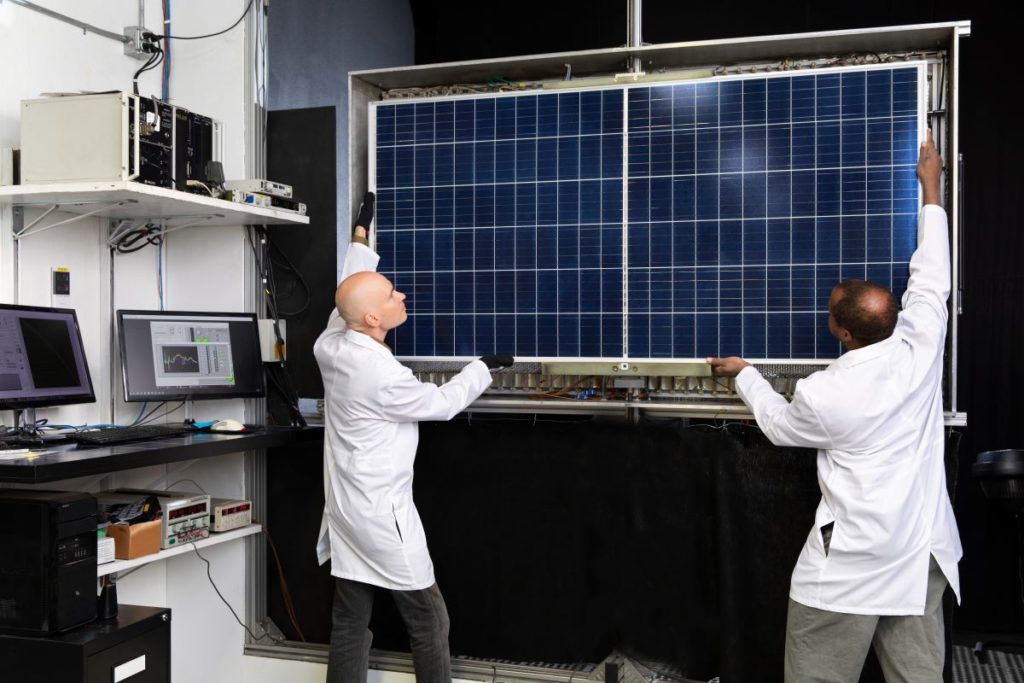
Tristan Erion-Lorico, VP of Sales and Marketing at PV Evolution Labs (PVEL), on the Inflation Reduction Act and its implications for the selection of materials going into producing solar modules.
Unlock unlimited access for 12 whole months of distinctive global analysis
Photovoltaics International is now included.
- Regular insight and analysis of the industry’s biggest developments
- In-depth interviews with the industry’s leading figures
- Unlimited digital access to the PV Tech Power journal catalogue
- Unlimited digital access to the Photovoltaics International journal catalogue
- Access to more than 1,000 technical papers
- Discounts on Solar Media’s portfolio of events, in-person and virtual
When the Inflation Reduction Act (IRA) was passed by the U.S. Congress in August 2022, the historic US$369 billion investment seemed poised to revolutionise the clean energy industry in the United States. New incentives would accelerate the manufacturing of key solar and wind components domestically, while additional tax credits stood to further increase project economics for wind and solar developers.
Research firm Wood Mackenzie predicted that the U.S. solar market could triple over the next five years. Likewise, a team of researchers at Dartmouth College and Princeton University released a report noting that the bill would create 1.6 million additional renewable energy jobs. The same report found that the IRA would allow solar projects to cut the cost of producing electricity by up to 60%.
The solar provisions of the IRA have two priorities: to increase domestic solar manufacturing, and to reduce dependence on Chinese imports. The bill aims to encourage more manufacturing of key solar components, including cells, wafers, frames, glass, and backsheets in the United States – and the solar industry is responding. By April 2023, the American Clean Power Association noted that over US$150 billion in domestic utility-scale clean energy investments had already been announced, along with 47 new manufacturing facilities. According to the Solar Energy Industry Association (SEIA), the IRA is expected to lead to more than US$600 billion in new solar investments and 200,000 new jobs over the next decade. Some of the most exciting elements of the bill have expanded on the existing investment tax credit (the Qualifying Advanced Energy Project Credit or Section 48C), and created the Advanced Manufacturing Production Tax Credit (Section 45X). Both the investment tax credit and production tax credit include adders for projects meeting domestic content requirements. However, there are lingering doubts about the industry’s ability to manufacture all the necessary components in the United States, and exactly what projects will qualify for the additional tax incentives.
