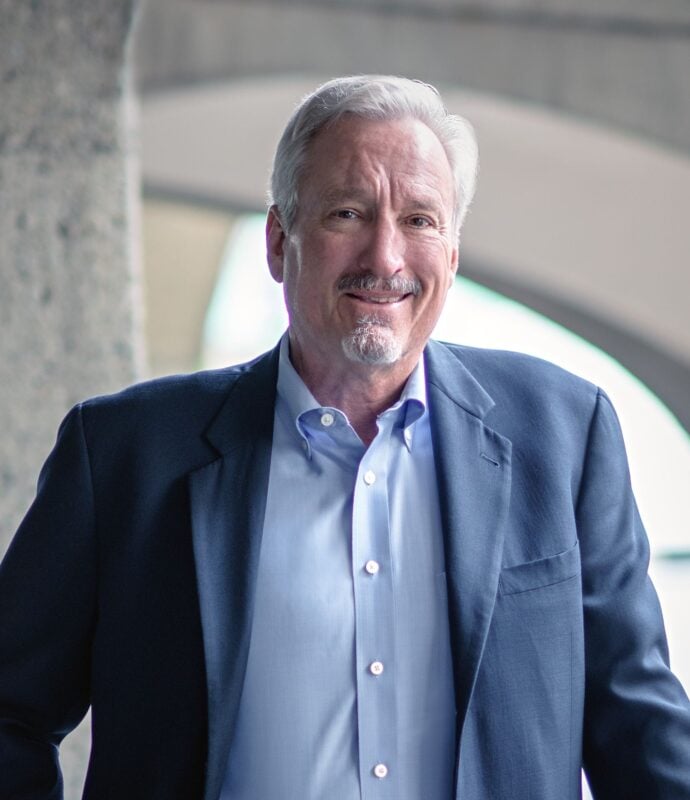
A lot can happen in less than a year, especially in the solar industry. For solar frame producer Origami Solar, change has happened on the domestic supply chain front. In the span of a year, the company has gone from talking about implementing a local supply chain to having plans in place for an imminent roll-out of several domestic steel frame lines across the US.
Among these upcoming steel frame lines is the recent partnership with industrial manufacturing service company Unimacts to establish a frame roll-forming manufacturing line in Houston, Texas. This is a location that will place the company near many module manufacturers and help drastically reduce the time it takes to obtain frames.
Unlock unlimited access for 12 whole months of distinctive global analysis
Photovoltaics International is now included.
- Regular insight and analysis of the industry’s biggest developments
- In-depth interviews with the industry’s leading figures
- Unlimited digital access to the PV Tech Power journal catalogue
- Unlimited digital access to the Photovoltaics International journal catalogue
- Access to more than 1,000 technical papers
- Discounts on Solar Media’s portfolio of events, in-person and virtual
“We’re going to be generally a few hours away, versus 45 to 60 days. The reduction in the inventory that they have to carry, the ability to get back to just-in-time manufacturing is one of the more enjoyable parts of our sales engagement,” explains Gregg Patterson, CEO at Origami Solar.
De-risking supply chain with domestic capacity
Reducing inventory needs and, more importantly, uncertainties regarding getting solar frames through customs are both key to accelerate the transition to steel frames, adds Patterson.
“With Trump winning the election, his focus on tariffs and duties as a key policy priority is just reinforcing the value of us de-risking the supply chain for our customers or the customers of our customers. Because the fundamental challenge of the solar industry is truly trying to figure out, how do you create certainty in supply and delivery?”
Creating a domestic supply chain allows companies to build a business continuity and predictable risk, says Patterson, especially in the US which has seen several tariffs imposed or increased last year across the entire value chain of a solar module – with most recently tariffs increasing from 25% to 50% for imported Chinese polysilicon and wafers under Section 301.
“In the world of today, in the US, you are unable to predict what your profit is because an arbitrary, capricious duty or tariff can change your cost structure overnight.”
Patterson explains how several customers have faced the issue of seeing their solar frames being impounded or delayed at customs “for months” as they try to qualify their assembly line.
