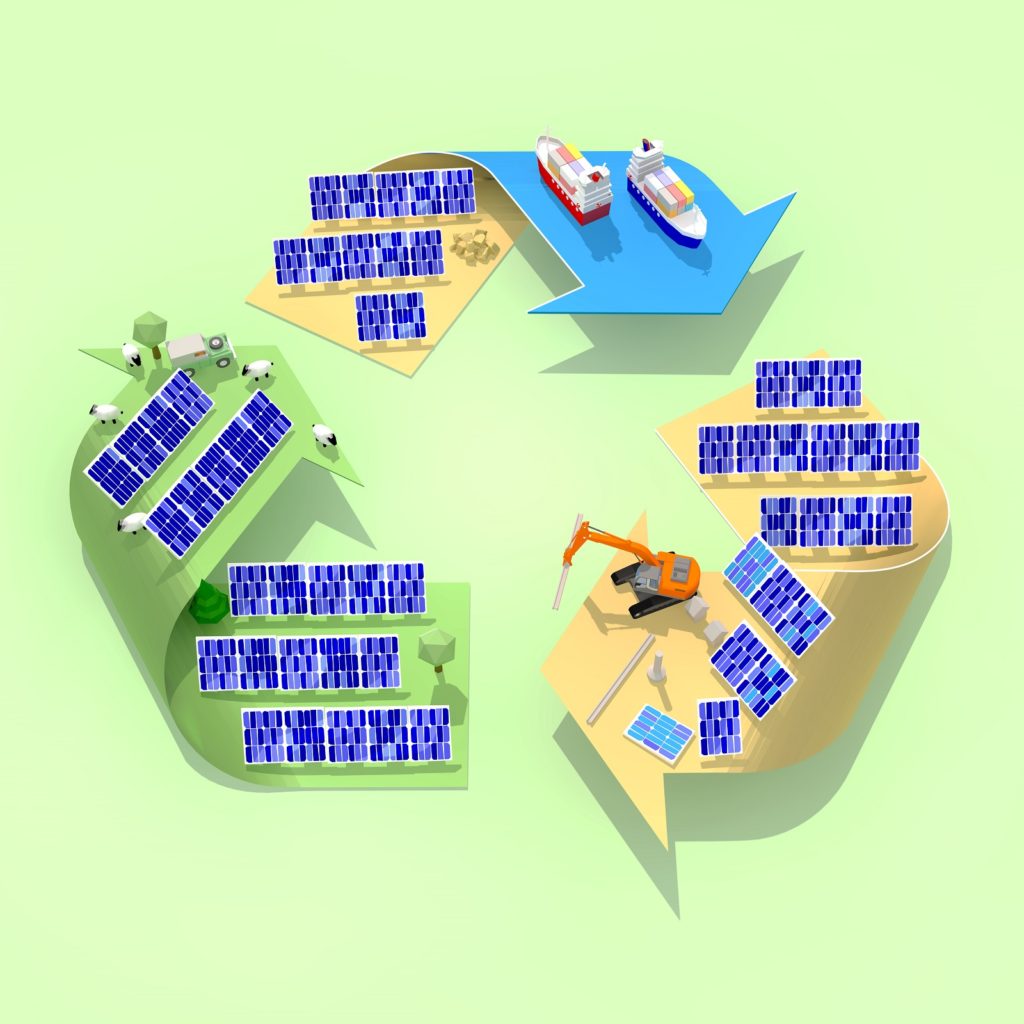
As the world leans on solar PV to decarbonise its power supply, so to must the solar industry clean up its act. Jules Scully charts the industry-wide efforts for a greener solar PV industry.
Reduced-carbon solar panels might not be top of the wish list of developers and procurement contractors currently struggling with volatile prices and supply chain uncertainty, but as clean energy buyers raise their demands, manufacturers are stepping up by greening the PV value chain through more sustainable production strategies.
Unlock unlimited access for 12 whole months of distinctive global analysis
Photovoltaics International is now included.
