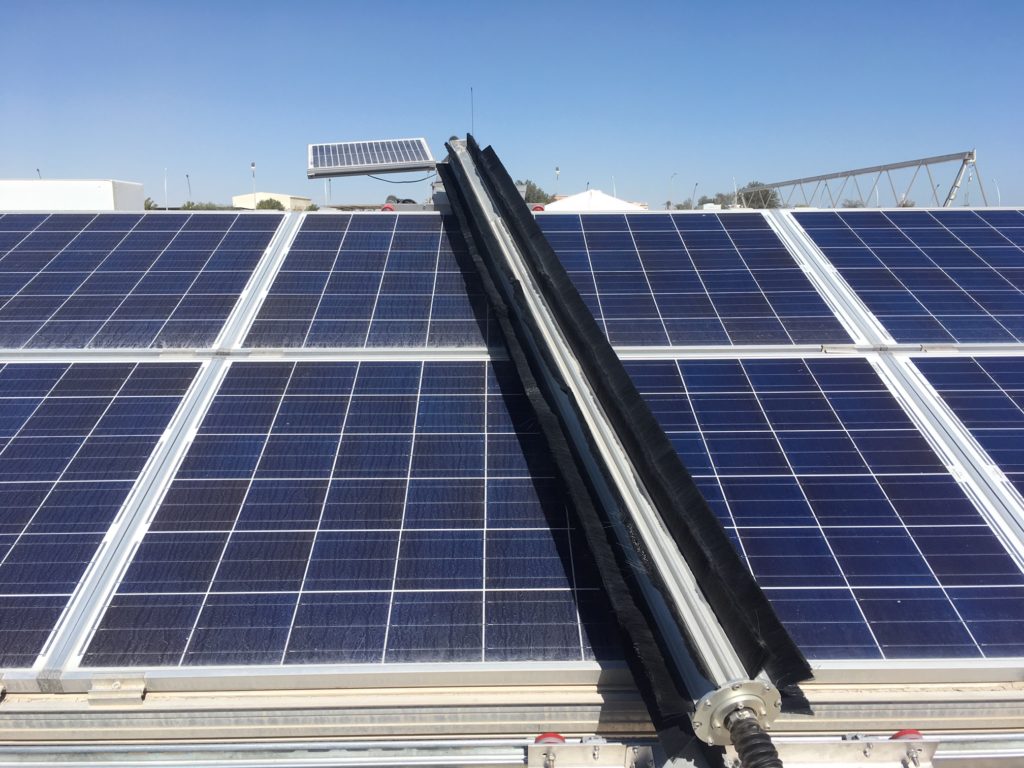
With PV cleaning robots posing significant advantages for solar O&M, Ben Figgis of the Qatar Environment & Energy Research Institute of Hamad bin Khalifa University, explores recent developments of standards in the field.
The robots are coming. And so are their test standards.
Unlock unlimited access for 12 whole months of distinctive global analysis
Photovoltaics International is now included.
- Regular insight and analysis of the industry’s biggest developments
- In-depth interviews with the industry’s leading figures
- Unlimited digital access to the PV Tech Power journal catalogue
- Unlimited digital access to the Photovoltaics International journal catalogue
- Access to more than 1,000 technical papers
- Discounts on Solar Media’s portfolio of events, in-person and virtual
It is now common to use machines to clean large-scale PV plants in desert regions. Soiling losses can reach 1% per day, and it is impractical to clean kilometres of PV arrays every few days by hand. Meanwhile the technology of robotics has improved while costs have fallen. But PV cleaning robots raise new questions, such as how often to run them, whether or not to use water and abrasion of the modules’ anti-reflective coating (ARC).
ARC abrasion is a particular concern. The coating increases light transmittance — and hence module power — by around 2-3%, and up to 5% at high irradiance angles. Yet it has a finite life even without contact cleaning, between one and 15 years according to a recent estimate (arxiv.org/abs/2101.05446v1). Some commercial cleaning robots use water to reduce potential abrasion, while others use dry brushing for simplicity and to avoid the use of scare water in desert environments. The question is how fast the ARC degrades depending on the brush type, cleaning frequency and wet/dry option.
