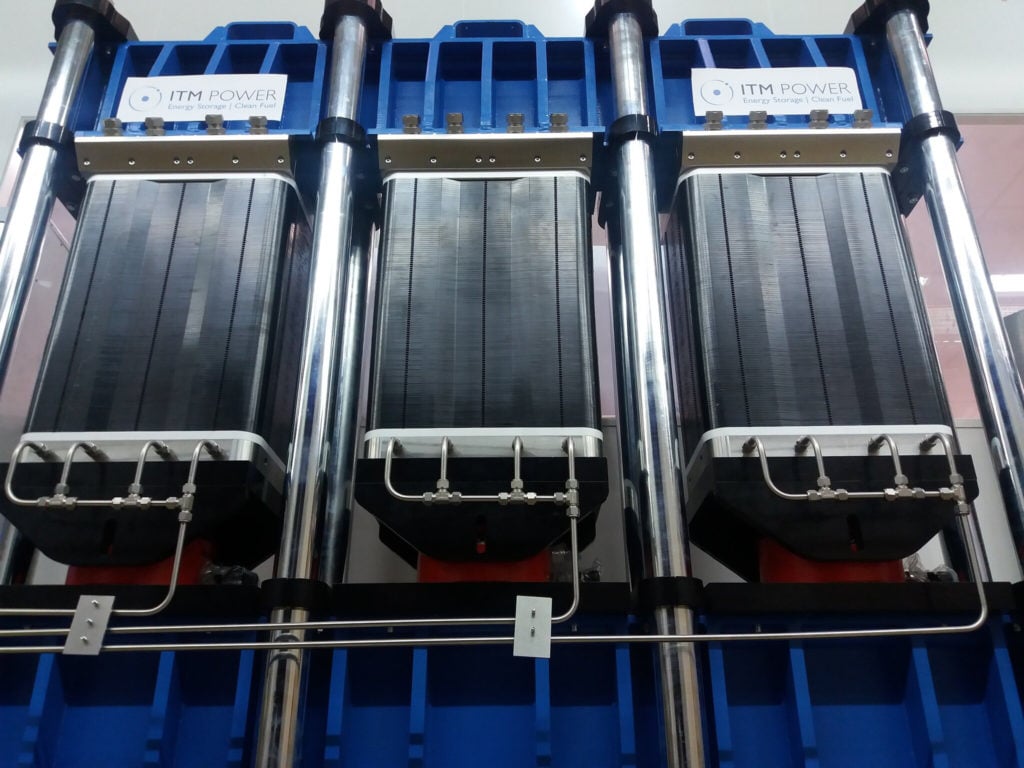
The race for green hydrogen dominance is on, with global markets ramping up the scale of their ambition in terms of deployment. But this too is causing a further fight for market share among the three core electrolysis technologies, as Jonathan Tourino Jacobo learns.
Until not so long ago, green hydrogen was considered an exorbitantly expensive cousin of its fossil fuel counterparts, so-called blue and grey hydrogen. But the conflict in Ukraine and the need for the European Union to reduce its reliance on Russian gas has significantly increased the price of production of grey and blue hydrogen, making the once-costly green counterpart seem a lot more cost efficient, and cleaner too.
Unlock unlimited access for 12 whole months of distinctive global analysis
Photovoltaics International is now included.
- Regular insight and analysis of the industry’s biggest developments
- In-depth interviews with the industry’s leading figures
- Unlimited digital access to the PV Tech Power journal catalogue
- Unlimited digital access to the Photovoltaics International journal catalogue
- Access to more than 1,000 technical papers
- Discounts on Solar Media’s portfolio of events, in-person and virtual
With production costs from green hydrogen expected to be lower in certain European countries than fossil fuels, it’s simply a matter of time before the scale of green hydrogen projects grows. For that, production of electrolysers will have to increase if the sector is to cope with demand.
Water-based electrolysis is currently the most common way to produce hydrogen given its capacity to produce hydrogen with purities in excess of 99.9%, and there are three core technologies leading the way: alkaline, proton exchange membrane or polymer electrolyte membrane (PEM) and solid oxide electrolysis cell (SOEC). Which one to choose can depend on different factors as each technology has its specificities and particularities that need to be taken into consideration.
