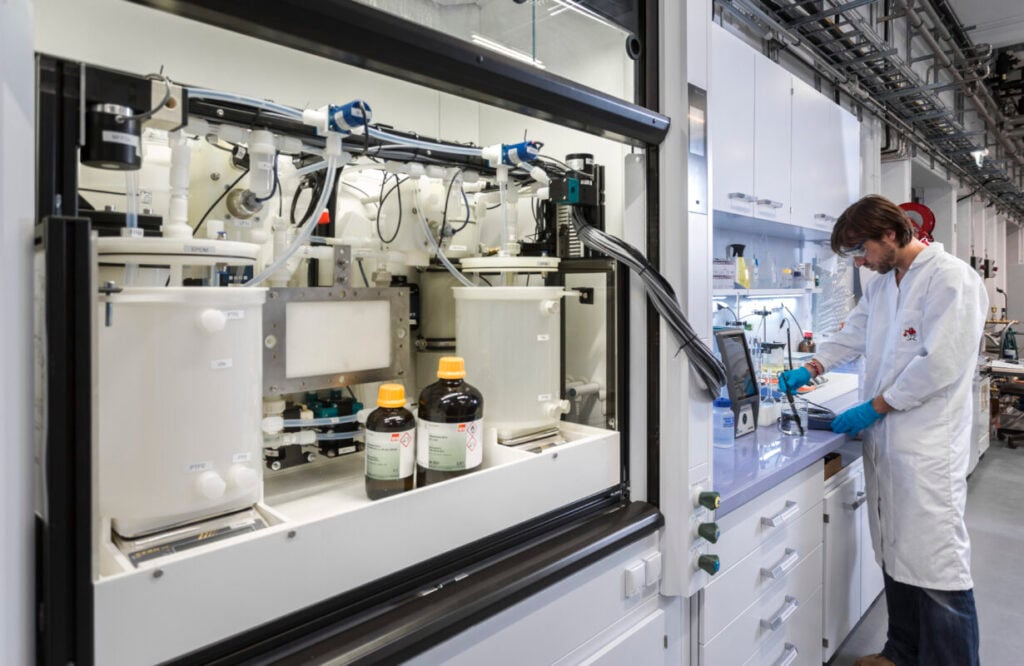
A solar cell manufacturing plant can reduce water consumption by up to 79% with existing technologies, according to recent research conducted by the Fraunhofer Institutes for Building Physics IBP and for Solar Energy Systems ISE, the Technical University of Berlin and Rena Technologies.
Researchers created a model of the water flows in a solar cell manufacturing plant with a production capacity of 5GWp a year. The model contains two steps. The first collects and validates data for the cell manufacturing plant, while the second applies a material flow analysis for all water-related processes and for treating wastewater streams.
Unlock unlimited access for 12 whole months of distinctive global analysis
Photovoltaics International is now included.
- Regular insight and analysis of the industry’s biggest developments
- In-depth interviews with the industry’s leading figures
- Unlimited digital access to the PV Tech Power journal catalogue
- Unlimited digital access to the Photovoltaics International journal catalogue
- Access to more than 1,000 technical papers
- Discounts on Solar Media’s portfolio of events, in-person and virtual
After these steps, researchers proposed two potential circular water strategies, including the reuse of low contaminated wastewater (LCR) and a minimal liquid discharge (MLD) approach, in which certain residual materials are recycled and used elsewhere. For example, etching solutions left over from solar cell production can be used in the cement production.
The results show that 38% and 79% of the water consumption and 40% and 84% of the wastewater indirect discharge at the cell manufacturing plant can be saved by the LCR and MLD approaches, respectively.
The researches said implementing the saving measures would not only impose any additional costs on production, but also reduce the overall costs slightly.
“These reductions are gained by saving 38% of the water and 40% of the wastewater discharge from the reference cell factory requirements,” the researchers said.
Based on the results of the research, the researchers believed that building a new solar cell manufacturing plant in locations with less water availability will be feasible in the future.
Aside from the potential of the new circular water strategies, the researchers also mentioned several challenges. For example, the quality and purity of the by-products should meet marketability specifications. Buyers of by-products should be available locally to minimise by-product transportation. Additional land is also needed for the installation of the water recycling units.
Moreover, the initial CAPEX investment for setting up the passivation emitter rear contact cell (PERC) production is about 8% higher in the case of a minimal liquid discharge (MLD) setup.