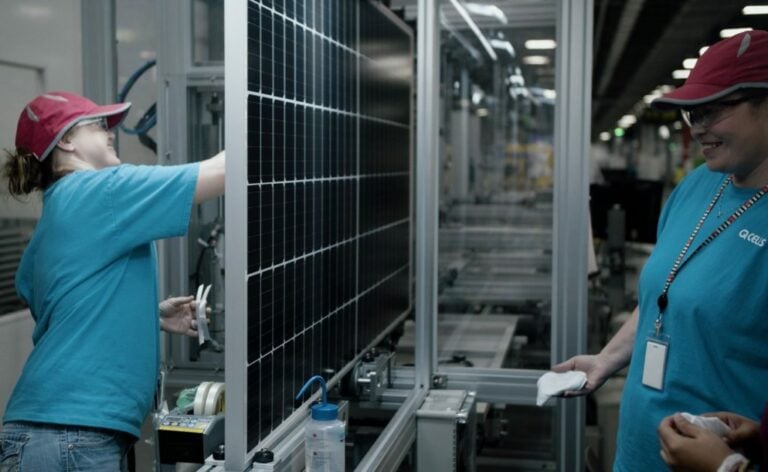
The largest solar investment in US history, a pivot to a vertically integrated PV manufacturing facility in the state of Georgia by Qcells, was enabled by a combination of state support, federal government investment and related benefits coming from the Inflation Reduction (IRA), according to the company.
With Senator Jon Ossoff at the helm, the state of Georgia has become attractive as a PV manufacturing location with various incentives and supports already drawing several large-scale clean energy investments. Indeed, it was Senator Ossoff who wrote the Solar Energy Manufacturing for America Act (SEMA), offering incentives for each unit of polysilicon, solar wafers, cells and modules produced within the US.
Unlock unlimited access for 12 whole months of distinctive global analysis
Photovoltaics International is now included.
- Regular insight and analysis of the industry’s biggest developments
- In-depth interviews with the industry’s leading figures
- Unlimited digital access to the PV Tech Power journal catalogue
- Unlimited digital access to the Photovoltaics International journal catalogue
- Access to more than 1,000 technical papers
- Discounts on Solar Media’s portfolio of events, in-person and virtual
With this background, Qcells recently announced plans to invest US$2.5 billion on a 3.3GW ingot, wafer, cell and module manufacturing plant in Bartow County, Georgia.
“A very big component of this is the IRA and within that was the SEMA tax credits,” Marta Stoepker, director of public relations at QCells, tells PV Tech Premium. “That really changed the game. I’ve been working in energy policy for a long time and the fact that we have tax credits that exist past a year allows us to plan to the future. That alone is massive. What it will do for the clean energy industry and for our business, it’s huge. We wouldn’t be able to go as big as we’re going without that.”
Given that most of the PV supply chain is controlled abroad, it can be hard to stay competitive in the global or even domestic market. Stoepker adds that the new financial supports provide a solid foundation to build on the significant support offered by Georgia to help build the new facility, and this is driven by a clear push towards buying modules made in America. Initially, the new factory will primarily serve the growing demand in the US market.
“Right now, 80% of ingots and wafers are made in China,” Stoepker adds. “So, this is really important in terms of diversifying where people can buy their components for solar panels. The demand is high for solar around the world. And we need to be able to rise to that demand.”
The significance of the new facility is held in its vertical integration, which has not been achieved in the US at this scale before. Silicon, ingots and wafers have tended to be vastly outweighed by cell production and module assembly in the US. However, by becoming a major stakeholder in REC Silicon, a Norway-headquartered producer of silicon materials that has two plants in the US, Qcells can now tap into this market and combine it with an already well-established cell and module production capability.
Silicon production is the most energy-intensive part of the PV manufacturing cycle, but REC Silicon’s operations at Moses Lake in the state of Washington and at Butte in Montana are 100% powered by hydropower.
“There are a lot of customers that are wanting to buy the most sustainable products out there and we’ll hopefully be able to offer that very soon,” says Stoepker, adding: “There are other companies that are exploring other components, but it is not vertically integrated. So, the fact that we are able to provide all of the pieces that make a panel whole for our customers is really attractive.”
Qcells did not provide details on which specific module types it would be producing.
Georgia’s pull
Led by Senator Ossoff, Georgia is making its own incentives for renewables and is working with clean energy companies to create the policy vehicles necessary for large-scale announcements like that of Qcells.
Qcells is already well positioned in the state having already put in place what is said to be the largest PV manufacturing facility in the western hemisphere in Dalton, which it has been working on with the state since 2018.
Georgia also has land available near city centres, which is important for Qcells’ requirement of hiring around 2,500 new people on top of its current workforce. Stoepker issues a common refrain heard from the US solar industry in recent months, which is that the biggest challenge is going to be hiring new employees.
“We have to hire people and we are going to ramp up really quickly,” she says. “We are going to be scrambling looking for really incredible individuals that want to join this company and be a part of our mission. it’s a challenge but it’s also a huge opportunity. That’s why we’ve strategically located our facilities in places that we think would be of interest to people who want to join the clean energy industry as a career.”
The site location is 40 miles from Atlanta, the largest city in the state, and Qcells is hoping to draw interest from high-skilled workers coming out of Georgia Tech university.
Qcells’ parent company, Hanwha Solutions, has said that it intends to break ground on the manufacturing plant in Q1 2023 and reach 8.4GW of module production in Georgia by 2024.
Last week, Qcells signed a deal with Microsoft to supply at least 2.5GW of its modules to projects from which the tech giant will purchase renewable energy.