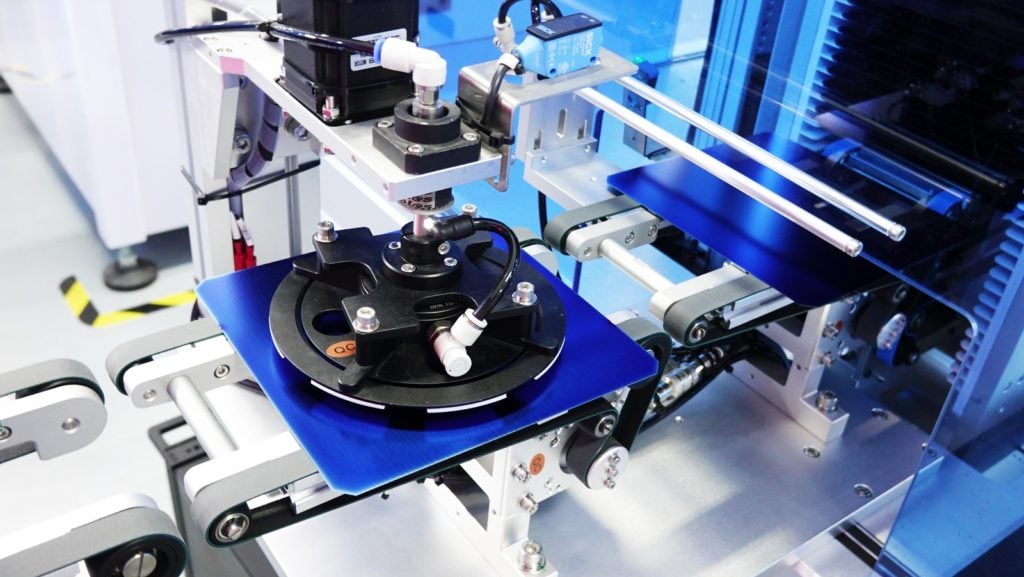
Abstract
TOPCon (tunnel oxide passivated contact) technology will be the next big thing from 2024 on. By the end of 2023, PV production capacity will exceed 450GW, putting this technology in first place in terms of market share in the following years. All TOPCon cells are equipped with passivating contact on the rear and most of them with selective emitters on front, which increase the voltage to above 720mV and enable cell efficiencies in production of over 24.5%. The next step in cell development is the implementation of passivating contacts for the p+ polarity.
There are two options for this: 1) transition to selective polysilicon (poly-Si) on the front side or 2) a direct transition to TOPCon back contact (TBC) structure. We will show that the second option is advantageous for several reasons. In general, a non-metallised front side offers the best option for highest possible efficiencies, and metallisation and interconnection on the backside is very simple. Therefore, we expect TBC to capture the market from 2028 onwards. Some powerful modules were already displayed at SNEC and Intersolar 2023.
Unlock unlimited access for 12 whole months of distinctive global analysis
Photovoltaics International is now included.
- Regular insight and analysis of the industry’s biggest developments
- In-depth interviews with the industry’s leading figures
- Unlimited digital access to the PV Tech Power journal catalogue
- Unlimited digital access to the Photovoltaics International journal catalogue
- Access to more than 1,000 technical papers
- Discounts on Solar Media’s portfolio of events, in-person and virtual
1. Introduction
The n-type crystalline silicon (c-Si) technology is on the rise. We started organising nPV workshops (http://2023.npv-workshop.com/previous-workshops/) in Konstanz in 2011, when low-cost bifacial n-type technology, such as n-type passivated emitter rear totally diffused (nPERT), became an alternative to the then dominant aluminium-backed surface field cell (Al-BSF) technology. However, bifacial passivated emitter and rear contact (PERC) won the competition soon after and became the dominant technology as of 2018, with solar cell efficiencies well above 22%. In 2020, PERC became the ‘king of the energy markets’ and as wafer sizes increased from M2 to M6 and now M10, bifacial PV systems reached levelised cost of energy (LCOE) of down to about 1USct/kWh [1]. In 2023, PERC cell efficiencies reached their limits at 23.5% and module efficiencies at less than 22%. This is the opportunity for n-type technologies like TOPCon, silicon heterojunctions (SHJ) and interdigitated back contact (IBC) to become the next big thing, and that is exactly what is happening now.

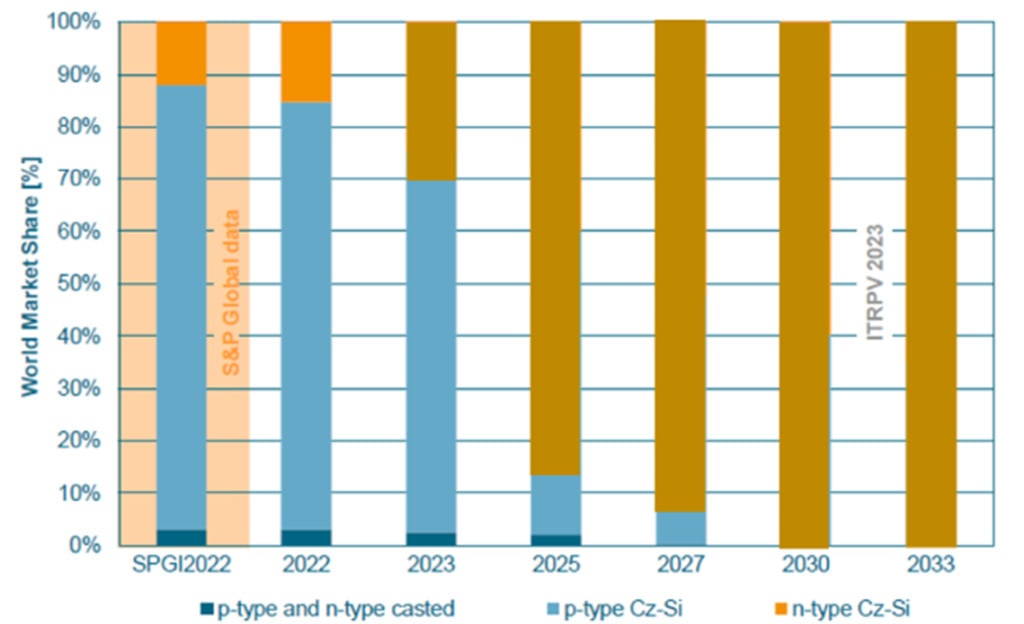
Fig. 1 on the top shows the current market share of n-type versus p-type technologies from the International Technology Roadmap for Photovoltaic (ITRPV) 2023 and its forecast until 2033. The roadmap indicates that in 2033 – i.e. in ten years – the market share of n-type technologies will increase to 70%. However, this is a very conservative forecast.
