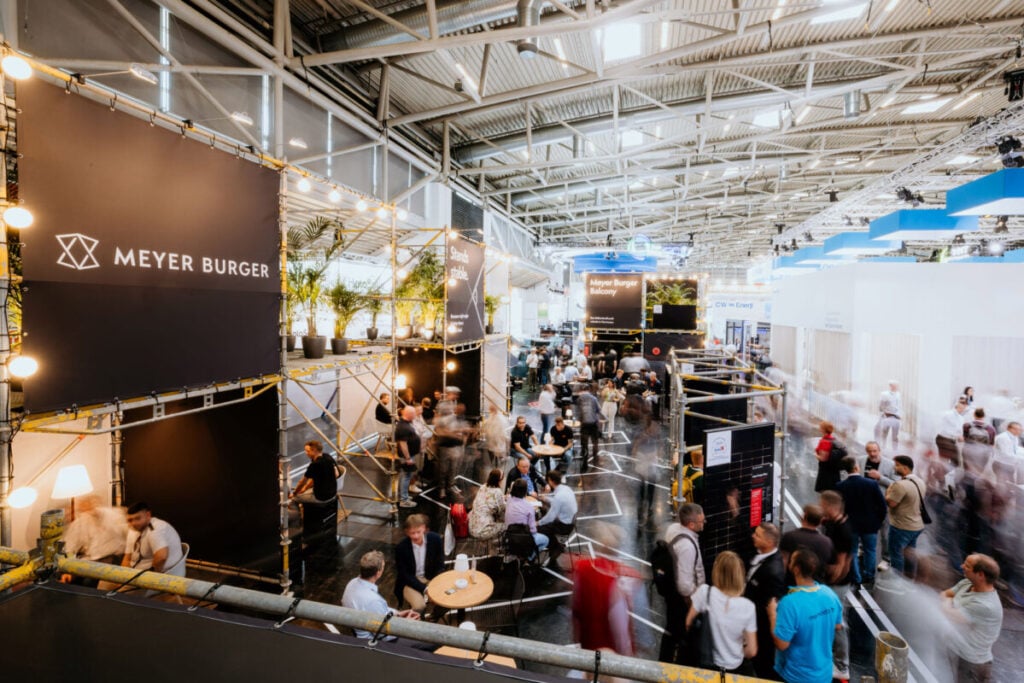
“It’s been a massive disappointment,” says Gunter Erfurt, CEO of Meyer Burger, of the EU’s efforts to support solar manufacturing.
“There has been so much macho talking…and exactly zero has happened. It has been a massive disappointment. And I say ‘has been’ because we are over it.”
Try Premium for just $1
- Full premium access for the first month at only $1
- Converts to an annual rate after 30 days unless cancelled
- Cancel anytime during the trial period
Premium Benefits
- Expert industry analysis and interviews
- Digital access to PV Tech Power journal
- Exclusive event discounts
Or get the full Premium subscription right away
Or continue reading this article for free
The Swiss-owned manufacturer has recently begun operations at its new module production facility in Arizona, US, after announcing the closure of its German module assembly plant in January this year.
Erfurt spoke with us at Meyer Burger’s stall at the Intersolar Europe 2024 show in Munich earlier this month. The company won a sustainability award for the stall itself—pictured above—which was made of scaffolding, black fabrics, solar modules and rented plants. It was also erected directly onto the scuffed, black hangar floor rather than insulated with carpet or imitation wood. To reach the stand, you had to pass directly in front of the brightly-coloured, brightly-lit, booths of other manufacturers (predominantly Chinese manufacturers) before reaching the skeletal black booth at the end of the row.
Beyond practical reasons (Erfurt says the company was combining “saving money…with the best sustainability”), the stall seemed to be a statement: a visual metaphor of the company’s decision to wash its hands of Europe for the time being and ship the cells produced at its remaining German factory directly to the US—a whole operation that can be relocated.
Decision to leave
Meyer Burger had been contemplating moving to the US before the Inflation Reduction Act (IRA) brought in major incentives for solar manufacturers. Erfurt says, “By the end of 2021, we had already spotted the building in Arizona and basically secured it. We were contemplating going to the US not only as a sales market but to produce.”