The recently released guidance on the domestic content adder states steel and iron products such as racking will need to be made 100% in the United States, while manufactured products such as trackers, photovoltaic (PV) modules, batteries, and inverters will need to be 40% made in the United States (for projects under construction before the end of 2025; 55% beginning in 2026). In our latest Solar Technology and Cost Forecast (STAC Report), PVEL and Exawatt conclude that current domestic crystalline module manufacturing is unlikely to allow developers to satisfy these requirements for at least the next couple of years.
Confusion around which suppliers and what projects qualify for tax credits is only part of the headache. New factories and new raw materials inherently create new risks. Changing material suppliers or components during the procurement process can have impacts on both the immediate and the long-term performance of modules in the field. For over a decade, PVEL’s lab data has shown that minor changes to a PV module’s unique bill of materials (BOM) can have major impacts on its reliability and performance. Along with following other procurement best practices, the risks associated with module procurement and changing supply can be mitigated through independent, third-party testing. While the IRA offers an exciting opportunity to rapidly advance the solar industry in the United States, understanding BOM-level performance and reliability is going to become even more important to maintain quality.
Why BOMs matter: not all modules are created equal
Through our suite of extended reliability and performance tests, known as the Product Quali‑cation Program (PQP), PVEL has tested over 500 unique BOM combinations. The PQP tests all BOMs consistently, using world class equipment via testing at PVEL’s facilities in California, or overseen by PVEL’s experts at our partner lab within the Kiwa Group, PI China, in Suzhou, China. Every year, we publish the Top Performer modules in our PV Module Reliability Scorecard (available at scorecard.pvel.com), with relevant case studies to support the methodology of our tests.
PV modules with the exact same model type can be manufactured from completely different BOMs. Suppliers are free to mix-and-match integral materials – even the cells – as long as all the components are listed in the manufacturer’s IEC/UL certification report. Results from PVEL’s testing have repeatedly shown that changes to these individual module components can dramatically affect product quality, and therefore, relying on certification testing alone is not sufficient to determine long-term performance and reliability.
In a recent example from our damp heat (DH) test, PVEL received two BOMs produced by the same module manufacturer that used the same cells and same front encapsulants. The DH test simulates long-term degradation and failure modes that are typical in high temperatures and high humidity conditions where moisture and heat can weaken the materials binding the module together. One of the modules tested was glass//glass, while the other used a glass//backsheet design. The glass// glass BOM was a Top Performer in DH testing, but the glass//backsheet BOM had more than 7% power loss after the same test. The backsheet had clearly allowed moisture to enter the laminate leading to cell corrosion.
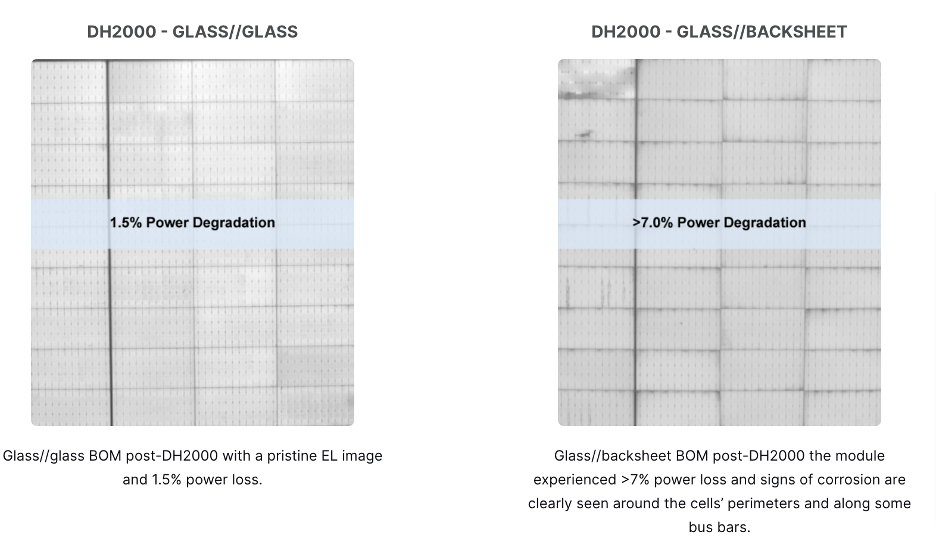
In another example from our 2023 Scorecard, PVEL tested two almost identical glass//glass BOMs from the same manufacturer for potential-induced degradation (PID). PID is triggered by high PV system voltages on ungrounded installations. PID is more likely to occur in projects that use transformer-less inverters, and is further accelerated by high-temperature and high-humidity environments. While it is sometimes reversible, severe and permanent PID can lower energy yield by as much as 30%.
