
Mono c-Si cell production is forecast to account for 49% of all c-Si cell production in 2018, and will become the dominant technology used in the PV industry by 2019, according to new research contained in the latest release of the PV Manufacturing & Technology Quarterly report, from the in-house research unit at PV-Tech’s parent company Solar Media Ltd.
Having been held back at the 25% level for the past few years, mono cell production is set for massive market-share gains in the next 18 months, with 2017 being the year of preparation and 2018 when the industry is truly shaken up by a collective momentum that can be traced back to the huge success of one company in particular, LONGi Group.
Try Premium for just $1
- Full premium access for the first month at only $1
- Converts to an annual rate after 30 days unless cancelled
- Cancel anytime during the trial period
Premium Benefits
- Expert industry analysis and interviews
- Digital access to PV Tech Power journal
- Exclusive event discounts
Or get the full Premium subscription right away
Or continue reading this article for free
This article reviews the background for this breaking-news, explains the various parameters that have come to fruition in the past few years, and outlines the final pieces of the jigsaw that we expect to be fulfilled in the next 12 months that will set forth a domino effect in terms of company and technology specific competitiveness going into 2020.
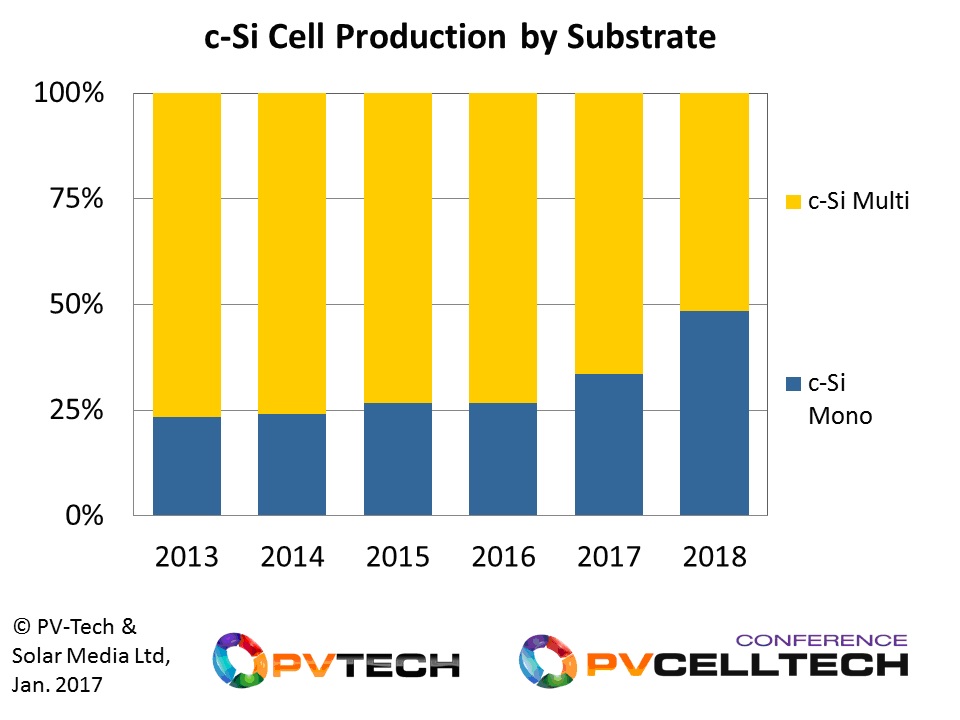
Why had multi been so dominant, for so long?
Any learned historian of the solar industry will know that solar began as a mono world, with the solar industry living off the scraps from the early dominant driver for polysilicon production – the semiconductor industry.
Casting blocks through directional solidification provided the breakthrough that enabled a cost-effective and purity-sufficient supply of wafers for solar cell production, and this technology became rampant across China as soon as the solar industry moved from academia to commercial status.
Multi-gigawatts of casting furnaces were installed globally as the solar industry moved from a few GWs of annual demand to one where the main driver for polysilicon plants was now the solar industry, not semiconductors. No country epitomized this revolution more than China: and no company more so than GCL-Poly.