On the bottom in Fig. 1, we have aligned the graph with PV Infolink’s forecast [2] that 70% market share will be reached as early as next year, 2024, as 450GW of TOPCon, 50GW of HJT (heterojunction technology) and 40GW of IBC/TBC capacity [2] will have been built by the end of 2023. Latest rumours from China say that machines for 1TW TOPCon cell production capacity have been built already. The switch from PERC to n-type technology, especially TOPCon, will happen as fast as the switch from Al-BSF to PERC.
Fig. 2 shows how the n-type switch will proceed. Many innovators have already introduced n-type technologies before 2018, e.g. SANYO, Sunpower, LG Electronics and Yingli.
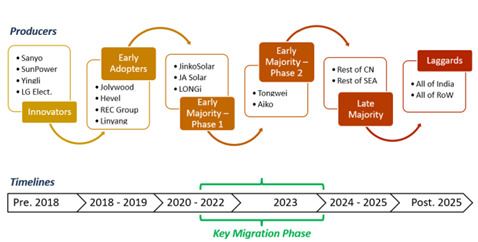
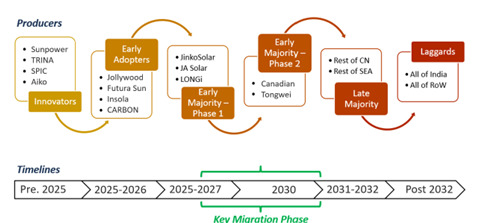
The graph in Fig. 2 is from the PV CellTech Conference 2023 in Berlin by Finlay Colville. It leaves out the innovators of low-cost bifacial n-type technologies before 2018 such as PVGS, sunpreme, MegaCell, TRINA and Adani though. Then followed the early adopters such as Jolywood, Hevel, REC Group and Linyang. However, the decisive phase of the migration began with the adoption of TOPCon technology by the first large Tier 1 manufacturers such as Jinko, JA Solar and LONGi. Today, Aiko and Tongwei are also going the n-type route, and the rest of China and later India will follow.
This proceeds in a similar fashion as the switch to PERC . It can be expected that TBC will follow the same route. Fig. 2 b) shows how we predict TBC will penetrate the PV market. Today, before 2025, we have innovators like sunpower, TRINA, SPIC, Aiko and ValoeCell. Later, early adopters like Jolywood, Futura Sun, Insola and CARBON will follow. And yet again, the big Tier1 manufacturers will take over and TBC will dominate the PV market from 2028. A very simple repeat of PV history to increase the cell voltage from TOPCon’s 725mV to the practical maximum of 740mV.
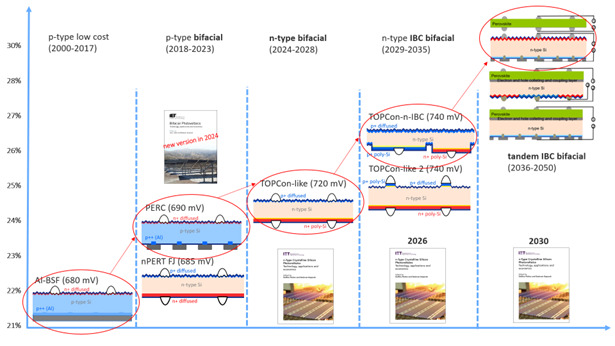
Finally, Fig. 3 describes 30 years of PV evolution of cell technology from 2000 to 2030. The modern era of PV started with the feed-in tariff in Germany around 2000 with a very simple Al-BSF structure and homogeneous emitters passivated by SiNx and screen-printed metallisation contacting emitters with a sheet resistance of about 50 Ohm/sq. That was also the time when polycrystalline silicon (mc-Si) dominated the PV market on substrate areas of 10×10 cm2 followed by 12.5×12.5 cm2 and finally 15.6×15.6 cm2, which then stayed standard for quite a long time.
In 2011, when we started the nPV workshop in Konstanz, more advanced, low-cost n-type concepts such as nPERT from Yingli, PVGS and BOSCH Solar and later from MegaCell, Adani and REC entered the market – mainly because of bifacial applications that gained interest.
However, from 2018 onwards, when p-type Al-BSF tech hit its 21% efficiency limit and LONGi launched low-cost p-type Cz-Si wafers, bifacial PERC technology gained momentum and took over market dominance – pushing Al-BSF and also mc-Si technology out of the market completely. nPERT concepts also lost market share, as they now had to be compared with PERC and no longer with Al-BSF.
However, starting with TRINA, REC, Jolywood, Sunpreme and others, TOPCon and SHJ gained momentum only a little later. However, the switch to n-type was also delayed with the introduction of ever larger substrates, as this trick was used by the powerful PERC manufacturers such as LONGi, Canadian Solar, JA Solar, Jinko and others to lower production costs (increase throughput) and displace smaller n-type manufacturers who could not follow the trend towards larger wafers like M10 (semi square 18.2×18.2 cm2) and G12 (full square 21.0×21.0 cm2). However, the real interest in TOPCon started when, as mentioned above, the first major Tier 1 manufacturer Jinko announced its big plans to switch to TOPCon as PERC was coming from 2021 on to its efficiency limits (at open circuit voltage Voc of about 695mV).
In 2023, TOPCon will grow to about 450GW, 50GW of HJT and 40GW of IBC/TBC production capacity [2]. The key distinguishing step from PERC in TOPCon is the passivating rear-side deposition technology, which is going through a race for the most promising, i.e. cost competitive, approach. The switch from low pressure chemical vapor deposition to plasma enhanced chemical vapour deposition and physical vapour deposition is also happening very quickly in poly-Si depositions.
This is another reason why TOPCon will be unbeatable in the coming years and will keep HJT – the other “emerging” n-type technology – at a low production level, as HJT now will be compared to TOPCon and not PERC. A future logical step will be an “upgrade” from TOPCon to TBC, because to reach voltages of about 740 mV, carrier-selective contacts (passivating contacts) must also be implemented for the p+ polarity.
