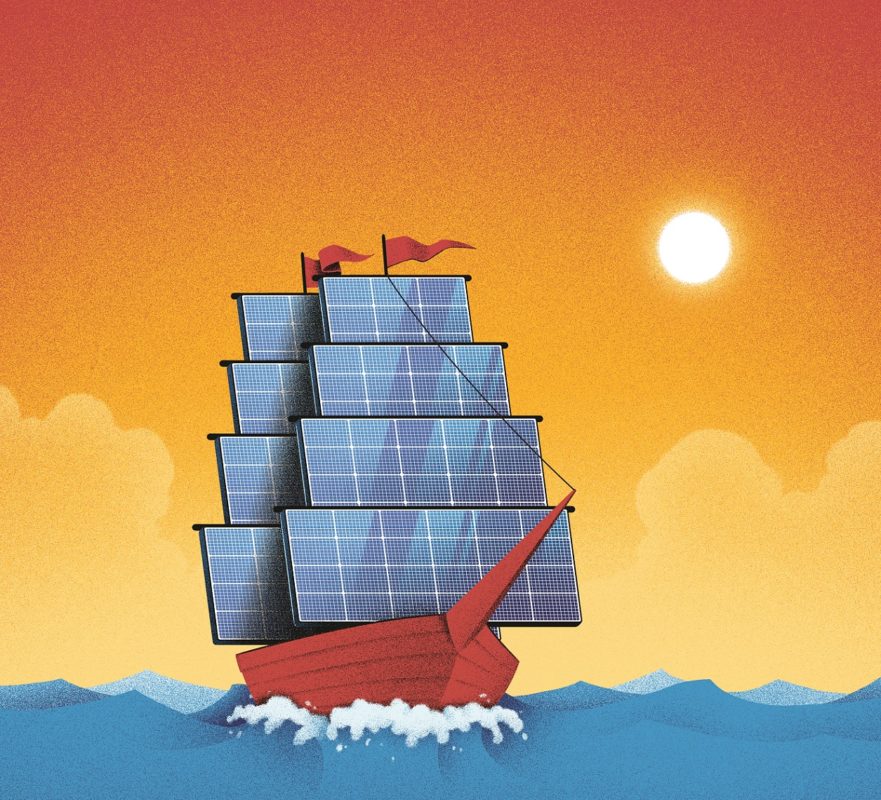
With China strengthening its position in recent years to dominate the PV supply chain, efforts are gathering pace to onshore some manufacturing to end markets as governments aim to support domestic production and reduce their reliance on imports.
China’s share in all key manufacturing stages of solar panels exceeds 80% today, according to a report published last year by the International Energy Agency (IEA). For key elements including polysilicon and wafers, this is set to rise to more than 95% in the coming years, based on publicly announced manufacturing capacity under construction. The research said the solar industry supply chain is one of the most geographically concentrated supply chains globally.
Unlock unlimited access for 12 whole months of distinctive global analysis
Photovoltaics International is now included.
- Regular insight and analysis of the industry’s biggest developments
- In-depth interviews with the industry’s leading figures
- Unlimited digital access to the PV Tech Power journal catalogue
- Unlimited digital access to the Photovoltaics International journal catalogue
- Access to more than 1,000 technical papers
- Discounts on Solar Media’s portfolio of events, in-person and virtual
Heymi Bahar, a senior analyst at the IEA and lead author of the report, tells PV Tech Power that China’s dominance has been achieved through an extensive industrial policy supporting both supply and demand, as the country chose solar as a strategic industry for economic development.
“It’s an important thing to understand why China is the largest producer – because they achieved the economies of scale, they achieved innovation and then thanks to this expansion of solar PV in China, the world enjoyed an 80% cost reduction of solar PV modules. That’s one reality that I think it’s important to acknowledge,” Bahar says.
The second reality, he argues, is that without a solar PV industrial policy, including demand- and supply-side policies and innovation, it will be difficult to bridge the cost gap with China. “I think countries are a little bit waking up to this,” Bahar says.
The importance of scaling up solar manufacturing in the US was highlighted by President Joe Biden, who said in a memo published last June that action to expand the domestic production of PV modules and components “is necessary to avert an industrial resource or critical technology item shortfall that would severely impair national defence capability”.
Why diversify?
