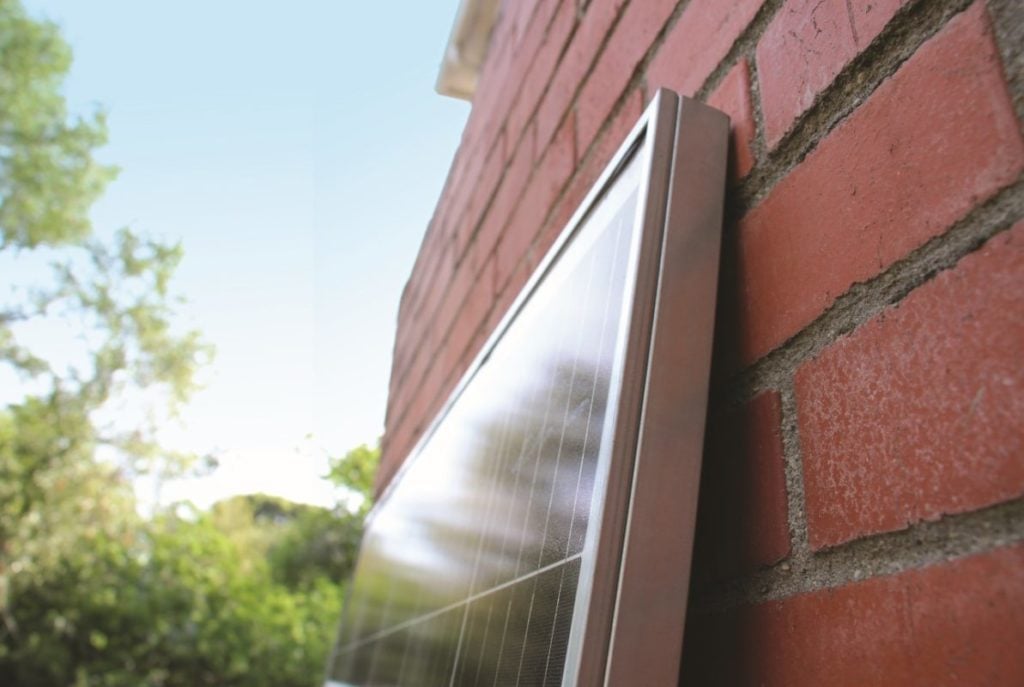
When US president Joe Biden signed the Inflation Reduction Act (IRA) in August 2022, the aim of that bill – for the renewables industry – was to build a domestic manufacturing industry and reduce the US’ reliance on foreign products.
If tax credits for polysilicon, wafers, cells and modules were part of the 45X Advanced Manufacturing Production Credit, a key component of a module was not part of the list: steel frames.
Unlock unlimited access for 12 whole months of distinctive global analysis
Photovoltaics International is now included.
- Regular insight and analysis of the industry’s biggest developments
- In-depth interviews with the industry’s leading figures
- Unlimited digital access to the PV Tech Power journal catalogue
- Unlimited digital access to the Photovoltaics International journal catalogue
- Access to more than 1,000 technical papers
- Discounts on Solar Media’s portfolio of events, in-person and virtual
“Aluminium frames were the standard, they never thought about steel. Part of the IRA requires all trackers and racking to be made with 100% steel in the US. But that does not cover the frame that we’re really pushing. If steel frames are adopted, we reinforce that domestic supply chain in the same way,” says Gregg Patterson, CEO at Origami Solar.
A domestic supply chain that seems poised to continue relying on exports from other markets as the announcements made in the past two years have had an imbalance between module capacity and cells.
This was explained last December by Martin Meyers, principal consultant, market intelligence at industry advisory company Clean Energy Associates (CEA) in a guest blog on PV Tech that can be read here.
Patterson explains that there has been a growing focus on the silicone side of the domestic supply chain in the US, however other elements needed to create a module – such as the frame, the glass or the back sheet – will also be required to be built domestically in the US. “It’s going to take time. And given the abundance of steel, the frame is the easiest and most impactful of the second tier non-silicon based component,” says Patterson.
“We’ve got a huge amount of interest and a growing focus and discussions with all of the big IPPs, EPCs and developers, because their fundamental driver is how do you de-risk the supply chain. The frame is the second most expensive part of the BOM [bill of materials] for a module after the solar cells.”
With both trackers and racks required to have 100% US-made steel, implementing that same policy for solar module frames would make sense, says Patterson, adding: “Steel is a third of the cost of aluminium”. However, with the solar module frames made with steel in the US, Origami Solar does meet domestic content requirements, explains Patterson.
“With the steel frame, we don’t need the financial incentives [of Section 45X], we want to contribute to the tax credit that the developer can harvest. But we want to make sure that you focus on using the steel industry that both the US and Europe have in abundance, and really achieve the strategic objectives that I believe IRA is trying to push.”
Steel vs aluminium
Similar to the PV supply capacity of the entire value chain of a module – polysilicon, ingots, wafers, cells and modules – coming from China, and accounting for more than 80% of the global supply, the supply of aluminium is also majorly located in China.
Nearly 60% of the aluminium supply chain comes from China, whereas steel is more abundantly available in the US and Europe and has the capacity to supply it, explains Patterson. Switching from using aluminium to steel would play a key role in helping set up a domestic production capacity in the US and reduce its reliance on imported frames from China and Southeast Asia. “The fundamental is you natively have the capacity and the capability to do an immediate turn on steel frames.”
Origami Solar started in 2019 and has been developing steel frames since then and has been working for the past two years developing a supply chain – from fabricators in the US and Europe – to deliver domestically made steel frames in the US.
Another relevant benefit from that shift is the reduction of the carbon footprint, says Patterson. “That translates to about 80 kilograms per module reduction in carbon, despite moving from imported aluminium to domestic recycled steel, which is what both Europe and the US have in abundance.”
Interest in compliance with environmental, sustainability and governance (ESG) standards has been increasing in the solar industry lately, as shown by PV Tech’s recent coverage of the issue both globally and in the residential solar segment.
“The fabrication of steel into a solar frame is using a process called roll forming, which is a continuous flow process. Aluminium is an extrusion, anodising, machining, milling, cutting and deburring process. It’s got a bigger carbon footprint than roll forming. And it is less scalable,” explains Patterson.
Overcoming the corrosion and weight issues for steel frames
Of course, using steel for a module frame still also brings its own challenges to the table, which are corrosion and weight, as steel is heavier than aluminium. For the issue of corrosion, a new coating – through galvanisation – provides the necessary protection against corrosion for solar frames, says Patterson.
“The second [challenge] is weight, and that’s why we have to use very thin steel to minimise the weight gain. Now we’ve gotten to a point where all of our customers that we’ve talked to are very comfortable because it’s minor. For a big utility-scale module, it will add about two kilograms. Which is not material to installation, or any aspect of it. And we believe we can get that down even further as we continue to refine and optimise the design.”
The concerns around the weight are a double layer; on one side, there is the importance of reducing its weight, while maintaining the structural performance of the frame, and on the other side, reducing the cost of it. “The steel frame is the second most expensive part of a module.”
“The market dynamics that have occurred in the last two years have all reinforced the value of what a domestically produced higher performance and lower carbon steel frame in terms of the value to the industry today,” concludes Patterson.