Given the fact that the IRA did not exist, this was driven by a desire to diversify the supply chain geographically, which was already overwhelmingly concentrated in China. “Interestingly enough, there were companies who were starting to look at the US around the time when Trump came into office to diversify supply chains,” he says.
“Then the IRA came, and two days later, we signed the first offtake agreement with DESRI (DE Shaw Renewable Investments), and two more came in 2023, and that triggered us to go full throttle into Goodyear, Arizona.”
At this point, the module production facility in Germany was still running, if perhaps beginning to strain under European market conditions. The company didn’t plan to abandon its module production in Europe until the “market erosion”, as Erfurt calls it, began in 2023. Reports of huge overcapacity of Chinese solar modules in Europe, largely from redirected shipments denied entry to the US, combined with overcapacity across the solar supply chain to push module prices off a cliff and imperil operations for Western manufacturers.
“At the time, we thought it would make sense to have a solar cell manufacturing hub in one place, which would have been Germany. That was the original strategy,” he says. But as the market conditions worsened and oversupply and low pricing continued, Meyer Burger waited for a response from the EU.
“We didn’t really see a response. So we decided last year, in the summer, to move the cell supply that was bound for Germany to Colorado Springs,” Erfurt explains. The company is currently building the 2GW Colorado Springs facility, which will produce its heterojunction technology (HJT) cells for module production in Arizona.
“We didn’t even know that the ITC (investment tax credit) scheme for domestic content would come in,” he says, citing the IRA’s Domestic Content Bonus which adds a 10% tax credit on top of the 30% ITC for products that meet the threshold for “US-made”.
Then, in January 2024, the same week that the company received a shipment of the manufacturing equipment at the new Arizona plant, it announced the abandonment of operations at the European module plant due to the “absence of firm commitments” from the EU.
“I think history has proven us right.”
Coming to America
Conditions for establishing solar manufacturing in the US have been good since the IRA came into force. The situation isn’t without challenges, and it has so far resulted in far more module assembly plants that rely on imported cells than upstream capacity that could supply US-made modules, which some observers have said is cause for concern. However, the US has seen an explosion in solar manufacturing capacity announcements since the act passed.
As Erfurt said, Meyer Burger was looking to set up stateside before the incentives came about, but the Domestic Content bonus – for which guidance was released in May last year – is “very, very good” for the company.
The Domestic Content adder requires that solar modules put into service are made with at least 40% “US-made” components, rising to 55% at the end of 2025. Crucially, the calculations for meeting the threshold are based on the cost of a product; for a solar module, that puts a huge emphasis on the solar cell, which constitutes the largest portion of any single component.
PV Tech Premium has previously covered the challenge that this posed to manufacturers at the time of the announcement, and the Solar Energy Manufacturers of America (SEMA) coalition has called for the Domestic Content adder to extend to “see” wafers in the solar supply chain to make it more effective for onshoring US supply. Developers who benefit from the tax break would theoretically provide a reliable market for domestically produced solar products.
For Erfurt, it’s more than theoretical: “The cell currently accounts for 39% [of the tax calculation]. I would say any product in the US that just has a module made of imported components is going to be unsellable sooner or later. Because developers are looking into how they can meet the minimum threshold, which is 45% this year, but you still get the ITC tax credit for the project regardless of where the material comes from.
“[By the end of 2025] you’ll get the ITC tax credit if you have 55% domestic content. That’s changing gears. So you have two options as a supplier: either you produce [more than modules] domestically in the US, or you need to compensate by dropping your prices to levels where nobody has fun.”
The conversation turned to another key issue that has been emerging in the industry of late: quality, and how it can be particularly relevant in the US.
“The average term for PPAs in the US is substantially longer than in Europe and other markets. If you’re a project financier, you ask ‘how sustainable is your product? Because I might finance you for the entirety of 20, 25, we’ve even heard 35 years.” There are also suggestions that US PPA prices will increase over the coming year, largely due to interest rates, permitting procedures and potential supply headwinds.
We published a deep dive into the looming quality problem that faces the PV industry in our downstream journal PV Tech Power at the start of this year, from which it emerged that the massive capacity expansions of Chinese-owned companies and the concurrent steep price drops across the value chain have put immense pressure on the cost of module production. It follows that manufacturers are at pains to cut those costs wherever they can, and it seems to be coming out in the wash with the solar modules hitting the market.