Although 38 countries have module assembly facilities, China was still responsible for about 70% of production in 2021, the IEA research revealed. With crystalline silicon cell manufacturing concentrated in the Asia-Pacific, large PV demand centres in the US, India and Europe depend strongly on imports for the main solar module components. The IEA said although these markets often possess multi-gigawatt module production capability, most of the plants simply assemble modules from parts shipped from manufacturers located mainly in mainland China.
China’s dominance in the PV supply chain is perhaps most obvious in terms of wafer production, with the country accounting for 97% of global manufacturing capacity, according to the IEA. It said that Chinese companies were able to become cost-competitive in wafer production relatively quickly, preventing other market participants from attaining significant market shares.
Among the advantages of onshoring some production closer to end markets is securitisation of supply. Increasing local manufacturing capability will go some way to ensuring supply disruptions for local development are minimised, says Sylvia Leyva Martinez, a senior analyst at research firm Wood Mackenzie. “Developing a domestic supply will reduce the reliance on other countries and will shield buyers from any changes in trade policy.”
Martin Meyers, director of market intelligence at solar and storage advisory firm Clean Energy Associates (CEA), argues that the most important benefit for US developers of increasing domestic PV manufacturing would be the significant reduction in supply chain frictions associated with trade and customs requirements, which have significantly impacted developers in recent years. He says a significant additional benefit would be much lower logistics risks, which were experienced by all trans-Pacific shippers in 2021.
As well as creating a greener supply chain by reducing shipping-related emissions, onshoring more manufacturing could also help the industry decarbonise by producing more components in areas with high levels of renewables penetration.
Currently, coal fuels 62% of the electricity used for solar PV manufacturing, significantly more than its share in global power generation (36%), largely because production is concentrated in China – mainly in the provinces of Xinjiang and Jiangsu – according to the IEA. The organisation said reducing the carbon intensity of manufacturing could thus be a prime opportunity for the PV sector to further decrease its carbon footprint.
While some countries are looking to realise these benefits as they earmark more resources to support domestic manufacturing, significant headwinds lie ahead as China continues to increase its market share, benefiting from economies of scale.
“The big challenge is everything boils down to cost differentials,” says Bahar. “Obviously, the cheapest way of producing solar PV panels in the world is in China and some of the countries in Southeast Asia.”
PV manufacturing costs in China are 10% lower than in India, 20% lower than in the US and 35% lower than in Europe, the IEA’s report revealed. It said the key reasons for this include longer construction and development timelines, labour and material costs, the higher cost of capital, a lack of economies of scale and a dearth of know-how in developing mega-scale PV manufacturing facilities.
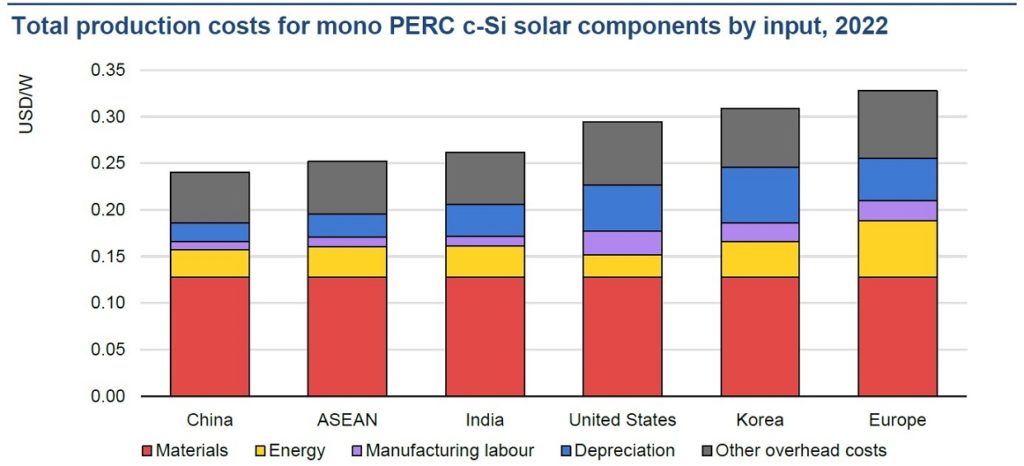
In the absence of subsidies and manufacturing support, achieving significant reductions in energy and labour costs remains challenging, the IEA said, adding that diversifying solar PV manufacturing will depend on the ability of nascent and new markets to match the cost efficiencies in China.
The markets outside East Asia that show the strongest potential for building a domestic solar panel manufacturing industry are the US and India, says Leyva Martinez, while Meyers also puts the European Union (EU) in that category.