Since the absorption of poly-Si layers is too high for full area front side application, this is easier to be realised on the rear side. The necessity to align the localised passivating structures with superfine line printing as common on the front side of state-of-the-art solar cells is very much eased, when placing it on the rear side of the solar cell in an alternating fashion. An additional and very important argument for the success of TBC is the easier implementation of alternative screen-printed contacts such as Cu or Al on the backside, which is described in section 4.
Bifacial TBC with Cu or Al screen-printing will, in our opinion, become mainstream from 2028. In parallel, the PV community is developing tandem technologies for all n-type c-Si cell concepts as the bottom cell. To the best of our knowledge, a four-terminal tandem with perovskite on top and a low-cost bifacial Cu or Al screen-printed TBC cell is the most suitable candidate to enter the market after 2030. However, the stability, homogeneity and many other properties of perovskites still need to be drastically improved here.
Fig. 3 also shows the books published by the workshop consortia during the years of transitions in PV technology. In 2018, we published a bifiPV book [3], which is now being rewritten for 2024. This year, 2023, we published the n-type book [4] in March. In the following years, probably 2026, we will publish a book on back-contact PV, followed by TandenPV in 2030 or even before.
2. IBC technology on the PV market
There are several IBC concepts on the PV market. Every both sided concept has its own IBC technology counterpart – such as PERC, nPERT, TOPCon and SHJ. In the following we will leave SHJ out as only the first three ones are currently coexisting in the PV market. In addition, the SHJ IBC developments from Meyer Burger and others also rather go in the direction of TBC as it is much more complicated to include a-Si layers in an IBC structure.
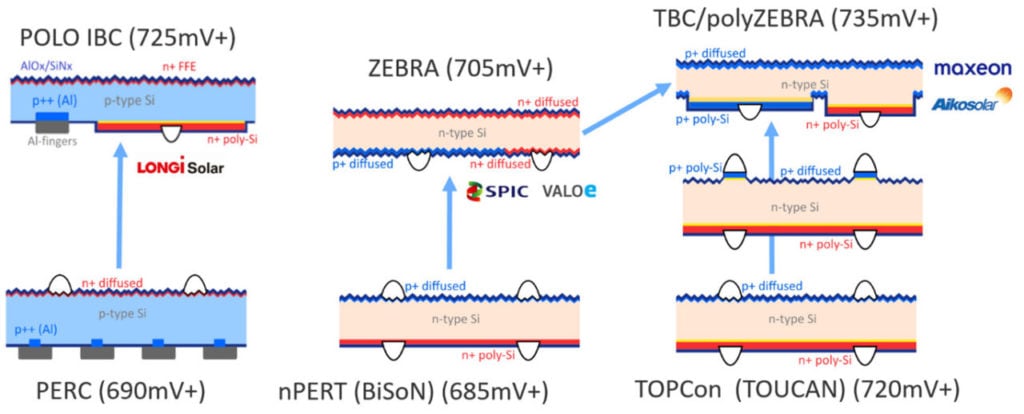
Fig. 4 shows these three concepts and the corresponding IBC/TBC structures. LONGi produces the so-called POLO IBC with Al and Ag screen printing contacts. This technology is limited to a open-circuit voltage of about 725 mV. SPIC and Valoe Cell currently produce the ZEBRA technology, which was developed by ISC Konstanz as an upgrade of the nPERT (BiSoN) technology. To our knowledge, ZEBRA technology is the only technology that uses POCl3 and BBr3 diffusion residues (PSG and BSG) as a passivation layer, eliminating the need for AlOx passivation. Furthermore, it is the solar cell with standard diffusion (without carrier selective contacts) that has the highest open-circuit voltage of up to 705mV.
On the far right of Fig. 4, you can see the evolution from TOPCon to TBC, which has so far been produced by Maxeon and Aiko using electroplating or other method as screen printing though. We are sure that this technology will be the next big thing after TOPCon, but with Cu and Al screen printing technology. We are currently working on further developing our ZEBRA technology by merging it with our TOPCon (TOUCAN) technology to TBC. SPIC and FuturaSun will be the first ones to implement it from 2024 on.
Fig. 5 shows the three IBC technologies currently coexisting in the PV market in a different order from left to right: IBC without a passivating contact (0PC, of 705mV from SPIC and ValoeCell), with a passivating contact of n+ (1PC, of 720mV from LONGi) and with both passivating contacts n+ and p+ – the so-called TOPCon Back Contact (TBC, of 735mV from Maxeon and AIKO).
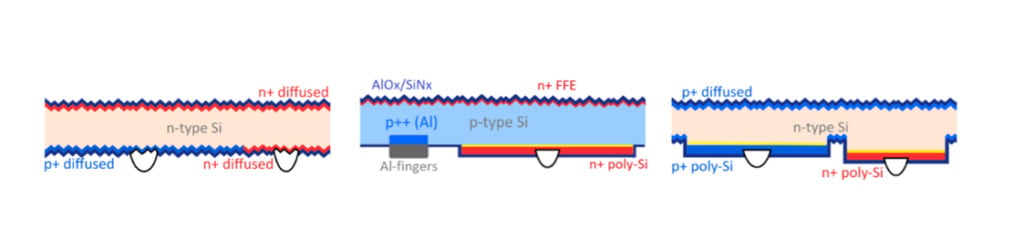
The first concept, called ZEBRA technology [5, 6, 7], is manufactured by SPIC at 250 MW M6 solar cell size and by Valoe Cell at 80MW G1 solar cell size. SPIC manufactures the only bifacial IBC modules (ANDROMEDA 2.0) shown in Fig. 11. The second 1PC POLO-IBC concept is produced by LONGi in a factory with 30 GW capacity and the TBC (2 PC) is produced by Maxeon with 0.6 GW and AIKO (the so-called ABC) with 0.5 GW, with plans to expand to 6.5 GW. FuturaSun plans to produce the polyZEBRA cell (TBC) with 1GW in China, which was announced at Intersolar 2023 in Munich, and SPIC has non-confirmed plans to produce TBC from 2025 on.
Table 1 show the properties of all IBC solar cell and module technologies on the market- or on case of ipv Stuttgart in development.
