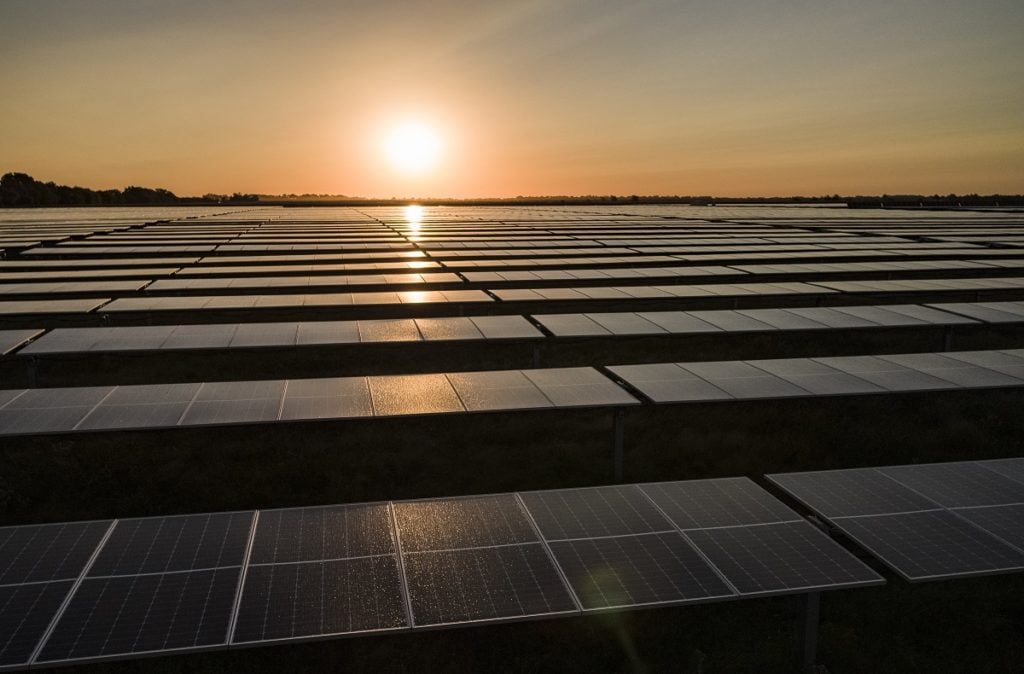
Investment in photovoltaic (PV) projects are a key driver to enabling sustainable growth in the solar PV installations market and thus, an important factor for the energy transition in many countries. To ensure the achievement of the desired rate of return on investment (ROI), it is important to establish a professional risk assessment, which serves to reduce the risks associated with related investments.
The risk assessment is an active quality management process where all stakeholders in the approval process of a PV project attempt to identify potential legal, technical and economic risks through the entire project lifecycle. These risks need to be quantitatively and qualitatively assessed, managed and controlled. Despite a wide overlap in this quality management process, the focus and the assessment criteria will vary depending on the stakeholder.
Unlock unlimited access for 12 whole months of distinctive global analysis
Photovoltaics International is now included.
- Regular insight and analysis of the industry’s biggest developments
- In-depth interviews with the industry’s leading figures
- Unlimited digital access to the PV Tech Power journal catalogue
- Unlimited digital access to the Photovoltaics International journal catalogue
- Access to more than 1,000 technical papers
- Discounts on Solar Media’s portfolio of events, in-person and virtual
The different stakeholders must each develop their own individual risk management strategy along the lifecycle of a PV project using a four-step process of risk identification, risk assessment, risk management and risk controlling. Best practice guidelines and concrete tools to better manage technical risks throughout the PV project lifetime are emerging as the experience level in the PV industry continues to rise. The ultimate responsibility of project risks remains with the owner and operator of the PV plant. With the help of a professional risk management plan they can significantly reduce and transfer the initial risks associated with a PV project.
With increasing experience gained from more and more projects, a more mature and professional PV industry, and established professional and standardised processes, these residual risks can be low. This is further supported by the positive experiences from many investors that have managed to run successful projects. But when one looks into the details, this may have occurred due to external phenomena such as increased irradiance levels not considered in the early stage of the project.
This article therefore presents updated methodology on key measures as part of the technical risk management during the design and procurement phase of a PV project, that helps to reduce technical risks and increase probability of commercially successful investment.
