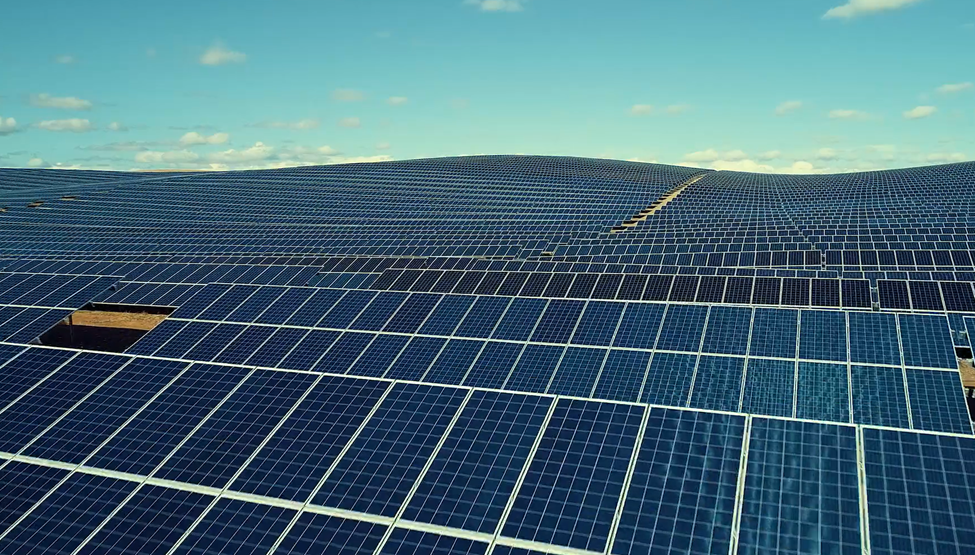
Spencer Jansen, head of new technology solutions at developers Hive Energy and Ethical Power, assesses how the introduction of large-format solar modules has had repercussions throughout the solar design and procurement process.
The module industry experienced some substantial changes from the beginning of the millennium until 2014, however, the arrival of mono-PERC and then bifacial modules in 2018 represented a significant technological milestone, which was followed in 2019 by the production of large-format modules to accommodate broad wafers (M10:182x182mm and M12: 210x210mm).
Unlock unlimited access for 12 whole months of distinctive global analysis
Photovoltaics International is now included.
- Regular insight and analysis of the industry’s biggest developments
- In-depth interviews with the industry’s leading figures
- Unlimited digital access to the PV Tech Power journal catalogue
- Unlimited digital access to the Photovoltaics International journal catalogue
- Access to more than 1,000 technical papers
- Discounts on Solar Media’s portfolio of events, in-person and virtual
The solar business has entered a new module-era, characterised by the production of the 600W+ bifacial ultra-high power modules, which leads to increased yield generation and a balance of system (BOS) cost reduction. Increased sized panels have significantly impacted multiple aspects of the rest of the installation, including inverter sizing and mounting structure design. Increases in project size from a typical 10MW project to 50MW+ has also highlighted the value of efficient and reliable communication technologies within our assets. With this increased reliance on newly developed installation technologies and communication software, safeguarding assets from liability has become a consideration of increased importance in the rapidly developing procurement landscape.
This article presents the background to Hive Energy and Ethical Power’s experience in large format solar procurement, provides an overview of procurement considerations for inverters, mounting structures, communication software and design software, and discusses the importance of safeguarding your procurement decisions.
Broad changes in the solar industry
Hive Energy and Ethical Power have been operating within the solar industry since 2010. Having recently acquired 50% of Ethical Power, Hive Energy has gained a wealth of experience in the procurement considerations for large-format module solar parks.
Ethical Power started by developing rooftop systems before moving into the subsidised solar farm engineering, procurement and construction (EPC) business where it financed, constructed, and sold its solar farm projects mainly to the large financial institutions. In addition to managing its own solar projects, Ethical Power O&M managed third-party portfolios. Due to an abundance of government funding in the field, the industry saw a swell of inexperienced small developers building rushed solar assets to meet feed-in tariff and Renewables Obligation deadlines in the UK.