IRA drives growth in the US
The significant obstacles facing the US solar sector were revealed in a Department of Energy report published last June, which warned trade and supply chain frictions had resulted in an acute shortage of PV equipment, potentially risking an abrupt slowdown in solar installation rates.
However, owing to the Department of Commerce’s inquiry into alleged circumvention of antidumping and countervailing duties, President Biden announced a two-year freeze on new tariffs on solar imports from Southeast Asia in June. This allowed industry players to kickstart deployment, and more good news was on the horizon.
Following months of speculation and political uncertainty, US lawmakers finally reached a deal last summer to pass legislation that earmarks US$369 billion for decarbonisation efforts, featuring expanded tax credits for utility-scale solar as well as manufacturing credits for a host of PV components.
Adopting a holistic approach and including a suite of policy options focused on long-term demand drivers, the Inflation Reduction Act (IRA) has incentives “that will, over time, lead to a renaissance in American solar manufacturing”, trade association the Solar Energy Industries Association (SEIA) said in a report.
“The IRA is the first true attempt at clean energy industrial policy in US history, and it has transformed the outlook for America’s solar and storage manufacturing sector,” John Smirnow, vice president of market strategy and general counsel for SEIA, tells PV Tech Power. Since the legislation was signed into law by Biden in August, manufacturers in the US have announced more than US$1 billion of investments in clean energy products and inputs such as solar modules, microinverters, trackers and racking.
“The IRA is the first true attempt at clean energy industrial policy in US history, and it has transformed the outlook for America’s solar and storage manufacturing sector”
John Smirnow, vice president of market strategy and general counsel at SEIA
Components eligible for manufacturing tax credits under the legislation include modules, thin-film or crystalline PV cells, wafers, polymeric backsheets, solar-grade polysilicon, inverters and trackers.
According to SEIA, the IRA established two credits for manufacturers: a 30% investment tax credit for eligible investment costs in facilities and equipment as well as a manufacturing production credit for certain components based on the volume of product manufactured. Manufacturers can only seek to take one or the other.
IRA triggers flurry of US solar manufacturing announcements
Since President Joe Biden signed the US’s Inflation Reduction Act into law on 16 August, solar manufacturers have shown their confidence in the legislation by announcing a host of new PV manufacturing facilities in the country.
Enacting the IRA has already resulted in billions of dollars in new solar manufacturing investments, according to trade body the Solar Energy Industries Association. Here are some of the announcements.
- Italian utility Enel is planning to build a new solar cell and module manufacturing facility in the US with an initial capacity of at least 3GW. The factory is intended to produce bifacial heterojunction PV cells, while the modules will have a tandem structure, utilising two stacked cells. Enel said there will be the possibility to scale up production at the facility to 6GW annually.
- Thin-film solar manufacturer First Solar announced in late August will invest up to US$1.2 billion to expand its manufacturing operations in the US, including setting up a vertically integrated factory in Alabama with an annual capacity of 3.5GWdc. The company’s CEO said the IRA “has firmly placed America on the path to a sustainable energy future”.
- Spain-based solar tracking solutions provider PV Hardware is planning to set up a 6GW tracker manufacturing facility in the US state of Texas that is due to be operational by June 2023.
- US microinverter manufacturer Enphase will aim to establish four to six new manufacturing lines in the country by mid-2023, the company revealed in its Q3 2022 results announcement.
- Solar developer SPI Energy plans to build 1.5GW of US wafer manufacturing capacity by 2023 and reach 3GW by 2024.
As a direct result of the IRA, SEIA expects to see significant new investments in domestic solar module, tracker, inverter and racking capacity within the next two to three years, followed by new investments in solar ingot, wafer and cell capacity within three to five years. The trade body said the IRA will be instrumental in ensuring the US solar industry meets a goal of having 50GW of domestic solar manufacturing capacity across all key industry segments by 2030.
“With the proper application and sequencing of the IRA’s incentives, coupled with state-level policies, we believe this law will help us meet or even exceed that goal,” Smirnow says.
Currently, however, the US has no domestic solar ingot, wafer, or cell manufacturing capacity and only modest capacity to produce solar modules.
SEIA has called on US PV manufacturers to consider the timing of demand for their products. For example, it said while module, inverter, mounting system and tracker manufacturers can expect to see immediate demand, it will take time to build demand for segments such as ingots and wafers.
Smirnow says this strategic sequencing helps minimise the chances of stranded assets and maximises the speed, efficiency and cost-effectiveness of building out a full US solar supply chain.