IBC without passivating contact (0PC) | POLO IBC (1PC) | TBC (2PC) | |||||
Company/Institute | SPIC/ISC | ipv Stuttgart | Jolywood | LONGi | Maxeon | AIKO | TRINA |
Brand-name | ZEBRA/Andromeda2.0 | MESA | – | POLO IBC | Maxeon 6 | Black Hole | – |
Type | n-type | n-type | n-type | p-type | n-type | n-type | n-type |
In production | Yes | No | Yes | No | Yes | Yes | No |
Efficiency | 24.6% [7] | 23.3% [8, 9] | 23-24% | 25% [10] | 25.5% [11] | 25.5% [12] | 25.04% [13] |
PERC Related | 80% | 75% | 70% | 90% | 0% (plated) | 10% (plated) | 10% (plated) |
Module efficiency | 22.3% [14] can be bifacial | Unknown | Unknown | 23.0% [14] | 22.8% [14] | 23.6% [14] | Unknown |
The ZEBRA solar cells have a maximum efficiency of 24.6 % in production and are thus the most efficient solar cells without charge carrier selective contact. The laser processing-based technology from ipv Stuttgart is at 23.3% and the IBC from Jolywood also reached efficiencies between 23-24%. The advantage of the 0PC IBC over the 2PC technology is that the process is very close to the PERC process. However, this technology is limited to 705mV, which is why 1PC and 2PC IBCs are becoming more and more important. LONGi’s cell is between 24-25% with a voltage limitation of 725 mV. The advantage of LONGi’s concept is that it is even closer to the PERC process with p-type Cz-Si wafers and Al screen metallisation.
However even being closer to PERC it is not easier to process compared to 0PC technology, and in addition the interconnection is relatively complicated, as Al-structures cannot be connected via soldering or gluing so easily. The future belongs therefore to the 2PC TBC technologies currently produced from Maxeon and AIKO only, which achieve efficiencies of over 25% at voltages close to 740mV. However, the metallisation is currently still believed to be done by electroplating (or at least no screen printing), which, as far as we know, will not be successful in the future for various reasons. Therefore, ISC Konstanz is first working on advanced Cu and Al screen-print metallisation for ZEBRA, which will then be transferred to TBC (polyZEBRA) in 2024.
The bottom row in Table 1 shows the corresponding module technologies on the PV market (when available) with 22.3% for SPIC’s ANDROMEDA 2.0, 23.0% for LONGI’s POLO IBC and 22.8% for Maxeon and 23.5% for AIKO’s Black Hole technology. The p-type POLO IBC from LONGi was, however, not displayed at Intersolar 2023 anymore and we expect the production to be shut down as there are many challenges concerning the material and the solar cell process itself. Therefore, TBC will be the only future back contact technology.
Fig. 6 shows the most efficient modules on the PV market in Q3 2023, all based on n-type technologies (with the exception of LONGi’s technology) – the TBC technology is among the top 4.
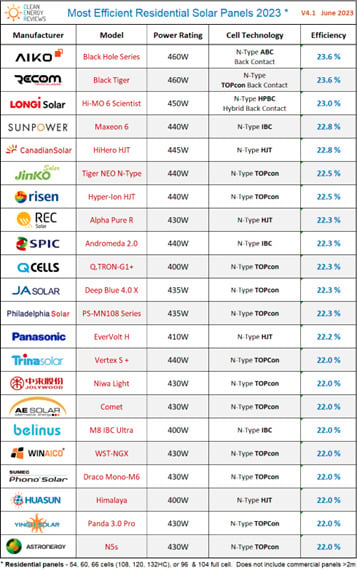
To our knowledge, the Black Tiger module from Recom is an OEM product from Aiko. We are convinced that in the next 4 years the first 10-15 places will be occupied by TBC technologies, which we expect to take the highest market share replacing TOPCon from 2028 onwards. Fig. 7 shows in a very simple way why.
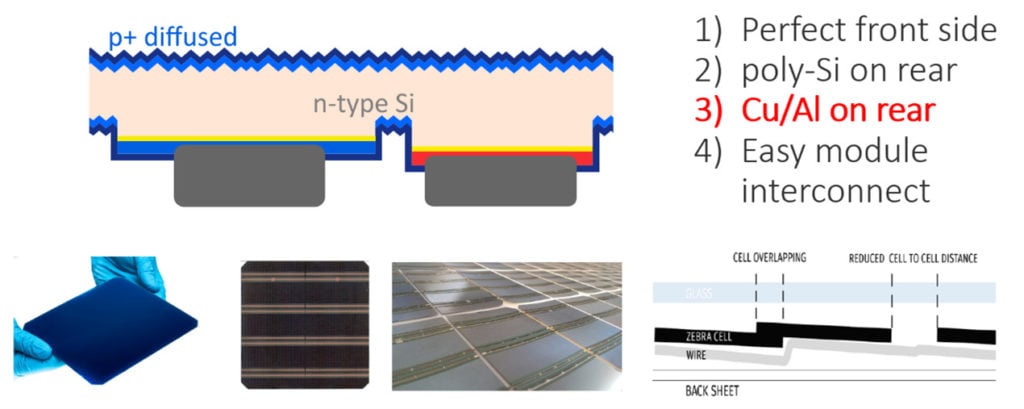
The arguments for this are again very simple: with TBC, the solar cell has a perfect front side without the need for selective poly-Si structures and metallisation on the front side. The processes on the back side contacting in a much simpler way. It allows for the use of Cu screen printing or even Al screen printing, which would not be possible on the front side without losing power due to shading effects. In addition, connecting the cells together is extremely easy, using standard stringing, in particular with 3D-interconnection patterns or conductive adhesives in the stringing process, or conductive backsheet technology. Shingling is also possible. At the moment, we prefer standard stringing with negative gap technology shown at the very right bottom of Fig. 7, to achieve highest bifaciality.
This inherent advantage of delivering a large degree of freedom concerning the metallization on the rear side makes TBC the most suited technology to allow for an annual 1TW PV market which is expected from 2027 onwards. For this alternative metallisation need to be used, which should be easily applied by screen printing on the rear side. How we believe this can happen and it will be covered in the next sections.