- Regular insight and analysis of the industry’s biggest developments
- In-depth interviews with the industry’s leading figures
- Unlimited digital access to the PV Tech Power journal catalogue
- Unlimited digital access to the Photovoltaics International journal catalogue
- Access to more than 1,000 technical papers
- Discounts on Solar Media’s portfolio of events, in-person and virtual
While solar manufacturing currently represents a small percentage of global emissions, a business-as-usual approach will see carbon emissions from PV production exceed those of aluminium manufacturing by 2040, according to the Clean Energy Buyers Institute (CEBI). Aluminium is currently the fourth largest industrial commodity from an emissions standpoint, the non-profit organisation said in a recent report.
With PV deployment on track to rapidly scale up in the coming years, those championing a greener solar sector say now is the time to focus on decarbonising the supply chain by reducing the proportion of components produced in areas predominantly powered by coal (or indeed, using more renewable power in the production process) while bringing some manufacturing closer to end markets.
At 50 – 63%, the share of energy required in manufacturing is the most influential factor on the CO2 footprint of a solar module, research from the Fraunhofer Institute for Solar Energy Systems ISE revealed. And in terms of market share, China dominates all stages of module production. Fraunhofer ISE found that as of 2019, China produced 68% of polysilicon, 96% of wafers, 76% of cells and 71% of PV modules.
Jochen Rentsch, head of the production technology department at Fraunhofer ISE, says that for a solar panel produced in China, the carbon footprint is heavily dominated by the energy-intensive parts of the value chain, such as polysilicon production and ingot growth. “And if you drive these energy-intensive parts with thermal power plants, so basically coal, then of course your carbon footprint is relatively high.”
Renewable at the source
German chemical group Wacker Chemie has worked on reducing the environmental impact of its polysilicon by interconnecting all the major steps in the production process, enabling the company to recycle intermediates and byproducts and use them as intermediates or raw materials in other parts of production.
“Another major advantage of our polysilicon production process is the fact that it is almost entirely electrified,” says Christian Westermeier, vice president of sales, marketing and application technology at Wacker’s polysilicon division. “This means that our process is reducing its already low carbon footprint with every kilowatt of renewable energy that is newly installed in Germany and fed into the power grid.”
Westermeier adds that the company also uses a sophisticated energy management scheme that “significantly reduces” energy consumption and, thus, the carbon footprint of its polysilicon.
As it bids to reach net zero by 2045, Wacker is also looking to power more of its operations with clean energy. The company signed an agreement in March with Statkraft that will mean 40% of the electricity needs of its silicon metal production site in Holla, Norway, will be met by hydropower in the future.
Another manufacturer that has been able to benefit from its location to boost the sustainability credentials of its products is Norwegian Crystals, which produces monocrystalline silicon products, such as bricks, wafers and ingots.
Blake Barthelmess, chief operations officer at Norwegian Crystals, says the energy mix where the company’s production plant is located in northern Norway is 99% hydropower and 1% wind, while it also benefits from a nearby glacier that provides naturally cool water.
With a focus on circular manufacturing, the company has developed recycling techniques for silicon material. “We don’t throw it away, we bring it back through our process and increase overall yield and consumption that way and reduce and eliminate waste,” Barthelmess says. “We’re trying to focus on all aspects of our footprint.”
Norwegian Crystals’ reduced-carbon footprint is also boosted by its procurement strategy of sourcing polysilicon from the US and Germany instead of China.
Coal made up 64% of power generation in China last year, the International Energy Agency found. And the majority of the most energy-intensive components of the PV supply chain have been placed in Chinese regions such as Xinjiang and Inner Mongolia, which have predominantly coal-powered grids, according to Michael Parr, executive director of the Ultra Low-Carbon Solar Alliance, which consists of companies and stakeholders committed to accelerating reductions in solar supply chain greenhouse gas emissions.
“The quickest way to have a lower-carbon footprint in solar manufacturing is to build your facility in a geography with a relatively decarbonised grid,” says Parr, who believes investments will reorient to lower-carbon manufacturing “and over time the Chinese supply chain will become less carbon-rich as it goes”.