With a deficit of PV cell suppliers compared to market demand, CEA vice president of manufacturing services Mark Hagedorn says: “Choreographed growth in the global and local supply chains throughout the value stream is required to achieve the meteoric growth teed up by the IRA.”
As crystalline silicon cell manufacturing is concentrated in Asia-Pacific, large solar PV demand centres in the US, India and Europe depend strongly on solar module component imports. However, the IEA report said that with some thin-film manufacturing capacity, the US is relatively less dependent on China for supply chain components than other markets.
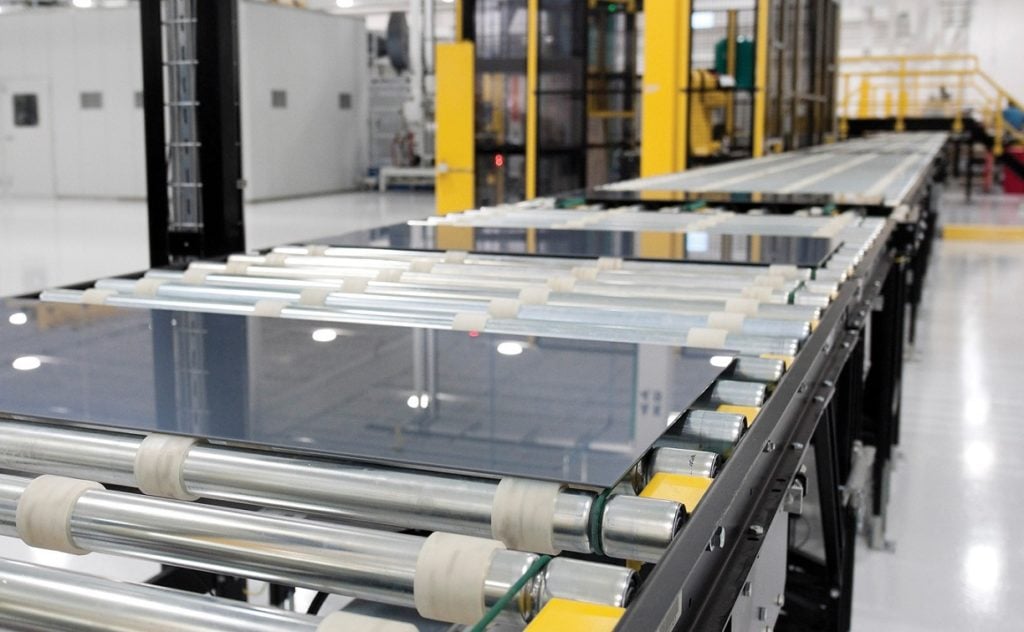
Just two weeks after Biden signed the IRA into law, thin-film solar manufacturer First Solar revealed it will invest up to US$1.2 billion to expand its manufacturing operations in the US, including setting up a vertically integrated factory in the country’s Southeast with an annual capacity of 3.5GWdc. The US-headquartered company plans to invest up to US$1 billion in the new factory – its fourth in the country – which is expected to begin operations in 2025.
“We believe that locating supply close to demand allows us to mitigate numerous risks, not least those posed by an overreliance on transoceanic shipping while enabling competitive pricing and supply reliability for our customers,” says Samantha Sloan, First Solar vice president of global policy, sustainability and marketing.
As well as constructing the new factory in the US Southeast, First Solar is expanding its two operating facilities in Perrysburg and Lake Township, Ohio, by 600MWdc to 3.6GWdc of annual Series 6 module capacity. It will also scale up its third Ohio factory, due to be commissioned in the first half of 2023, to 3.5GWdc of annual Series 7 module capacity. The company is aiming to reach more than 10GWdc of US solar manufacturing capacity by 2025.
In terms of IRA support, First Solar anticipates guidance on the domestic content bonus that project owners may seek under the new production tax credit and extended investment tax credit for solar, Sloan says. She adds that given First Solar’s manufacturing process, which transforms raw materials into a finished module under one roof, the company expects its product to qualify as US domestic content and secure bonus incentives.
Another US thin-film module manufacturer that is ramping up production on the back of the IRA is Ohio-based Toledo Solar, which revealed in September is aims to reach 2.8GW of module capacity by 2027, up from 100MW today.
