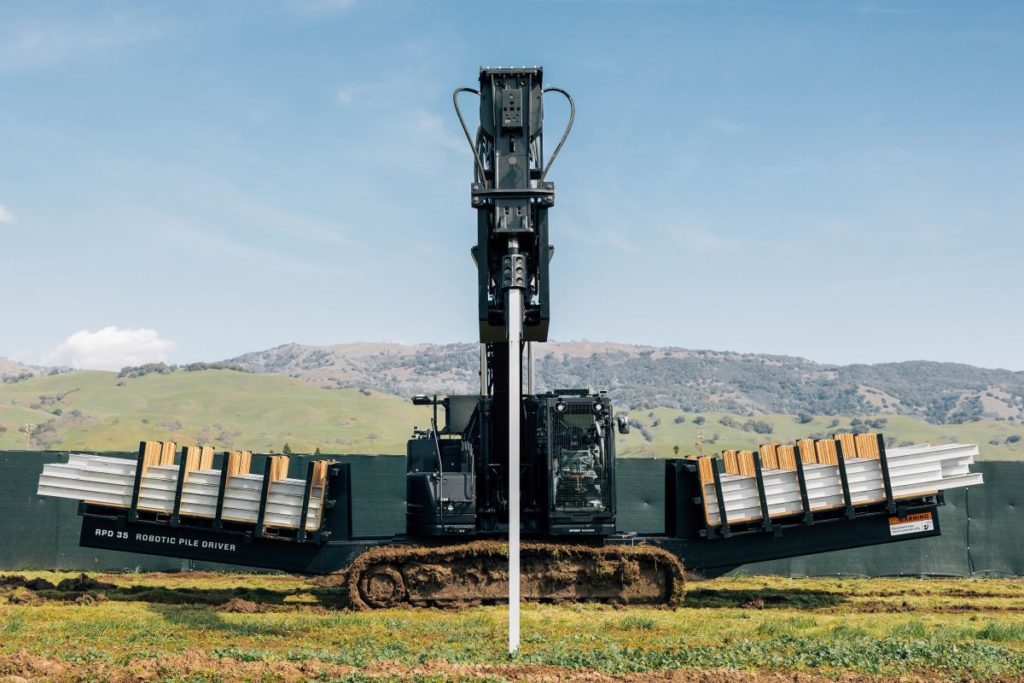
The streamlining of all phases of a PV project will be essential to ensuring anticipated deployment goals are met. Tom Kenning looks at the AI-enabled technologies helping speed up project construction and easing a shortage of skilled labour.
Unlock unlimited access for 12 whole months of distinctive global analysis
Photovoltaics International is now included.
- Regular insight and analysis of the industry’s biggest developments
- In-depth interviews with the industry’s leading figures
- Unlimited digital access to the PV Tech Power journal catalogue
- Unlimited digital access to the Photovoltaics International journal catalogue
- Access to more than 1,000 technical papers
- Discounts on Solar Media’s portfolio of events, in-person and virtual
In the solar ‘terawatt era’, huge volumes of PV coming online mean the construction of projects must be as streamlined as possible to meet capacity targets despite logistical delays and labour shortages. Artificial intelligence is now being used across a variety of applications from robots installing trenches and foundations, to systems that can model a whole construction site and offer numerous optimal response options to any potential problem. With global solar capacity expected to hit 2TW in early 2025 and 3.5TW by the end of 2027, the use of AI promises to help solar EPC companies build more projects in faster times while saving money. AI has mainly been used in the construction phase to date, so this feature examines the smart technologies being deployed to overcome construction challenges encountered in large-scale solar.
While the availability of suitable land dwindles but projects increase in size, the huge procedures of installing millions of modules, trackers, piles and cables with precision are under increasing scrutiny with developers looking to AI. Similarly, while solar supply chain obstacles from COVID-19 and trade restrictions are abating to some extent, responding to logistical delays optimally remains a huge challenge and AI can offer solutions.
Built Robotics
The workforce gap in US construction, for example, is particularly problematic, with EPCs struggling to find workers to build projects, costs being high and many using old and outdated techniques. Companies are, therefore, analysing each step of the solar construction process and considering whether there are better tools or automation that could apply.