3. Standard ZEBRA IBC technology
As already mentioned, the standard ZEBRA solar cell is manufactured by SPIC in Xining, China, and by Valoe Cell in Vilnius, Lithuania [15, 16]. To our knowledge, it is the standard diffused solar cell technology with the highest open-circuit voltage of up to 705mV. This is due to our proprietary advanced screen printing technology, where only 1.5% of the emitter surface comes into contact with the silver contact points. The rest of the fingers and busbars float on the SiNx anti reflective coating, as shown in Fig. 8 and especially also in Fig. 13.
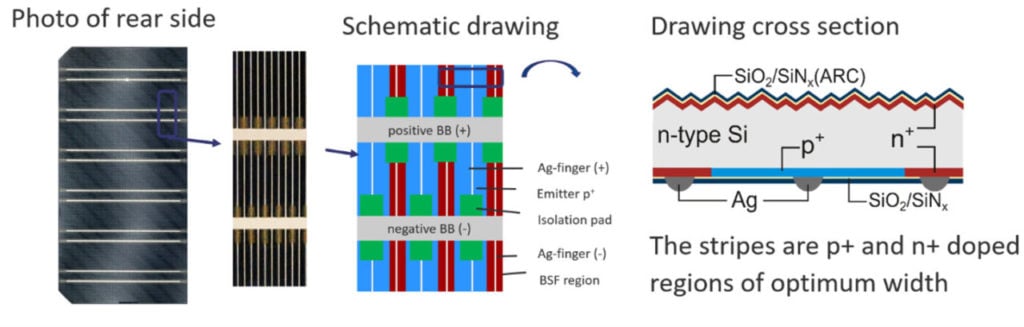
Fig. 8 shows the back of an M6 ZEBRA cell with 6 busbars on the left, a picture and schematic metallisation drawing in the middle and a cross-section of the cell on the far right. Every second finger is covered by an isolation paste underneath the positive and negative busbars, creating a 3D screen printed metallisation layout.
The process flows of the n-type technologies compared to a PERC process flow are shown in Fig. 9. Since the ZEBRA IBC technology is based on PERC and TOPCon, it also has a very lean process flow.
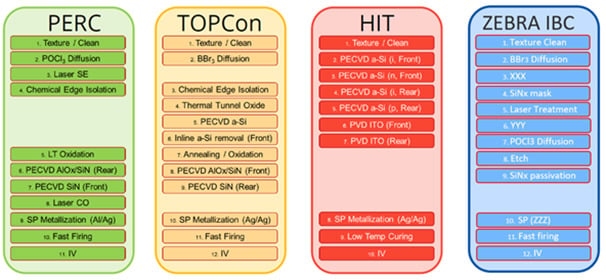
The heterojunction with intrinsic thin layer (HIT) sequence looks simple, but the complexity of a process is only one feature. Throughput and yield are two other very important parameters that make classical technologies like PERC, TOPCon and ZEBRA IBC unbeatable in terms of operating costs. The results of mass production of ZEBRA IBC technology at SPIC in Xining in China are shown in Fig. 10, as well as a summary of the parameters in Table 1.
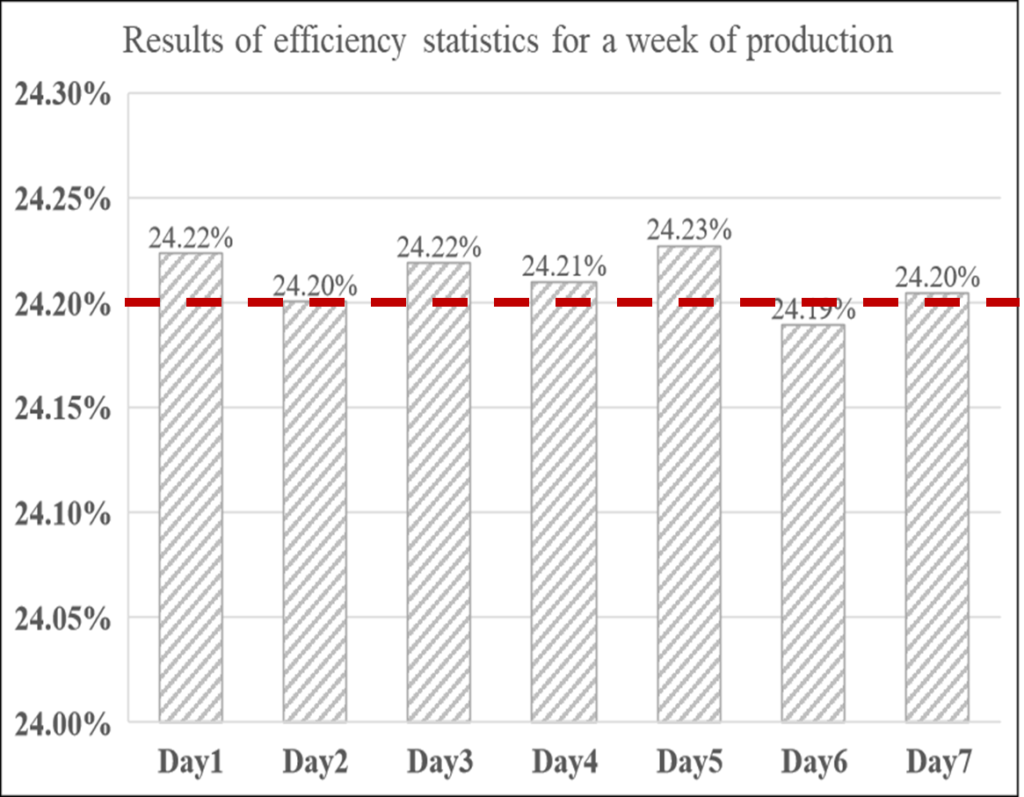
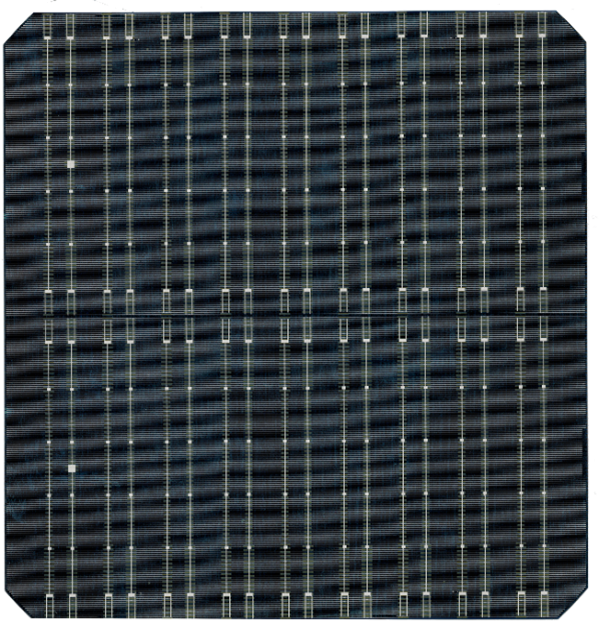
Cells | Voc/V | Isc/A | FF/% | eta/% |
Best | 0.704 | 11.9 | 80.6 | 24.6 |
Average | 0.700 | 11.8 | 80.2 | 24.2 |
The M6 ZEBRA IBC solar cells with nine busbars are produced with an average efficiency of 24.2% at an average open-circuit voltage of 700mV and a maximum efficiency of 24.6% at an open-circuit voltage of up to 704mV. The Ag content of the cell is 20mg/WP, which has a big potential for improvement and will be discussed in the following paragraph. The ZEBRA IBC technology can be soldered in a way which is similar to standard solar cells, and is, therefore, also suitable as a low-cost product at module level. Fig. 11 shows the backsides of all bifacial modules in the PV sector, making ZEBRA IBC the only bifacial IBC technology with a bifacial factor comparable to PERC modules.