PV Tech Power spoke with analysts and manufacturers to examine how electrolysis technologies work, what differentiates them from each other, what they are best suited for and which one is best placed to dominate the green hydrogen market in the future.
Alkaline electrolysis offering maturity
Out of the three core electrolysis technologies, alkaline electrolysis is the most mature, with the basic principles of the technology having been used for more than a century. It relies on the use of the alkaline being a liquid electrolyte, with an asbestos diaphragm that separates the electrodes used to split oxygen and hydrogen from water. The reaction further generates heat, which can be harnessed to increase the reaction’s efficiency.
With alkaline electrolysers, since the water is non-conductive, the process to separate hydrogen and oxygen needs the use of a further chemical, normally potassium hydroxide. This is used as a liquid electrolyte to increase the ionic conductivity in the cell stack. Other processes can use sodium hydroxide or sodium chloride as electrolytes, but potassium hydroxide is the most commonly used. However, this makes alkaline electrolysers highly corrosive due to the liquid state of the electrolyte and requires more components in order to clean, raising its maintenance cost.
Alkaline electrolysis is, however, limited by the fact a more permanent and stable power source is needed. Alkaline-based electrolysers take time to start and cannot be stopped instantly, meaning variable source of power such as wind and solar PV are more complicated to be used as a direct source of electricity. This has lent weight to developers assessing other technologies that could, at least in theory, be better suited towards green hydrogen production.
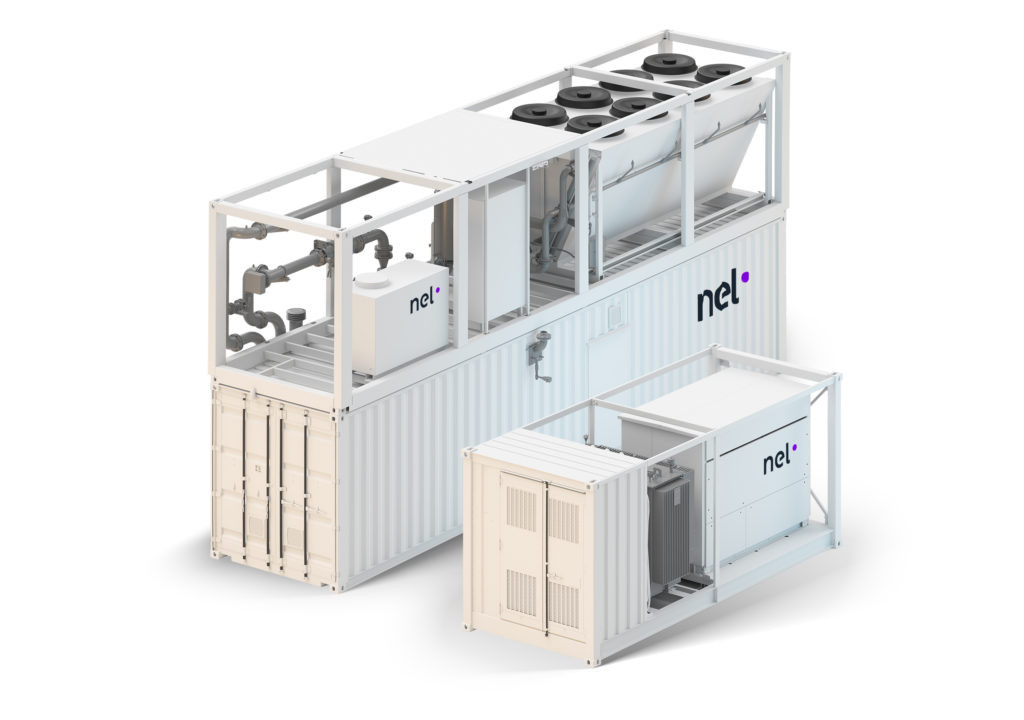
Partnering with PEM
Even though PEM technology is more recent than alkaline, the structure of the electrolyser is quite similar given how it works at a low temperature – between 30 – 80 degrees Celsisus – with electrolysers not passing the 100◦C threshold.