This ability for a company such as Origami Solar to scale up its capacity to meet demand of steel solar frames is not necessarily unique to the US market says Patterson, and could be replicated globally.
“We could take the lines and all the automation that really are optimized to make our steel frames, and we can copy and paste them pretty much in any region of the world. And we’ve got plenty of both domestic and overseas steel partners and fabricators that we can activate very quickly.”
Steel corrosion no longer an issue
Among the topics covered in last year’s PV Tech conversation with Patterson was in regard to the challenge of steel corrosion and how a new coating application – through galvanisation – could provide necessary protection against corrosion.
A year later, this is no longer among the most pressing topics of conversation says Patterson, adding that “People get it”.
Other improvements the company has been looking at in the past year include third-party testing. More than six customers have already gone through full certification testing of Origami Solar’s frames with great results compared to aluminium frames, Patterson claims.
“We’re delivering basically twice the performance of a typical aluminium frame currently,” he adds. “But what we’re also seeing in the industry is a very rapidly emerging, broadly understood field breakage issue. Be it glass or micro-fractures in the glass or cells, which is a very significant risk to the fundamental financial models for big projects or small.
“In other words, the reductions in cost in both the glass and the frame have created a fragility issue, and the best and most cost-effective way to solve it is with a stronger, high-performance frame,” explains Patterson.
He adds that the change glass sizes from 3.2mm to 2mm creates a challenge as, at the same time, the amount of aluminium in frames reduced by 35% to 40% as modules have got bigger. Breakage in either shipping, installation or due to extreme weather events has started to “become a concern”, adds Patterson.
Steel frames providing support to extreme weather conditions
Although perceived as a challenge, the added weight from using steel frames can actually offer some benefits in certain applications, says Patterson.
“A high-performance steel frame, while slightly heavier, actually reduces installed cost where most of the solar is going.”
Patterson explains that the application in question where steel frames give a benefit is for solar projects that have extreme wind loading. This is the case in Texas for instance or more broadly in the Southeast and Atlantic coast in the US.
“What we’re getting out now is the clarity that the steel frames are absolutely a net positive to install cost and a net positive to long-term risk. From an LCOE perspective.”
Patterson says that even though steel frames can adapt and optimise to any segment “quickly and easily”, their use for extreme weather cases offers an advantage and a cost reduction.
“We validated that while the steel frames weigh a little more, it does not add cost to the structure to support the module with that weight gain,” says Patterson adding that it will actually reduce the installed cost. This is because the frame will cover and provide the support to the module in “all kinds of conditions”.
Using recycled steel frames to improve carbon footprint
With the abundance of steel at a global scale, in comparison with aluminium being concentrated in only a few markets, one of which China, it would not only allow de-risking the supply chain, as covered in last year’s conversation, but also steel frames could overtake aluminium frames as the leading standard in the industry and at a fast pace, says Patterson. This could be achieved in a similar fashion to what tunnel oxide passivated contact (TOPCon) technology achieved in the last few years.
“If you look at the history of solar and, for example, TOPCon, it went from literally 0% of the global shipments to 80% in less than four years. We expect a similar response as people see the value of steel. It’s not just a US solution, it’s the right answer globally. We believe the transition to steel as the standard will be very, very rapid.”
This would also make it easier when thinking about end-of-life use of the steel frames and recycling it. “Solar recycling is one of the hottest emerging markets in the US. It’s also quickly going global, especially in Europe.”
Patterson explains that switching from importing aluminium to using domestic recycled steel could reduce the carbon footprint by 90kg per module. He mentions that the numbers were validated by a third-party life-cycle analysis firm which specializes in it but also by the Ultra Low Carbon Solar Alliance, which is a coalition of solar manufacturing companies using market forces to decarbonise the solar supply chain, making clean energy even cleaner.
Reducing the carbon footprint on a solar module and, more broadly, environmental, social and governance (ESG) standards continues to be a hot topic in the industry and one that will grow every year.
“As we’ve talked to multiple experts, the lowest hanging and most material fruit to pick is moving to a recycled steel frame.”
Origami Solar and PV Tech are partnering on a webinar exploring steel module frames in extreme weather conditions on 19 February. For details, click here.