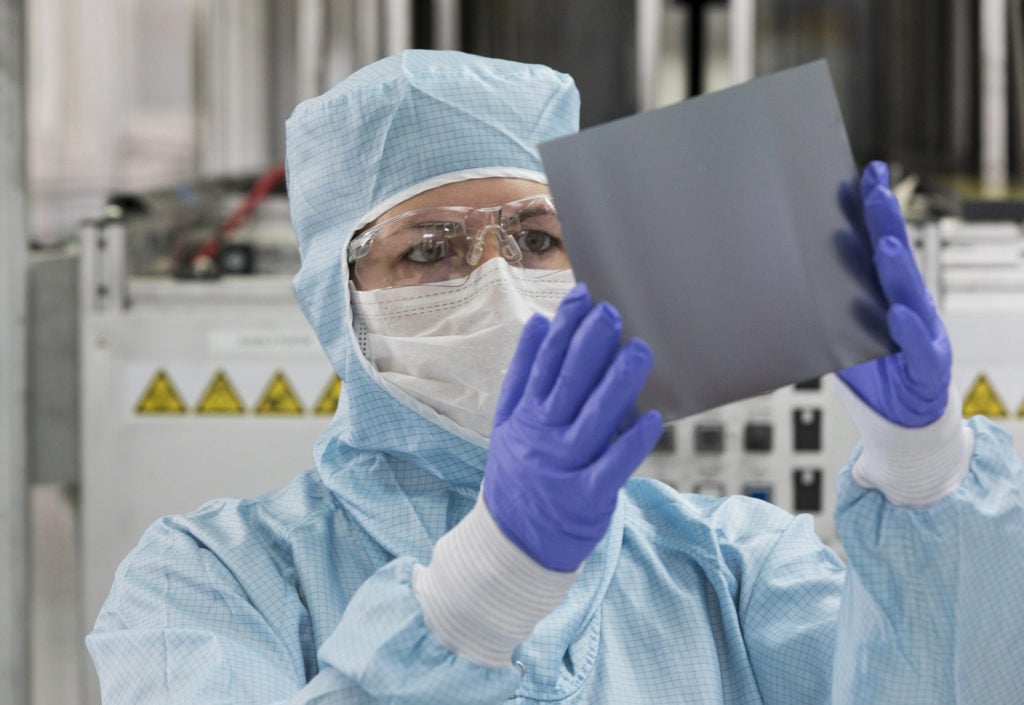
Vertically integrated Chinese module manufacturers JinkoSolar and LONGi have committed to sourcing 100% renewable electricity across their global operations by 2025 and 2028, respectively. When JinkoSolar announced that ambition in 2020 it said it would accelerate studies on new and recycled material alternatives while also building new factories in or adjacent to renewables-rich regions.
Questions have been raised, however, about the effectiveness of simply setting up new production facilities in areas with high levels of renewables. “The problem is that if you have a country with a particular energy mix, if one producer is using the hydropower, they’re robbing Peter to pay Paul,” says Davor Sutija, CEO of wafer producer NexWafe. “Just to say that you are buying hydroelectric-generated electricity, I think is somewhat disingenuous.”
A spinoff from Fraunhofer ISE, Germany-headquartered NexWafe is developing monocrystalline silicon wafers grown directly from a feedstock gas through its EpiWafer process, which obviates the need for intermediate steps such as polysilicon production and ingot pulling on which traditional wafer manufacturing relies.
According to a recently commissioned white paper from NexWafe, conventional wafer manufacturing via the Czochralski process has many inherently energy-intensive aspects, including the need to remelt the cropped wings of the ingot and the high levels of silicon waste due to kerf loss. The company believes these issues leave an opportunity for a manufacturing method such as its EpiWafer process to offer significant energy and carbon savings.
“What is different about our process is that independent of the source of electricity, we actually consume 70% less energy and therefore emit 70% less CO2 than the conventional Czochralski methodology,” Sutija says. “By going gas to wafer, it’s not just green branding, it’s actually energy reduction in manufacturing.”
Alongside innovations from polysilicon and wafer producers, decarbonisation efforts are also being seen further down the PV value chain as some module manufacturers work to green their operations in response to policy drivers, most notably in France.
France spearheading policy efforts to decarbonise module supply
French efforts to source more sustainable solar modules for projects backed by tenders have been successful in driving PV manufacturers to decarbonise their supply chains, according to industry observers, amid calls for the policy to be replicated elsewhere.