The main difference between PEM and alkaline electrolysers is the former uses a solid polymer membrane electrolyte to absorb the water, creating a physical barrier between the two electrodes instead of a liquid solution such as potassium hydroxide. This means you can generate high pressure hydrogen, says Graham Cooley, CEO at ITM Power, which has been manufacturing PEM electrolysers in the UK for the past two decades.
The physical barrier prevents gases from mixing and only lets through positively-charged hydrogen, avoiding at the same time any corrosion that would incur higher maintenance costs. Cooley adds that the presence of a physical barrier also allows PEM technology to be easily turned on and off without any disruption as it does not create any turbulence in the bottom strings, which at the same time allows for the use of fluctuating power supply such as solar PV or wind.
“I don’t think there’s any limit to what projects you can do with PEM electrolysis”
While in operation the electrolysis can cause a decrease in moisture, and it is necessary to control the presence of water, but PEM technology can work with differential pressure and can be directly set to a specific pressure, given the equipment can be stabilised quite fast. It’s claimed PEM electrolysis also has a smaller physical footprint, as it can produce more kilograms of hydrogen per m3 of cell stack and needs far fewer components than alkaline electrolysis. As for the type of projects PEM can be used for, Cooley says: “I don’t think there’s any limit to what projects you can do with PEM electrolysis.”
He adds that even though in the past ITM Power wasn’t able to get the same modular scale required, now ITM Power is able to make modules in 2MW and 5MW capacities that can be stacked up, as evidenced by the fact the company’s largest electrolyser project underway has a planned capacity of 100MW.
Using steam to produce hydrogen with SOEC
The process for solid oxide electrolysers (SOEC) is quite different from the previous two in the sense that the electrolyte uses a solid ceramic material, making it compact with a fast response time, and also conducts a negatively charged oxygen ion membrane.
While alkaline and PEM both operate at temperatures no higher than 100°C, solid oxide electrolysis works with higher temperatures ranging from 500 – 1,000°C, which in itself increases the electrolysis efficiency rate as it is able to use the heat generated by the temperature and reduce the amount of electricity that’s required to break the water into hydrogen and oxygen, says Chris Ball, head of technology advocacy at solid oxide manufacturer Bloom Energy.
This higher temperature also permits SOEC to use industrial waste heat from other sources, using steam as an energy input that can in itself be used in the process instead of water, reducing further the electricity needed to produce hydrogen in comparison with other electrolysers.
Similar to PEM technology, SOEC has so far been used mainly for smaller-scale projects and its higher temperature can cause a greater degradation and corrosion of the metals, resulting in an increase in maintenance costs, similar to alkaline electrolysers.
“I don’t think that there’s a real difference between the different technologies as far as how the projects are built,” Bloom Energy’s Ball says, adding: “I think it’s more about the hydrogen economy what’s needed. Certainly, large-scale, purpose built hydrogen facilities are going to be the most cost effective.”
Be project specific
When confronted with the choice of different electrolyser technologies, many factors must therefore be taken into consideration. Is this for a small- or large-scale project? Does the technology requirements dictate that only the highest-efficiency technology will suffice, or is it more a question of the project capex and its return on investment?
At the moment there is not a single approach capable of ticking all the industry’s boxes, meaning that it remains a case-by-case basis when it comes to technology selection. There is no “universal tendency” to prefer one technology across the board, Stephen Szymanski, director of business development at Nel Hydrogen, says.
However Mollie McCorkindale, market analyst at PV Tech Power publisher Solar Media’s market research division, suggests that PEM technology is currently favoured for green hydrogen applications given how it operates alongside variable power supplies – negating the need for a constant power source or to be paired with battery energy storage systems – and the added fact that PEM electrolysers have more simple maintenance procedures and fewer component parts.
But if projects are viewed in terms of capital cost, Szymanski notes that alkaline electrolyser technologies – when viewed a cost-per-kilowatt basis – is around US$1/kW lower than that of PEM electrolysers at the moment, increasing the technology’s appeal to projects operating on more of a budget. Alkaline is also favoured when factoring the scale of the project, McCorkindale notes, pointing in particular to how green hydrogen projects coming forward in the UK using PEM are mostly of a smaller scale.