The cells, glass and almost all other materials tested for PID were identical; the only differences between the BOMs was that the encapsulants were from two different suppliers (although both were front side EVA + rear side POE), and different frame and junction box sealants were used. After PID192(-) testing one BOM had 1.1% power degradation, and the almost identical BOM had 4.5% power degradation. What some may consider minor BOM changes resulted in one BOM having four times higher PID susceptibility.
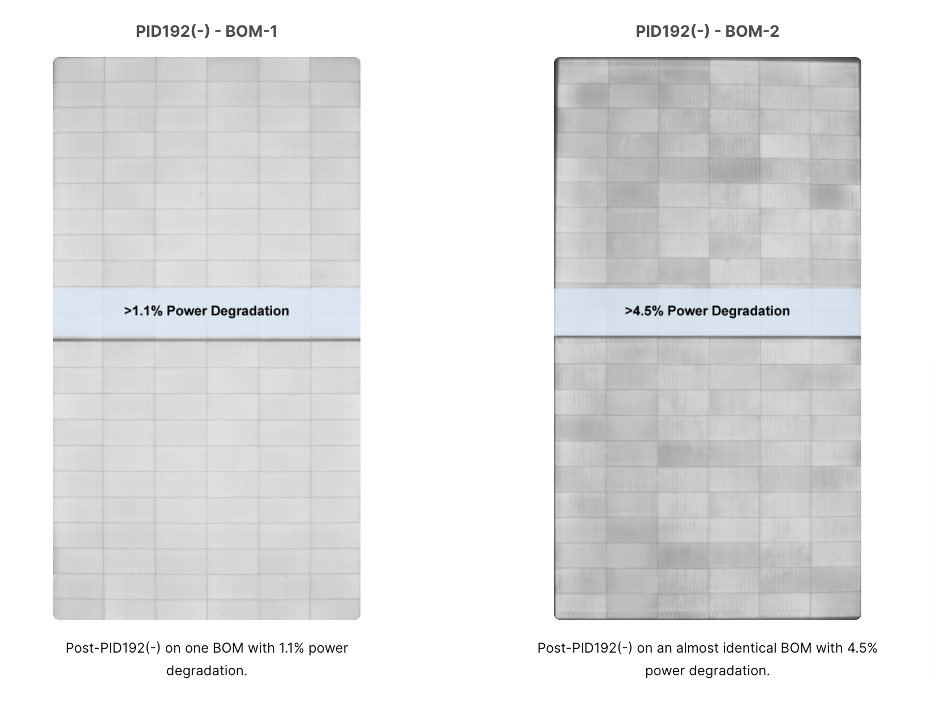
During PVEL’s thermal cycling (TC), another sequence in the PQP test, modules are subjected to extreme temperature swings in an environmental chamber. They are first brought to a temperature of -40°C, after which the temperature increases to +85°C. While the temperature is increased, the modules are subjected to maximum power current providing additional field-relevant stress. The cycle repeats 600 times in total, and characterisations are conducted every 200 cycles.
While most modules we test perform well for the IEC 61215 standard’s 200 thermal cycle test duration, some of those same modules experience catastrophic defects during the PQP extended thermal cycling. In a recent TC example, the module performed well through TC200 and TC400. However, after TC600 the module had no power output and a black EL image. PVEL investigated the failure and discovered an open circuit inside one of the module’s junction boxes. Had this been installed in the field it would have caused the entire string to have no output.