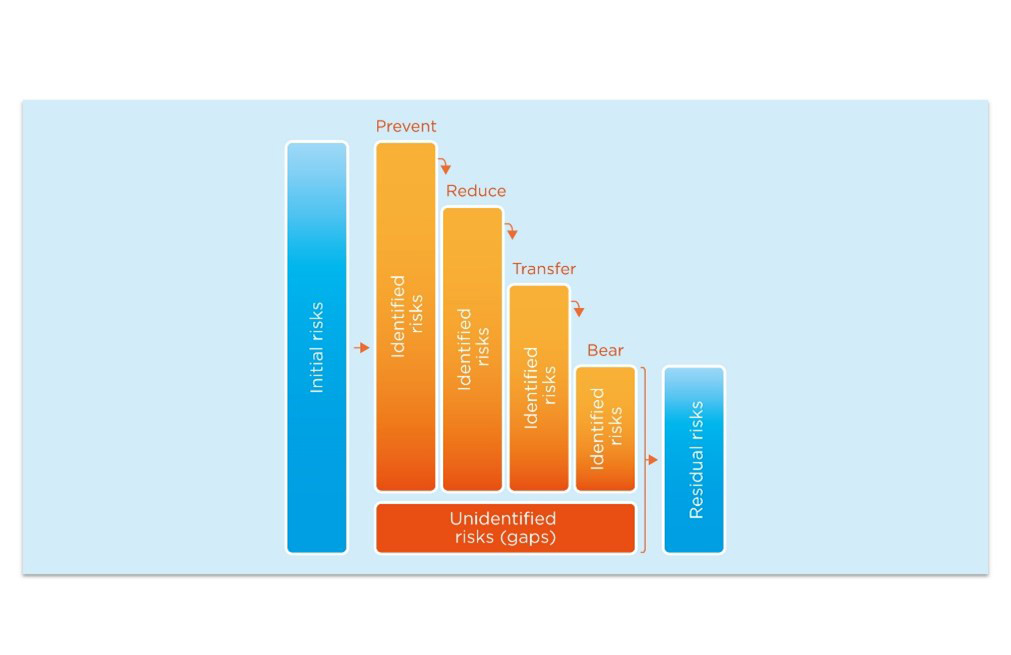
The yield assessment – frequently underestimated risk in the design phase
Yield assessments (YA) and long-term yield predictions (LTYP) are used by investors in order to take business decisions on long term investments. Investors know that past performance is no guarantee for future results. Yield assessment is an essential step in a PV project, as it helps to determine whether a system will be funded or not. However, the YA is not only about the utilised software, it is mainly about the user. YAs may not be as reliable as expected, and for example in the IEA PVPS Task 13 Report “Uncertainties in Yield Assessments and PV LCOE” [IEA2020], the authors demonstrated how seven highly skilled specialists did not arrive at the same result, despite having been provided the same detailed inputs.
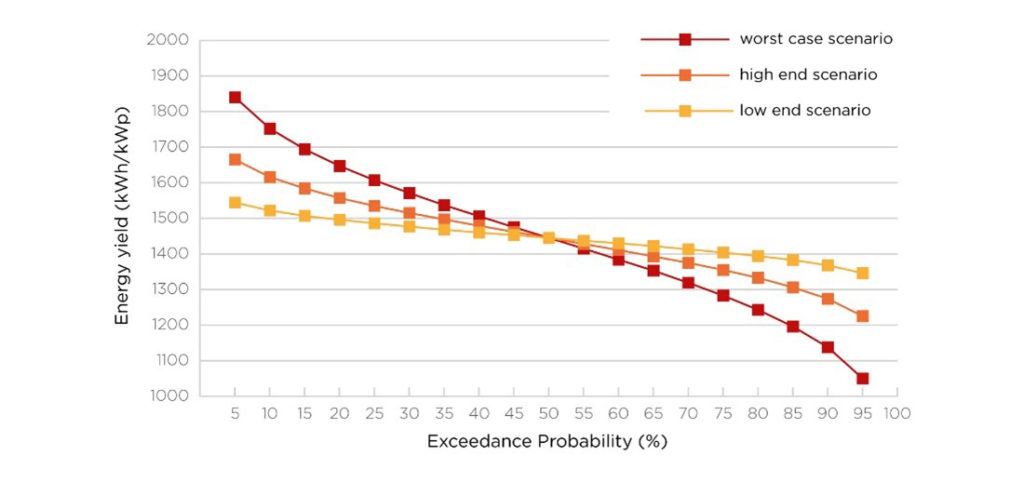
Together with cost data (CAPEX, OPEX and discount rate), the output of a YA and LTYP (utilisation rate, performance loss rate and lifetime) provide the financial investors the parameters needed for the calculation of the levelised cost of electricity (LCOE) and to assess the cash flow model of an investment with relative internal rate of return (IRR) and net present value (NPV).