In fact, one of the most noticeable things on the trade show floor where we spoke with Erfurt was the prevalence of quality assurance and maintenance companies.
‘Quality matters’
‘The industry has maybe got a bit of an awkward reputation recently,” Erfurt says, in response to a question about growing quality concerns. “There was new technology implemented, but then we start to see all these reports…”
He is referring to a report from the University of New South Wales (UNSW)in Australia which found TOPCon solar cells suffer “significant degradation” under damp heat testing in comparison with their older, less efficient PERC counterparts. The results were striking; TOPCon cells suffered power losses ranging between 4% and 65% compared with PERC’s consistent 1-2% loss. All of the major Chinese solar manufacturers have set out their stores for TOPCon cells and modules over the next two years at least. There have also been reports from a number of testing houses that have shown increases in solar cell and module defects, often from major producers.
“And the UNSW is not just a university – it’s the whole Martin Green thing,” Erfurt says – Martin Green being the Queen Elizabeth prize-winning inventor of PERC solar technology.
He continues: “Many players thought they would just convert a PERC line and just run TOPCon, and continue with the old PERC BOM (bill of materials). It’s just not working, and you might ask, ‘How can this happen when all these guys have achieved a certification?’”
This question, it turned out, was to be left unanswered by Erfurt, but when we looked into quality concerns for a previous PV Tech Premium article, we were confronted with stories that suggested cost-cutting measures on the part of manufacturers that were impacting products on the ground.
With PPAs growing longer, particularly in the US, quality issues have tangible effects for investors, financiers, deployers and asset owners, Erfurt says. “You cannot allow any mistakes, The message is clear: quality matters.”
As we were running out of time, we asked Erfurt about the prospect of coming back to the European market. Multiple staff members on the show floor told us that the equipment was still sitting in the German module factory, covered and switched off, awaiting a reason to power back up or, as the case may be, to be shipped elsewhere or sold.
So what would it take for Meyer Burger to come back to Europe?
“If we face the brutal facts, the only chance Europe has is to make sure there’s a level playing field, and then the NZIA measures, if any, could help.”
The NZIA came into force last week after publication in the EU’s Official Journal, containing mandates for the bloc to meet 40% of its solar deployments with domestically produced products. It is now “in the hands of member states”, according to the European Solar Manufacturing Council (ESMC), to make European PV manufacturing competitive.
Erfurt says that, despite measures that may be included in the NZIA, “Without a level playing field, there is not going to be any production in Europe.”
A ‘level playing field’ is a phrase often used by Meyer Burger’s new American neighbours in the discussion around tariffs and trade barriers against Chinese-made PV products. Such measures do not seem forthcoming in Europe; the closest the EU has come is in its Forced Labour Ban, which will not come into force until 2027.
Erfurt says: “As much as it might seem a great situation right now for people in the supply chain that stuff is getting gifted by China, it is not sustainable. And they should realise it.
“We have been hearing less-than-good things from the inverter makers, we are seeing similar things in the wind industry and batteries, and now the big threat on EVs from China,” by which he means the emerging muscle-flexing and trade disputes between the EU and China over electric vehicles.
He continues and says that Meyer Burger’s “friends on the other side [of both the Intersolar trade hall and the globe] aren’t happy either.
“We have lost hundreds of millions in 2023; these guys are losing billions and laying off people. What’s happening right now has the potential for a massive implosion of the sector. We should really try and avoid it.”
For Erfurt, the only solution is the “level playing field. It enables fair competition, whatever that means. I think the idea of just having an NZIA is just romantic, it doesn’t work.”
The sense of harsh reality that Meyer Burger projected with its bare scaffolding stall was present until the end of our time with Erfurt.
“The net effect of regrowing an industry is always overlooked in Europe because we only ever discuss how much public money is spent. We should ask how much the public sector gets back via the taxpayers. The resilience bonus in Germany would’ve cost the country €25 million in 2024, and it would have solved the problem. It’s nothing.
And the industry always said that, in the very moment that this weird supply situation ends, take [the subsidies] away. We don’t want to be subsidised, we don’t do business to be subsidised. But they didn’t listen.”