This resulted in poorly constructed projects with multiple faults and poor yield. Ethical therefore found itself in a position where project owners were asking it to come and fix faulty projects – this provided the company with valuable experience of what can go wrong and what to do about it.
Apart from fundamentally poor construction resulting in connection, cable and mounting system failures, another key issue was the poor selection of components. Inadequately selected components had ineffective performance monitoring and communication systems with money wasted on ineffective CCTV and poorly installed measuring equipment.
Since this period Ethical has acquired and developed an independent connections provider (ICP), providing further insight into the ICP world, and required connection considerations. As such, Hive Energy and Ethical Power’s combined position as the only fully integrated company that develops and acquires projects, is an ICP, EPC and O&M, provides them with a unique position to understand what it takes to build a reliable solar park.
Considerations for inverters, transformers and battery systems
One of the changes that has taken place in the large-format module era is that inverter manufacturers have had to adapt to the higher current levels associated with the new modules. In the case of central inverters or PV station solutions, the adoption of the higher current has been quickly implemented. However, it has also created a problem with the string combiner boxes that have seen increased costs due to the added complexity to their design as a result of the higher current coming from the strings, making the overall central inverter system more expensive.
String inverter manufacturers have also quickly adapted their products (mostly at zero cost) to high current modules, with a higher power rating with 250kW now typically available, taking an economically advantageous position since the combiner boxes are not needed, meaning there is virtually no cost increase in the string inverter system. This adds to the typical known benefits from the string inverter system.
Furthermore, going forward, we will start to see bi-polar strings +/- 1,500V systems reducing cable cost and improving efficiency where there is a smart string control on the module array coupled to a centralised string inverter station next to the STC unit in 6MW+ blocks. This will see string inverters move to over 300kW and allow for other DC coupled devices, such as storage systems, to be integrated at the DC level where possible, removing the cost for a second set of inverters as an example.
One of the important benefits of string inverter systems, and an important consideration when selecting inverter technologies, is the power line communications technologies – where commands between inverters and transformer (TX) stations are sent via the power cables. These communications drastically increase the reliability of the system.
Previously, inverter failure would result in individual component testing, resulting in time and money wasted sending an engineer to pinpoint the fault. However, with integrated IV curve testing, in which inverter current and voltage is monitored in real time at string level, engineers can be sent directly to the fault. This integration of communications is an important consideration for us when selecting our inverter supplier, saving time and money when the solar farm is operational.
The second consideration when selecting a string inverter system over other technologies is that most of the big string inverter suppliers like Huawei and Sungrow now offer a wrapped-up solution including an inverter and TX station system. This allows them to compete with the PV station/central inverter solution and offers the EPC contractor and end client a much more robust contractual and warranty position, packaging the onsite electrical system from the end of a string to the client substation under one supply contract. Experience tells you that failures occur at the interfaces between contractors and is where any liability becomes unclear. Removing these interfaces improves reliability and reduces cost and gives greater accountability
Battery energy storage systems (BESS) over the next few years will become part of any standard solar farm solution at some level. It is therefore critical that any solar farm being developed today takes this into account and understands how these BESS will be integrated or specifically not integrated into the project. The lifespan of a battery is dependent on its operational management, how good the digital architecture is, how well is it cooled, how modular (plug and play) the system is, how well it integrates with the grid, and what common parts are used with the solar system. It may well be, going forward, that the BESS are distributed in blocks over the solar farm. These are key questions that need to be asked now from the supply chain partners to avoid last minute changes resulting in poor design.
