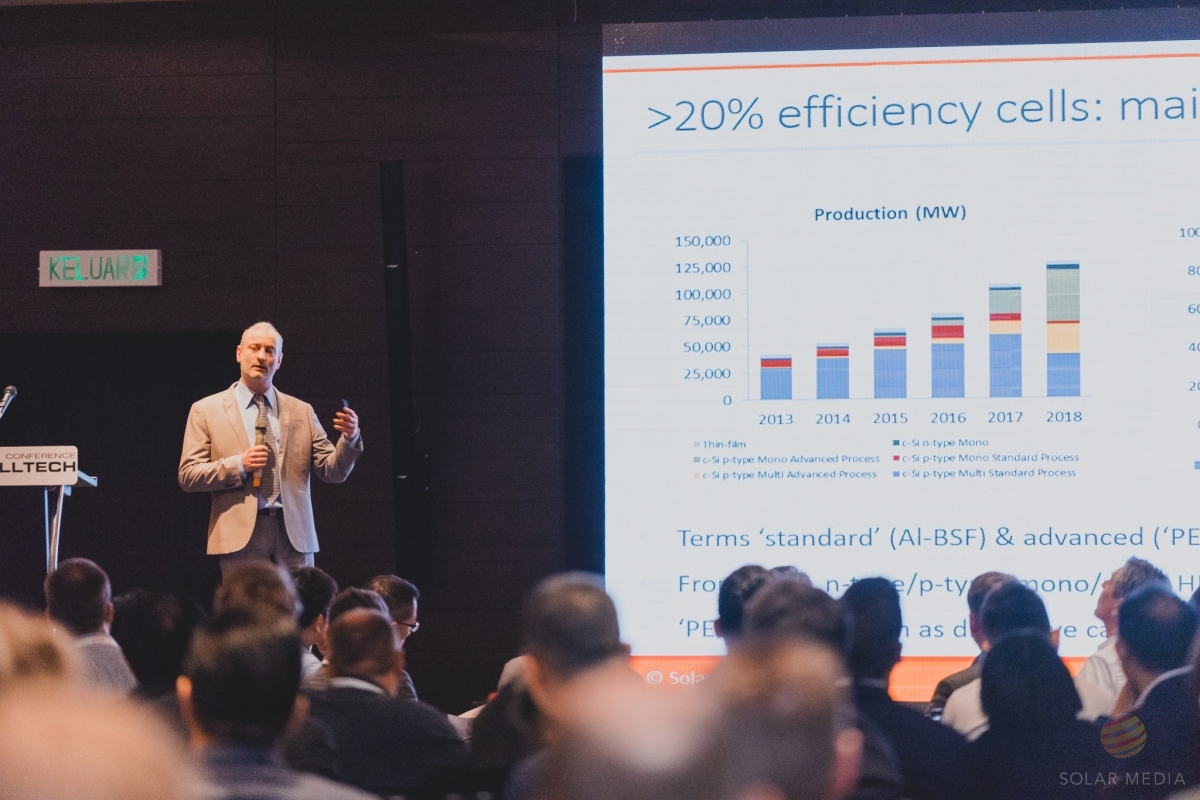
PV CellTech 2018 saw Chief Technology Officers and senior executives from the world's top solar cell manufacturers and equipment suppliers give key indications of which cell technologies will be driving the industry in the coming years.
This blog includes some of the hunches and opinions gathered from delegates over the two days in Penang, Malaysia. The newest and highest efficiency cell technologies are on the rise, but we also heard of stalwart multi-crystalline silicon technologies managing to scrape back the efficiency gaps with their own innovations. Timing will be critical in terms of which technologies will take off over the next two years.
Unlock unlimited access for 12 whole months of distinctive global analysis
Photovoltaics International is now included.
- Regular insight and analysis of the industry’s biggest developments
- In-depth interviews with the industry’s leading figures
- Unlimited digital access to the PV Tech Power journal catalogue
- Unlimited digital access to the Photovoltaics International journal catalogue
- Access to more than 1,000 technical papers
- Discounts on Solar Media’s portfolio of events, in-person and virtual
Most delegates were cautious in their responses and when it came to certain technology comparisons they felt that it was just too soon to predict, even in an industry that has started moving at pace.
Kicking off the conference, Finlay Colville, head of market research, PV Tech and Solar Media, said that the US import tariffs resulting from Section 201 were far from the main global issue today – adding: “Everything is about signs over the next few years of there being a slow down in investment going into manufacturing in China; that is literally the single biggest, most important thing for the whole solar industry.
“Also the ability of the downstream channels to actually install all these modules.”
Despite the formidable rise of monocrystalline cell technology, changes and developments in multi-crystalline technology have allowed it to continue prevailing in the last two years, while also keeping manufacturing capacity at the necessary levels to reach the major industry milestone of 100GW in a year, said Colville.