YA and LTYP outputs should be provided with a related exceedance probability. This gives the right tool to stakeholders involved in PV projects to take the best decision in terms of risk-aversion. A reduction in the uncertainty of the energy yield can lead to higher values for a given exceedance probability and hence a stronger business case.
The main challenge in yield assessment (YA) and long-term yield prediction (LTYP) relates to the trustworthiness of site-specific information. In a global market it is in fact not uncommon to be assigned the task of assessing the yield of a PV plant to be located in areas which are not familiar for the yield assessor, and therefore access to local knowledge is of extreme importance.
The most important parameter influencing the energy yield assessment is in fact the site-specific insolation. Several aspects need to be considered: reliability of the database, interannual variability, and long-term trends. Availability of validated satellite data or availability of ground measurements is thus an essential first step. To this extent, site adaptation techniques can increase the reliability of the selected site-specific insolation as they combine short periods of measured data with satellite-derived data having a long period of record with not necessarily site-specific characteristics. Upon completion of the measurement campaign, which is typically around six months/one year, different methodologies can be applied to reduce the bias. The bias corrected record of satellite data is then used in this relationship to predict the long-term solar resource at the target site.
Other parameters directly affecting the estimation of the incident radiation are linked to i) the calculation of the irradiation on the module plane and thus the model used for the decomposition and transposition of the global horizontal irradiance to global tilted irradiance, ii) shading losses (near and far), iii) soiling losses, and iv) reflection losses. Shading and soiling losses are also site-specific and knowledge on the local conditions can ensure that the losses are properly assessed.
Finally, all the conversion steps from irradiance to electricity must be considered. The power calculation in PV modelling software not only depends on the software’s algorithms, it also requires that components (modules, inverters) have been correctly characterised and are available as inputs for the software. While the modeller can input or translate datasheet values as provided by the manufacturer, as of yet, no guarantee is given by most manufacturers as to the accuracy of these key inputs. The uncertainties on (sub)components in the PV power modelling chain are often relatively low through the implementation of peer-reviewed methods. However, modelling risks can occur through errors in module or inverter files, which can negatively affect the yield, and with it, the financial viability of PV plants. Therefore, it is increasingly becoming the common industry standard that PV modules or inverters are subjected to additional characterisation by independent laboratories upon instruction by investors to ensure that the power plant model is bankable. Special care must be taken during this phase in terms of number of modules to be tested and selection procedure in order to obtain a reliable mean value of electrical parameters to be used in power calculation.
To summarise, the main risks related to yield assessments are:
- The choice of database for the horizontal irradiation. Irradiation data derived from satellite images are increasingly used as input for long-term yield estimations and as the basis for reference yield calculations for monitoring and business reporting. Several authors have evaluated the quality of satellite-based irradiance data in the past, typical normalised root mean square errors for satellite-based irradiation reported in literature are situated between 4 % to 8 % for monthly and 2 % to 6 % for annual irradiation values.
- Inexperienced yield assessor, or one that is not familiar with a specific location
- Input parameters not validated for a specific location
- Assumed degradation rates higher/lower than expected with an impact on the long-term yield assessment
- Specification of components do not correspond to their datasheet and guaranteed values
- Typically, investors require one YA. In some cases, more YAs might be requested if results are unclear. The various YAs can be averaged to assign a purchase value to a given project and this could be a source of error. YAs should contain all information needed to assess their reliability.
Best practices to ensure realistic yield and LCOE calculations over the project lifetime
Investing resources during the design phase is of extreme importance as mitigation measures which prevent future failures in the field and allowed optimal system design are the most effective from the perspective of a cost-benefit analysis. Some measures can be easily applied to reduce risks in yield assessments and long-term yield predictions:
- Request the satellite data provider for validated data with ground measurements, or apply site adaptation measures
- Gain local knowledge to validate site specific parameters
- Check the trend over different time-periods (.e.g 2011-2020, 2001-2010) to check for long term trends
- Check reliability of provided files, ask manufacturer for qualified data or use independent third-party services for PV component quality assurance
- Make sure that for LTYP module degradation is not the only factor included (use performance loss rates instead of degradation) and that unavailability and reversible failures are also considered
- Design review and construction monitoring serve to detect issues caused by bad PV plant conception and poor PV construction workmanship;
- As asset manager, include all the information used in the YA, LTYP and business model inside the same digital platform used for the EPC and O&M phase in order to have a complete overview of the history of the asset.
The direct follow-on consequence from deviations in yield assessments is that LCOE values will also exhibit a variance, on top of the additional modelling assumptions that can be employed for LCOE calculations. Determining P50 and P90 values for LCOE results and highlighting the assumptions/modelling chain will be important. From an industry perspective, it would be beneficial if more “live” post-mortem analyses (i.e. comparison of the LTYP and measured data, at e.g. every 5 years of system life) would be made and published. These can then be used as crucial feedback and inputs for YA modelers, financiers, and insurers.