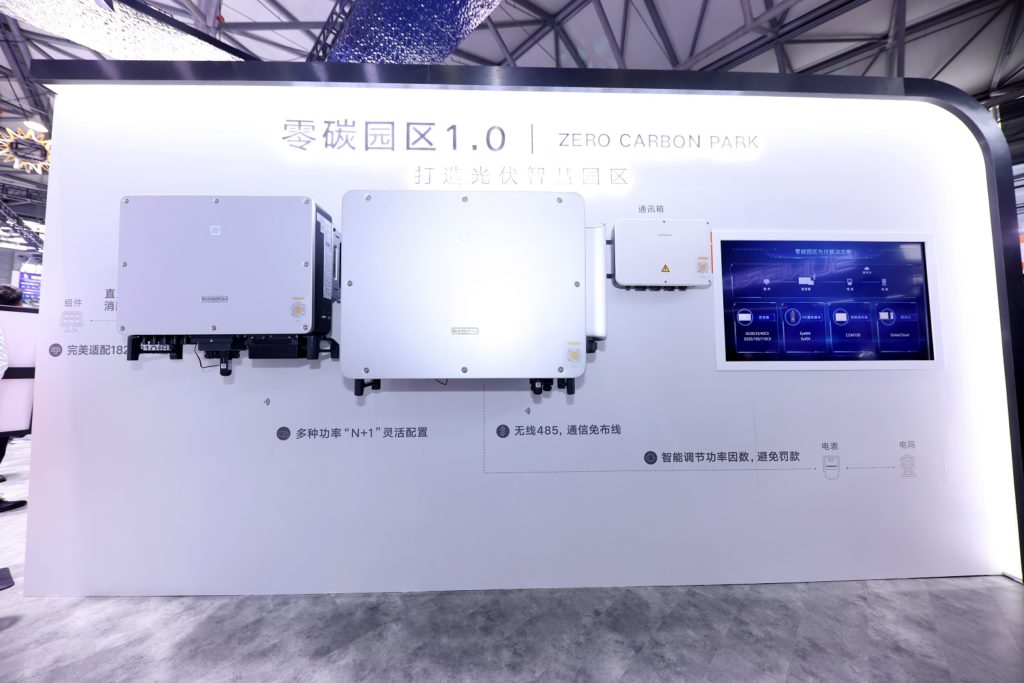
Considerations for mounting structures
Large-format modules require new procurement considerations for the mounting structure due to geometrical and electrical features to incorporate bigger wafers, a configuration of lower open-circuit voltage, higher short circuit current, and a new string design.
Trackers, in combination with bifacial modules, are becoming the standard PV installation throughout the world. This is due to the increased yields that can be achieved when combining the two elements, which generates revenues that generally overcome the extra cost associated with the tracker installation within a few years.
Tracker systems have come a long way in the last five years, but they haven’t been free from issues related to wind loading, with several examples of installations ruined under apparently low wind loads. Accordingly, the most critical challenge of the photovoltaic installation in this new era is the reconfiguration of tracker design, since the accommodation of 600W+ involves a higher pressure of wind load on the system that affects the trackers’ stability and reliability.
The widespread availability of large-format modules and the increase of energy generation brought about a significant reduction in system cost. Additionally, the need arose for accommodating technology changes in the PV systems, since ultra-high-power modules add significant weight and require mechanical and electrical adaptations in trackers, to guarantee optimum yield and efficiency.
The design and configuration of solar trackers are closely related to the dimensions of the photovoltaic panel. The installation of large-format modules implies subject to different dynamic behaviour in tracker structure, including heavier loads.
The use of large-format modules requires longer chords, longer rows, stronger structures and, overall, more robust cross-sections to structurally bear the extra weight and conserve stability against wind effects.
The electrical configuration of the tracker is also affected by the mounting of ultra-high-power modules due to the change in the number of strings (modules connected in series) assembled in a row.
Module changes | Changes in tracker stiffness/stability | Impact on tracker/component design |
---|---|---|
Length increase | Chord increase High effect on aeroelastic critical wind speed | Higher structures Adjusted stow strategy |
Width increase | Longer rows Lower torsional stiffness | Improved drive system |
Surface increase | Higher wind load on module surface Higher torque on lock systems Higher foundation reactions | Bigger tracker surface Stiffer purlin Strengthened tube Higher post |
Mass increase | Lower natural frequency Changes in damping High effect on aeroelastic critical wind speed | Improved drive system Adjusted stow strategy |
Eliminating procurement risk
Due to the rapid developments in this large format module era, there is a heightened chance that the technologies selected will be without an established operational track record. Therefore, building and maintaining relationships with manufacturers has become a primary consideration when designing utility-scale solar systems. Building a relationship upfront with Huawei and others has allowed us to eliminate risk where possible through the integration of inverters, transformers, and battery systems.