The Mono vs Multi debate
A question the whole industry still wants to know is which of mono or multi will dominate over the next 3-5 years.
It’s not going to be as clear cut,” said Gordon Deans, founder and COO, Aurora Solar Technologies. “There’s advantages to both technologies and what you can see from people talking this year at CellTech and also last year is that sometimes you'll get somebody saying multi is the clear winner for them and other people will say mono is the clear winner for them.
“It depends what you are trying to achieve and what your cost factors are in your sourcing of materials and your supply chain and your production as well. There’s not one single answer, it’s how does your particular situation drive what your decisions are – that’s what matters.”
This balanced view was echoed by Guangyao Jin, chief scientist, DuPont Photovoltaic & Advanced Materials, who said: “We believe both multi and mono have their own advantages. The cost of mono wafer has trended down while multi has tried very hard to increase efficiency and power output. They will coexist for quite a long period of time.”
Closing gaps
Such a question can’t be asked without hearing from the heavyweights in mono technology LONGi Green Energy Technology. Xie Tian, the firm’s director of Wafer Quality Management said that there was a very big wafer price gap between multi and mono last year, mostly due to the mono wafer shortage, but the price gap between multi and mono is consistently becoming smaller and smaller.
Pierre Verlinden, who until recently was the long-standing chief scientist of Silicon Module Super League (SMSL) member, Trina Solar, said that, historically, multi has clearly dominated. However, despite it being able to regain some interest back from the mono surge due to the conversion of the technology from Al-BSF to PERC, there is still a greater interest in mono because “the best benefits” come from mono. Nonetheless, the industry has often demonstrated new efficiencies with mono technology only for the developments to be transferred back to multi to reduce cost and Verlinden believes this trend will continue.
He said: “Today we make high performance multi wafers that are almost as good as Cz wafers. […] If you focus on impurities you can improve the lifetime of your multi-crystalline wafers and then get roughly about the same performance as you get in mono-crystalline Cz technology.”
Finlay Colville introduced GCL-Poly, which has been one of the biggest drivers of multi on the wafer side in the last 3-4 years, along with Canadian Solar, one of the biggest proponents of multi cell manufacturing – a unique company that has its arm in every part of the value chain from cell manufacturing all the way to project development and EPC activities. Colville said together, both firms had been key to keeping multi competitive and retaining its market share.
Guoqiang Xing, SVP and CTO, Canadian Solar, said the cost of multi-PERC technology is reducing along with the inception of high performance multi technologies. More importantly he said his firm had taken multi-PERC into mass production at the Gigawatt level last year – adding: “we have a long way to go but I think multi will stay competitive for a long time to come.”
Meanwhile, Yuepeng Wan, CTO, GCL-Poly said that for multi to keep its market dominance it was “very critical” that it is able to offer higher output modules so that the end consumer has a choice of level of output.
Breaking even
However, PV Tech heard one executive suggest that the multi-crystalline business case has not shortage of challenges to remain competitive. Efficiency gains are increasing much faster for mono than multi, combined with decreasing manufacturing step costs for mono wafers, and there are some markets where mono-PERC modules are now slightly cheaper than Al-BSF modules. Although, this is not the case in markets with high costs of capital, such as Turkey and India, the executive said.
Indeed, Basma Amezian, business developer, Singapore Solar Exchange, looking at manufacturing break-even price/cost boundaries, said: “Taking as a reference absolute best-in-class processing costs in the industry, which would be relevant for the multi-gigawatt China-based factories, we can see that multi cell makers struggle to make profits. On the other hand, for mono we consider that there is a more or less good margin between the processing costs and the break-even boundaries.
“Of course it will depend on each company, processing costs and strategies and a lot of different variables, but if the assumptions are correct we can see here that the multi cell makers made loses in the first quarter and the fourth quarter of 2017, they barely broke even in Q3 and they only made a one-digit profit in Q2.
“For mono cell makers, however, we consider their margins were between 8 and 15% and even on their lowest price level in Q1 2018, their margin was the lowest of the year but also the maximum that the multi cell makers made.”
The p-type vs n-type debate
N-type technology is on most people’s radar today and the industry is watching closely for any hints at whether it will come to trump p-type technology or co-exist happily over the next decade should the industry reach Terawatt production levels.
It’s worth nothing that another of the major questions at CellTech was ‘What happens after PERC? – Particularly as we heard several times that PERC is set to become dominant in the market as early is this year. This question is certainly partly tied up in the n versus p-type debate going forward.
Super Top Runner
China’s 'Super Top Runner' programme which targets the highest efficiency technologies is seen as a key enabler for technologies using n-type and heterojunction, but Finlay Colvile said the 1.5GW put aside for this – in a market that can do 65GW – is still very small, allowing more traditional cell technologies to continue to prosper.
