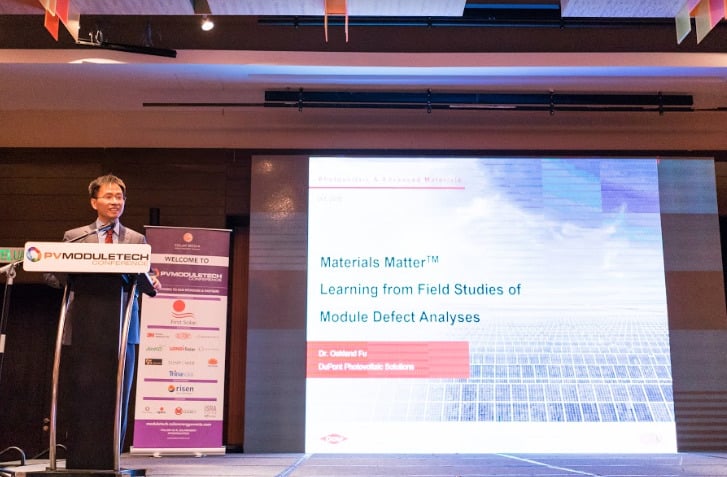
PV Tech caught up with Oakland Fu, technical manager at DuPont, to discuss data from one of the industry’s largest field studies as well as challenges for the industry in adapting to new technologies on the way to grid parity.
DuPont has been carrying out a major field study since 2011. What has been the key lesson?
Unlock unlimited access for 12 whole months of distinctive global analysis
Photovoltaics International is now included.
- Regular insight and analysis of the industry’s biggest developments
- In-depth interviews with the industry’s leading figures
- Unlimited digital access to the PV Tech Power journal catalogue
- Unlimited digital access to the Photovoltaics International journal catalogue
- Access to more than 1,000 technical papers
- Discounts on Solar Media’s portfolio of events, in-person and virtual
Oakland Fu: This year our cumulative surveyed solar systems have gone beyond 1GW, making ours one of the largest field programme studies in the industry across different regions, including North America, Asia Pacific and Europe. It covers different climates as well as applications like rooftop, ground-mount and floating solar systems.
The field survey also covers more than 4 million panels with all kinds of module technologies from around 92 module makers across nearly 300 solar systems. Our major finding is that the defects rate has remained at a high percentage (22.3%) across the past 8 years without showing a trend of decrease.
So while the PV industry has moved fast towards grid parity, the defect rates have stayed at a high level and this will be an issue before we fully reach grid parity.
Delegates from the downstream sector at PV ModuleTech this year have said they are puzzled by new technology introductions. What is your advice to them and how can manufacturers clearly explain what their offerings are to developers and investors?
This is always the issue. To achieve grid parity you have to adopt new technology, but there is a dilemma when you go for new products. The downstream developers only want proven technology so there is always a conflict there. The industry has to work together to solve this issue – not just module makers.
Currently, module manufacturers just buy materials and components, assemble the product and conduct some simple lab tests before sending the module for third-party certification, but developers and owners are not fully satisfied with this methodology.
So I do believe that module makers have to work with the upstream and downstream to have more systematic ways to evaluate this kind of reliability issue, not just focusing on high efficiency.
From DuPont's view, when we launch a new product, we put reliability at top priority, using high standards for lab aging tests as well as focusing on getting field data.
Module makers need to get more field data to support their new product development, not just lab tests. They can do this by working with developers on 1MW or 2MW beta test sites to accumulate such field data to satisfy the downstream customers that this kind of new technology has some field proven record in different kinds of situation.
Third-parties are of course also very important to this game, because they are also working on different testing protocols beyond IEC testing standards to meet this industry’s needs. They need to set a high bar for testing new products – not just two or three times the standardised trial – you have to simulate the field situations to get the better results that can convince module makers and customers to adopt new technology. It takes time but you have to do it.
How have you had to shape and advance your products to meet new technology trends in the last year?
A lot of new innovations have come on the way like bifacial cells and modules and leading module makers such as JinkoSolar and LONGi are also working on this kind of technology, while further downstream, developers are also showing interest. That’s why DuPont launched its clear Tedlar film for transparent backsheet and we are working with module makers on testing it.
Reliability is core to this product and we invested a lot of time and resources to evaluate the aging performance of this material. In our lab we do more than 500kWh per square metre UV aging trials. The backsheet is also tested at four or five times above the industry standard by module makers. This is to make sure it can maintain high performance at all kind of harsh environments.
As it happens, given what I’ve already said about the importance of field data, our transparent backsheet made with clear Tedlar PVF film has been used in BIPV modules for the past 20 years so it already has a long track record.