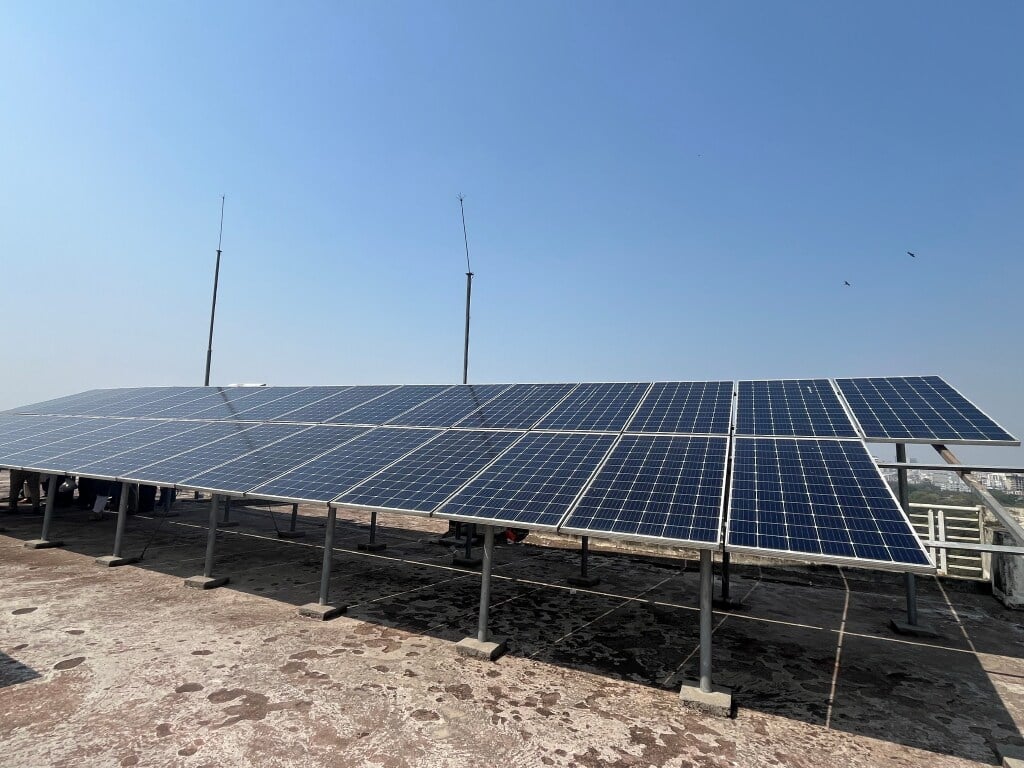
The US Department of Energy’s (DOE’s) National Renewable Energy Laboratory (NREL) has published a report into the use of laser welding processes in solar module production, which researchers suggest could make the panels easier to recycle.
The report, ‘Towards Polymer-Free, Femto-Second Laser-Welder Glass/Glass Solar Modules,’ discusses the potential of femtosecond lasers, lasers emitted in short, sharp bursts over the duration of a fraction of a second, for module manufacturing. These laser pulses can be used to weld glass components of solar panels together, eliminating the need for plastic polymer sheets, which are currently widely used to connect glass components.
Unlock unlimited access for 12 whole months of distinctive global analysis
Photovoltaics International is now included.
- Regular insight and analysis of the industry’s biggest developments
- In-depth interviews with the industry’s leading figures
- Unlimited digital access to the PV Tech Power journal catalogue
- Unlimited digital access to the Photovoltaics International journal catalogue
- Access to more than 1,000 technical papers
- Discounts on Solar Media’s portfolio of events, in-person and virtual
These plastic polymers are a potential barrier to panel recycling, as they must be treated differently to the module’s glass components. A panel made without such polymers can be shattered, and the glass and metal wires within easily collected and reused in other modules, improving the efficiency of the recycling process.
While the removal of such polymers could weaken the structural integrity of modules made in this way, the NREL researchers are confident that this should not discourage interest in femtosecond laser technology.
“As long as the glass doesn’t break, the weld is not going to break,” said David Young, senior scientist and group manager for the High-Efficiency Crystalline Photovoltaics group in the Chemistry and Nanoscience department at NREL, and lead author of the paper.
“However, not having the polymers between the sheets of glass requires welded modules to be much stiffer,” added Young. “Our paper showed that with proper mounting and a modification to the embossed features of the rolled glass, a welded module can be made stiff enough to pass static load testing.”
The research was completed through the Durable Module Materials Consortium, a subsidiary of the DOE that is led by NREL, and funded by the department’s Solar Energy Technologies Office.
Significantly for the solar manufacturing sector, which experiences a rapid rate of change in both the cell and module spaces, the NREL suggests that the laser welding process could be used on any kind of solar technology, including silicon, cadmium telluride (CdTe) and perovskites, as the laser focus used is only a few millimetres away from where the weld will take place.
The research into recycling is part of a growing wave of interest in minimsing the carbon footprint of solar equipment production. Earlier this year, JinkoSolar unveiled a new range of modules, the Tiger Neo Green tunnel oxide passivated contact (TOPCon) series, which it claims to produce using entirely renewable energy.