Focusing on traditional piling infrastructure for solar PV farms, San Francisco-based company Built Robotics takes heavy equipment, skid steers, continuous track loaders (CTL), dozers and excavators and turns them into robots by installing its hardware and software package known as the Exosytem. Once connected internally this turns the machinery into fully autonomous robots that can also be controlled via company software.
One of the first processes automated by Built Robotics was moving PV panels into place for material handling using a CTL. It then performed trenching on solar farms for the underlying electrical frameworks and the company is now trialling driving traditional metal pile foundations into the ground for solar. Erol Ahmed, director of communications at Built Robotics, claims the tools typically used for this were never meant for pile driving at scale and are loud, repetitive and dangerous, so it should be an automated process.
The company claims that contractors using the robots to automate trenching tasks can bring about savings of 10–30% on the existing costs of those specific tasks, depending on the labour market cost in that project locale. The savings come from installing faster with more precision and less reworking. The firm has completed around 24 projects across the US and Australia ranging between 100-250MW in capacity using its trenching robots since 2018, with its piling offering to be launched next year with similar savings expected.
“What’s interesting about solar is it’s built like a large outdoor factory,” says Ahmed. “The difficulty of robotics in construction historically has been that construction sites are super dynamic and hard to automate. They’re not assembly lines or warehouses which are designed to be automatable.”
Solar farms, on the other hand, are well suited to automation because of the highly repetitive processes involved combined with the technology becoming cheap enough.
Ojjo
AI-based offerings can also go beyond traditional structures. California-based Ojjo, for example, offers a truss foundation optimised for solar that can bear the same loads as a single member placed directly into the ground, but using around half the amount of material. Taking advantage of the forces of tension and compression, the truss bears weight in “a much more elegant way than straight lines do,” says Mike Miskovsky, founder, chairman and CEO of Ojjo.
On top of this, the company uses AI in its unique Truss Driver machines to significantly reduce foundation installation time. Here, the AI can sense changes in conditions in real-time and then make intelligent choices to optimise the installation in terms of accuracy, time and wear on equipment (see case study in box).
EPCs can deploy a fleet of these Truss Driver machines to deliver precision foundations on huge sites. They use automation software to drill to soil-specific conditions sensed by the machine and perform simultaneous drill and drive operations.
How building large-scale solar with AI can jettison three machines, crews and processes
The Gemini, North America’s largest standalone solar-plus-storage system, comprising 967MW of solar and a 380MW battery, required vast quantities of foundations to be installed on tricky terrain in the northwestern Mojave Desert. Soil conditions were too challenging and variable to use brute force alone. The project owner Primergy chose foundation technology provider Ojjo to use its software-driven Earth Truss system to install 257,000 trusses.
Mike Miskovsky, founder, chairman and CEO of Ojjo says the introduction of this level of machine intelligence and accuracy helps EPCs to drop the use of three classes of machines, three crews, and three parts of a typical project schedule.
Without this software-driven approach, EPCs are compelled to use a very expensive drill to predrill the holes for every single H pile. They also have to over-engineer by clearing the way for obstructions and unknowns. They then need to bring a second class of machines with a pile driver to pound each of those H piles into the ground. Then a third class of machine is required to bring bent, twisted or torqued piles back into alignment and put refused piles – those that have not been driven to their full depth – all the way down to their intended depths.