High quality components – a critical part of achieving planned ROI
Carrying out proper quality assurance in the procurement phase ensures that an appropriate quality level can be achieved, and that the equipment is within the planned specifications. This sounds simple enough in theory, but in reality, there are many cases that indicate otherwise – i.e. where components installed in the field did not meet the desired criteria.
To cite an example: VDE Renewables assessed a PV portfolio in Turkey with a total capacity of 230MWp. The portfolio of systems used eight different PV module types, each of which possessed certification according to international standards. However, underperforming PV modules were detected at the start of PV system operation. The comprehensive quality assurance work carried out by VDE Renewables determined that there were two types of PV modules which were underperforming by around -4%, which was beyond the tolerance limit taking into account measurement uncertainty. These underperforming modules were used in 26% of the whole portfolio. Based on a 4% underperformance rate, the sub-par PV modules lead to annual losses of approximately US$200,000 (or US$2,000,000 over 10 years of operation). Proper quality assurance in the procurement phase would have detected the problem before operation, strengthened the basis for negotiations for the buyer, and saved cost and effort in making the claim to the manufacturer.
However, underperformance of the equipment is by far not the only problem when it comes to procurement. Other risks can arise as well, such as:
- Low quality and reduced reliability due to bad workmanship, pre-damaged materials (e.g. cells with higher tendency of cell breakage) as a result of weak QA processes in the factory
- Uncertified products which can occur if the manufacturer replaces materials in the product bill of materials and does not carry out re-certification and reliability testing
- Fraud due to fake materials or products
In the procurement phase of a PV project, there has always been a strong focus on the quality of the PV modules. The reasons behind this are understandable: modules represent a large share of total costs, are difficult/impossible to repair, and quality assurance results are often easy to interpret and address. The coupling of performance to purchase price, and conversely, low performance to yield loss, are some of the strongest arguments a buyer can use with a supplier. However, problems with other components have also been reported in the field. Inverters are certainly a blind spot when it comes to independent quality assurance during procurement.
But at the same time the expectations are increasing. In the past, inverters were often operated in a protected and climatically controlled environment, such as in building structures (e.g. central inverters). Nowadays, more and more string inverters with 100 to almost 200kVA are operating unprotected in the field. This of course increases stress on the inverter and thus increases requirements around reliability and weathering resistance. In addition, more variability of operating conditions occurs.
Yield losses mainly result from underperformance in the field compared to the data sheet, but also due to downtime caused by inverter failures. In [NREL2019] it is reported that majority of failures in PV power plants are caused by the power electronics. Possessing certification according to existing technical standards alone do not ensure that the specifications are fulfilled, and that the modules and inverters will operate in the field without any problems.
How can I make sure my equipment will perform according to plan?
Quality control and risk mitigation for procurement should begin at a very early stage in order to reduce downtime and output losses of the plant. It also helps avoid/reduce the time and effort in making warranty claims or even lawsuits against the manufacturer and replacing defective equipment.
Equipment buyers should specify their quality requirements as well as the quality assurance measures that they plan to implement before they even start approaching manufacturers. Some PV module buyers for example, fail to agree on the terms for taking samples from production to be sent to an independent test lab. It is important to spread out sample selection across the different lines/workshops and production shifts and dates in order to ensure proper representativity during testing.
It is often the goal of manufacturers to limit sample selection to just a few pallets in order to reduce the logistical effort required. Potential arguments with the manufacturer can therefore be avoided if these conditions are agreed upfront with the buyer in their purchase contracts.
Engaging an independent quality assurance partner such as VDE Renewables is a best practice followed by many professional project developers. There are a myriad of quality assurance measures that a buyer can take advantage of, such as the ones listed below
- Review of product certificates and bill-of-materials (BOM) of the selected product – to ensure that the BOM specified by the manufacturer is properly certified
- Pre-production factory audit – to evaluate if the manufacturer’s production facility meets industry standard
- On-line production supervision – involves the full or part-time supervision of production of the buyer’s products in the factory. This helps verify that the product is being produced according to the contractually agreed BOM, and that quality parameters and processes are being followed properly.
- Pre-shipment inspection – after production, products are typically tested in the factory for quality and performance. The products are then packed and loaded in containers. This shall be witnessed by an independent inspector to ensure all quality parameters are properly executed.
