Module selection for utility-scale solar sites in 2019 is likely to see the widespread availability of higher performance products with average selling prices significantly lower than witnessed over the past 12-18 months.
While on the surface, this may appear as a dream-come-true for project developers and EPCs (especially outside China), the challenges in identifying bankable suppliers with quality product offerings are set to increase dramatically, placing far more pressure on making the correct decision to mitigate against risk of plant underperformance over a 20-30 year operating lifetime.
Unlock unlimited access for 12 whole months of distinctive global analysis
Photovoltaics International is now included.
- Regular insight and analysis of the industry’s biggest developments
- In-depth interviews with the industry’s leading figures
- Unlimited digital access to the PV Tech Power journal catalogue
- Unlimited digital access to the Photovoltaics International journal catalogue
- Access to more than 1,000 technical papers
- Discounts on Solar Media’s portfolio of events, in-person and virtual
This article explains the background to these imminent changes to module supply, including an outline of the module suppliers’ landscape for 2019, while also identifying the most challenging criteria for developers and EPCs in terms of module supplier and technology-type selection.
The discussion below on module technology (and supplier) selection is perhaps the key takeaway for EPCs and developers, providing top-level selection criteria on modules for 2019 and the areas where increased scrutiny will be required.
Data shown here is taken from PV Tech’s Market Research analysis, included in the May 2018 release of the PV Manufacturing & Technology Quarterly report.
Reference is also made to the themes set to be covered in the forthcoming PV ModuleTech 2018 meeting on 23-24 October 2018, in Penang, Malaysia, where module supplier benchmarking is addressed in detail.
72-cell multi modules met utility demand with few questions asked
Until the end of 2017, the PV industry had depended critically on the availability of p-type multi crystalline silicon (p-multi c-Si) modules somewhat as the default go-to choice for utility-scale deployment by many developers and EPCs.
The main exceptions were projects that used First Solar’s Series 4 thin-film panels, or SunPower’s E-Series c-Si premium (n-type back-contact) panels.
An uptick has been seen in the use of p-type mono c-Si panels over the past few years, with much of the deployment here being within China, using modules where the entire value-chain of manufacturing (poly/ingot/wafer/cell/module) has been domestic.
Otherwise, for the (non-China) global developers and EPCs, module selection has been mostly about which supplier of 72-cell p-type multi modules is successful, and less so on the technology type. It is this category of developers/EPCs that needs to be most aware of the changes set to unfold regarding module technologies (mono driven) and the new paradigm of ASPs on offer.
Why has multi been so dominant for utility-scale solar?
The answer to the subheading above is not complicated. Utility solar has been the main driver of growth in the solar industry in the past 10 years, and this has been accompanied by limited supply of mono-grown ingots (needed for mono wafers used to make mono cells/modules).
In fact, capacity and production levels of multi c-Si wafers and cells has rarely been in short supply, maintaining widespread low-cost product availability for developers and EPCs. Barriers-to-entry in making multi wafers have been low, and having GCL-Poly setting up tens of GW of low-cost/low-price wafers set the benchmark for every other multi wafer supplier in China/Taiwan.
Had the world decided collectively overnight that the choice of utility-scale solar was to be confined to First Solar, SunPower or p-type mono modules, then it would have seen more than 80% of utility-scale solar being removed, due entirely to lack of module availability from this subset.