Obligatory for solar plants with a capacity of more than 100kWp, the policy requires installed modules to have passed a calculation that certifies the life cycle carbon impacts associated with each step of the manufacturing process with a maximum score corresponding to a return on carbon no higher than half of the life cycle of a PV power plant.
With silicon purification and ingot manufacturing being so energy-intensive, the first thing module manufacturers had to do to enter the market was find low carbon wafers, according to France Jonathan, executive director at consultancy Pink Strategy.
She says while this initially gave wafer manufacturers in Norway a head start thanks to the country’s green electricity grid, Chinese wafer producers are becoming competitive as a result of reduced energy and argon consumption during manufacturing.
Given the programme’s effectiveness, Jonathan says “it is a policy that is interesting to a lot of other countries”.
The EU has been preparing the introduction of an Ecodesign and Energy Label for PV modules, inverters and systems, which will include carbon footprint information requirements, according to SolarPower Europe, while the Netherlands and Norway have introduced environmental product declaration requirements for PV modules, which include carbon footprint reporting.
“Each country should probably have a mechanism like France,” says Jonathan. “My feeling working with manufacturers and developers mostly is that it is a good and proven way to guarantee continuous improvement of solar panel efficiency in terms of carbon emissions.”
Johannes Linder, head of system design and innovation at Belectric, believes the current situation allows manufacturers to simply sort their products for specific markets depending on whether those countries have low carbon requirements. He says: “In the future, if more countries would have certain regulations, for sure the manufacturers would react.”
Progress in greening modules
Modules selected for installation in larger solar projects participating in France’s tenders must pass an assessment of their carbon impact. Authorities can require certificates from module suppliers proving the origin of components, according to SolarPower Europe, which said modules with low footprints can collect bonus points and thus afford higher electricity price bids. South Korea introduced a similar system in 2020.
There are indications that there will be more efforts to incentivise ultra-low-carbon solar, similar to France’s procurement programme, says Karen Drozdiak, head of ESG and sustainability at thin-film cadmium telluride (CdTe) module manufacturer First Solar. “France’s efforts to encourage the use of lower-carbon solar by including a carbon assessment in its tender process sets a benchmark that other countries, such as Spain, could follow.”
Between 2008 and 2019, First Solar’s carbon intensity decreased by around 46% thanks in part to increased module efficiency, manufacturing throughput and capacity utilisation, decreased emissions intensity of purchased grid electricity and energy conservation initiatives.
Providing around 5% of the global module market, thin-film technologies are an example of low carbon PV solutions, SolarPower Europe said in a report published last year. This is due to a lower amount of energy needed for the upstream processing of raw materials compared with silicon-based PV products and a low amount of semiconductor material required to make modules. The trade association said, therefore, thin-film PV lifecycle emissions “are significantly lower than in silicon-based PV products”.
According to First Solar, the carbon footprint of its thin-film modules is 2.5 times lower than that of monocrystalline silicon panels on a life-cycle basis. “Our lower carbon footprint is primarily due to our resource-efficient manufacturing process and avoidance of energy-intensive polysilicon production,” says Drozdiak.
Alongside changes to manufacturing processes, module sustainability can be bolstered by adjustments to how panels are assembled and by the replacement of energy-intensive components.
Research published last year by Fraunhofer ISE found that glass-glass modules enable an emissions reduction of 7.5 – 12.5% compared to PV modules with backsheet films, regardless of their production location. The reason for this is not the backsheet itself, but the fact that glass-glass modules do not need an aluminium frame, which is very energy-intensive to produce.
Fraunhofer ISE’s Jochen Rentsch says reducing the material input from mounting structures can also contribute. “All parts which are heavily energy dependent, if you reduce the amount in the final panel or the final system, that will help.”
Replacing glass and aluminium frames with lightweight polymers is a strategy deployed by Netherlands-based module manufacturer Solarge, which has been able to produce modules that weigh less than half of alternatives while also lowering their carbon footprint. Citing research that suggests as much as 40% of roofs in the Netherlands cannot support traditional modules because of their weight, the company is targeting the country’s commercial sector before expanding overseas.