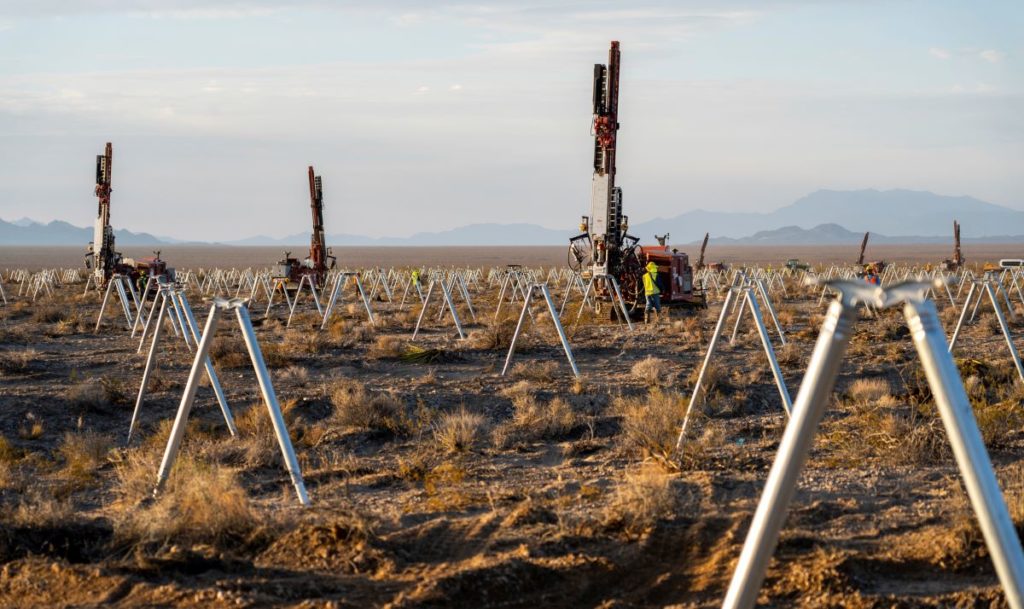
Miskovsky claims that the Ojjo machine eliminates the need for separate drilling and driving operations by doing both in one pass, whilst also avoiding the remediation stage as “each of the foundations is dead accurate each time, every time”.
At the Gemini project, the AI system dynamically sensed when the conditions were changing underground, finding vast portions of the site where the soil conditions changed at every foundation. It was able to penetrate very difficult hard soils and rocky sections underground, but also dynamically sense where the soil became soft. Such sudden variations require dramatic changes in drilling behaviour such as slowing down to disturb less soil. The machine can make this change in a timeframe that, Miskovsky claims, would be unavailable to a human operator using a diesel-powered machine.
“The very soil you’re drilling through is the only thing that’s going to provide you with the friction and pull-out force for the foundation that you’re installing. Two foundations later it could be hard caliche soil, almost like a parking lot cement from the topsoil on down and the machine needs to be able to make these real-time decisions to get a job of that scale accomplished on time and budget.”
He also says it’s very important that, as the industry expands into larger projects, it judiciously uses factory automation, machine automation and artificial intelligence, to make its decisions and processes “faster, more compact, more intelligent and more accurate”.
The Gemini project has been installed, but it is currently in the process of being energised sequentially.
The technology has been deployed on 2GW of installed projects already since 2019 with another 2.7GW under commitment, including some of the country’s largest projects such as the 284MW Eagle Shadow Mountain facility in Nevada, which was considered to have some of the toughest caliche soil in the country. Ojjo’s system was able to eliminate the need for predrilling at this difficult site.
“We’re beginning to develop those projects in ever more difficult soil conditions, where underfoot you’ll run into any number of unknowns,” adds Miskovsky. “Conditions underground are dramatically different from foundation to foundation and left to their own devices, the machinery operators installing these piles are faced with any number of opportunities for inaccuracy and for time and project money lost.”
Spoiled for choice and simulating future solutions
San Francisco-based Alice Technologies offers a platform that uses AI to generate many possible construction schedules for a solar project. Each of these schedules represents a fully resourced planning option, instead of relying on one plan put together arduously over a long period.
The AI technology known as ALICE can then be used for what the company calls “optioneering” where an EPC can go through a range of possible scenarios to see how the project build could be optimised.
Phil Carpenter, CMO at ALICE Technologies, describes how after ALICE has suggested a set of promising drilling schedules, a team can then experiment via AI-driven simulations, such as adding an extra crane on site to see if the build would go faster, adding an extra concrete crew for two days, or testing the overall impacts of an extreme weather event preventing construction for a month. Many multifaceted options can then be tested quickly for that EPC to finalise a construction schedule that fits best.