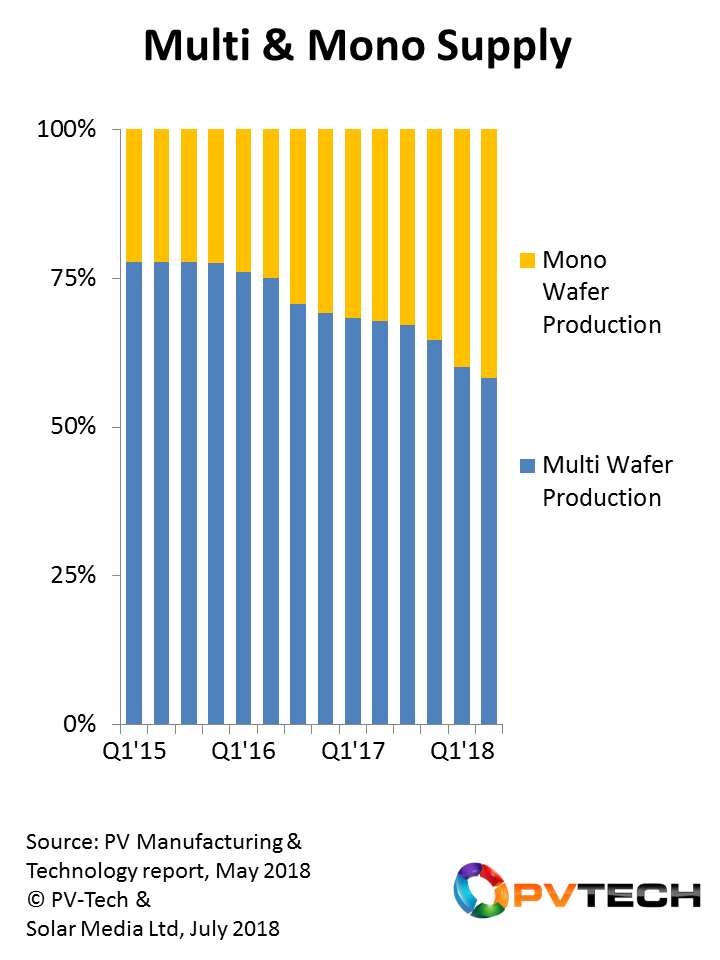
Developers and EPCs have needed 72-cell p-type multi modules to exist. And many of them have been largely unconcerned with origin-of-manufacture, and whether the maker of the product was in Vietnam or Thailand or chosen ad-hoc from one of China’s many quasi-OEM state-funded institutions.
Pricing was low, often serving the primary goal of lowering site capex and maximising profits when flipping signed-off accredited/PPA-secured plants. Product was available in droves, even during the various trade-related cases in recent memory.
If module suppliers and their respective technologies had been created equal, then this would be the end of the story. However, the raft of underperforming solar plants globally today indicates this is clearly not the case, and anyone thinking that solar modules are a commodity offering needs to spend a few hours with asset owners and O&Ms to get a strong reality check.
For most of last year, for example, looking at many of the 72-cell modules installed globally (or at least reading off the datasheets) showed few if any differences across 50-100 module suppliers, differing only in frame dimensions.
It is therefore little surprise that one of the most frequent questions asked has been: which is the best module supplier – who should I buy from?
If EPCs and developers thought life was tricky in the past few years (having to select which company for 72-cell p-multi modules!), then they are in for a rude awakening by the end of this year, unless they become far more educated in what the GW-scale module supply landscape is set to become shortly. These changes are set to offer major opportunities for plant design, but come with an equal dose of risk should the wrong supplier or technology-type be deployed.
Mono, n-type variants, bifaciality, and Series 6 thin-film panels
Going into 2019, an increasing number of utility solar farms are going to be utilizing p-type mono modules (almost all of which will be PERC based), with ASPs largely at parity with p-type multi offerings and at sub 30c/W (EXW) pricing.
While design and operation of solar farms will reflect the higher powers from p-type mono, the main question for module users is likely to come from the increased number of Chinese based suppliers, and which company to choose for site deliveries.
By now, it is no great secret that the Chinese market is not going to keep growing exponentially, simply to absorb the collective shipment targets of companies that have added capacity (from polysilicon through to modules) over the past couple of years. This single fact will see approximately 20-30 Chinese-based module suppliers seeking to grow export business, adding to the 10-20 existing Chinese companies that have appreciable overseas sales revenues today.
Which of the 30-50 Chinese module suppliers are truly bankable? How many of these companies have a level of manufacturing quality control that is low enough risk for external solar farm investors? Are their PERC modules reliable, with a fully-audited bill-of-materials?
But perhaps more pertinent, how many of these companies will be solvent 2-3 years out and able to honour 20-30 year performance guarantees?
In addition simply to increased p-type mono modules (72-cell PERC), there will be more offers for n-type modules than seen before. Several caveats apply here, as n-type now includes a wide range of company types and performance levels, not to mention strategies.