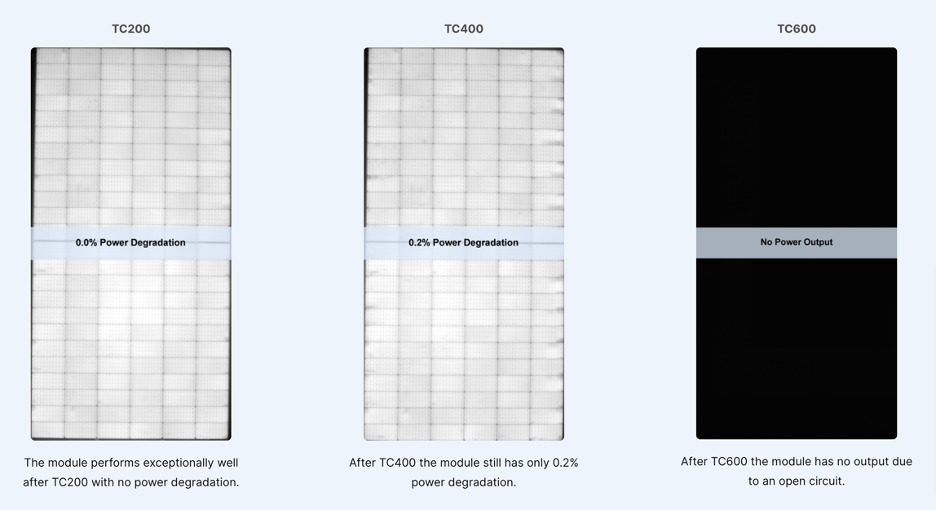
Failures occur in the lab and the field
While our 2023 Scorecard showcases the ways that overall PV module reliability trends are improving, the above examples are not unusual. In fact, 54% of manufacturers eligible for the 2023 Scorecard experienced at least one failure during PQP testing.
There are various types of failures observed in PQP testing. Modules can fail during visual inspection, including modules breaking during mechanical stress, junction box lids falling off, burn marks, melted/failing connectors, delamination, and power labels peeling off or becoming illegible. Safety failures are recorded when modules do not meet the minimum requirement for electrical resistance, something that is increasingly common during pre-stress testing. Power degradation failures happen when the power loss is beyond what the module manufacturer (or their customer) deems to be acceptable. And finally, diode failures are when the module’s bypass diode is no longer functional. Diode failures fall into a larger category of junction box failures which also include melted connectors, exposed wires, wet leakage failures traced to the junction box and failed junction box soldering. In the 2023 Scorecard, we reported that 29% of manufacturers and 19% of BOMs had at least one junction box related failure.
Failures observed in the lab can have real implications in the field. In a recent case, fellow Kiwa Group member Extel Energy was contracted to visit a 12 MW rooftop site in Taiwan. The project used 340W half-cut 120-cell mono PERC modules and was commissioned in 2021. Routine drone infrared (IR) imaging revealed hot spots at the junction boxes for some modules, along with some activated bypass diodes. Upon further inspection of the site, Extel found some completely burnt junction boxes. Of the around 35,000 modules on site, 700 had hot spots at the junction boxes visible in IR images, 70 had bypass diodes activated and 10 had extreme junction box burning. The module manufacturer investigated and determined that these were all due to a soldering issue within the junction box. They have since updated their quality and process control to implement pull testing on their junction box soldering.