PV projects spread over several different sections or fields are very suited to using ALICE, says Kevin Fuller, industrial solutions leader at ALICE Technologies. Using the least fertile farmland, for example, may require building a project on eight different fields, in which case it becomes important to decipher the best order of operations, with trucks travelling long distances between sites. ALICE can also model long linear cabling activities and electrical work between the sites. It can then dynamically model how to pivot if conditions change such as the weather or working with new contractors.
EPCs also often have to be flexible around late deliveries, while procuring electrical grid connection equipment and transformers is a major bottleneck in the industry at present. However, if there is a delayed transformer, for example, the ALICE AI can help companies model how to meet commission deadlines despite the setback. Moreover, if a project falls behind during construction, ALICE can generate corrective schedules automatically to bring a project back on track.
The construction aspect of solar is “not wildly complex”, says Fuller, but putting in rails, adding solar panels and running trenches thousands of times over becomes more difficult with scale. This is where AI can deliver sequencing plans that consider an abundance of different possible scenarios.
“The easiest thing to do in construction is put things together,” he adds. “The hardest thing to do is put them together in the right area in the right order at the right time.”
The savings offered by the ALICE technology for solar projects have been reported to average a 17% reduction in project duration, a 14% reduction in labour costs, and a 12% reduction in equipment costs. So far, the company has worked with large general contractors in Europe and North America.
Does AI take away jobs?
The creation of jobs by solar development has been a major PR win for the PV industry, but in many industries, there are fears of human labour being replaced by AI. Nonetheless, many of the AI solution providers in this article claim instead that there is a shortage of workers in the solar industry on projects for which strong financing and public willingness exist. Furthermore, these AI tools will often be put in the hands of skilled labourers rather than taking away manual jobs. Miskovsky claims these new tools allow EPCs to make more judicious use of labour to build more projects and deliver higher project capacities out of a finite and difficult to locate labour pool.
“We’re paving the way for tonnes of new jobs and making it possible for a larger number of workers to quickly train and to learn how to use these machines,” he adds.
His company Ojjo, for example, provides training to employees with no direct background in in solar construction to quickly receive certifications to operate its machines out in the field.
“You still require a lot of humans, they’re just doing different tasks, and we would argue tasks that serve them very well throughout their careers,” adds Miskovsky. Ahmed agrees that if anything, AI will help create more jobs, because it will enable the building of more solar than without it.
AI to enable grid integration of PV
One company is ensuring that AI uses for solar go beyond construction by focusing on grid resiliency in a world increasingly threatened by storms, floods and other extreme weather events. US-based company Rhizome uses AI and historical data to model the social and economic costs of future extreme weather events on the grid and offers a tool to utilities for long-term planning of the grid.
Both distributed and large-scale solar are used as mitigating power generating technologies in many geographies. Still, Rhizome CEO and co-founder Mish Thadani claims that there are no comprehensive mechanisms for utilities to assess the future reliability and resilience requirements for PV additions as extreme weather events get worse over the coming decades.
Rhizome’s tool helps utilities to decide what hard investments will be needed such as undergrounding, replacing ageing assets on transmission and distribution infrastructure, and – notably for PV developers – introducing the right mix of distributed technologies to ensure long-term resilience on these grids.
“When utilities are doing Distributed Resource Planning or third parties are implementing these solutions for resilience purposes, it’s really hard to quantify that value of resilience to get the buy-in from regulators as well as the customers,” says Thadani. “By measuring risk over the long term and how much investments reduce that risk, our platform comes up with cost-benefit analyses for any type of solar project on the distribution system today.”
Thadani admits this does not fully solve the grid interconnection issue facing many solar developers, but the tool will enable more distributed energy resources to be deployed by making a business case to both customers and regulators for those resources by calculating their value of resilience.
Bearing in mind all the AI solutions covered in this article, it seems clear that AI looks forward to a bright future in solar project construction and planning, with a plethora of as yet undiscovered uses still to come.
“We are very much at the dawn of the use of this technology,” says Miskovsky. “We’re all assessing where it makes sense to increase the level of automation and intelligence in the tools and processes that we’re using. We’re all working for the same goal, which is more solar and a faster, cleaner energy infrastructure, because we just don’t have time to wait.”
“It definitely has the feeling of a gold rush period,” adds Ahmed.