- Independent lab testing – in order to independently verify the test results from the factory, buyers can have their purchased products tested on a sample basis at a third party testing laboratory. Additional tests can be carried out to verify claims made by the manufacturer about their product, for example for PV module resistance against Potential Induced Degradation (PID). These tests can be carried out at the country of manufacture (e.g. China) so that in the case that a batch fails a test and has to be rejected, it can be done so before the products are shipped to their end destination. It can also be additionally performed at the destination country as well as an additional measure.
The above-mentioned quality assurance measures provide buyers with the opportunity to establish “quality gates” during the procurement process. Should the equipment supplier fail at any one of these gates, the buyer can quickly demand for a replacement batch of equipment, which at the same time minimizes the impact on the project timeline thanks to early failure detection.
Buyers can further benefit from the neutral expertise of experience professionals to help define their quality criteria, analyze the results of inspections and tests, and explore corrective actions in case any quality shortcomings are found during the project.
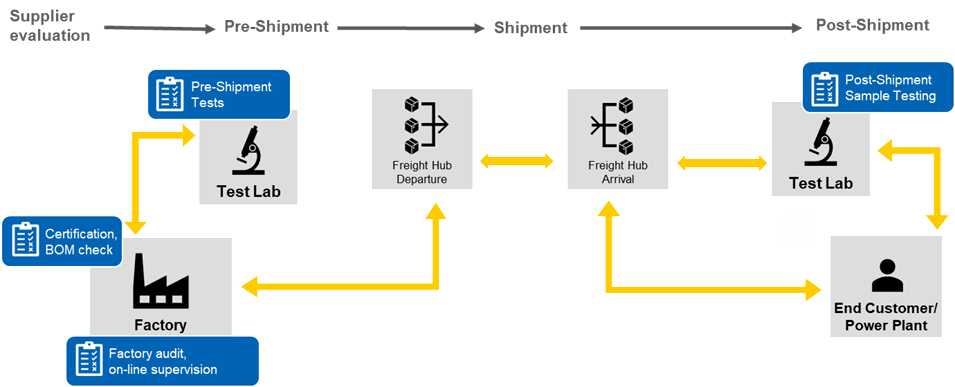
Conclusion
- Quality assurance in the earliest stages of the project have the highest impact on future performance and thus ROI of the PV plant. It also reduces cost and efforts for remediation down the road.
- Independent QA also establishes trust with financial stakeholders and insurance providers at an early phase of the project, thus supporting a developer with acquiring financing and insurance thanks to the increased attractiveness of the project.
- Some of the most critical focus areas for early stage independent quality assurance are the yield assessment and equipment procurement.
- Streamlined and standardized quality assurance processes, which can be achieved for example by working with experienced independent experts, will reduce complexity, cost and effort.
References
[IEA2020] David Moser et al., “Uncertainties in Yield Assessments and PV LCOE,” IEA-PVPS T13-18, 2020; https://iea-pvps.org/key-topics/uncertainties-yield-assessments/
[NREL2019] Nagarajan, Adarsh, Ramanathan Thiagarajan, Ingrid Repins, and Peter Hacke. 2019. Photovoltaic Inverter Reliability Assessment. Golden, CO: National Renewable Energy Laboratory. NREL/TP-5D00-74462. https://www.nrel.gov/docs/fy20osti/74462.pdf.
Authors
Boris Farnung
Boris Farnung is global head of division power plants and systems at VDE Renewables GmbH, Germany. Over the past 15 years, Boris has established relationships and gained the trust of leading technology companies, utilities and international financial institutions in developing, managing and completing complex technical projects. He is the Operating Agent of the IEA PVPS Task 13 – Performance and Reliability of Photovoltaic Systems. In this role, he has proven his ability to manage and coordinate international and distributed technical experts and scientists. During his career, Boris has proven his ability in developing and leading teams, change management and intercultural skills. He has a broad network in the renewable energy industry and established relationships with international contacts.
Keith Punzalan
Keith Punzalan heads strategy and business development at VDE Renewables, covering the fields of solar and wind energy, as well as energy storage. Keith has spent his entire career in the field of renewable energy. During his time at the Solar Energy Research Institute of Singapore, he supported the ramp up of the institute in its early days and worked on solar power plant feasibility studies and other market research projects around the Southeast Asian region. In his career at VDE, Keith also established and grew a global series of renewable energy events focused on addressing bankability and quality topics in the industry. Through these events and projects, he regularly deals with renewable energy manufacturers, project developers, banks, investors, insurers, government agencies, utilities, market researchers and advisory firms.
David Moser
David Moser is research group leader at EURAC Research’s Institute for Renewable Energy, where his main fields of research include the indoor and outdoor characterisation of PV modules, the monitoring of PV project performance and modelling and analysis of energy systems.