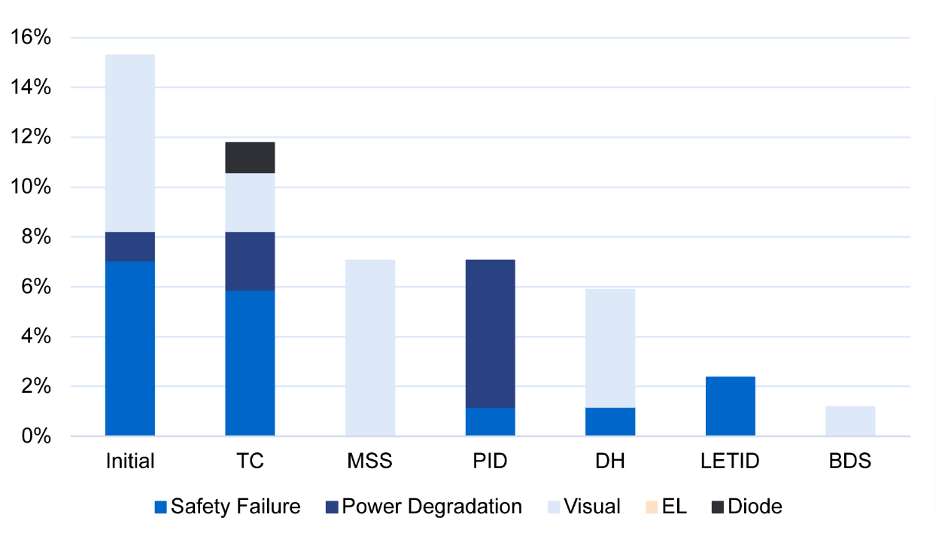
While replacements for the affected modules were provided by the manufacturer, the cost of labour to replace these modules and to diagnose the issue was not covered by the module manufacturer’s warranty. It is unclear if other modules will be affected by this failure mode in the future, given that they will experience natural temperature cycling in the field and its effects on soldering reliability.
PVEL has reported junction box related failure issues in every edition of the Scorecard since 2019. This problem remains persistent both in the failures identified by PQP testing and on modules in the field. As we diversify supply, and source components from new market entrants or factory locations, buyers need to do their due diligence to avoid the risk of unforeseen replacement costs if issues occur.
Taking steps to mitigate risks during procurement
Specifying top performing PV modules is only one aspect of risk mitigation during PV module procurement. As part of the Kiwa Group, PVEL and other member companies support downstream project stakeholders at every step of project development, construction, and operation. Below, we outline some of the Kiwa recommended best practices for module procurement:
- Specify Top Performing Bills of Materials. At PVEL’s labs, we test and report on the module’s unique bill of materials, providing this information to downstream partners so they can use this data to specify the BOM combinations that meet project requirements in PV module supply agreements.
- Audit and Monitor Factories. Sophisticated module purchasers require factory audits (independent inspections of a manufacturer’s production process) before PV module procurement to ensure suppliers meet quality standards. Monitoring PV module production during the manufacturing process also helps prevent quality issues in the modules produced for a specific project and ensures that the PQP-tested BOM is being used. These services are performed by companies like PI Berlin and others in the Kiwa Group.
- Validate Quality. Testing statistically significant samples of PV modules during module production helps buyers identify and remedy quality issues in the modules being deployed to their sites. This process, known as batch testing, requires shipping a randomly selected subset of PV modules from the factory to PVEL or other Kiwa Group labs for assessment. This can also be performed via third party oversight in the manufacturer’s in-factory lab.
- Verify Performance. Kiwa recommends on-site testing for large and utility-scale solar projects. Testing PV modules upon delivery to the project site and prior to system commissioning helps identify damage that has occurred during transportation or installation. When performance or reliability issues arise in the field, PVEL and the Kiwa Group are available to diagnose problems and provide guidance for remediation.
Working together to ensure a strong solar future
The solar provisions in the IRA could bring massive benefits to the U.S. industry, transforming the manufacturing landscape in the country and rapidly creating new jobs. But as the industry moves to quickly expand and change the PV module supply chain in the United States, proper due diligence must be conducted to ensure that quality and reliability are maintained. Years of PVEL’s lab data show that small differences to materials and components could have huge impacts on project economics. Manufacturers have a remarkable opportunity to expand production in the United States, and developers in the country can source domestic products. However, regardless of their source, buyers need to take caution that not all PV modules are the same.
Module buyers can help to mitigate overall project risks by following best practices during procurement, including reviewing third-party reports and specifying BOM combinations. For manufacturers in an increasingly competitive market, submitting modules for third-party testing can help differentiate products and increase customer confidence. And when working together to continuously prepare for, review, and address issues in module performance both during production and operation, we can help ensure that the billions of dollars invested in our industry creates a strong solar future that benefits all.
Author
Tristan Erion-Lorico has over 15 years of solar and electrical industry experience that spans manufacturing, testing, project development and operations and maintenance. As vice president of sales and marketing at PV Evolution Labs (PVEL), Tristan oversees PVEL’s commercial activities including collaborating with PV module buyers, investors and manufacturers to develop innovative test programmes for product qualification. |