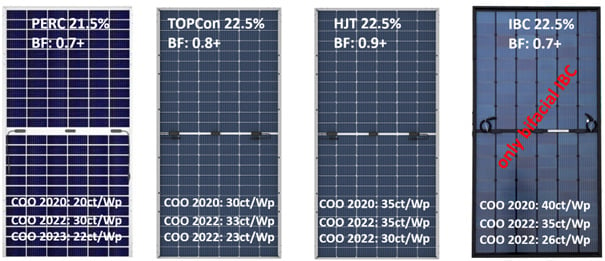
As costs of ownership (COOs) are currently changing a lot due to fluctuating Si and Ag prices, the relative difference between the technologies is more interesting than the absolute values. It is worth noting that the COO of PERC and TOPCon are currently at the same level (at SNEC 2023, some TOPCon modules offered as low as US$0.17/Wp) and the COO of ZEBRA IBC is not much higher. Higher efficiencies and the introduction of low-cost Cu metallisation will make bifacial Cu ZEBRA unbeatable in the future.
4. Beyond standard ZEBRA IBC technology
As mentioned earlier, the Ag consumption for ZEBRA IBC is at around 20mg/Wp and thus it is far too high to bring this technology to the PV market with much impact. On the other hand, IBC technology is the most suitable technology to implement Cu and/or Al metallisation and is discussed below. Fig. 12 shows how such replacement of Ag by Cu works for busbars only (top) and also for fingers (bottom).
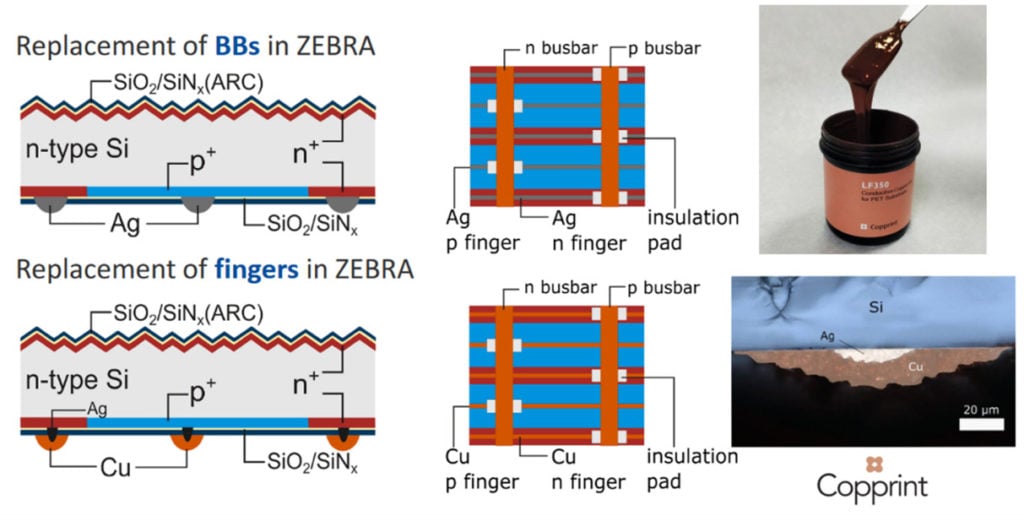
The lower cross-sections and the microscope image show the metallisation concept very clearly. The Ag-silver contacts have three main tasks in the metallization. They fire through the SiNx, make contact with the emitter and the base, and prevent the Cu particles from in-diffusing into the silicon. Therefore, only 4mg/Wp Ag is needed to achieve the same efficiency as the ZEBRA IBC cell printed entirely with Ag (see Fig. 13) [16]. Since these are the results from research and development at the ISC Konstanz, the efficiencies in this case are lower than in mass production at SPIC. However, it can be clearly seen that the solar cell parameters are the same in the case of Cu metallisation compared to the reference and still slightly lower in the case of Al metallisation.
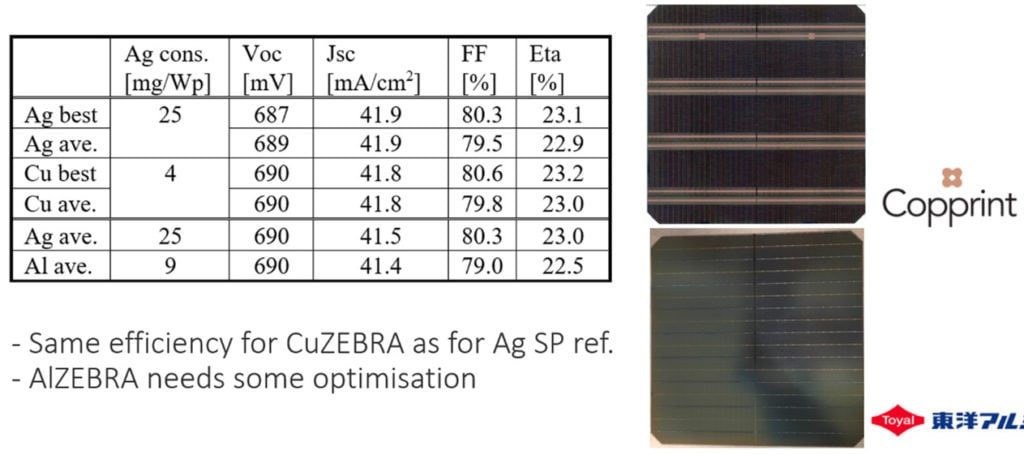
Extensive tests with the hot plate method, temperature cycling as well as damp heat and tensile tests were successful [17], so that our Cu-ZEBRA technology is expected to be transferred to mass production in the coming years.