Economy of scale was created for the first time, for ingot/wafer supply to the industry, and catered perfectly for a thriving multi c-Si cell infrastructure that was benefiting from the demand for 60-cell p-type modules in the 230-240W range.
Mono pulling had become a niche art, with a defined supply chain for 5-inch wafers or n-type cell customers that were bespoke on their wafer specification requirements. Even as mono wafers shifted to 6-inch, mono pulling capacity was counted in the hundreds-of-megawatts capacity range, while GCL-Poly and many others by this stage were counting multi wafer production in the multi-GW range.
Then LONGi came onto the scene and the industry got its first major process flow upgrade route for many years, PERC. And at the same time, pricing collapsed to 40 cents per Watt by the end of 2016.
Mono supply-constraint makes ingot pulling key to technology split
While the signs of mono becoming more commonplace have been there to see for the past couple of years, counting the numbers from a market-share perspective have not borne this out until now. This is something that has confused many, so let’s try to explain what has been going on.
First, you need to remember that the industry has expanded from the 50-GW mark to the high 70’s in just 2 years. So any technology, or company, holding market-share levels at static values, was still in mega-growth phase. In fact, were it not for LONGi and other mono drivers in the market over the past couple of years, we would have been looking at a market even more dominated by multi c-Si cell production.
Indeed, this also provides the first indicator of supply tightness for mono supply, in general, albeit on a far smaller scale that we are set to see for the next couple of years.
Even today, through 2017, the share of mono will be effectively driven by the supply levels of mono wafers coming from LONGi, and one other company, Zhonghuan Semiconductor.
In the past couple of years, we have commented many times on PV-Tech that, despite the capex investments, wafer quality and low-cost structure of LONGi, the industry needed about 2-3 players like this, before any meaningful technology shift was to happen; or at least to hasten the inevitable move from multi to mono.
This has actually been the key issue we have been tracking in our market research at PV-Tech, not the frequent announcements from cell makers hypothesising about becoming multi-GW heterojunction cell producers overnight.
Predicting technology trends from the cell maker’s lofty production plans is currently a red herring, and this extends to n-type adoption. (We will be discussing the n-type landscape shortly on PV-Tech, so will not expand more on this for now.)
Consider this, to understand the above statement: let’s say just a handful of the cell makers did install multi-GW of new p-mono PERC, n-PERT, or heterojunction cell capacity: they all have one big problem, wafer supply. That is assuming mass production processing is achieved at market-required costs, which will likely be the Achilles heel for most.
LONGi and Zhonghuan are not the only two GW mono wafer makers with expansion plans coming online this year, and beyond. It’s just that they are by far the dominant ones, and each has a GCL-like capacity-growth hunger. Analogies between the companies are even more pertinent, when looking behind the data on capacity and production however.
When GCL-Poly came to dominate multi wafer supply, it was through having the necessary relationships in China for polysilicon supply, coupled with sales channels through formal and informal arrangements with the industry’s leading cell producers in China and beyond.
Scanning the JDAs, supply arrangement, JV’s in China (and beyond) over the past 18 months, a large amount of these have involved both LONGi and Zhonghuan, as these two companies set out the stage that will unfold in the inevitable dominance of mono by 2019.
What will happen to multi?
The section title defines the dilemma for many in the industry now: what to do with the gigawatt glut of casting furnaces, and by default, what next for GCL-Poly?
Predicting this over the next couple of years is far from simple, as there are many options.
The naïve argument being advocated by many in the industry goes along these lines. Multi wafer suppliers will implement diamond wire saws, see an instant 10% productivity throughput improvement, translate this into lower cost wafer pricing: while at the same time, cell makers will change texturing (or wafer suppliers will oblige through pre-texturing), with the resultant cells lower cost and higher efficiency.
There are so many issues here that just don’t seem to stack up however.
The whole story just seems somewhat rushed, knee-jerk and an option that is the only game in town, however challenged. Doing nothing is not an option, and where else can multi go – it has to do something after years of marginal improvements at the casting/cell stages (aside from Hanwha Q-CELLS and REC Solar).
The change also requires a unified approach in texturing and across a huge number of wafer and cell producers. The solar industry has a pretty sketchy track record of doing anything unified, and with debate still ongoing regarding texturing (pre-texture, wet, dry), we would seem to be light years away from this drop-in change falling into place with a competitive cost structure.
