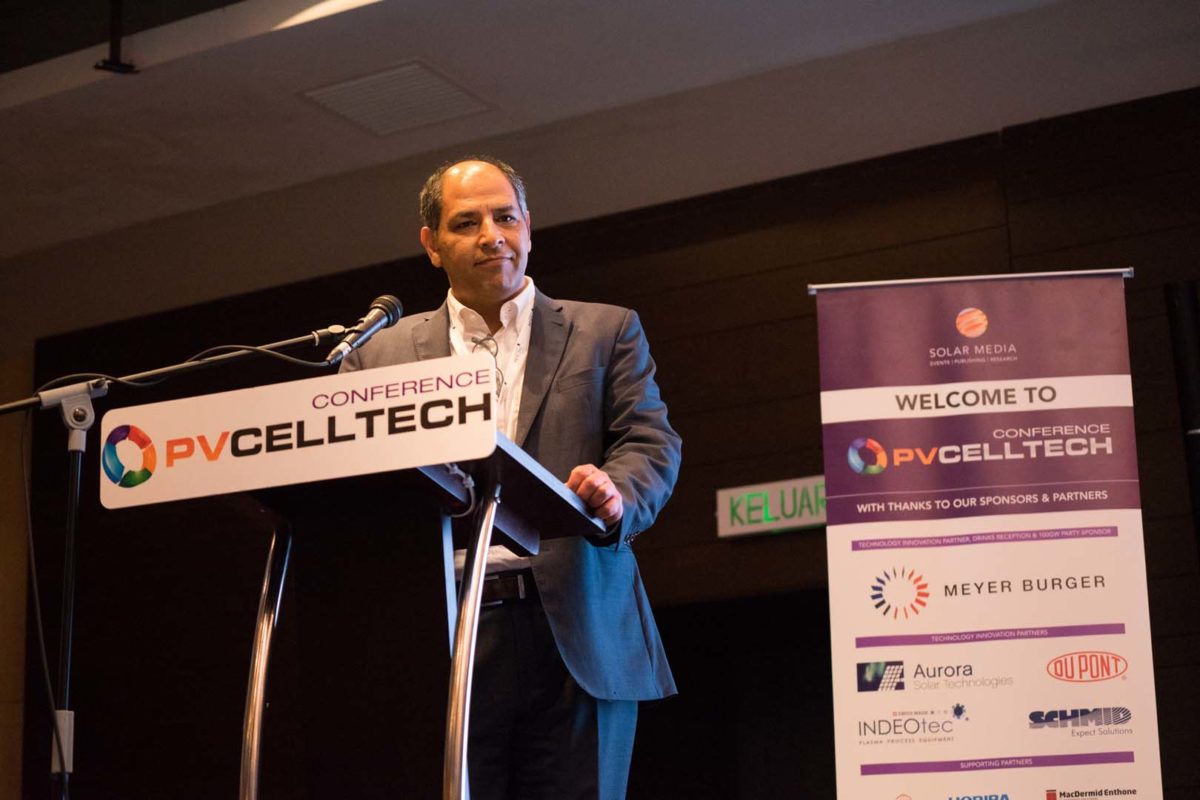
PV CellTech 2018 kicked off in Penang, Malaysia, yesterday, with the heads of technology in the PV industry debating the key topics for solar cells in the present and future. PV Tech caught up with Omid Shojaei, the CEO of cell processing equipment supplier INDEOtec to unpick the increasing interest surrounding the technology for key emerging technologies such as heterojunction (HJ).
PV CellTech 2018 has strong contributions from n-type cell producers, and in particular heterojunction. Why do you feel there is so much investment going into heterojunction today, and are we likely to see any multi-Gigawatt producers emerging in the next few years?
Unlock unlimited access for 12 whole months of distinctive global analysis
Photovoltaics International is now included.
- Regular insight and analysis of the industry’s biggest developments
- In-depth interviews with the industry’s leading figures
- Unlimited digital access to the PV Tech Power journal catalogue
- Unlimited digital access to the Photovoltaics International journal catalogue
- Access to more than 1,000 technical papers
- Discounts on Solar Media’s portfolio of events, in-person and virtual
Omid Shojaei: People are already doing PERC as an upgrade to their existing lines, but this also has a limitation in terms of cell efficiency, which can get to around 21-22% maximum on the industrial level. This will be where the maximum efficiency of PERC ends, so it will also be the limit in the reduction in the levelised cost of electricity (LCOE).
Our Asian friends and the cell producers have already done a lot to reduce the cost of material. They have used economies of scale to push down the price, but now there is no other way to push the price of electricity lower down besides going to higher efficiency, so higher efficiency comes as a low hanging fruit with heterojunction technology.
Everyone knows about the efficiency potential of heterojunction cells, mainly from Panasonic’s success, but where do we stand with processing costs?
Today, what we can tell is that there is a new wave of equipment suppliers coming towards heterojunction, so this will already help to reduce the manufacturing costs. Secondly, there are companies like our own, INDEOtec, who really bring innovative solutions that can help to reduce the cost. Furthermore, we hope heterojunction will soon get to a Gigawatt level, then naturally the price will go down
When will heterojuntion reach Gigawatt levels across the industry?
We are in very close contact will almost all the people who are thinking of investing, so according to our own data collection, there are around 22 to 23 Gigawatts of intentions in heterojuntion already announced.
We also see another trend of players coming out of the blue, not necessarily people who have experience in cell manufacturing, but they come with a lot of downstream EPC experience or they come from other industries like semiconductors and they talk about setting up multi-Gigawatt factories. Altogether, it’s even more than 23GW, as that capacity is just from the traditional cell manufacturers and those with whom we are already in discussion.
Why is deposition so important in making heterojunction cells, and what is different about the Octopus platform that INDEOtec supplies today?
The difference between heterojunction and other technologies is the fact that you only have a few steps – much less steps than in the PERC or in the aluminium back surface field. There are two major tools that are important for heterojunction, PECVD and PVD, and these tools generally are more expensive that the tools that are used in the aluminium back surface field or PERC, but you need much less tools in terms of the number of processing steps.
Furthermore we bring to the market our 20 years of PECVD development with our background coming from flat panel displays. Our dedicated machines can even reduce further the cost of production.
If you want to really go down to the cost roadmap, then you have to bring new ideas and this is what we do with our mirror solution. The mirror machine is about six times smaller than the competition, which translates into lower costs. It also has benefits in terms of automation, since we don’t need to flip the wafer between the top and bottom side deposition and we know how to manage the cross contamination by simplifying the whole manufacturing step.