The federal government’s commitment to renewable energy security has allowed Toledo Solar to commit larger amounts of capital for expansion over the next five to ten years, says the company’s CEO, Aaron Bates. Prior to the IRA, Bates says such investments “were difficult for companies like ours to commit with such an unlevel playing field in imported solar”.
Among the most significant part of the legislation for Toledo Solar is a more than 40% investment tax credit for domestically manufactured PV modules, which “has been a great way for Americans to be incentivised to purchase our modules”, Bates adds.
In addition to ramping up production in the US, First Solar revealed plans in 2021 to construct a 3.3GWdc module assembly facility in India. According to Sloan, the company aims to replicate its US strategy of primarily using domestically made components and materials at the company’s first India factory, due to come online this year.
Duties and incentives in India
As part of government efforts to become more self-reliant, India has doubled down on a strategy of supporting domestic PV manufacturers by implementing duties and financial incentives. The country’s module and cell manufacturing capacities were on track to reach approximately 30GW and 10GW, respectively, by the end of 2022, according to CEA research.
However, a report published earlier last year by consultancy JMK Research & Analytics and think tank the Institute for Energy Economics and Financial Analysis (IEEFA) revealed that India has no manufacturing capacity for the initial stages of the PV value chain, from polysilicon to wafer. It said developing significant manufacturing capacities in raw materials, especially polysilicon, “will be highly capital intensive and technologically complex but it is of paramount necessity”.
To encourage vertically integrated PV production facilities, India’s government introduced a production-linked incentive (PLI) scheme, which provides grants to companies manufacturing high-efficiency cells from locally produced supply chain components, from polysilicon to modules.
Aiming to support 10GW of integrated manufacturing capacity, the initial PLI tender received a more than fourfold oversubscription, leading the government to announce a second phase that intends to add 65GW of manufacturing capacity of fully and partially integrated solar PV modules.
Indian conglomerates Reliance Industries and Adani Group and transformer manufacturer Shirdi Sai Electricals were winners of the first PLI tranche and are looking to set up 12GW of integrated solar manufacturing.
Alongside its 2021 acquisition of solar module manufacturer REC Group, Reliance Industries invested US$29 million in German wafer manufacturer NexWafe. Davor Sutija, CEO at NexWafe, told PV Tech last year that Reliance will build gigawatt-scale facilities in India using his company’s technology.
Another Indian manufacturer looking to capitalise on India’s growing demand for domestically produced modules is Goldi Solar, which revealed in September it plans to increase its module manufacturing capacity from 2.5GW today to 6GW by the end of 2025, when it also aims to have 5GW of cell capacity.
The company has confirmed to PV Tech it will participate in the next PLI tender. “It is a very good initiative by the government… and it will help us to scale our capacity,” says, Bharat Bhut, director at Goldi Solar.
Although capacities awarded in the first PLI tranche are expected to start coming onstream from 2024, the scheme has been delayed significantly as bidding for the second stage is yet to be completed, according to Vinay Rustagi, managing director at consultancy Bridge to India, who says it is too early to judge how successful the PLI scheme has been.
Rustagi argues that India’s biggest policy support for solar manufacturers is the basic customs duty, which came into effect last April, introducing a 40% and 25% import duty on modules and cells, respectively. “The proposed duty level is quite a bit higher than estimated cost disadvantage of making modules in India,” Rustagi says.
Additional policies include a lower corporate tax rate of 15% for new manufacturers besides a non-tariff barrier in the form of an approved list of modules and manufacturers, whereby the government is basically deciding which companies may or may not sell modules in India, according to Rustagi.
Among the challenges facing India’s PV manufacturing sector, said the JMK/IEEFA report, is limited funding for research and development, a lack of skilled manpower and export limitation. The research said that in the absence of a domestic certifying agency permitting the export of PV products, Indian manufacturers must rely on international authorities to obtain certification, a highly expensive and time-consuming process “that is more prohibitive than attractive”.
Bridge to India expects final module costs in India to be 20-25% higher than those of imported modules, eroding some of solar’s cost advantage. Questioned whether module buyers will go back to procuring cheaper alternatives from overseas once policy support expires, Rustagi says: “That risk can never be discounted. Policy instability is a real issue in India and amongst the biggest risks for investors. But on the other hand, the government seems to be really determined this time around in doing whatever it takes to support domestic manufacturing.”
Europe lags in policy support
As the US and India progress with their new policies to scale up PV manufacturing, some European manufacturers are fearful that the continent will become less competitive unless similar measures are introduced.
