
Solar systems, we’re often told, are a low maintenance source of generating electricity. ‘Stick it on your roof or in your field and forget about it’ is a commonly heard phrase in the industry. Granted, compared to wind and CSP installations – both of which are an engineer’s dream – photovoltaics is relatively ‘plug-and-play’ in its simplicity. Yet things can and do go wrong with PV, which is to be largely expected for such a nascent industry.
According to the National Renewable Energy Laboratory (NREL) of the US, around 90% of the world’s commercial solar PV systems only became operable in the past seven years. Quite simply, the industry does not yet have an adequate amount of heuristic data to accurately estimate a PV system’s operation and maintenance (O&M) costs.
Unlock unlimited access for 12 whole months of distinctive global analysis
Photovoltaics International is now included.
- Regular insight and analysis of the industry’s biggest developments
- In-depth interviews with the industry’s leading figures
- Unlimited digital access to the PV Tech Power journal catalogue
- Unlimited digital access to the Photovoltaics International journal catalogue
- Access to more than 1,000 technical papers
- Discounts on Solar Media’s portfolio of events, in-person and virtual
Once a PV system is installed, a mass of extenuating factors immediately begin to buffet and shape its existence, affecting performance in many different ways. The solar industry has undertaken incredible work and research to calculate these factors, and expert O&M providers can – with reasonably good precision – predict what the average US$/kW O&M cost of a system will be based on parameters such as location, climate, size, system configuration and materials used.
And costs to maintain a solar plant are falling. NREL assesses that the average total lifetime O&M for a typical PV array in 2007 was $35/kW/year; in 2019, that figure was just $17/kW/year – a respectable rate of learning. Most of the administrative costs of a solar PV plant are influenced by factors beyond the immediate reach of the solar industry. However, the industry does have a far greater degree of control when it comes to failure rates, and how to minimise them.
Common failure modes identified in the field include failures in combiner boxes, inverter fans, AC disconnect and, of course, failures with the modules themselves, such as PID, LID, solder durability and backsheet erosion.
Today, these are the most common causes of solar module failure identified by Q CELLS and renowned independent testing body, TÜV Rheinland. Identifying the problem is merely the first step towards tackling it. Tackling and solving these failure modes results in lower operating costs for system owners, and a greater return of investment. Solar may be a young industry, but a lot of learning has been crammed into the past two decades; much of it driven and shaped by Q CELLS.
A problem shared
In December 2020, TÜV Rheinland officially launched its new Quality Controlled PV program. The intention of this program is create a new pathway to higher PV standards. The first mover in the program is Q CELLS, which – along with other industry partners – worked closely with TÜV Rheinland at various stages of the program’s creation in order to accurately determine the main quality issues in PV, and how to tackle them.
“Our intention was to set the industry standard, which I believe we have,” said Dr. Nicole Nelles, head of Q CELLS Global Quality Management. “And we won’t rest there. We want to help TÜV Rheinland to maintain that standard moving forward.”
Dr. Nelles guided the Q CELLS quality management and R&D teams in Thalheim, Germany, in close cooperation with module testing experts at TÜV Rheinland, in the development of this program. TÜV Rheinland’s objective is that it will become a dynamic standard bearer in ensuring that the solar industry never rests on its laurels where module durability is concerned.
To create such a groundbreaking program, TÜV Rheinland experts were invited to work with Q CELLS’ quality management experts at Europe’s largest solar testing facility – the Technology and R&D Headquarters of Q CELLS in Thalheim. The result of this cooperation, as well as TÜV Rheinland’s work with other industry partners, was not only the creation of higher testing standards for existing test schemes, but to devise completely new program components. These include regular, independent and random module production testing overseen by an onsite expert from TÜV Rheinland, and regular material tests from running production – two component steps that help make the Quality Controlled PV program the new benchmark for solar module quality.
Owing to its close cooperation with TÜV Rheinland, Q CELLS has become the first module manufacturer to pass the new, completely independent three-component Quality Controlled PV certification process. So what does the program entail, and how is it different to standards that preceded it?
Introducing unique levels of surveillance and monitoring
The Quality Controlled PV program sees independent TÜV Rheinland experts visit the production sites/module testing locations of module manufacturers, where they take up residence while performing three key components of the quality control program. By having these TÜV Rheinland representatives onsite, a manufacturer’s production processes are subjected to transparent and impartial quality control oversight. There can be no cherry picking by staff of model modules; rather, TÜV Rheinland’s independent experts have free rein to select and test samples at will – regularly and randomly.
