings. It is now down to the module suppliers to explain clearly what they are offering, to the third-party testing/auditing/certification labs to undertake the appropriate analysis of the companies/products, and of course to the EPCs/developers/owners to be adequately tooled to make qualified judgements.
Exception-not-the-norm summary statement needs to be turned upside-down
Despite the FiT driven residential early-adoption of solar, and the sustainability-motivated holistic approach from the corporates operating with acres of empty flat rooftops, the 100-GW-climate of the PV industry today is a utility-driven institutional-motived asset class that fulfils global energy needs in a post-fossil-fuel world.
As such, the importance of plant return-on-investment becomes the single most important metric judging the success of the solar industry as a whole. Therefore putting built utility-scale plants under the microscope is fully justified and essential to move performance levels forward.
There are hundreds of well-build, reliable and target-fulfilling solar plants in operation today, with asset managers and O&Ms monitoring, optimizing and maintaining energy yields. However, they are still outnumbered by the plants that see teething problems almost from the off. Flipping this ratio around is now the next big challenge of the industry, so that underperforming sites become the exceptions.
Over the next couple of months on PV-Tech, we will hear the views of EPCs, developers and asset owners/managers, pulling together a wish-list to the module supply community about the need for transparency in terms of product certification and reliability testing, down to factory operations and bill-of-materials. This wish-list will then become the basis of the talks and presentations delivered by relevant stakeholders at the PV ModuleTech conference in Penang, on 23-24 October, 2018.
Anyone wishing to contribute to the series of articles on PV-Tech can email me direct here. To sign up to attend and participate in the PV ModuleTech 2018 event, please visit our webpage here.