While the US and India imported 77% and 75% of their installed solar PV modules in the last five years, respectively, this was 84% for the EU, which also has notably higher PV manufacturing costs than its rivals, IEA figures reveal.
“It makes a lot of sense to invest in the US. But currently is simply not attractive, comparatively, to invest in Europe,” Moritz Borgmann, chief commercial officer at heterojunction cell and module manufacturer Meyer Burger, said during a webinar hosted by SolarPower Europe in October. He added that the support in the US’s IRA “is just so concrete, so simple, so transparent and so massive that it is very difficult for us in this current environment, unless things really change in the EU, to continue investing at the scale that is required”.
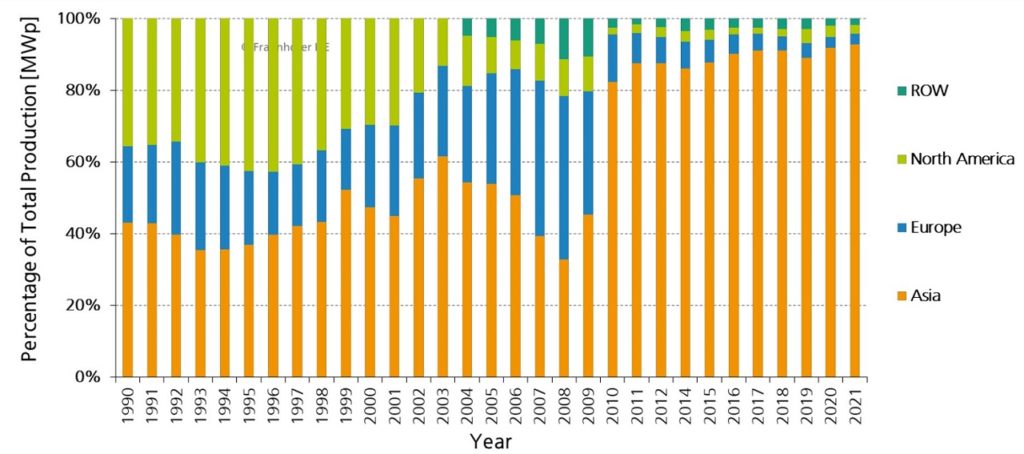
European PV manufacturers are also faced with soaring electricity prices due to the ongoing energy crisis. This puts around 35GW of planned manufacturing facilities in Europe at risk, Rystad Energy recently warned. The consultancy said that the energy-intensive nature of solar PV manufacturing processes is leading some operators to temporarily close or abandon production facilities as the cost of doing business escalates.
Among the initiatives aimed at helping manufacturers is the European Solar Photovoltaic Industry Alliance, which was formally launched in December and aims to help the EU reach 30GW of annual solar manufacturing capacity by 2025.
One area where EU manufacturers might gain an advantage is by producing modules with a lower carbon footprint. Recent analysis from market research firm InfoLink Consulting said the EU could win a competitive edge by focusing on n-type technology and low-carbon footprint products, which are two markets that China has yet to secure.
“PV panel manufacturing is already greener in the EU than in the rest of the world,” says Eliano Russo, head of 3Sun Gigafactory at Enel Green Power. The solar module manufacturing subsidiary of Italian utility Enel, 3Sun is aiming to reach 3GW of heterojunction (HJT) module production in 2024 at its factory in Sicily.
Russo says the EU should continue to promote sustainability with the introduction of instruments such as non-price criteria in renewables auctions or price premiums for sustainable PV panels. “The establishment of an EU certificate that demonstrates that all production and manufacturing steps of the PV panels comply with the principles of human rights, sustainability and circular economy of the EU and its decarbonisation goals is essential.”
Illustrating wider concerns that the EU may miss out on new PV manufacturing investments given the lack of support, Enel revealed in November it plans to build a 3GW HJT cell and module manufacturing plant in the US, leveraging its experience from the 3Sun Gigafactory. The company said tailwinds from the IRA serve as a catalyst for its US solar manufacturing ambitions.
The US IRA and efforts in India look set to generate notable PV manufacturing capacity, allowing local production to become more economically viable while alleviating some supply chain concerns.
First Solar’s Samantha Sloan says the past two years have demonstrated that the solar industry’s global hub-based manufacturing approach “represents a significant risk in the fight against climate change”. She adds: “We must recognise that strategic domestic manufacturing provides a significant degree of certainty, efficiencies and price competitiveness that traditional hub-based manufacturing does not.”