But more challenges can be found at the cell side. Cell technology (for p-type) is somewhat mono/multi flexible, and surely the easy thing for the early mono cell movers is simply to flip production lines from multi to mono, add PERC and seek to secure mono wafer supply? Indeed, the past 6 months has seen this clearly from the likes of Neo Solar Power, JinkoSolar, and SolarWorld to name just a few.
And even if, 12 months down the line, we have a viable supply chain for diamond wire cut multi wafers, have we not simply just delayed the inevitable for multi, at quite some cost and effort?
The other ambitious rescue plan for multi casting can be found once again in the industry from the recent wave of announcements relating to grand plans to adopt variants of a hitherto unsuccessful technology change: cast-based mono, or described before as quasi-mono or other terms that suggested mono-like quality of casted material.
Like the black silicon hopes, it would seem again that the hand is being somewhat forced by mono pulling, and with the industry moving to higher cell efficiencies, can it really be expected that anything but high purity mono wafers (from pulling) will dominate the industry shortly?
Of course, if GCL-Poly could press a button and convert 15GW of multi furnaces, and create mono-like wafer quality that could be used by PERC and n-type proponents, we could have a major game changer. But only as far as wafer supply is concerned; if successful, then it would only further hasten the demise of multi cell production.
Our forecasts however are based on multi wafer supply being under extreme oversupply pressure during 2018, with chronic inventory build, low-price pressure selling, and basically on a downward spiral from which only a radically new wafering technology (e.g. direct/kerfless) could possibly reverse.
Interestingly, multi cell makers will likely see a short-term boom from effectively naming their price on wafer supply, so keeping many hoping that multi has a longer future than reality suggests.
Factors that change everything!
Predicting next quarter is hard enough in solar, as everyone has seen in the past few years (or more), and there is no shortage at all of factors that may throw multi a lifeline that extends its life way longer than we are forecasting.
For starters, the mono expansions of LONGi and Zhonghuan need to come to fruition, and while we see low risk to this, the prospects of unforeseen delays or external market effects, cannot and should not be discounted.
Similarly, there is the perennial moving-target in end-market demand. Not news to anyone that has been tracking the industry for the past 5-10 years, and having seen final annual deployment coming in way above the general consensus at the start of each year. And just last year, this was no exception, with almost all market research firms being 10-15GW on the low side: this is a large miss by any standards.
Let’s consider the two options to forecasting end-market demand now.
If the industry contracts, or even remains static, it will only increase the rate of mono market-share gains over multi, as mono is tight in supply and has the scope to be competitive with multi now. In this scenario, multi is wiped out faster than expected.
Conversely, if the market over-performs, and ends up over 85GW (don’t discount for one second), then multi has a lifeline due to the supply constraints of mono. And potentially more time to get its act together for low cost wafering and cell efficiency improvements.
Also, if we do see a major development on direct or kerless wafering that fundamentally changes the cost envelope for multi wafer supply, then we have a game changer for sure.
Finally, there is the wildcard issue of the new n-type wannabees, which anyone that did the rounds at SNEC a few weeks ago cannot have failed to have clocked. If these companies can find the instant recipe for low-cost n-type cell production, and have low-cost high-yield GW-level cell production of cells anywhere close to Panasonic or SunPower, then the demand on mono wafers will only become more powerful and will surely unlock even more new capital to shore up the ingot pulling supply capacity in China.
Final comments
So, across the board, there are plenty of what-if’s in the mix, and you can judge for yourself which are more or less likely.
In this context, our forecasts, derived bottom up from actual ingot production, wafer supply, cell production, module supply, and end-market demand, are complete from a value-chain perspective. The only unknown is what will ultimately unfold, but all the signs are clear on mono finally coming of age in a mature industry pushing towards the 100-GW annual deployment level.
And if this comes true, it would be fair to conclude today: mono is the future.
The latest release of the PV Manufacturing & Technology Quarterly report is released today by our research team. More information on accessing the analysis, findings, and company-specific technology forecasts can be found by clicking on this hyperlink now.