In theory n-type modules have the capability of higher efficiencies (power ratings) and superior elevated temperature operation, compared to p-type mono and multi modules, as explained below. EPCs and developers should at a minimum absorb these basic facts.
There are three basic types of n-type modules: n-type PERT (using manufacturing processes and equipment closely aligned with p-type mono PERC), n-type heterojunction (HJT), and n-type back-contact (or often assigned as interdigitated back-contact or IBC).
Currently, the efficiencies (STC power ratings) from n-type PERT modules are not that different from best-in-class p-type mono PERC variants, suggesting that the value-added proposition for n-type PERT lies mainly in the temperature coefficients.
At the top-end, LG Electronics version sits as the gold standard today, with several in-house differentiators (front/rear implanting, multi-wire front grid interconnections): however, LG’s priority (excluding its domestic market and a few isolated occurrences) is mainly on rooftops, and not mega-solar ground-mount deployment. Therefore, many global utility-based developers and EPCs will remain somewhat excluded from using these panels still.
Other n-type PERT modules are coming now from new Chinese companies, none of which has any strong heritage in solar cell production (aside from Yingli Green’s legacy PANDA lines). All of these companies have plans to export in volume to global utility projects in 2019, and this certainly points to a greater awareness of module users when it comes to qualifying these suppliers.
The next n-type architecture seeing increased attention is heterojunction. For years, HJT modules were synonymous with Sanyo’s trademarked ‘HIT’ modules, simply rebranded as Panasonic following the acquisition phase. HJT production is fundamentally different to all p-type cell/module assembly, and to n-type PERT variants. These lines are process and equipment tool specific and represent a step-up in terms of manufacturing complexity.
In the past 2-3 years, it is mostly HJT that has seen the investment dollars in China across new entrants in cell/module production that needed to select an advanced technology-type to differentiate from the p-type juggernaut that is already in operation. HJT has also been a convenient technology-transfer route for a number of a-Si thin-film fabs (extending outside China also) that had adaptable deposition equipment/know-how needed to make c-Si HJT cells.
In an ideal world, HJT deployment sits firmly on residential rooftops, commanding ASP premiums that are needed to absorb higher material and production costs compared to the leading multi-GW p-type suppliers today. While LG and Panasonic have been able to manage this mostly during their solar industry participation, these companies benefit from brand association and installer confidence levels built up over many years.
New HJT suppliers are therefore left to focus on ground/utility segments, suggesting again that global EPCs/developers are likely to see new offers from this grouping during 2019, as GW levels of production hits the market with no easy supply channels in China to absorb all produce.
The final n-type (and the most advanced and premium performance) category is based on the back-contact or IBC structure, something that (aside from pilot-line activity in Korea) is the sole domain of SunPower across its Southeast Asia fab operations. This is no indication at all that this will change in 2019 or the foreseeable future, such is the barrier-to-entry level in terms of in-house IP (process and equipment tooling based) that SunPower has meticulously crafted over 20 years of production experience.
This ensures that SunPower’s products will remain the highest-performing (STC and elevated temperatures) and with the highest ASPs in the industry, largely without technology-specific competition. This continues to allow SunPower to be selective (for its IBC product lines) in terms of application segments (residential, C&I and utility split), regional deployment, and shipment to in-house or third-party sales. Applying these factors, and given the GW level of IBC product available (compared to the 10GW mark now common to several of the global p-type module leaders), one can conclude that most of the global EPCs/developers will continue to be forced to make choices confined to the other module technology types.
The final technology type to consider of course is thin-film, with this technology belonging to one company today – First Solar. Yes, there are other thin-film companies in the solar sector still, but they are either seeing declining fortunes in terms of product availability and global competitiveness (e.g. Solar Frontier) or have limited if any market credibility or bankability (e.g. almost all Chinese based thin-film investments going back well over 10 years now).
Manufacturing exclusivity aside however, First Solar’s successful roll-out of its Series 6 panels (coupled with multi-GW of new fab builds across three countries now) is set to provide higher performance products in far greater volumes than seen in the past. However, this is not simply confined to product coming off the production lines, but the amount that is now being shipped or sold to third-party developers and EPCs.