This is perhaps why the efficiency of the three technologies is under the microscope. “[It’s] where the real differences are between the technologies,” Ball says, adding that the fact SOEC uses less electricity offers that technology class a competitive edge.
“With a high temperature electrolyser we’re using less electricity, electricity being the most expensive part of electrolysis, that’s really important,” says Ball. When using electricity as the sole input, Ball says SOEC technologies can achieve a 15% efficiency advantage compared to alkaline or PEM. When the use of steam is also factored in, that efficiency increases even further. “Our efficiency goes up to 30% when you have steam because again you’re using less electricity, so we have an efficiency advantage,” adds Ball.
Scale and the race to the top
With the three core electrolysis technologies possessing different competitive advantages, the key battleground for green hydrogen dominance could well be scale. With numerous markets establishing sizeable targets for green hydrogen development – further increasing in the wake of Russia’s invasion of Ukraine – gigawatts of electrolysers will need to be manufactured and installed this decade. Szymanski says Nel Hydrogen’s alkaline electrolyser plant in Herøya, Norway, has an existing output of 500MW per year, although this could expanded with the addition of up to four production lines, taking its output to 2GW. The company is also looking into scaling up production of its PEM technology in the US. The reason the company is currently prioritising alkaline, Szymanski says, is due to the fact larger projects would, at the moment, have a bigger demand for alkaline electrolysers over PEM.
Cooley says ITM Power, meanwhile, currently has a 1GW production facility in the UK, and the company is already building a second facility of 1.5GW output, consistent with a strategy to reach 5GW per year by the end of 2024.
Bloom Energy is currently building a new factory in California for its solid oxide fuel cells that is close to 1GW, which Ball says could be converted to manufacture electrolysers in response to market demand. That switch would equate to around 2.4GW of capacity.
The race for scale is therefore clearly on, and other companies have announced they are to accelerate the manufacture of electrolysers to reach the gigawatt-scale production needed.
Market demand is proving to be a major driver in this regard. The need to faster increase green hydrogen production is increasing globally. In March 2022 the European Union revised its plans for the decarbonisation of its region and updated its goals through the REPowerEU programme. Whilst before the bloc estimated that around 5MT of green hydrogen was needed by 2030, that number rose to 20MT in the programme recent revision, increasing the for electrolysers from 80GW to more than 200GW in less than eight years. A report from McKinsey & Company in February 2021 estimated worldwide investments would reach US$300 billion by the end of this decade, with almost half of it coming from Europe.
In the shorter term alkaline electrolysers might still be favoured for large-scale projects, as perhaps evidenced by Nel Hydrogen’s manufacturing capacity being larger for that technology than PEM and as Szymanski alludes to, market demand is higher for this technology. At the beginning of this year, BloombergNEF published its prediction for hydrogen in 2022, expecting alkaline to increase its market share over the other technologies and account for 75-78% of shipments. The research firm cited its lower cost and the fact it is best suited for large-scale projects for its increased dominance.
“Cost reductions will mean that alkaline electrolysis will find it difficult to find a market”
But as costs continue to fall in the coming years, PEM will be able to compete with alkaline, Cooley believes. “Cost reductions will mean that alkaline electrolysis will find it difficult to find a market,” he says. If the UK is any suggestion to what might happen, alkaline might still be favoured for large-scale projects at the moment, with PEM being used for those of smaller scale, as McCorkindale says. But that might change in the future if manufacturing costs of PEM electrolysers continue dropping.
Moreover, providing we can rule out the entrance of a new technology that could have the capacity to disrupt the market before the end of this decade, PEM technology is expected to be best suited to dominate the market in the long run when producing green hydrogen, providing the cost of manufacturing continues to fall in line with expectations. Its advantages of no counter-effect from power fluctuation coming from renewable sources and a lower maintenance cost looks set to position it on top.
While that does remain subject to some debate in the industry, it is without doubt that electricity remains the largest cost of hydrogen production, making up to 80% of the levelised cost. It’s for that reason that green hydrogen’s aim of reaching its coveted production cost of US$1.50/kg – one that will see it outcompete blue and grey hydrogen – does still rely on the cost of power production, and therefore solar PV and wind, to find further cost reductions this decade.