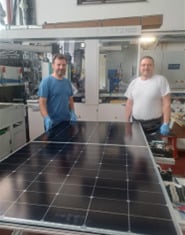
The polyZEBRA concept is designed to work as an upgrade of standard ZEBRA manufacturing and it features an identical back-end [19,20] and will accordingly profit from the development, yielding even higher efficiencies with similarly low COO. More details on this will follow in the last section.
5. The polyZEBRA (TBC) concept
As already discussed, the ZEBRA concept is very simple and extremely robust in production, however, limited to 705mV. In order to reach the practical short circuit voltage limit of about 740mV, the TBC (polyZEBRA) concept has to be used, where both polarities are using passivating contacts. LONGi is going an intermediate step with one passivated polarity only, but information at Intersolar 2023 indicate that they will stop the production of their POLO-IBC, because of the competition with much simpler TOPCon already reaching 720mV+ as well.
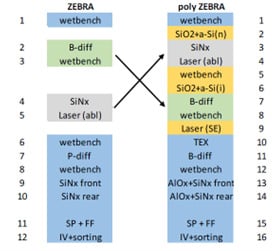
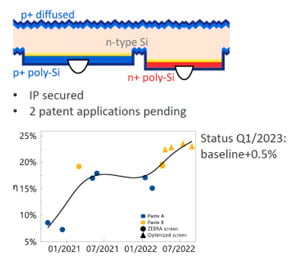
Fig. 15 shows one of our processes for polyZEBRA (TBC) in comparison to ZEBRA (IBC), its cross section and efficiency improvement. The polyZEBRA cell will be transferred to Futura Suns’ 1GW production in 2024. As the major patents of sunpower are running out in two years, the TBC technology will have even more freedom in future. This is why we believe that the next logical step from TOPCon will be bifacial Cu metallised TBC. In the following we will discuss the costs of the modules and of the electricity from the PV systems.
6. COO and LCOE
We have shown that TOPCon will be the future trend after PERC in 2024, replacing PERC, which will already have a 70% market share in 2024. Shortly thereafter, bifacial screen-printed Cu and/or Al TBC technology will take the lead as the next logical evolutionary step in PV development. IBC technology is currently used in a wide range of applications, from product-integrated photovoltaics, building-integrated photovoltaics and vehicle-integrated photovoltaics, to industrial scale bifacial mode test systems. Fig. 16 shows such applications from SPIC, ISC Konstanz and Valoe Cell.
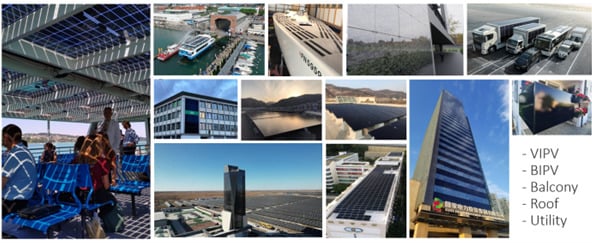
To make TBC the next big thing though, we need to increase efficiency, lower the costs and make the modules bifacial. In summary, all that was necessary for PERC to replace Al-BSF and TOPCon to replace PERC later on. To this end, we are working within the EU project IBC4EU [18] to bring TBC technology to production maturity in the EU, and for utility-scale applications. Fig. 17 and Fig. 18 show how this can be achieved.
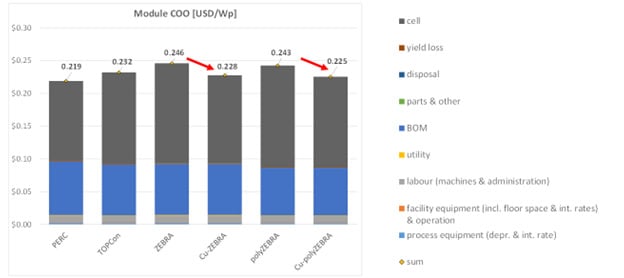
Fig. 16 shows the COO for PERC, TOPCon and IBC (ZEBRA)/TBC (polyZEBRA) modules with different metallization approaches. It shows that TOPCon is already very close to PERC, but has a higher efficiency, higher bifaciality and lower degradation, which is why it already shows advantages at utility scale (see Fig. 17). ZEBRA and polyZEBRA are still more expensive, but with future efficiency improvements and the switch from Ag to Cu and/or Al, this will lead to bifacial Cu polyZEBRA being the Holy Grail from 2027 onwards.
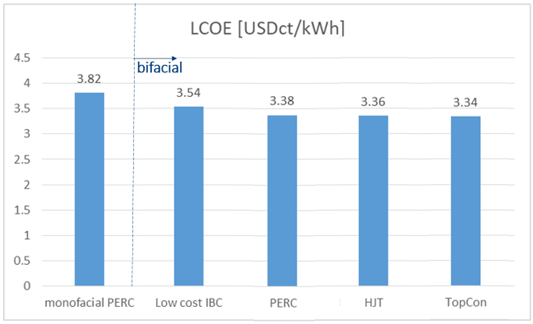
7. Summary and conclusion
We have shown that TOPCon will be the next big thing after PERC in 2024, replacing PERC, which already will have a 70% market share at that time. The next logical step is to switch to TBC which we expect about four years later, from around 2028, due to the higher efficiency potential (with open-circuit voltages of 740mV) and the advantage of possible replacement of Ag with low-cost materials such as Cu or Al. With both, the Ag content can be reduced down to 4 mg/Wp Ag in these new cell concepts. We will push ahead with the industrialisation of our Cu and Al ZEBRA and polyZEBRA IBCs in the coming years.