To put this into context, during 2019, MW-levels of shipments to third-party developers/EPCs are forecast to increase by approximately one order of magnitude, compared to third-party shipments just 4-5 years ago, and could easily exceed the 4GW mark next year.
Given also that First Solar’s product is – for all purposes – utility-segment specific, this effectively propels First Solar to a new place in the PV industry, and will bring a whole bunch of new EPCs/developers into contact with thin-film products for the first time, or simply re-engage those that had been champions of thin-film panels for utility deployment in the past but were forced to rely on p-type multi-modules to fulfil build-out plans over the past few years.
What does this really mean for EPCs and developers?
In short, the companies and product types being considered for utility-scale solar in 2019 will be different to what has been seen for most of the past 2-3 years (where almost everything was 72-cell p-type multi).
Many of these companies have minimal track-records in exporting supply out of China, some are new to cell/module production and are trying to ramp up GW-levels of new process flows for the first time, while others (JinkoSolar, Canadian Solar, JA Solar, First Solar, for example) are firmly established with global EPCs/developers and will release new module versions with improved performance and reliability.
It is probably fair to say that any developer/EPC currently planning a utility-based solar site for 2019 based on 72-cell p-type multi-modules should pause, and ask whether this is the best option in terms of investment ROI or secondary site valuation figures in three years from now.
While not wanting to complicate the issues, seasoned campaigners may well be asking why there is no talk above of bifacial/half-cut/shingles. The reason for this is relatively simple.
Right now, these are still options, not necessities in the market. The benefits are not in doubt. It is just that they are more additive to existing plans (which are not yet fully implemented and qualified in production).
Bifacial remains a curiosity more than a must-have, with widespread confusion about just what is on offer in terms of yield deltas, and how it is possible at all to predict performance over 20-30 years. While the easy argument is to say that anything extra is always good, this is as dangerous a statement for investors and O&M’s as is anything impacting site underperformance.
How do you value the worth of a site, if you can’t forecast yield over 20 years? How can you set performance ratios for O&Ms or even dare to include upside payments based on over-performance relative to a fixed (unknown) reference line?
Either you bit the bullet and have some carefully-worded clauses into supply arrangements (power guarantees) or have highly-flexible O&M contracts (especially during the first 2-3 years), while baseline parameters (likely almost all site/environment specific) are established. Or you just wait a few years until the industry has worked out how to deal with double-sided absorption from solar modules.
Half-cut modules are less of an unknown or a differentiation and EPCs/developers have less reasons to fear them, other than diving into module supplier selection from an unknown entity. Until now, half-cut cell module design has been a key focus from REC Solar: it is unclear still how much the Chinese sector will fully embrace. Will China solar want to laser cut all its cells in two and re-assemble them all across its various cell/module supply-chains? Taking this one step further to multi-cut – or singulated cells designs – and potentially we enter more niche-status manufacturing today.
PV ModuleTech 2018 to provide clarity for EPCs and developers
Going into its second year, PV ModuleTech 2018 will focus specifically on utility-scale module supply and demand for the 2019/2020 period, in particular for all countries/regions outside China.
Therefore, this two-day conference should provide EPCs and developers with the tools they need to assess and benchmark module suppliers and product technologies for sites in preparation or going into planning/approval phases over the next 12 months.
The event will include a non-China specific geographic module supply session, where the demand for modules outside China in 2019/2020 will be explained, including company and technology market-shares in key regions globally today and how this may change going forward.
Leading module suppliers will then outline product availability, and what measures are in place to ensure bankability and product quality, and how these companies are placed to honour 20-30 year performance guarantees.
PV ModuleTech 2018 will again hear from leading independent engineers, test and inspection organizations, certification labs, factory auditors, and module assembly materials and equipment suppliers.
Findings from the event will be invaluable to companies (EPCs, investors, developers, O&Ms) whose business models are contingent on the correct module type and supplier being chosen.
Details on how to attend PV ModuleTech 2019 can be found here, including the event agenda. Speakers are by invite-only from the PV Tech team, and will be revealed by us in the coming weeks.