Canadian Solar’s Guoqiang Xing said that for the Super Top Runner programme, players only have to score on the technology rather than the levelised cost of Electricity (LCOE), which is driving the production in newer technologies.
As a side note, Xing said that he had expected diamond wire sawing (DWS) to have a 70% market share in 2019, but instead it is likely to reach 100% already this year. “It’s like a tornado,” he said.
One wonders if any specific cell architectures could also become tornados in their own right.
DuPont’s Jin said that due to the super Top Runner programs driven by China, his firm expects significant growth of n-type passivated contact technology in the coming few years. However, he said the question of whether it will become mainstream to replace p-type position in the market today, will be “highly subject to the total cost of ownership improvement throughout the whole value chain engagement”.
Omid Shojaei, CEO, INDEOTec said he could not see much limitation in terms of people switching between p-type and n-type, assuming there is enough supply of mono wafers.
HJT
Shojaei added: “If we talk about heterojunction – of course we can do it with both p-mono and n-mono. The results are better with the n-mono so there is probably something like 1% absolute efficiency that are better with the n-types so I would say that if heterojunction picks up, this will also increase the share of n-type versus p-type mono but its not an easy question.”
He said there are a lot of new players in heterojunction, with more than 30 labs just working on its next generation, adding that he sees the HJT market rising from 2GW to 22GW in the next three years.
He said Japan remains the best market for the moment led by Kaneka and Panasonic, but there are no specific plans to expand. So to reach that 22GW, there will be roughly 2GW in Korea, 5GW in the rest of the world and the rest made up by China, which is clearly the biggest investor today in the HJT market.
Shojaei had said that PERC can get to around 21-22% maximum on the industrial level, but this was an area of contention at the conference.
Holger Neuhaus, director innovation and Technology, SolarWorld Industries, later claimed that PERC would reach >24% in industrial production. While Martin Green, of the University of New South Wales said PERC should see 23.6% in production in the next 2-3 years.
Is n-type really ‘better’?
Pierre Verlinden said that n-type is a “wonderful material” because it’s less sensitive to iron impurities than p-type. However, he noted that if such metallic impurities were removed from the equation in wafers – if the iron concentration is reduced – then theoretically p-type efficiency would be better than n-type.
He added: “So there is no reason technically why we should go switching to n-type if we stay with the standard PERC technology.”
P-type multi still dominates manufacturing, he claimed, but n-type is the preferred choice with passivated contact technology.
Gunter Erfurt, CTO, Meyer Burger, said: “This is too early to say. When you look at the highest efficiency cells so far for PERC, these were p-type. It started with the initial Martin Green [UNSW] cell – this was a p-type above 24.6 or 25% and now with the p-PERC cells that ISFH presented one month back it’s another proof that it is a false statement when people say n is by definition better than p. This is not true, it’s all about managing the silicon bulk quality to get it to a level where it’s allowing for higher efficiencies.
“Next year, I think 2019/20, the two dominating gallium doping patent families are expiring after 20 years – Shin-Etsu and Kyocera. I believe this will be the moment when people are getting rid of boron and putting gallium because all the highly efficient PERC cells were all gallium-doped. You get very nice lifetimes, very little degradation only and there are more tricks and other ideas to use other doping instead of boron so I would say for the time being this is an open question.”
“At the end of the day it’s all about balancing the cost structure and if n is unable to reach the yields to make it a profitable business, it will not make the breakthrough.”
Hyun Jung Park, research fellow, Solar R&D Laboratory, LG Electronics, said the cell efficiency gap between both technologies had been reducing, but LG has been developing n-PERT, TOPcon and HJT cells to maintain the gap between p and n-type. However, she noted that cost is still the weakness for n-type as it has higher wafer material costs than p-type wafers.
Nevertheless, LONGi’s Tian said he expects the n-type market to become bigger and bigger, which will make the cost difference between p and n smaller.
Wei Shan, CTO, JA Solar on the other hand said that p-type PERC will remain the prevailing technology for the next few years and said it was “a tall ask” to challenge that in terms of cost effective mass production of alternatives. Nevertheless, he said issues such as cost and yield would gradually be resolved and eventually n-type will take off.
Further reading on the n-versus-p debate
Commenting shortly after PV CellTech 2018, Finlay Colville added that the growth of the solar industry, driven by China in 2016 and 2017, had opened the door for a wide range of high-efficiency platforms across both n-type and p-type cell technologies.
“In many cases, especially in China, the technologies are not in direct competition with one another. And often, deployment in China is coming from secondary factors, such as parent company involvement in project development and EPC activities, or carve-outs for cell or module efficiency levels. This is hiding a genuine comparison based on operating costs and energy yields.”
“But it is clear that the n-type landscape is moving fast, and the technical success of LG Electronics has ushered in a new wave of companies seeking to make modules where the key differentiation today is based on cell efficiency, with these companies yet to fully address the issues yet to come when operating factories profitably at the multi-gigawatt level.”