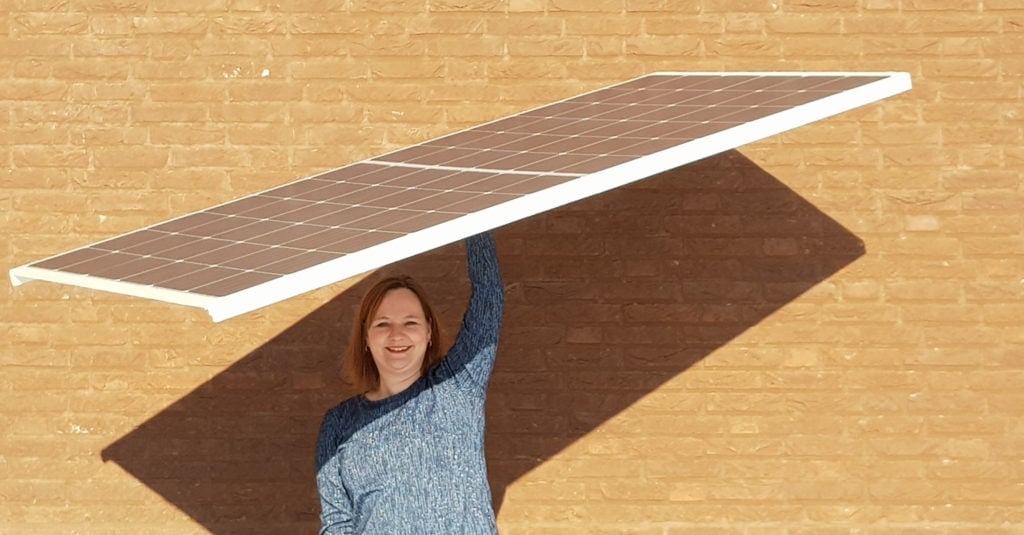
In addition be being fully recyclable – thanks to a reheating step that allows the components to be taken apart from each other without contamination – Solarge modules also have a 25% lower carbon footprint than other solar modules, according to the manufacturer.
Gerard de Leede, co-founder and chief technology officer at Solarge, says the company’s decarbonisation strategy is based on three steps: eliminating the use of glass and aluminium, procuring low carbon cells and using plant-based or recycled polymers.
Having been focused on pilot production and certifying its product, Solarge announced in March it secured a €10 million (US$11 million) investment that will enable it to begin the large-scale production of its modules as it works on setting up a 100MW manufacturing plant in the Netherlands that it hopes to increase to 350MW by the end of 2024.
The company then aims to set up production plants in other countries – enabling it to be closer to end markets, rather than supplying from one location – as well as license its technology to other module manufacturers. De Leede says Solarge is currently in discussion with three parties for licensing its technology, adding: “That allows this whole product to grow faster into the market, with the advantage of [being] lightweight and low carbon.”
Shipping and sustainable construction
While upstream processes have the biggest carbon impact on solar modules, efforts to regionalise some PV manufacturing outside China – most notably in North America, Europe and India – are gaining momentum, potentially reducing long-haul transportation of goods while lowering their carbon footprint.
Fraunhofer ISE research suggests that for a PV module from China, the CO2 emissions generated during transport to Europe account for about 3% of the total emissions.
Despite this small share, logistics challenges and limited product availability mean some solar components can accumulate significant distances before being put to use in a final product.
Blake Barthelmess of Norwegian Crystals points to the journey sometimes made by quartz, which he says is mined in the US, sent to Norway for further refinement, shipped to China to be pressed and formed into crucibles, before being returned to Norway for consumption. “The number of steps that are introduced and the amount of carbon that is associated with that series of steps in the value chain is insane,” he says. “Not only does it cost more, but it’s also just inefficient.”
“Not only does it cost more, but it’s also just inefficient”
Therefore, Barthelmess adds, developing regional supply chain stability “will be fundamental in lowering the overall carbon footprint of the PV industry”.
Although there may be a demand from some purchasers for more locally manufactured modules, sourcing such panels can prove problematic. “We are highly interested in module alternatives from Chinese supply chains,” says Johannes Linder, head of system design and innovation at solar developer Belectric, adding that alternatives become “very thin in the market, especially for utility-scale projects. This is something which is not a healthy situation.”