To predict ARC lifetime, a combination of laboratory and real-world tests are needed. Accelerated lab tests provide results quickly and in controlled conditions. Real-world tests validate the accelerated-test simulations, and allow effects other than abrasion to be studied, such as module micro-cracking. Of course it is desirable for accelerated-test results to be repeatable and “apples-to-apples” between different labs, hence abrasion test standards have been developed specifically for PV coatings (both anti-reflective and anti-soiling).
Abrasion test standards were a major theme of the recent PV Robot Cleaning Workshop, organised by the Qatar Environment & Energy Research Institute of Hamad bin Khalifa University. Two open standards were published this year, and at least one PV module manufacturer is developing its own in-house test protocol.
Standard development
The US National Renewable Energy Laboratory led the development of IEC 62788-7-3, published in February 2022, motivated by the fact that existing abrasion standards from other industries did not adequately simulate PV soiling and cleaning. By default the standard uses medium Arizona test dust as the abrasive for the brush test methods, although other compositions can be used for local studies.
It is primarily designed for testing coupons — samples can be as small as 7.5cm square — though in principle full-size PV modules or cover glass can also be used. The standard also covers many different abrasion scenarios: linear and/or rotating brushes, in wet or dry operation with test dust, as well as falling or blowing sand. The closest simulation of large-scale PV plant cleaning is a rotating brush with linear motion, although as the standard notes, “there is no existing commercial test equipment” for this set-up.
The other standard launched this year, DIN SPEC 4867:2022-04, came from a consortium led by Fraunhofer CSP in Germany. It is focused on simulating real-world PV module cleaning. Samples must be “original format” (full-size) modules or glass samples, to achieve industrial-grade ARC fabrication and coating properties. The cleaning mechanism is a linearly-moving rotating brush, with tools and cleaning characteristics typical of commercial products. For consistency, the default abrasive is feldspar, which is applied only as a wet slurry. The standard has two “modes”: comparing durability of different ARCs, and comparing abrasion by different cleaning parameters such as brushes. Unlike the IEC standard, the DIN one specifies in detail the how the resulting ARC abrasion is to be measured and calculated, using a reflectance photometer.