“This step is, we believe, something unique in the solar industry,” said Dr. Nelles, adding that the catalogue of tests carried out by TÜV Rheinland onsite have been established to go beyond the standard level of approval and safety qualification typically applied in solar.
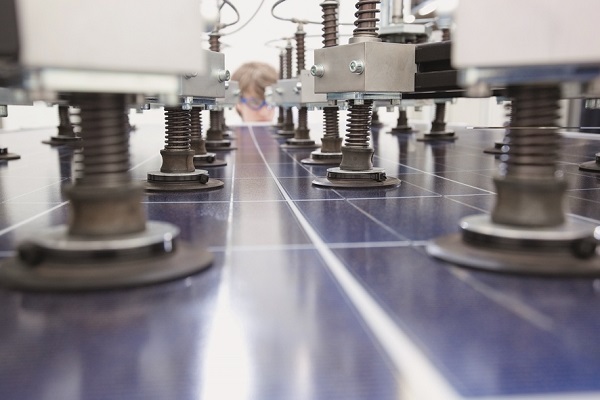
A more stringent testing process
To create the Quality Controlled PV program, TÜV Rheinland first identified exactly what the current testing standards did NOT do. With the assistance and valuable input of Q CELLS, they deduced that current certification procedures for module quality did NOT:
- Verify long-term reliability in the field
- Test regarding recent failure modes observed in the industry (such as component durability, solder durability, PID and LETID)
- Continuously monitor the quality of materials used in production
- Monitor the production quality of the modules
A new three-component procedure was devised to address this (see In detail, below). Q CELLS has already put its flagship Q.PEAK DUO-G9 solar modules through the new Quality Controlled PV program, and can report that the series has been certified by TÜV Rheinland.
And this is just the beginning, explained Dr. Nelles. “Q CELLS is delighted to have achieved certification, and continues to develop additional test programs in parallel at our module testing site in Thalheim – each designed to ensure greater improvements in solar module quality and durability.”
The objective of TÜV Rheinland is to continuously update and improve the Quality Controlled PV program to ensure that it remains a vital, dynamic piece of the fast-moving PV landscape. “Solar technology is constantly evolving,” said Lukas Jakisch, Business Field Manager – PV Modules and Solar Thermal at TÜV Rheinland. “We are determined to ensure that quality standards keep pace with technological advances so that the bar for quality never dips.”
In detail: The new Quality Controlled PV testing program
Component one: The initial qualification test conducted by TÜV Rheinland assesses long-term reliability of modules by applying testing durations that are up to three-times longer than standard IEC and UL tests. The program also adds and adapts sequences to address new failure modes. This includes:
- 2,000 hours of damp heat (DH) testing – twice the duration of a typical 1,000 hour IEC/UL damp heat test
- 600 thermal cycles (TC) – around three times as many cycles as those performed for the IEC
- Extended sequential test sequence combining static and dynamic mechanical load testing with climate chamber stresses
- A UV-test sequence combining DH + UV irradiation + Humidity Freeze + UV irradiation + TC
- PID and LETID testing
Component two: Random sampling of production sees TÜV Rheinland representatives stationed at the module test labs at the production sites where they can randomly select samples for testing from running production.
Component three: regular monitoring of materials and core components of the module delivers an additional layer of quality surveillance. The TÜV Rheinland expert will monitor supplier audits and conduct a material footprint analysis of materials regularly used. The result is a continuous oversight of standards.
Currently, there are several players in the market providing programs for testing, but they are mainly driven by big volume customers rather than by manufacturers. Small-scale customers cannot generally benefit directly from such results. In offering this Quality Controlled PV program, Q CELLS, as a manufacturer, offers a quality testing program to customers with continuous testing throughout, resulting in high quality products with an official certification.
Visit PV Tech for Quality Time for Solar PV Part II next month as Q CELLS delves into cell and module efficiency, next-generation technologies and the importance of expert collaboration and cooperation.
Q CELLS, TÜV Rheinland and PV Tech have collaborated on a webinar to introduce the new Quality Controlled PV program. That webinar, which explored the new QCPV program in detail, is available on-demand here.