This is done within the EU project IBC4EU [19] and also in industrial projects with many partners such as SPIC, Valoe Cell, Futurasun, Insola, Carbon, SolarNord and others. The results of our and other consortia’s developments will be discussed at the upcoming Back Contact Workshop on 29-30 November 2023 in Hamelin [20]. On 23 June 2023, the German government’s expression of interest was published [21], looking for companies to build a total PV production landscape of 10GW in Germany in the first phase.
The technical requirements in this tender fit very well with the bifacial Cu screen-printed TBC technology. The German government is looking for future technologies that achieve 24% module efficiency, solderless connections and reduction of critical material. We are sure that TBC technology will play a very important role in restoring PV production in the EU and the US.
Authors
Radovan Kopecek, Florian Buchholz, Valentin D. Mihailetchi, Joris Libal, Ning Chen, Haifeng Chu, Christoph Peter, Dominik Rudolph, Razvan Roescu, Pirmin Preis, Lejo J. Koduvelikulathu Tom Kollek, Thomas Buck, Jan Lossen, Tudor Timofte and Andreas Halm.
International Solar Energy Research Center Konstanz, Rudolf Diesel Strasse 15, 78467 Konstanz, Germany.
References
[1] Lowest bid in Saudi Arabia: https://www.pv-tech.org/saudi-arabia-solar-tariffs-jump-43-on-higher-module-costs/
[2] PV Infolink: https://www.infolink-group.com/
[3] Libal J.; Kopecek R.; Bifacial Photovoltaics: Technology, applications and economics, Institution of Engineering and Technology, 2018
[4] Muñoz D.; Kopecek R.; N-Type Crystalline Silicon Photovoltaics: Technology, Applications and Economics, Institution of Engineering and Technology, 2023
[5] Kopecek, R., Libal, J.; Lossen, J., Mihailetchi, V.D., Chu, H., Peter, C., Buchholz, F., Wefringhaus, E.; Halm, A., Ma, J., et al. ZEBRA technology, Low cost bifacial IBC solar cells in mass production with efficiency exceeding 23.5%. In Proceedings of the 47th IEEE Photovoltaic Specialists Conference (PVSC). IEEE, Calgary, AB, Canada, 15 June–21 August 2020; pp. 1008–1012. https://doi.org/10.1109/PVSC45281.2020.9300503.
[6] Kopecek R.; Libal J.; Mihailetchi V. D.; Buchholz F.; Chu H.; Roescu R.; Lossen J.; Peter Ch.; Halm A.; and Wefringhaus E.; IBC technology: Back contacts move to the front; PVI46, February 2021
[7] Lossen J. et al.; Industrial production of high efficient ZEBRA IBC cells and modules, Back Contact Workshop, Munich 2022 [Online]. Available: https://www.backcontact-workshop.com/pdf/2022-1/9_SPIC.pdf (accessed on October 10 2022).
[8] Dahlinger M.; Carstens K.; Hoffmann E.; Zapf-Gottwick R.; Werner J.H.; 23.2% laser processed back contact solar cell: fabrication, characterization and modeling. Prog. Photovolt: Res. Appl. 2017; 25, pp: 192–200. DOI: 10.1002/pip.2854.
[9] Zapf-Gottwick R. et al.; Solar Cells with Laser Doped Boron Layers from Atmospheric Pressure Chemical Vapor Deposition, Solar 2 (2), 274-292
[10] LONGi´s POLO IBC: https://rethinkresearch.biz/articles/longi-launches-hpbc-type-module-for-distributed-market/
[11] Maxeon´s IBC: https://corp.maxeon.com/static-files/c5e8e15e-b191-4bab-96ff-cec504040019
[12] Aiko´s ABC: https://www.solarbeglobal.com/aikosolar-refreshes-n-type-non-silver-abc-solar-cell-efficiency-by-25-5/
[13] Trina Solar takes n-type mono IBC cell to record 25.04% conversion efficiency [Online]. Available: https://www.pv-tech.org/trina-solar-takes-n-type-mono-ibc-cell-to-record-25-04-conversion-efficienc/ (accessed on October 10 2022).
[14] https://www.cleanenergyreviews.info/blog/most-efficient-solar-panels
[15] Kopecek, R.; Buchholz, F.; Mihailetchi, V.D.; Libal, J.; Lossen, J.; Chen, N.; Chu, H.; Peter, C.; Timofte, T.; Halm, A.; et al. IBC Technology as Final Evolution for Industrial Crystalline Single-Junction Silicon Solar Cell. Solar 2023, 3(1), 1-14. https://doi.org/10.3390/solar3010001
[16] Chen, N., Rudolph, D., Peter, C., Zeman, M., Isabella, O., Rosen, Y., Grouchko, M., Shochet, O., & Mihailetchi, V. D. (2022). Thermal Stable High-Efficiency Copper Screen Printed Back Contact Solar Cells. Solar RRL, 7 (2023)(2), 1-9. [2200874]. https://doi.org/10.1002/solr.202200874
[17] Rudolph, D., Improvement of solder interconnections applied on back contact solar cells with low-T Cu paste busbars, Metallisation WS 2023, https://miworkshop.info/wp-content/uploads/2023/05/4_ZEBRA-Interconnection-d-rudolph.pdf
[18] Cu screen printed 60 cell IBC (ZEBRA module): https://www.linkedin.com/feed/update/urn:li:activity:7080062637908078592/
[19] Linke, J. et al. Fully Passivating Contact IBC Solar Cells Using Laser Processing. Proceedings of the WCPEC 2022, 102- 106
[20] Buchholz, et al. PV, The polyZEBRA concept – upgrade of low cost IBC solar cell production, PV Cell Tech, Berlin, 2023
[19] EU funded project IBC4EU: https://ibc4.eu/
[20] BCworkshop2023 in Hamelin: https://www.backcontact-workshop.com/
[21] Bundesministerium für Wirtschaft und Klimaschutz Bekanntmachung des Interessenbekundungsverfahrens zur geplanten Förderung von Leuchtturmprojekten zum Hochlauf der industriellen Produktionskapazitäten im Bereich Photovoltaik: https://www.bundesanzeiger.de/pub/de/amtliche-veroeffentlichung?6