Beyond the maintenance of relationships with suppliers, risk within procurement is eliminated through frequent and thorough testing of components. In addition to seeking the confirmation of the relevant independent certifications from suppliers, we would also carry out factory inspections where, in the case of solar modules, we cover:
- Incoming quality controls
- Materials warehousing and storage controls
- Material and process controls used in all major assembly steps
- Outgoing quality controls and inspection
- Finished goods management
- Supply chain, production, and quality management
- General factory organisation, cleanliness, safety, employment, and environmental standards
In addition, we would also carry out production inspection and testing that would cover items such as:
- Flash (IV) Testing – checking for power and resistance defects
- Electroluminescence (EL) imaging – checking for cell defects
- Visual inspection – checking module component integrity
- Schedule and packing checks
And finally, we would also take sample modules from a batch to an independent lab to confirm that would typically be:
- Visual inspection
- Maximum power determination at STC
- Electroluminescence
- Wet leakage current
- Potential-induced degradation
- Stabilisation test
- LeTID test
- Low irradiance measurements at 200 W/m²
- EVA gel content measurement
This is to ensure that the datafiles shared for modelling are accurate. As such, it is important that the supply chain is shielded from risk through production line checks, factory audits and material supply chain checks, so only manufacturers that pass the highest level of quality control within an independent laboratory will be utilised within the design of a utility-scale solar park. This benchmarking of manufacturers drives procurement considerations prior to any design and operational requirements of the selected technologies.
Increasing efficiencies in software procurement
For 5 -10 MW projects in 2016, utilising simple CAD software was sufficient to manually place our solar modules on fields, although it was a time-consuming process. However, for utility scale projects that incorporate large-format high current modules, transformers, and tracker systems there is a clear advantage in utilising software with fully automated and advanced modelling capabilities to design solar systems.
Software has been required to keep pace with the development of solar components, and now design software procurement is as important a consideration as the physical structures within the park. Helios 3D is a fully developed software package used by Ethical Power that lays out the solar farm relative to topography and fully optimises the site both mechanically and electrically within a given set of parameters. This design can then be imported into to PVsyst, which then calculates the performance of the project, using SolarGIS typical monthly year weather data.
As with any software, success comes from having the right inputs and drivers with a deep understanding of how it all works and comes together, working hand in hand software provider. However, once you have mastered this, changes can quickly be made to any given design with an output that does not just give you a layout, but a full bill of materials (BOM) that covers cable sizing, lengths, and equipment placing, with some manual intervention to make it more practical where required,
Due to considerable reliance on technology within the large-format module era, building and maintaining a relationship with the software manufacturer helps achieve the full capability of the software to maximise solar yields. When issues in system design are highlighted, a close relationship with the software manufacturer means they can promptly modify the software, reducing delay in design timescales and ultimately project timescales. This means that gaining even small efficiencies in project design through long term relationship building and maintenance is a key consideration for us when deciding software usage.
A solar park is an engineering and procurement exercise. The rapid development of all parts of the solar park are resulting in a consistently accelerating procurement landscape. Beyond the technological requirements that drive procurement considerations both for solar components and software, building and maintaining long term relationships with manufacturers has allowed for Hive Energy and Ethical Power to design things that aren’t widely available, and create innovative solar assets that optimise yields in complex scenarios.
Despite the trends of automation and integration for utility-scale solar projects within the large format module era, success in procurement is driven by experience in risk elimination through manufacturer quality control and relationship development.
Author
Spencer Jansen is head of new technology solutions at developers Hive Energy and Ethical Power, UK-based developers of utility-scale solar projects.