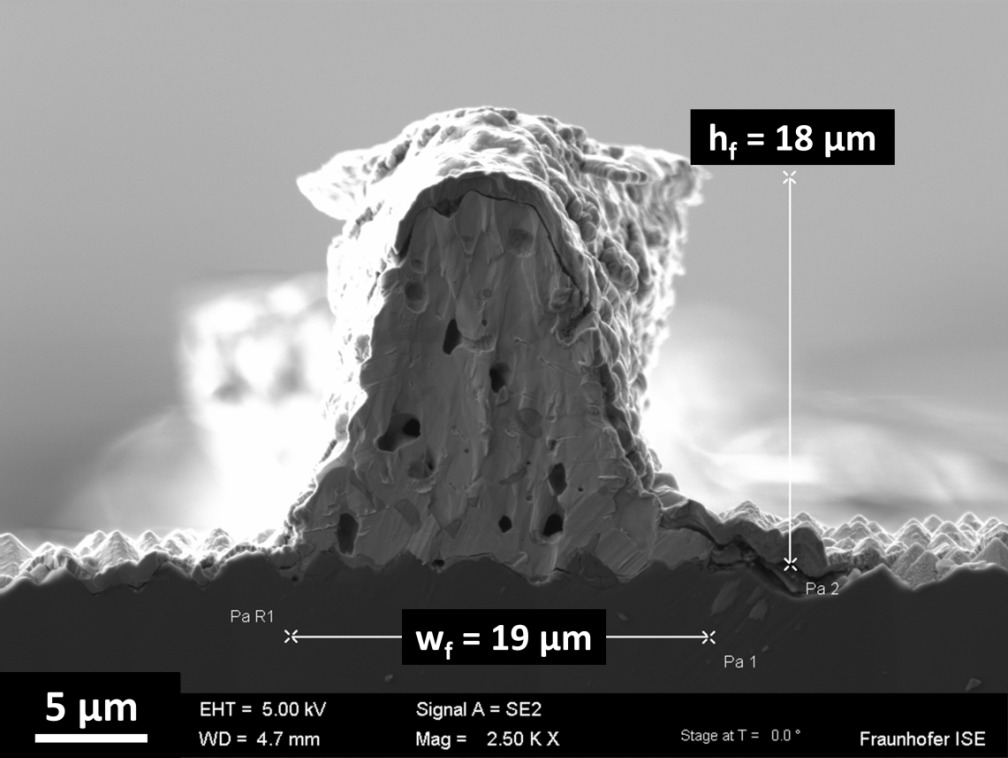
Fraunhofer ISE in collaboration with industrial partners have developed a fine-line metallisation process to create contact fingers with a width of 19µm and a height of 18µm in a single printing step that is almost invisible to the naked eye.
The collaborative project dubbed, ‘FINALE’ includes screen manufacturers Koenen and Murakami and screen chemical supplier, Kissel + Wolf. Optical inspection specialist, Wickon Hightech also participated in the project which was funded by funded by the German Federal Ministry for Economic Affairs and Energy BMWi.
Unlock unlimited access for 12 whole months of distinctive global analysis
Photovoltaics International is now included.
- Regular insight and analysis of the industry’s biggest developments
- In-depth interviews with the industry’s leading figures
- Unlimited digital access to the PV Tech Power journal catalogue
- Unlimited digital access to the Photovoltaics International journal catalogue
- Access to more than 1,000 technical papers
- Discounts on Solar Media’s portfolio of events, in-person and virtual
Dr.-Ing. Andreas Lorenz, project manager in the Printing Technology group at Fraunhofer ISE said, “Working together with industry partners in fine-line screen printing metallization, in particular with screen manufacturers Koenen GmbH and Murakami Co. Ltd. as well as screen chemical supplier Kissel + Wolf GmbH, we have managed to reduce the contact fingers’ width to less than 20 micrometers — a reduction of 30 to 40 percent compared with the current industry standard.”
Fraunhofer ISE said that innovative fine-mesh screens were used in the metallisation of passivated emitter and rear contact (PERC) solar cells in two independent test series that created contact fingers with a width of merely 19µm and a height of 18µm in a single printing step.
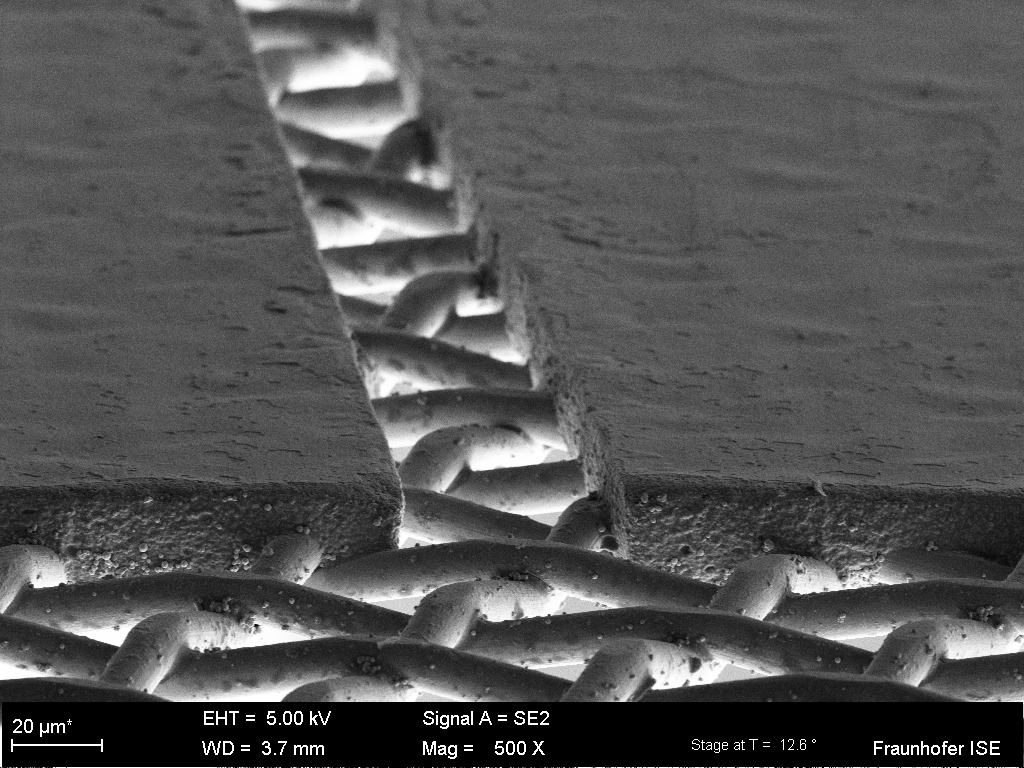
When integrated into modules that would be able to deploy multi-busbar interconnection with 8 to 15 busbars, higher electrical properties and lower power losses can be achieved, according to Fraunhofer ISE.
“Using highly engineered screen and paste systems for fine-line metallisation, it could be possible to start manufacturing solar cells with nearly invisible contact fingers on an industrial scale in the near future. This would represent a great advantage for applications in integrated photovoltaics, where aesthetic, homogeneous module surfaces are in demand,” added Dr. Florian Clement, Head of the Production Technology — Structuring and Metallisation Department at Fraunhofer ISE.
The results of these test series will be presented at two upcoming PV conferences — the 36th EU PVSEC in Marseille, France, and the 29th PVSEC in Xi’an, China.