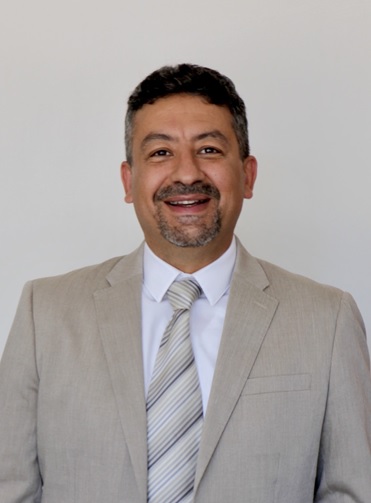
Recently, PV-Tech featured an extended interview with Cherif Kedir, the President and CEO at the Renewable Energy Test Center (RETC), based in Fremont, California, regarding new trends in module reliability and performance testing.
Following this Q&A, we returned to chat with Cherif again to explore some of the key themes raised during the initial discussion, and ahead of a forthcoming webinar hosted by PV-Tech on 12 November 2020, featuring Cherif and PV-Tech’s head of research Finlay Colville; registration to the webinar is free and details can be found here.
Unlock unlimited access for 12 whole months of distinctive global analysis
Photovoltaics International is now included.
- Regular insight and analysis of the industry’s biggest developments
- In-depth interviews with the industry’s leading figures
- Unlimited digital access to the PV Tech Power journal catalogue
- Unlimited digital access to the Photovoltaics International journal catalogue
- Access to more than 1,000 technical papers
- Discounts on Solar Media’s portfolio of events, in-person and virtual
What different PV module trends is RETC seeing most during 2020, from a technology and format standpoint?
Cherif: “As many have taken notice, we have seen a push towards the larger format modules with full adoption of bifaciality. Bifacial technology is no longer considered a novel technology by developers and the rest of the downstream community. The larger modules with higher power outputs have become the trend in 2020, and we don’t see it slowing down.
We have had numerous discussions with module manufacturers as well as raw material suppliers, and it seems the entire value chain is shifting their capacity towards large format modules.
There are clear cost benefits for the manufacturers as well as a positive impact on total project cost; as module power increases, fewer modules need to be installed for a fixed target capacity.”
As these changes are being implemented by leading module suppliers, what impact is this having on module durability, especially in real-world conditions?
Cherif: “We have seen more failures in recent reliability tests where previous generations of modules had consistently performed better. Larger and more powerful modules are great for our industry; however, as modules get larger, they get heavier and more difficult to handle and install, thus potentially increasing the installation labour cost. This has led most manufacturers to reduce glass and frame thickness, both to reduce cost, and to make the modules easier to handle. This has created a challenge for these modules in their ability to withstand stringent mechanical tests. Moreover, when the front glass thickness is reduced, they are less able to withstand hail impact. This is not a great development considering the number of installations in hail prone areas as well as the documented increase in frequency and severity of hail events.”
Are there any particular stand-out qualities being undertaken during module assembly that other module suppliers should be seeking to implement to improve module reliability?
Cherif: “High power modules in conjunction with a structurally robust module are ideal for today’s market needs. We have seen manufacturers utilize varying designs to make modules more robust. Some examples include internal support designs, thick frames and glass, etc. However, we have seen the most innovation to real life situations from tracker and racking companies who have had to adapt to this changing landscape of module sizes. New features such as hail and wind stow are very relevant to today’s PV projects and where they are being installed.”
Cherif: High power modules in conjunction with a structurally robust module are ideal for today’s market needs. We have seen manufacturers utilize varying designs to make modules more robust. Some examples include internal support designs, thick frames and glass, etc. However, we have seen the most innovation to real life situations from tracker and racking companies who have had to adapt to this changing landscape of module sizes. New features such as hail and wind stow are very relevant to today’s PV projects and where they are being installed
Cherif: “Back in 2009 and 2010, we worked with the industry to introduce the first consolidated durability test protocols as a result of the countless failures we were seeing as we worked with manufacturers racing to certify modules they wanted to introduce into the market. In recent years, after we launched the bifacial characterization program in 2018 in collaboration with Black and Veatch and the hard work of Dr. Ralph Romero, we started noticing mechanical failures at a higher frequency than monofacial modules. As the modules lost some of their structural integrity, racking and tracker manufacturers compensated with different clamps and rails to maintain compliance and prevent modules from failing. However, when it came to hail, there was no other way to compensate. Glass cannot be covered or protected.
As a result of the types of failures we were seeing, we developed a program, the Hail Durability Test, which can be used to assess the hail tolerance of modules. The results can be by developers, independent engineers, financial institutions as well as module manufacturers to assess the risk associated with installing certain modules in specific hail prone regions based on historical and projected hail severity.”
Thanks again Cherif, and looking forward to seeing much more on the hail testing during the webinar!
The webinar on 12 November 2020 – PV Module Reliability & Bankability for Utility Solar Deployment – will feature online presentations by Cherif Kadir and PV-Tech’s Finlay Colville.
The talk from Finlay will also see the first preview of the new Q4 2020 PV ModuleTech Bankability Ratings pyramid hierarchy, revealing which module suppliers have increased scores in the past 3 months.
To register to attend the webinar, please follow the instructions at the webpage here.