These standards will help achieve repeatable and comparable laboratory abrasion tests. They are especially useful for “A vs. B” tests, for example comparing the durability of different ARC candidates or brush types. Another potential use may be to fast-track approval to use a certain robot with a certain module. For example, if a robot is already approved to be used with module X, and a standard test shows that module Y has the same abrasion resistance as module X, then the robot could be safely approved for module Y.
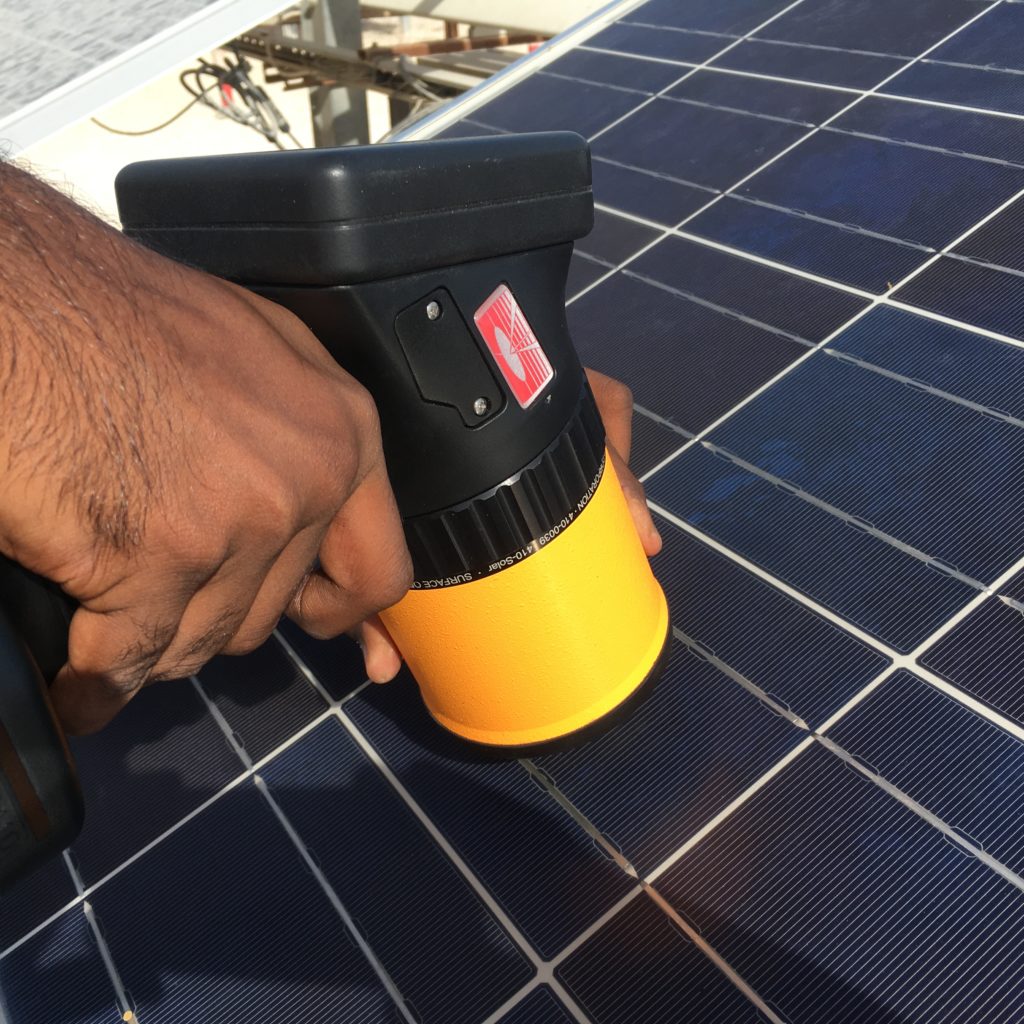
Rise of the robots
The workshop also discussed comparative robot testing. Jinko Solar presented their Dust Cleaning Robot Testing Project; the company says it is the first module supplier to conduct such abrasion tests. The program field-tests robots proposed for a specific PV project during the planning stage, with results validated by Jinko, the EPC and “third parties”. The tests inspect not only ARC abrasion but also the robot’s movement — tracker crossing, obstacle resilience and emergency stopping.
Much testing has been conducted with Jinko’s Tiger-Neo n-type modules, to confirm that the modules’ power rating is minimally affected. Robots run on an accelerated schedule of 10,000 passes, simulating 30 years of operation. So far Jinko has tested robots from five manufacturers. Eventually it aims to run the tests for other PV manufacturers and to release the protocol as an industry standard.
A key question is how well laboratory tests simulate the mechanics of real-world module abrasion over the long term, and whether one brush cycle in the lab stand equals one brush cycle in the field. A main difference is that in the field, dust accumulates over one or more days between cleanings, during which dew, humidity and high temperatures on PV modules can affect the dust properties. Therefore it is useful to validate results from indoor tests with outdoor field testing. Such indoor/outdoor comparisons will also help tailor accelerated tests for local dust types and sticking mechanisms.
At the workshop QEERI presented its outdoor robot testing program, part of its Solar Consortium industry group. The project has been using a dry-brush cleaning robot on the same PV modules and coupons at the Outdoor Test Facility continuously since 2020. Uniquely, the tests are non-accelerated — samples are cleaned either once per day, once per week, or not at all. Although this approach takes years to yield results (final measurements are due late 2022), it will provide highly realistic data on robot PV abrasion in desert conditions.