Having built more than 4GW of solar globally to date, Germany-headquartered Belectric is working to green its operations by predominantly using direct ramming in project construction without the need for concrete. While this technique requires more steel, it means it will be easier to bring the site back to its original condition at the end of the project’s life.
Belectric is also exploring the potential of dual land use by combining solar with agriculture. With governments across Europe scaling up their solar deployment ambitions, Linder says agriPV could be one solution “because it has certain advantages in terms of sustainability” while also increasing social acceptance of PV as it allows farmers to keep their jobs.
Another form of greening the PV sector is by simply getting the most out of all components and achieving the highest production possible, allowing solar farms to displace as much non-renewable power as possible. “Sustainability is also about profitability,” Linder says. “We optimise our projects in a way to make sure that each project can deploy the maximum volume of energy and also for customers the maximum profit.”
Demand signals
Efforts are underway to leverage the purchasing power of clean energy buyers to create demand signals that reverberate across the supply chain, possibly spurring solar manufacturers to reduce the carbon impact of their products.
One such programme is the Decarbonizing Industrial Supply Chain Energy (DISC-e) initiative, which supports energy customers with educational resources to develop an understanding of solar PV supply chain emissions and accelerate the uptake of low carbon solar. Launched by CEBI, DISC-e has published a request for proposal guide with recommendations for energy customers on how to integrate low carbon preferences into clean energy procurement.
Energy customers have an opportunity to maximise their impact and lead the way to a carbon-free energy future by bringing embodied carbon into the solar PV project selection process, says CEBI senior manager Jen Snook. “As awareness around emissions across the solar PV supply chain and the environmental value of low carbon solar grow, more stakeholders will begin to take the no-cost actions to prioritise it and we expect demand will only continue to increase.”
Among the actions clean energy buyers can take include asking PV suppliers for information about the embodied carbon of equipment being employed in projects, which CEBI believes can have a ripple effect in the supply chain, with the information provided fed into databases to improve procurement strategies.
Another tool to assist purchasers is the EPEAT ecolabel, which aims to help clean energy buyers identify and select more sustainable products. Managed by US-based non-profit the Global Electronics Council (GEC), EPEAT addresses the full product life cycle, including managing substances in the product, manufacturing energy and water use, packaging, end-of-life recycling and corporate responsibility.
Having created a solar module and inverter category in its EPEAT registry, GEC is responding to increased market demand for lower-carbon products by adding a new criterion for low embodied carbon that is expected to go live by September. Establishing a carbon threshold, that criterion will be consistent with the methodology used in France’s tender.
GEC senior manager Debbie Graham-Clifford says the organisation has been working in recent months to document the demand signals from solar buyers and “let the manufacturers that are considering EPEAT know that the demand is there already, it exists today”.
Later this year will also see advocacy organisation the Silicon Valley Toxics Coalition release information on the environmental performance of PV manufacturers as part of its Solar Scorecard initiative, which aims to help customers evaluate purchases based on sustainability.
SVTC science advisor Dustin Mulvaney believes that while it is important to address sustainability challenges early in the solar industry’s growth, he is unsure if there will be increased demand for more environmentally friendly PV products. “One would think that as industry grows, it would result in some seeking out more sustainable PV modules, but without widespread campaigns and broader support, this is challenging. Most folks seem to think that PV modules are good enough and don’t want to ask hard questions.”
A similar view is taken by Jenny Chase, head of solar analysis at research organisation BloombergNEF. “I think people just buy the cheapest solar panels. Especially right now when there is something of a supply shortage, I don’t think anyone can be very fussy about it,” she says, adding: “I don’t see manufacturers trying to establish it as a key differentiator.”
Regardless of whether customer demand rises for more sustainable PV products, increased renewables penetration, more efficient manufacturing processes and efforts to recycle a higher percentage of modules will lead to a more decarbonised PV sector.
Michael Parr of the Ultra Low-Carbon Solar Alliance believes there is increased awareness in the market of the levels of embodied carbon in modules. With the projected ramp-up in PV manufacturing as the industry reaches new heights, Parr says there is a “unique opportunity” to help guide that growth “in a more sustainable trajectory that will both reduce carbon emissions in manufacturing, but even more importantly, help de-risk some of the supply constraints in the current supply chain”.